MIG vs MAG Welding: Key Differences Explained
MIG (Metal Inert Gas) and MAG (Metal Active Gas) welding are two widely used arc welding processes, often grouped under the broader term Gas Metal Arc Welding (GMAW). While they share similarities in equipment and technique, the fundamental difference lies in the type of shielding gas used. Understanding these variations is crucial for welders to select the appropriate process for specific applications. This comprehensive guide delves into the principles, key differences, applications, and advantages of MIG and MAG welding to help you make an informed choice.
Understanding MIG and MAG Welding
MIG Welding (Metal Inert Gas)
MIG welding employs a continuous solid wire electrode that is fed through the welding gun and an inert shielding gas, typically argon or helium, to protect the weld pool from atmospheric contamination. The inert gas does not chemically react with the molten metal, making it suitable for welding non-ferrous metals like aluminum, copper, and magnesium.
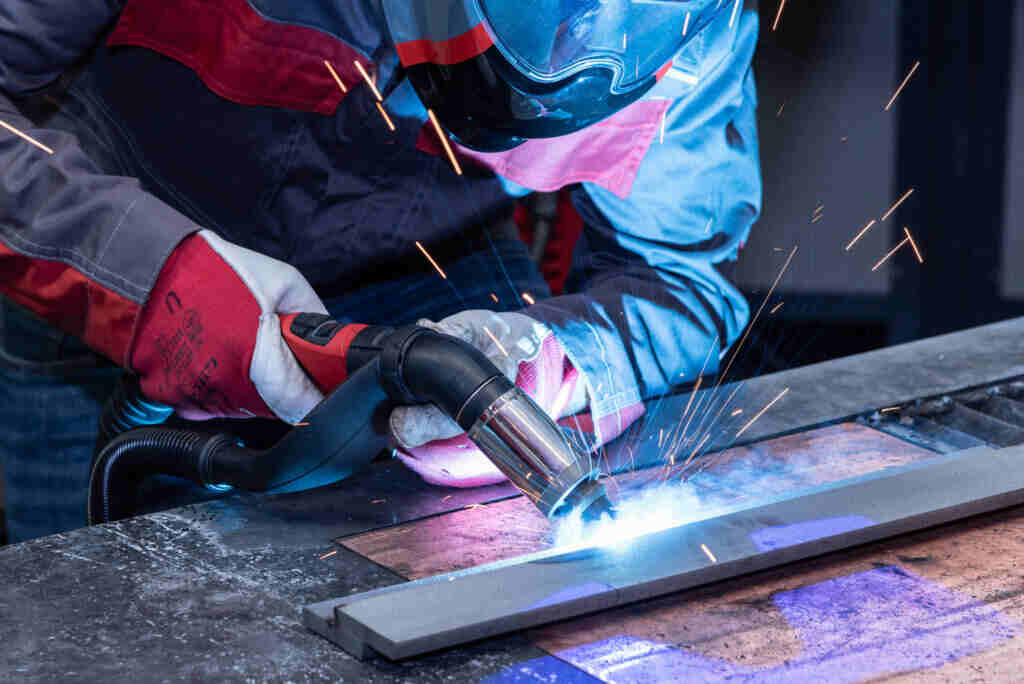
- Shielding Gas: Argon, helium, or a mixture of both.
- Applications: Primarily used for non-ferrous metals and thin materials.
- Characteristics: Produces clean, precise welds with minimal spatter.
MAG Welding (Metal Active Gas)
MAG welding, on the other hand, uses an active gas or gas mixture such as carbon dioxide (CO₂) or a combination of CO₂ and argon. The active gas interacts with the molten metal, influencing the arc stability and weld properties. MAG welding is more commonly used for ferrous metals like mild steel and stainless steel due to the gas’s ability to enhance penetration and weld strength.
- Shielding Gas: CO₂ or a mixture of CO₂ and argon.
- Applications: Best suited for welding ferrous metals, including steel and its alloys.
- Characteristics: High penetration, good mechanical properties, and increased spatter compared to MIG.
Key Differences Between MIG and MAG Welding
- Shielding Gas Composition
The most prominent distinction between the two processes lies in the composition of the shielding gas.- MIG Welding: Uses inert gases like argon and helium.
- MAG Welding: Uses active gases like CO₂ or argon-CO₂ blends.
- Material Compatibility
MIG welding is ideal for non-ferrous metals, while MAG welding is preferred for ferrous metals due to the active gas’s effect on the weld’s metallurgical properties. - Weld Quality and Appearance
MIG welding typically produces cleaner, aesthetically pleasing welds with minimal spatter. In contrast, MAG welding may result in more spatter and require additional post-weld cleaning. - Arc Characteristics
The arc in MIG welding is generally more stable due to the use of inert gases, resulting in less oxidation and a smoother finish. In MAG welding, the arc can be more turbulent due to the active gas’s reactivity, affecting the stability and weld appearance. - Penetration and Strength
MAG welding provides deeper penetration and stronger welds for thicker materials, making it ideal for heavy-duty applications like structural steelwork.
Advantages and Disadvantages of MIG and MAG Welding
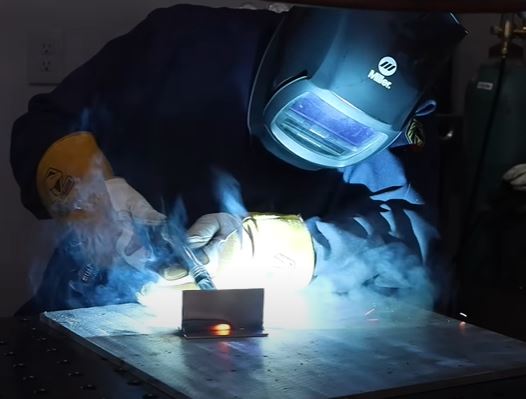
MIG Welding
- Advantages:
- Clean, high-quality welds with minimal spatter.
- Suitable for thin materials and non-ferrous metals.
- Lower post-weld cleanup required.
- Easier for beginners to learn due to stable arc and controlled weld pool.
- Disadvantages:
- Limited penetration on thicker materials.
- More expensive shielding gas.
- Less effective for outdoor applications due to gas sensitivity.
MAG Welding
- Advantages:
- Deep penetration and stronger welds.
- Cost-effective shielding gas options.
- Ideal for welding thicker ferrous metals.
- Versatile for a wide range of industrial applications.
- Disadvantages:
- More spatter and potential for oxidation.
- Requires additional cleanup and finishing.
- Higher risk of weld defects if not properly controlled
Applications of MIG and MAG Welding
Understanding the appropriate use cases for MIG and MAG welding is critical to achieving the desired weld quality and meeting project specifications. Let’s explore the primary applications for each process:
MIG Welding Applications
- Automotive Industry:
MIG welding is widely used in automotive manufacturing and repair, particularly for joining thin sheets of metal like aluminum body panels. The clean welds produced are ideal for creating strong, lightweight joints with minimal distortion. - Aerospace Sector:
Due to its suitability for non-ferrous metals, MIG welding is a preferred choice for aerospace applications, where materials like aluminum and titanium are commonly used. - Fabrication of Metal Furniture:
MIG welding’s precision and low spatter production make it well-suited for the fabrication of metal furniture, where aesthetics and smooth finishes are crucial. - Hobbyist and DIY Projects:
Beginners and hobbyists often start with MIG welding because of its user-friendly nature, enabling them to create neat, professional-looking welds even with minimal experience. - General Maintenance and Repair Work:
MIG welding is also used in various maintenance and repair tasks, especially for joining small components made of non-ferrous metals.
MAG Welding Applications
- Structural Steelwork:
MAG welding is commonly used for structural steel fabrication, offering deep penetration and robust welds required for heavy-duty applications like bridge construction and steel frameworks. - Shipbuilding Industry:
The shipbuilding industry relies on MAG welding for constructing large, durable joints in steel components, where high strength and integrity are paramount. - Pipeline Welding:
With its capability for deep penetration, MAG welding is ideal for pipeline welding, ensuring strong, leak-proof joints for critical infrastructure projects. - Heavy Equipment Manufacturing:
Manufacturers of heavy machinery and equipment use MAG welding for joining thick steel plates and components, ensuring durability and reliability in challenging environments. - Automated and Robotic Welding Systems:
MAG welding is often integrated into automated systems due to its adaptability to various welding positions and materials, enhancing efficiency in mass production settings.
Choosing Between MIG and MAG Welding: Key Considerations
Selecting between MIG and MAG welding depends on several factors, including the material type, joint thickness, project requirements, and cost constraints. Here are some key considerations to help you decide:
- Material Type:
- Choose MIG welding for non-ferrous metals like aluminum, copper, and magnesium.
- Opt for MAG welding for ferrous metals like mild steel and stainless steel.
- Weld Strength and Penetration:
- Use MAG welding when deep penetration and high-strength welds are necessary, such as in structural applications.
- Select MIG welding for applications where a cleaner, aesthetically pleasing finish is essential.
- Cost of Shielding Gas:
- MAG welding uses CO₂ or CO₂-argon mixtures, which are generally more cost-effective than the inert gases used in MIG welding. Consider MAG welding for large-scale projects to reduce costs.
- Welding Environment:
- MIG welding is sensitive to wind and outdoor conditions due to the inert gas shielding. For outdoor applications, choose MAG welding, which is less affected by environmental factors.
- Equipment and Setup Costs:
- MIG and MAG welding equipment is similar, but the choice of shielding gas and consumables can influence overall costs. Consider your budget and project scope when making a decision.
Avoiding Common Issues in MIG and MAG Welding
While both MIG and MAG welding offer distinct advantages, they also pose potential challenges if not properly managed. Here’s a look at some common issues and strategies to prevent them:
Porosity
Porosity occurs when gas pockets are trapped in the weld metal, leading to weak spots and compromised weld integrity.
- Causes:
- Improper gas flow rate.
- Contaminated surfaces (oil, rust, or paint).
- Poor shielding gas coverage.
- Prevention:
- Ensure a clean work surface before welding.
- Use the correct gas flow rate (typically 20-30 cubic feet per hour for MIG/MAG).
- Maintain consistent shielding gas coverage and avoid excessive drafts.
Spatter
Spatter refers to molten metal droplets that are expelled during the welding process, creating a rough and uneven weld surface.
- Causes:
- Excessive voltage or amperage.
- Incorrect wire feed speed.
- Active gases (common in MAG welding).
- Prevention:
- Adjust voltage and amperage settings according to material thickness.
- Use anti-spatter sprays or gels on the workpiece.
- Optimize wire feed speed to maintain a stable arc.
Lack of Fusion
Lack of fusion occurs when the weld metal does not fully bond with the base metal, resulting in weak joints and potential failure.
- Causes:
- Insufficient heat input.
- Improper joint preparation.
- Incorrect torch angle.
- Prevention:
- Increase the heat input by adjusting voltage or amperage.
- Ensure proper joint preparation and fit-up.
- Use a consistent torch angle to direct the arc into the joint.
Burn-Through
Burn-through happens when excessive heat melts through the base metal, creating holes and an incomplete weld.
- Causes:
- High heat input.
- Thin material thickness.
- Inadequate travel speed.
- Prevention:
- Lower the heat input by reducing voltage or amperage.
- Increase the travel speed to distribute heat evenly.
- Use backing plates or chill bars for thin materials.
Optimizing MIG and MAG Welding for Quality Results
To achieve optimal results in both MIG and MAG welding, consider the following best practices:
- Select the Appropriate Filler Material:
Use filler wire that matches the base metal composition to ensure compatibility and strong joints. - Maintain a Consistent Arc Length:
Keeping a short, consistent arc length helps maintain arc stability and minimizes defects. - Control Heat Input:
Adjust voltage and amperage settings based on material thickness and joint configuration. Use pulsed MIG/MAG welding for better control on thin materials. - Use Proper Welding Techniques:
Employ techniques like weaving or stringer beads based on the joint type and desired weld profile. For thicker materials, use multi-pass welding to achieve adequate penetration. - Regularly Clean and Inspect Equipment:
Ensure that the welding gun, contact tips, and wire feed system are in good condition. Regular maintenance reduces equipment-related issues and enhances weld quality.
Conclusion:
MIG and MAG welding are versatile processes, each with unique characteristics and advantages. By understanding the differences between the two and considering factors such as material type, weld strength, and environmental conditions, welders can select the most appropriate method for their projects. Proper technique, equipment settings, and adherence to best practices will ensure high-quality, reliable welds, whether you’re working with non-ferrous alloys or structural steel.
Ultimately, mastering both MIG and MAG welding provides welders with the flexibility to tackle a wide range of applications, from intricate fabrication work to heavy-duty industrial welding.