Welding Burn-Through
Introduction to Welding Defects
Welding is a crucial process in numerous industries, ensuring the strength and integrity of structures and machinery. However, as with any technical process, there is always room for error, and in welding, these errors manifest as defects. Welding defects can significantly impact the quality and safety of a weld, leading to potential failures if not addressed properly. Among these defects, burn-through or excessive heat input, which is visibly represented in the image you shared, is one of the more concerning issues.
This article delves into the specifics of burn-through, how it occurs, its causes, and steps to avoid it. We’ll also touch on the broader topic of welding defects and how they can be managed or repaired to ensure a structurally sound and reliable weld.
Understanding Welding Burn-Through
What is Burn-Through?
Burn-through occurs when too much heat is applied to a weld, causing the base material to melt excessively and resulting in a hole or weak point in the joint. This typically happens when the welder loses control of the weld pool, allowing the molten metal to become too fluid and over-penetrating the joint. The molten pool burns through the metal, creating a hole or significant thinning of the material that compromises the integrity of the weld.
Burn-through is especially common when welding thinner materials or using processes that generate a lot of heat, such as Gas Tungsten Arc Welding (GTAW), Gas Metal Arc Welding (GMAW), or shielded metal arc welding (SMAW). In thicker materials, burn-through can also happen if poor welding techniques or excessive current settings are used.
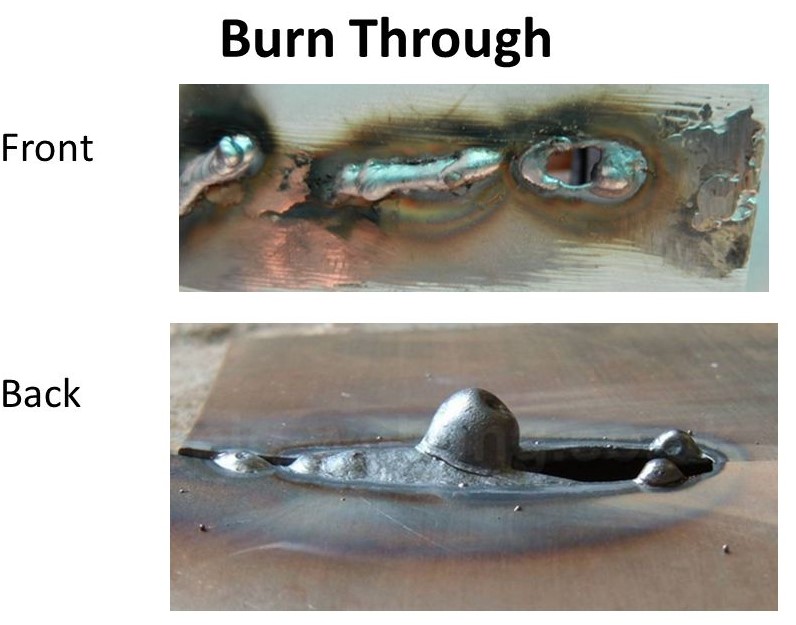
Key Characteristics of Burn-Through:
- Visible hole or thinning in the welded joint.
- Excessively large molten pool.
- High heat input.
- Weak point in the weld, often leading to a failed weld test.
Burn-through not only reduces the strength of the weld but also creates a significant weak point that can lead to cracking, material failure, and ultimately, catastrophic failure of the structure or component.
Causes of Burn-Through in Welding
Understanding the root causes of burn-through is essential for preventing this defect. Several factors can contribute to burn-through, including improper technique, incorrect settings on the welding machine, or issues with the material being welded.
- Excessive Heat Input: The most common cause of burn-through is applying too much heat to the workpiece. This occurs when the amperage or voltage settings on the welding machine are too high for the material thickness, leading to over-penetration and melting of the base material.
- Incorrect Travel Speed: When the travel speed is too slow, the welding torch or electrode lingers too long in one spot, allowing too much heat to build up in the weld pool. This excess heat melts the base metal, resulting in burn-through. Conversely, moving too fast can also cause issues, such as lack of fusion, but it’s the slow travel speed that often contributes to burn-through.
- Poor Joint Design: Joint preparation and design play a crucial role in preventing burn-through. If the gap between the materials being welded is too wide, there is insufficient support for the molten pool, making it easier for the weld to burn through. Ensuring proper joint fit-up and alignment is essential, especially when working with thinner materials.
- Inappropriate Electrode or Filler Material: Using an electrode or filler material that is too large or inappropriate for the base material can increase the risk of burn-through. Overloading the weld pool with too much filler material at once can also overwhelm the base material and lead to excess heat.
- Welding Thin Materials: Thin materials are especially prone to burn-through because they cannot withstand as much heat as thicker materials. Proper technique, lower heat settings, and faster travel speeds are critical when welding thin metals to avoid this defect.
- Improper Gas Shielding: In processes like GTAW or GMAW, the shielding gas plays a crucial role in protecting the weld pool from contaminants. If the shielding gas flow is too high or too low, it can affect the stability of the arc, leading to inconsistent heat input and, in some cases, burn-through.
Effects of Burn-Through on Weld Integrity
Burn-through can have severe consequences for the overall integrity of a welded joint. The weakened section where the burn-through occurred often becomes the starting point for cracks or fractures. Additionally, because the base material has been excessively thinned, it is more likely to fail under load or stress.
In critical applications, such as pressure vessels, pipelines, or structural components in construction, even a small instance of burn-through can result in catastrophic failure. That’s why it’s essential to properly inspect and test welds to ensure that defects like burn-through are detected and repaired before the component is put into service.
Preventing Burn-Through
Preventing burn-through requires a combination of proper technique, machine settings, and an understanding of the material being welded. Here are several steps that welders can take to avoid burn-through:
- Use Proper Heat Settings: One of the most effective ways to prevent burn-through is to ensure that the welding machine is set to the correct amperage or voltage for the material thickness. Lowering the heat input is especially important when welding thinner materials.
- Increase Travel Speed: Keeping a consistent and appropriate travel speed helps to distribute heat evenly along the weld joint. This reduces the risk of excess heat building up in one spot and burning through the base material.
- Improve Joint Design and Fit-Up: Ensuring that the joint is properly prepared and fitted can reduce the risk of burn-through. Tight joint fit-up is especially important when working with thin materials or when performing full-penetration welds.
- Use a Backing Bar or Chill Block: When welding thin materials, using a backing bar or chill block can help to absorb excess heat and prevent burn-through. These accessories provide support to the molten pool and help to dissipate heat away from the weld area.
- Use Smaller Electrodes or Filler Material: Using a smaller diameter electrode or less filler material reduces the amount of heat generated in the weld pool, making it less likely to burn through the base material.
- Choose the Right Shielding Gas: Ensure that the shielding gas flow rate is set correctly and that the gas is appropriate for the welding process being used. Proper gas flow can help maintain a stable arc and prevent fluctuations in heat input.
Repairing Burn-Through
If burn-through does occur during welding, it’s essential to repair the defect before proceeding. Depending on the severity of the burn-through and the requirements of the application, several methods can be used to fix the issue:
- Filling the Hole: For small instances of burn-through, the defect can be repaired by filling the hole with additional weld passes. This method works best when the burn-through is relatively minor and doesn’t significantly affect the surrounding base material.
- Grinding and Rewelding: In more severe cases, the area around the burn-through may need to be ground down and the weld remade. This approach ensures that the weak section of the base material is removed and replaced with sound weld metal.
- Patch Welding: For critical applications where the base material has been severely thinned or damaged, a patch may need to be welded over the burn-through area. This provides additional strength and prevents further cracking or failure.
Other Common Welding Defects
Burn-through is just one of many potential welding defects that can occur during the process. Some other common defects include:
- Porosity: Caused by trapped gas in the weld pool, porosity appears as small holes or voids in the weld metal. It can weaken the weld and make it more prone to failure.
- Lack of Fusion: Occurs when the weld metal fails to fuse properly with the base material. This can result in a weak joint that may crack or break under stress.
- Cracking: Cracks can form in the weld metal or heat-affected zone (HAZ) due to rapid cooling, excessive stress, or poor joint design. Cracks are one of the most severe welding defects and often require extensive repair.
- Undercut: Undercut occurs when the base material is melted away at the edges of the weld, leaving a groove or depression. This weakens the joint and can lead to cracking or failure.
- Inclusion: Inclusions are foreign materials, such as slag or oxides, that become trapped in the weld metal. They can reduce the strength of the weld and cause defects like porosity or cracking.
Conclusion
Burn-through is a significant welding defect that can compromise the strength and integrity of a welded joint. By understanding the causes of burn-through, welders can take steps to prevent it, ensuring that their welds are structurally sound and safe. Proper technique, appropriate machine settings, and attention to detail are all essential for avoiding burn-through and other common welding defects.
In critical applications where weld integrity is paramount, it’s important to thoroughly inspect and test welds to ensure that defects are detected and repaired. By following best practices and employing proper repair techniques, welders can produce high-quality welds that stand the test of time.
Preventing and managing burn-through is not just about skill; it’s about applying the right knowledge and using the correct equipment to maintain the integrity of your welds. Whether you’re a beginner or an experienced welder, this insight will help you navigate through potential challenges and achieve top-quality results in your welding projects.