Understanding 2T/4T/S4T Features in Welding: Differences and Usage
Introduction
Welding technology has evolved significantly, offering diverse modes that optimize precision, efficiency, and ease of use. Selecting the right mode is crucial to ensure effective welding outcomes. Among the various features available, the 2T, 4T, and S4T modes are widely used but often misunderstood. This guide explains these modes, their differences, and their appropriate applications.
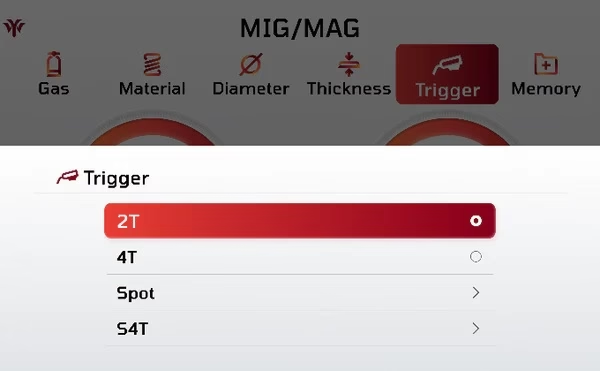
What Does 2T/4T/S4T Mean in Welding?
Understanding 2T Mode (Two Touch)
- Clear definition and operational explanation of 2T mode
- Step-by-step working mechanism of 2T mode
- Specific advantages including simplicity and quick operation
- Limitations like operator fatigue and its impact on weld quality
Exploring 4T Mode (Four Touch)
- Comprehensive definition and operational details of 4T mode
- Detailed working mechanism of 4T mode including the trigger functions
- Benefits including reduced operator fatigue and improved comfort
- Potential drawbacks like slightly increased complexity and learning curve
What is S4T Mode (Special Four Touch)?
- Thorough explanation of S4T mode, its unique features, and operational details
- Key differentiators between S4T and regular 4T mode
- Advantages such as superior precision, control, and suitability for complex tasks
- Challenges such as higher complexity and the necessity of skilled operation
2T vs. 4T vs. S4T Difference?
Operational Differences
Trigger Mechanism: 2T is simple, while 4T and S4T offer enhanced ergonomics and reduced strain.
Ease of Use: 2T easiest; S4T most complex.
Applications: 2T for short welds, 4T for medium to long tasks, S4T for precision-critical welds.
Technical and Practical Implications
Precision: S4T offers highest control, beneficial in critical welds.
Quality: S4T and 4T modes often yield superior weld quality due to stable operation.
Comfort: 4T and S4T reduce operator fatigue significantly compared to 2T.
When to Use Each Mode?
Best Uses for 2T
- Ideal situations including short and simple welding tasks
- Explanation of practical examples and scenarios
Ideal Situations for 4T
- Recommendations for prolonged and continuous welding operations
- Practical insights into scenarios benefiting from reduced operator fatigue
Appropriate Scenarios for S4T
- Explanation of complex, critical, and precision-demanding welding tasks
- Examples showcasing the superior control of S4T
Advantages and Disadvantages Summarized
Pros and Cons of 2T Mode
- In-depth analysis of advantages such as ease of use and speed
- Discussion of disadvantages, particularly related to operator fatigue
Pros and Cons of 4T Mode
- Examination of advantages like reduced fatigue and enhanced operator comfort
- Exploration of cons, notably the slight complexity in mastering the mode
Pros and Cons of S4T Mode
- Detailed insight into advantages of high precision and control
- Consideration of disadvantages like complexity and necessity for advanced skill
Choosing the Right Welding Mode
- Guidance on evaluating task requirements
- Discussion on the importance of considering operator skill level and experience
- Impact of mode selection on weld quality and overall productivity
Common Mistakes to Avoid
- Identification of frequent errors such as underestimating task complexity
- Explanation of the consequences of ignoring operator comfort and fatigue
- Importance of ensuring equipment compatibility with selected mode
FAQs
Can beginners use 4T and S4T modes?
Yes, but beginners may require initial training and practice.
What types of welding benefit most from S4T?
Precision welding, industrial applications, and critical welds benefit most.
How does switching between modes affect welding equipment?
Switching modes typically does not affect equipment adversely but may require adjustments to settings.
Are special training sessions necessary for S4T mode?
Special training is beneficial due to the advanced controls and precision settings in S4T mode.
Conclusion
Understanding the differences between 2T, 4T, and S4T welding modes is essential for optimizing your welding tasks. By carefully evaluating the task and operator skill level, welders can choose the most effective mode, improving overall performance and quality.