Shielding Gas for MIG Welding
Introduction
MIG welding, also known as Gas Metal Arc Welding (GMAW), is a widely used welding process in industrial and fabrication settings. It involves the use of a consumable electrode wire, which is continuously fed through a welding gun. The arc generated between the electrode wire and the workpiece melts both the wire and the base metal, creating a strong weld joint. One critical aspect of MIG welding is the use of shielding gas, which plays a vital role in ensuring the quality and integrity of the weld.
Definition of MIG Welding
MIG welding is a semi-automatic or automatic welding process that utilizes a consumable electrode wire and an inert or active shielding gas to protect the weld area from atmospheric contamination. The electrode wire is continuously fed through a welding gun, where it is melted and deposited onto the workpiece, forming the weld bead.
Importance of Shielding Gas in MIG Welding Process
Shielding gas is indispensable in the MIG welding process for several reasons. Firstly, it serves to protect the weld pool and the molten metal from atmospheric gases such as oxygen, nitrogen, and hydrogen, which can cause weld defects such as porosity, brittleness, and oxidation. Secondly, shielding gas helps stabilize the arc, ensuring smooth and consistent weld bead formation. Additionally, it influences the characteristics of the weld, including penetration depth, bead profile, and spatter formation. In essence, the quality and effectiveness of the shielding gas directly impact the overall success of the MIG welding operation.
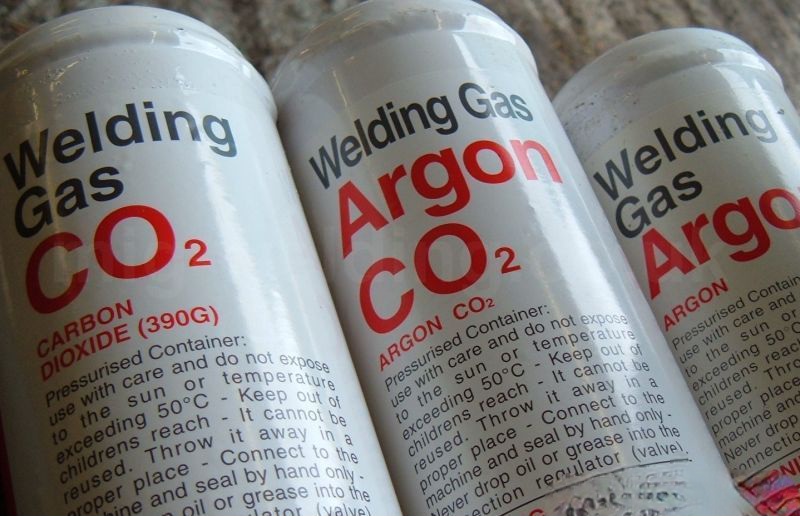
Role of Shielding Gas
Definition and Function of Shielding Gas
Shielding gas is a vital component of the MIG welding process, serving to protect the weld area from atmospheric contamination during welding. It creates a shield or barrier around the arc and the molten weld pool, displacing air and preventing reactions with atmospheric gases such as oxygen, nitrogen, and hydrogen. By shielding the weld area, the gas helps maintain the integrity and quality of the weld, reducing the likelihood of defects and ensuring strong, durable weld joints.
Protection of Weld Pool and Electrode Wire
Shielding gas plays a crucial role in protecting both the molten weld pool and the electrode wire during the welding process. By enveloping the weld area, the gas prevents atmospheric gases from coming into contact with the molten metal, reducing the risk of weld defects such as porosity, undercutting, and spatter. Additionally, shielding gas helps prevent oxidation of the electrode wire, ensuring smooth and consistent wire feed and stable arc performance.
Influence on Weld Bead Characteristics
The type and composition of shielding gas used in MIG welding can significantly influence the characteristics of the weld bead. Different gases have varying effects on weld penetration, bead profile, and overall weld quality. For example, inert gases such as argon are commonly used for welding non-ferrous metals like aluminum and stainless steel, producing clean and aesthetically pleasing welds with minimal spatter. On the other hand, active gases like carbon dioxide (CO2) are often used for welding carbon steels, providing deeper penetration and faster welding speeds. The selection of shielding gas depends on factors such as the material being welded, desired weld characteristics, and specific welding requirements.
Types of Shielding Gases
- Inert Gases: Inert gases are chemically stable and do not react with the molten metal or surrounding atmosphere during welding. They are commonly used as shielding gases in MIG welding applications where minimal reactivity and excellent arc stability are desired. Argon is the most widely used inert gas in MIG welding, particularly for welding non-ferrous metals such as aluminum, magnesium, and titanium.
- Active Gases: Active gases, also known as reactive gases, contain reactive elements such as oxygen, carbon dioxide, or hydrogen. These gases can influence weld characteristics by altering arc stability, penetration depth, and weld bead appearance. Carbon dioxide (CO2) is a commonly used active gas in MIG welding, particularly for welding carbon steels. It provides deeper penetration and higher welding speeds compared to inert gases.
- Mixed Gases: Mixed gases combine inert and active gases in various proportions to achieve desired welding outcomes. These gas mixtures offer a balance of arc stability, penetration, and weld bead appearance, making them suitable for a wide range of welding applications. Common mixed gases include argon-CO2 blends, which are widely used for welding carbon steels and low-alloy steels, offering a compromise between the benefits of inert and active gases.
Common Shielding Gases Used in MIG Welding
Argon
- Properties:
- Argon is an inert gas, colorless, odorless, and non-reactive.
- It has a higher atomic weight than other shielding gases, providing excellent arc stability.
- Argon is heavier than air, which helps create a stable shield around the weld area.
- It is typically used in pure form or as a component of gas mixtures for MIG welding applications.
- Applications:
- Argon is commonly used for welding non-ferrous metals such as aluminum, magnesium, and titanium.
- It produces clean and aesthetically pleasing welds with minimal spatter.
- Argon shielding gas is suitable for applications requiring precise control over weld bead appearance and quality, such as automotive, aerospace, and architectural fabrication.
Carbon Dioxide (CO2)
- Properties:
- Carbon dioxide (CO2) is an active gas, colorless, and odorless.
- It is readily available, cost-effective, and commonly used in MIG welding applications.
- CO2 provides deeper penetration and higher welding speeds compared to inert gases.
- It can increase the risk of weld spatter and produce a more turbulent arc compared to inert gases.
- Applications:
- CO2 is primarily used for welding carbon steels and low-alloy steels in industries such as construction, shipbuilding, and structural fabrication.
- It is suitable for applications where higher welding speeds and increased productivity are desired.
- CO2 shielding gas is often used in combination with other gases or as part of gas mixtures to improve arc stability and weld quality.
Argon-CO2 Mixtures
- Properties:
- Argon-CO2 mixtures combine the benefits of both inert and active gases.
- These mixtures offer a balance of arc stability, penetration, and weld bead appearance.
- The ratio of argon to CO2 can be adjusted to meet specific welding requirements and achieve desired welding outcomes.
- Argon-CO2 mixtures are available in various compositions, with common blends including 75% argon and 25% CO2, or 80% argon and 20% CO2.
- Applications:
- Argon-CO2 mixtures are widely used for welding carbon steels and low-alloy steels in a variety of industrial applications.
- These mixtures provide improved arc stability compared to pure CO2, resulting in reduced spatter and improved weld quality.
- Argon-CO2 shielding gas blends are suitable for both manual and automated welding processes, offering versatility and flexibility in various welding environments.
Selection Criteria for Shielding Gas
Material Being Welded
- The type of material being welded is a crucial factor in determining the appropriate shielding gas. Different metals and alloys require specific shielding gases to achieve optimal weld quality and performance.
- For example, non-ferrous metals such as aluminum, magnesium, and titanium typically require inert gases like argon due to their high reactivity with oxygen and other atmospheric gases.
- Carbon steels and low-alloy steels, on the other hand, are commonly welded using active gases like carbon dioxide (CO2) or argon-CO2 mixtures to achieve adequate penetration and weld strength.
Welding Parameters
- Welding parameters, including voltage, current, wire feed speed, and travel speed, play a significant role in determining the appropriate shielding gas for MIG welding.
- Higher welding currents and faster travel speeds may necessitate the use of active gases like CO2 to achieve deeper penetration and faster welding speeds.
- Conversely, lower welding currents and slower travel speeds may benefit from inert gases like argon to maintain arc stability and minimize spatter.
Desired Weld Characteristics
- The desired weld characteristics, such as weld bead appearance, penetration depth, and mechanical properties, influence the selection of shielding gas.
- For applications requiring clean and aesthetically pleasing welds with minimal spatter, inert gases like argon are preferred.
- Applications that prioritize deeper penetration, higher welding speeds, or specific mechanical properties may benefit from active gases like CO2 or argon-CO2 mixtures.
Cost Considerations
- Cost considerations are essential when selecting shielding gas for MIG welding, as different gases have varying prices and availability.
- In general, inert gases like argon tend to be more expensive than active gases like CO2. However, the overall cost-effectiveness of the shielding gas depends on factors such as weld quality, productivity, and material savings.
- While inert gases may incur higher initial costs, they can result in lower overall welding costs by reducing the need for post-weld cleaning, rework, and material waste.
Gas Flow and Delivery Systems
Gas Flow Rates
- Gas flow rates refer to the rate at which shielding gas is delivered to the welding torch during MIG welding.
- The appropriate gas flow rate is essential for maintaining an adequate shield around the weld area and ensuring proper protection against atmospheric contamination.
- The optimal gas flow rate depends on factors such as welding parameters, torch configuration, and shielding gas type.
- Typical gas flow rates for MIG welding range from 15 to 30 cubic feet per hour (CFH), but specific recommendations may vary based on welding conditions and equipment manufacturer guidelines.
Gas Delivery Methods
- Gas Cylinders:
- Gas cylinders are commonly used to store and transport shielding gases for MIG welding.
- The cylinders are typically made of steel or aluminum and come in various sizes ranging from small portable cylinders to large industrial cylinders.
- The cylinders are filled with compressed shielding gas at high pressure and equipped with valves for regulating gas flow.
- Proper handling and storage of gas cylinders are essential to ensure safety and prevent accidents.
- Gas Flow Regulators:
- Gas flow regulators are devices used to control and regulate the flow of shielding gas from the cylinder to the welding torch.
- The regulator attaches to the gas cylinder valve and reduces the high-pressure gas to a lower, more manageable flow rate suitable for welding.
- It typically consists of a pressure gauge to indicate the gas pressure inside the cylinder and an adjustment knob to set the desired gas flow rate.
- Gas flow regulators ensure consistent and precise control over shielding gas delivery, contributing to stable arc performance and weld quality.
- Gas Hoses and Fittings:
- Gas hoses and fittings are used to connect the gas cylinder, regulator, and welding torch in the gas delivery system.
- Hoses are typically made of durable materials such as rubber or thermoplastic and are designed to withstand the high-pressure flow of shielding gas.
- Fittings, such as couplings, adapters, and connectors, facilitate the secure attachment of hoses to the gas cylinder, regulator, and torch.
- Proper installation and maintenance of gas hoses and fittings are essential to prevent gas leaks and ensure the integrity of the gas delivery system.
Best Practices for Shielding Gas Usage
Proper Gas Selection
- Proper gas selection is crucial for achieving high-quality welds in MIG welding applications.
- Consider the material being welded, welding process parameters, and desired weld characteristics when selecting the appropriate shielding gas.
- Consult with welding procedure specifications (WPS) or material manufacturer recommendations to determine the most suitable shielding gas for the specific welding application.
- Evaluate the properties and characteristics of different shielding gases, such as inert gases (e.g., argon) or active gases (e.g., CO2), to choose the gas that best meets the requirements of the welding process.
Correct Gas Flow Settings
- Correct gas flow settings are essential for maintaining an adequate shield around the weld area and ensuring proper protection against atmospheric contamination.
- Follow equipment manufacturer guidelines and welding procedure specifications to determine the recommended gas flow rate for the specific welding application.
- Adjust the gas flow rate using the gas flow regulator to achieve the optimal flow rate based on welding parameters, torch configuration, and shielding gas type.
- Monitor gas flow during welding operations and make adjustments as necessary to maintain consistent and uniform gas coverage over the weld area.
Maintenance of Gas Delivery System
- Regular maintenance of the gas delivery system is essential to ensure reliable and efficient shielding gas delivery during welding operations.
- Inspect gas cylinders, regulators, hoses, and fittings for signs of damage, corrosion, or wear and tear.
- Replace damaged or worn components as needed to prevent gas leaks and ensure the integrity of the gas delivery system.
- Keep gas cylinders securely fastened and stored in well-ventilated areas away from heat sources, flames, or electrical equipment.
- Clean and purge gas hoses and fittings regularly to remove any contaminants or debris that could affect gas flow and compromise weld quality.
Monitoring Gas Purity
- Monitoring gas purity is essential for ensuring the quality and effectiveness of shielding gas during MIG welding.
- Use gas purity analyzers or gas detectors to periodically test the purity and composition of shielding gases.
- Verify that the shielding gas meets industry standards and specifications for purity levels, such as American Welding Society (AWS) or International Organization for Standardization (ISO) guidelines.
- Replace gas cylinders or refill them with fresh gas as needed to maintain consistent gas purity and quality.
- Keep records of gas cylinder usage, refills, and purity tests to track gas consumption and ensure compliance with welding procedure requirements.
Troubleshooting Shielding Gas Issues
Common Problems with Shielding Gas
- Gas Leaks: Leakage from damaged hoses, fittings, or connections can result in inadequate gas coverage, leading to weld defects such as porosity and incomplete fusion.
- Gas Contamination: Contamination of shielding gas with atmospheric gases or foreign particles can cause weld defects such as porosity, spatter, and poor bead appearance.
- Improper Gas Flow: Incorrect gas flow settings can result in insufficient or excessive shielding gas coverage, affecting weld quality and performance.
- Gas Cylinder Depletion: Running out of shielding gas during welding can interrupt the welding process and result in incomplete welds or discontinuities.
- Gas Purity Issues: Inconsistent gas purity levels or contamination with impurities can impact weld quality and consistency.
Identification and Resolution of Gas-Related Welding Defects
- Porosity: Identify porosity, which appears as small holes or voids in the weld bead. Resolve by checking for gas leaks, ensuring proper gas flow settings, and maintaining gas purity.
- Incomplete Fusion: Detect incomplete fusion, where the weld fails to fully penetrate and fuse with the base metal. Correct by adjusting gas flow rates, increasing welding parameters, and improving joint preparation.
- Excessive Spatter: Address excessive spatter, which results in unwanted metal droplets around the weld area. Resolve by optimizing gas flow settings, adjusting welding parameters, and cleaning or replacing consumables.
- Inconsistent Bead Appearance: Notice inconsistencies in weld bead appearance, such as unevenness or irregularities. Rectify by ensuring proper gas coverage, optimizing welding parameters, and maintaining consistent travel speed and torch angle.
- Weld Discontinuities: Identify weld discontinuities, including cracks, lack of fusion, or undercutting. Resolve by inspecting gas delivery system components, verifying gas purity, and optimizing welding techniques.
Prevention Techniques
- Regular Maintenance: Conduct regular maintenance of gas delivery system components, including hoses, fittings, regulators, and torches, to prevent gas leaks and contamination.
- Proper Handling: Handle gas cylinders with care, ensuring they are stored upright, secured, and protected from physical damage or exposure to extreme temperatures.
- Quality Control: Implement quality control measures to monitor gas purity levels, verify gas cylinder contents, and perform periodic gas purity testing.
- Training and Education: Provide comprehensive training and education to welding operators on proper gas selection, handling, and troubleshooting techniques to prevent and address gas-related welding issues effectively.
- Documentation and Record-Keeping: Maintain accurate records of gas cylinder usage, refills, inspections, and maintenance activities to track gas consumption and ensure compliance with safety and quality standards.
FAQs
What is the primary purpose of shielding gas in MIG welding?
The primary purpose of shielding gas is to protect the weld area from atmospheric contamination, such as oxidation and impurities.
How do I choose the right shielding gas for my welding application?
The choice of shielding gas depends on factors such as the type of metal being welded, the welding process, and cost considerations. Consult with welding experts or refer to welding guidelines for specific recommendations.
What are the advantages of using inert gases like argon in MIG welding?
Inert gases like argon provide excellent arc stability and are suitable for welding non-ferrous metals like aluminum. They also help minimize spatter and produce clean, aesthetically pleasing welds.
Can I mix different shielding gases together?
Yes, mixed gas blends are commonly used in MIG welding to combine the benefits of different gases, such as improved arc characteristics and penetration.
How can I reduce the environmental impact of shielding gases?
To reduce environmental impact, consider using greener alternatives, recycling and reusing gases whenever possible, and implementing efficient gas management practices.
Conclusion
In conclusion, shielding gas remains an indispensable component of MIG welding, playing a vital role in ensuring high-quality welds and achieving optimal welding performance. By embracing advancements in shielding gas technology and adhering to best practices, welding industries can meet the evolving demands of modern manufacturing while contributing to a more sustainable and efficient future.