What is Plasma Welding?
Plasma welding is an advanced and highly precise welding process that utilizes the unique properties of plasma, a state of matter similar to gas but with ionized particles, to create a concentrated arc for welding. This process is often employed in industries where precision and control are paramount, such as aerospace, electronics, and specialized manufacturing. In this comprehensive guide, we delve into the intricacies of plasma welding, exploring its working principles, advantages, applications, and how it compares to other welding techniques.
Understanding Plasma Welding
The Plasma State
Before we delve into the plasma arc welding process, it’s essential to understand what plasma is. Plasma is often referred to as the fourth state of matter, distinct from solid, liquid, and gas. When a gas is heated to extremely high temperatures, its atoms gain enough energy to ionize, creating a mixture of charged particles—electrons and ions. This ionized state is what we refer to as plasma. Plasma is highly conductive and can be manipulated with electromagnetic fields, making it ideal for welding applications.
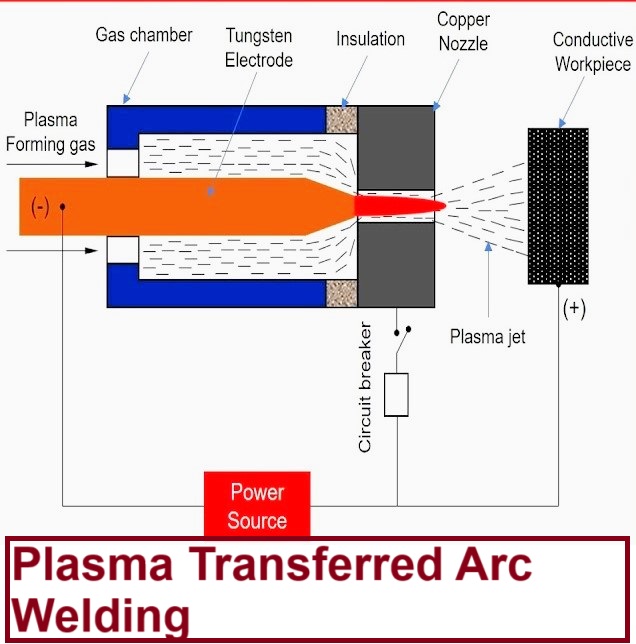
How Plasma Welding Works
In plasma arc welding (PAW), a plasma arc is generated between a tungsten electrode and the workpiece. The plasma is forced through a fine-bore copper nozzle, which constricts the arc and increases its temperature and intensity. This results in a highly concentrated and stable arc that is capable of welding with exceptional precision.
The welding process can be categorized into two main types:
- Transferred Arc Plasma Welding: In this mode, the plasma arc is established between the electrode and the workpiece. This type of arc provides deep penetration and is typically used for thicker materials.
- Non-Transferred Arc Plasma Welding: Here, the arc is formed between the electrode and the nozzle, and the plasma is then directed toward the workpiece. This mode is used for applications requiring lower heat input and is ideal for thinner materials.
Types of Plasma Welding
Plasma arc welding isn’t a one-size-fits-all process. Depending on the application and material, different types of plasma welding can be employed.
Micro Plasma Welding
This type is used for welding thin materials, typically between 0.1 to 1.5 mm in thickness. It offers high precision, making it ideal for delicate tasks such as electronic component manufacturing.
Medium Current Plasma Welding
This method is suited for materials that are slightly thicker, ranging from 1.5 to 6 mm. It’s a versatile approach used in various industries, including automotive and general fabrication.
Keyhole Plasma Welding
For welding thicker materials, keyhole plasma welding is the go-to method. It creates a keyhole in the workpiece, which allows for deeper weld penetration. This type is commonly used in the aerospace industry for joining high-strength materials.
Equipment and Materials
To perform plasma welding, specialized equipment and materials are required:
Plasma Welding Machines
These machines are the heart of the operation, providing the necessary power and control to generate the plasma arc. Advanced models come with features like automated controls, making the process more efficient.
Electrodes and Nozzles
Tungsten electrodes are commonly used due to their high melting point. The nozzle, typically made of copper, constricts the arc and focuses the plasma jet.
Shielding Gas and Filler Materials
Argon is the most commonly used shielding gas, though helium and hydrogen may also be used depending on the material being welded. Filler materials are selected based on the base material and the desired properties of the weld.
Advantages of Plasma Welding
Precision and Control
One of the most significant advantages of plasma arc welding is its precision. The constricted arc allows for pinpoint accuracy, making it ideal for applications where tolerance is critical. This precision reduces the risk of defects and ensures high-quality welds.
Versatility
Plasma welding can be used on a wide range of materials, including stainless steel, titanium, and aluminum. Its versatility extends to the thickness of the materials as well, allowing for welding of both thin sheets and thicker components.
Higher Weld Quality
The concentrated heat of the plasma arc results in deeper penetration with less heat input to the surrounding material. This reduces distortion and the heat-affected zone (HAZ), leading to a cleaner, stronger weld.
Automation Compatibility
Plasma welding is well-suited for automation, which is crucial for industries that require consistent and repeatable welds. Automated plasma welding systems can significantly increase productivity while maintaining high standards of quality.
Applications of Plasma Welding
Aerospace Industry
In the aerospace sector, plasma arc welding is employed for its ability to produce precise and reliable welds on high-strength, lightweight materials such as titanium and aluminum alloys. Components such as fuel tanks, engine parts, and structural elements benefit from the accuracy and quality of plasma welding.
Electronics Manufacturing
The electronics industry requires welding techniques that minimize heat input and prevent damage to delicate components. Plasma welding’s precision and ability to control heat make it ideal for assembling electronic devices, where even minor defects can lead to significant issues.
Medical Device Fabrication
Medical devices often require complex welds on small, intricate parts. Plasma welding is favored in this field due to its ability to create clean, high-quality welds with minimal thermal distortion, ensuring the integrity and functionality of medical components.
Automotive Industry
Plasma welding is used in the automotive industry for joining thin sheet metals, particularly in exhaust systems, fuel tanks, and other components where corrosion resistance and strength are critical.
Comparison with Other Welding Techniques
To fully appreciate plasma arc welding, it’s helpful to compare it with other common welding methods:
Plasma Welding vs. TIG Welding
Both techniques use a tungsten electrode, but plasma welding offers greater control and is better suited for deeper penetration. TIG welding, on the other hand, is simpler and more widely used, especially for thinner materials.
Plasma Welding vs. MIG Welding
MIG welding is faster and easier to learn, making it popular for general fabrication. However, plasma welding offers superior precision and is better for specialized applications.
Plasma Welding vs. Laser Welding
Laser welding is another high-precision technique, but it’s typically more expensive than plasma welding. Laser welding also has limitations in terms of the materials it can handle, whereas plasma welding is more versatile.
Challenges and Considerations
Cost of Equipment
One of the primary challenges associated with plasma welding is the cost of equipment. Plasma welding systems tend to be more expensive than traditional welding setups, which can be a barrier for small-scale operations.
Skill Level Required
Operating a plasma welding system requires a higher skill level than more conventional welding techniques. Welders must be trained in handling the equipment and understanding the nuances of the process to achieve optimal results.
Maintenance
The precision components of a plasma welding system, such as the torch and nozzle, require regular maintenance to ensure consistent performance. This includes replacing worn-out parts and ensuring that the cooling system is functioning correctly.
FAQs
What materials can be welded using plasma arc welding?
Plasma welding is suitable for a wide range of materials, including stainless steel, aluminum, titanium, and high-strength alloys.
How does plasma welding differ from TIG welding?
Plasma welding offers greater control and deeper penetration than TIG welding, making it better suited for thicker materials and precision applications.
What are the safety precautions for plasma arc welding?
Safety precautions include wearing protective gear such as gloves, welding helmets with appropriate filters, and ensuring proper ventilation to avoid inhaling harmful fumes.
Can plasma welding be automated?
Yes, plasma welding can be automated, which increases consistency and efficiency, particularly in large-scale manufacturing environments.
What are the maintenance requirements for plasma welding equipment?
Regular maintenance includes checking and replacing worn electrodes and nozzles, ensuring proper gas flow, and inspecting electrical connections for wear and tear.
Conclusion
Plasma welding stands out as a superior welding technique for applications requiring precision, control, and high weld quality. Its versatility across various industries, from aerospace to electronics, demonstrates its value in modern manufacturing. While the initial investment and skill requirements may be higher, the long-term benefits of plasma welding—such as reduced defects, faster production times, and compatibility with automation—make it a worthwhile choice for advanced welding needs.