Welding Techniques for Lead: A Comprehensive Guide
Lead is a heavy and soft metal that finds its use in various industries, including battery manufacturing, radiation shielding, and plumbing. Lead welding is a crucial skill in various industries, from construction to plumbing. Whether you’re a seasoned welder or just starting, understanding the best practices for welding lead is essential. Welding techniques for lead are crucial for joining lead materials effectively. In this article, we will delve into the details of welding techniques specifically tailored for lead, considering its unique properties and the importance of performing these processes correctly.
Introduction
Lead welding, often known as lead burning or lead soldering, is the process of joining lead materials together using heat. This technique is prevalent in the construction of roofs, plumbing systems, and stained glass artwork. To become proficient in lead welding, one must master various techniques and safety measures. In this article, we will delve into the intricacies of welding techniques for lead, providing you with a step-by-step guide to ensure successful lead welding projects.
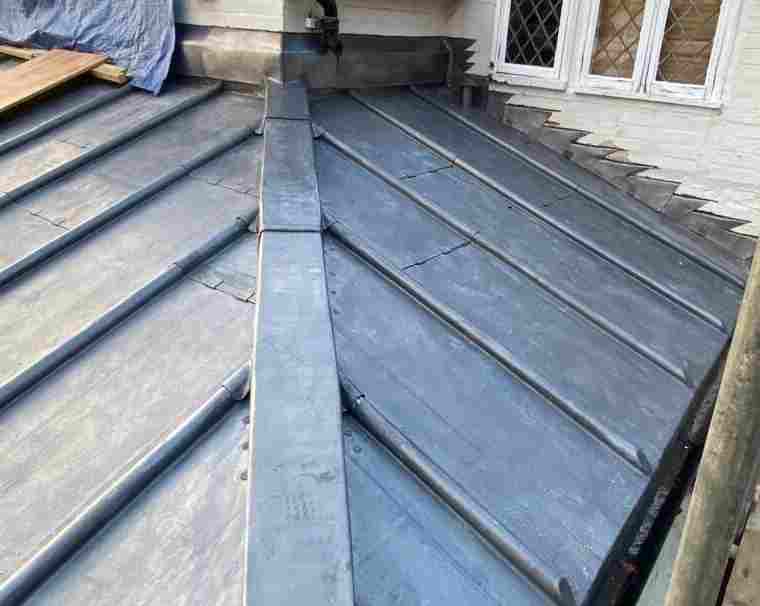
Properties of Lead
Lead possesses unique properties that significantly influence the welding techniques and considerations associated with this metal. Understanding these properties is essential for welders working with lead materials.
Physical Properties
- Melting PointLead has a relatively low melting point compared to many other metals, making it one of the primary challenges in lead welding. Its melting point is approximately 621.5 degrees Fahrenheit (327.5 degrees Celsius). This low melting point requires careful control of temperature during welding to prevent overheating and maintain structural integrity.
- DensityLead is renowned for its high density, which makes it suitable for various applications where mass is required. The density of lead is around 11.34 grams per cubic centimeter, making it effective for radiation shielding and as a ballast material.
- ConductivityWhile lead is not known for its electrical conductivity compared to metals like copper or aluminum, it still exhibits some degree of electrical conductivity. Understanding lead’s electrical properties is important in applications where electrical conductivity is a consideration, such as electrical connectors or certain plumbing systems.
Chemical Properties
- Corrosion ResistanceOne of lead’s notable qualities is its corrosion resistance, particularly to acids and alkalis. This property makes lead a preferred choice for applications where chemical stability is critical, such as in the construction of chemical storage tanks or pipes. Proper welding techniques must be employed to maintain this corrosion resistance, as improper welding can compromise the protective oxide layer on the lead surface.
- Toxicity ConcernsLead is a highly toxic material, and this is a critical consideration in any welding process involving lead. Inhalation or ingestion of lead particles or fumes can lead to severe health issues, including lead poisoning. Welders working with lead must take strict safety precautions, including wearing appropriate personal protective equipment (PPE) and ensuring adequate ventilation in the workspace.
Welding Techniques
Welding lead materials requires a nuanced approach due to the unique properties of lead and the associated safety concerns. This section explores various welding techniques and the considerations involved in welding with lead.
Pre-welding Preparations
- Surface Cleaning and Preparation: Proper surface preparation is critical for successful lead welding. The surfaces to be welded must be clean, free of contaminants, and devoid of any oxides. A wire brush or abrasive material can be used to clean the lead surfaces thoroughly.
- Joint Design and Fit-Up: Joint design and fit-up are essential for achieving strong and durable lead welds. Ensure that the joint is well-aligned and tight-fitting, minimizing gaps or unevenness. Proper joint design can vary depending on the welding technique chosen.
Welding Processes for Lead
- Oxyfuel Welding: Oxyfuel welding is a common method for lead welding. It involves using a combination of oxygen and a fuel gas (typically acetylene) to create a controlled flame. The low melting point of lead makes oxyfuel welding suitable, as it allows precise temperature control to prevent overheating.
- TIG (Tungsten Inert Gas) Welding: TIG welding uses a non-consumable tungsten electrode to create an arc and join lead materials. It offers excellent control over heat input and can be used for intricate welds. Argon gas is typically used as the shielding gas.
- Resistance Welding: Resistance welding is employed in industrial applications for joining lead materials. It utilizes electrical resistance to generate heat at the joint and create the weld. Proper alignment of the lead parts is crucial for successful resistance welding.
Welding Parameters
- Temperature Control: Maintaining precise temperature control is vital when welding lead. This involves adjusting the flame temperature in oxyfuel welding or the current and voltage settings in TIG or resistance welding to keep the lead within its melting range without overheating.
- Electrode Selection: The choice of electrode, particularly in TIG welding, is important. Tungsten electrodes are commonly used for lead welding due to their high melting point and inert nature.
- Welding Current and Voltage: In TIG and resistance welding, the selection of appropriate welding current and voltage settings is critical to achieve the desired weld penetration and quality.
Special Considerations for Lead Welding
- Lead Fumes and Fume Extraction: Lead fumes are highly toxic. Adequate fume extraction and ventilation systems must be in place to remove lead fumes from the work area and protect the health of the welder.
- Avoiding Contamination: It’s essential to prevent contamination of lead materials with other metals, as this can weaken the weld and compromise its integrity.
- Post-Welding Inspections: After welding, inspect the welds for quality, including checking for defects such as cracks, porosity, or incomplete fusion. Any substandard welds should be repaired promptly.
Common Applications of Lead Welding
Lead welding, with its specialized techniques, plays a significant role in various industries and sectors due to the unique properties of lead. In this section, we explore the common industries that rely on lead welding and provide examples of specific applications within these sectors.
Industries and Sectors that Use Lead Welding
Lead welding finds extensive use in the following industries and sectors:
- Battery Manufacturing: Lead-acid batteries are a staple in automotive, industrial, and backup power systems. Lead welding is pivotal in battery manufacturing, ensuring secure connections between battery plates and terminals, which is essential for reliable electrical performance.
- Construction: The construction industry utilizes lead welding, particularly in applications involving lead sheets or lead-coated materials. Examples include roofing, flashing, and waterproofing systems, where lead’s malleability and corrosion resistance make it a preferred choice.
- Medical Equipment: In the healthcare sector, lead welding is crucial for manufacturing medical equipment that requires radiation shielding. Devices like X-ray machines and radiation therapy equipment depend on lead-lined rooms and barriers assembled using lead welding techniques to provide effective radiation protection.
- Chemical Processing: Chemical plants and facilities rely on lead welding for the fabrication of chemical storage tanks, pipes, and containers. Lead’s resistance to corrosion and chemicals makes it an ideal choice for safely storing and transporting hazardous substances.
Examples of Lead Welding Applications
- Battery Manufacturing: Lead welding is fundamental in battery manufacturing processes. It is used to join lead plates to connectors, ensuring a secure and efficient electrical connection. This is essential for the proper functioning of lead-acid batteries, which power a wide range of devices and vehicles.
- Radiation Shielding: Lead serves as a primary material for radiation shielding, protecting workers and patients from harmful ionizing radiation in medical and industrial settings. Lead welding plays a pivotal role in assembling lead sheets and panels into shielding structures that effectively block radiation.
- Plumbing: Lead has a historical presence in plumbing, particularly for joining pipes and fittings. Although its use in plumbing has diminished due to health concerns, older plumbing systems may still require maintenance and repairs that involve lead welding. Modern plumbing systems primarily use alternative materials.
- Roofing and Flashing: Lead flashing and roofing applications benefit greatly from lead welding techniques. Welding lead sheets together or to other materials ensures a watertight seal, making lead a preferred choice for weatherproofing in the construction industry.
- Chemical Containers: Lead welding is employed in the fabrication of chemical containers, tanks, and pipelines used in the chemical industry. The resistance of lead to corrosive chemicals and its malleability make it a suitable choice for containing and transporting hazardous substances.
Safety Considerations for Lead Welding
Welding with lead demands rigorous safety precautions due to the toxic nature of lead fumes and the associated health risks. In this section, we delve into the critical safety considerations that must be observed when working with lead materials.
Health Hazards Associated with Lead
Lead welding presents specific health hazards, including:
- Lead Poisoning: The primary health risk linked to lead exposure is lead poisoning. Inhalation or ingestion of lead particles or fumes can result in lead poisoning, which can manifest in symptoms such as fatigue, nausea, abdominal pain, and neurological issues. Chronic exposure can lead to severe health problems, underscoring the importance of minimizing exposure through stringent safety measures.
- Respiratory Issues: Inhaling lead fumes can cause respiratory problems, including coughing, wheezing, and reduced lung function. Long-term exposure may lead to chronic respiratory conditions, emphasizing the need for effective fume control.
- Reproductive and Developmental Effects: Lead exposure can harm the reproductive system and cause developmental issues in fetuses. Pregnant women and individuals planning to start a family should exercise extra caution when working with lead.
Personal Protective Equipment (PPE)
To mitigate the health risks associated with lead exposure, welders should don appropriate personal protective equipment (PPE):
- Respirators: High-efficiency particulate air (HEPA) respirators or supplied-air respirators are essential to protect against inhaling lead fumes and particles. The choice of respirator should match the level of exposure and the specific welding process.
- Protective Clothing: Welders should wear full-body protective clothing, including coveralls and gloves, to prevent skin contact with lead dust or materials. The clothing should be designed to resist penetration by lead particles.
- Eye and Face Protection: Safety goggles or a face shield should be worn to safeguard the eyes and face from lead particles and potential splatter during welding.
- Footwear: Sturdy, closed-toe shoes or boots should be worn to protect the feet from falling objects or lead materials.
Ventilation and Containment Measures
Proper ventilation and containment measures are crucial in lead welding to prevent the dispersion of lead fumes and particles:
- Local Exhaust Ventilation (LEV): Implement local exhaust ventilation systems equipped with hoods and ducts to capture and remove lead fumes at the source. These systems should be regularly inspected and maintained for optimal performance.
- General Ventilation: Ensure adequate general ventilation in the welding area to dilute and remove airborne contaminants. Proper air exchange rates and airflow should be maintained.
- Containment: Lead welding should ideally take place within enclosed spaces or enclosures designed to contain lead fumes and particles. These enclosures should be properly sealed to prevent leaks.
- Regular Cleaning: Implement regular cleaning protocols to remove lead dust and residues from the work area. Cleaning should be performed using methods that minimize the generation of airborne particles.
- Waste Disposal: Dispose of lead-contaminated materials and waste in accordance with local regulations. Proper waste management is crucial to prevent environmental contamination.
Common Challenges in Lead Welding
Welding with lead can be complex and presents specific challenges due to the unique properties of lead and the associated health and safety concerns. In this section, we explore common welding defects, their causes, how to address these issues, and methods for preventing contamination and porosity in lead welding.
Welding Defects and Their Causes
Welding defects can compromise the integrity and quality of lead welds. Here are some common defects and their causes:
- Cracks: Cracks in lead welds can occur due to rapid cooling or uneven heating during the welding process. Additionally, contamination or impurities in the lead material can contribute to cracking.
- Porosity: Porosity in lead welds appears as small, round voids or holes within the weld. It is often caused by gas entrapment, such as hydrogen, during the welding process. Contaminated filler materials or insufficient shielding gas can also lead to porosity.
- Incomplete Fusion: Incomplete fusion occurs when the filler material does not fuse completely with the base metal. This defect can result from inadequate heat input or poor joint fit-up.
- Excessive Spatter: Excessive spatter, the expulsion of molten metal droplets, can occur due to improper welding parameters or contaminated materials.
How to Address Common Welding Issues
Addressing common welding issues in lead welding requires a systematic approach:
- Cracks: To address cracks, ensure proper preheat and post-weld heat treatment. Verify that the welding parameters are appropriate for lead’s low melting point. Contaminated lead materials should be avoided, and joint preparation should be thorough.
- Porosity: Preventing porosity involves using clean filler materials and maintaining a pure shielding gas atmosphere. Proper welding techniques, including ensuring adequate gas coverage and adjusting welding parameters, can help reduce porosity.
- Incomplete Fusion: To correct incomplete fusion, improve joint fit-up to ensure proper contact between the base metals. Adjust welding parameters to ensure sufficient heat input for complete fusion.
- Excessive Spatter: Excessive spatter can be minimized by selecting the right welding parameters, such as adjusting current and voltage settings. Ensure that welding surfaces are clean and free of contaminants.
Preventing Contamination and Porosity
Preventing contamination and porosity is critical in lead welding to achieve high-quality welds:
- Cleanliness: Keep all materials, surfaces, and equipment clean and free of contaminants. Use clean filler materials and ensure that the welding area is free from dust, grease, and other foreign substances.
- Gas Quality: Maintain the purity of shielding gases, such as argon for TIG welding. Regularly inspect gas cylinders and replace them when necessary to prevent gas contamination.
- Welding Parameters: Select and adjust welding parameters carefully to match the specific requirements of lead welding. Pay attention to heat input, electrode selection, and gas flow rates.
- Joint Preparation: Properly prepare the joint by cleaning and aligning the lead materials. Adequate joint fit-up ensures a strong and consistent weld.
- Training and Skill Development: Welders should receive comprehensive training in lead welding techniques, troubleshooting, and defect prevention. Skilled welders are better equipped to address challenges effectively.
FAQs
Can I use a regular soldering iron for lead welding?
It’s recommended to use a soldering iron specifically designed for lead welding to ensure optimal results and safety.
Is lead welding safe for stained glass projects?
Yes, lead welding is a common technique used in stained glass projects. Ensure proper ventilation and safety precautions when working with lead materials.
What safety measures should I take when welding lead?
Always wear appropriate safety gear, work in a well-ventilated area, and have a fire extinguisher nearby. Additionally, wash your hands thoroughly after handling lead.
Can I weld lead in outdoor conditions?
While it’s possible to weld lead outdoors, it’s advisable to work in a controlled indoor environment to maintain better control over the welding process.
How do I prevent overheating while welding lead?
Gradually apply heat and avoid concentrating it in one area. This will help prevent overheating and potential damage to the lead.
Are there any environmentally friendly alternatives to lead solder?
Yes, there are lead-free solder options available that are more environmentally friendly. Consider using these alternatives when appropriate.
Conclusion
Mastering welding techniques for lead is a valuable skill that opens doors to various industries and projects. By following the steps outlined in this guide and practicing diligently, you can become a proficient lead welder. Remember to prioritize safety, cleanliness, and attention to detail in your lead welding endeavors.