Surfacing of Materials in Welding
Surfacing of materials is a specialized welding technique where a layer of material is deposited on a base metal to improve its surface properties. Unlike conventional welding, which focuses on joining two parts, surfacing aims to enhance the surface by improving wear resistance, corrosion resistance, or restoring worn-out components to their original state.
Why is this process important? Imagine machinery parts that are exposed to friction, extreme temperatures, or corrosive environments. Replacing such parts can be costly and time-consuming. Surfacing, on the other hand, provides a cost-effective and efficient solution to prolong the life of these components.
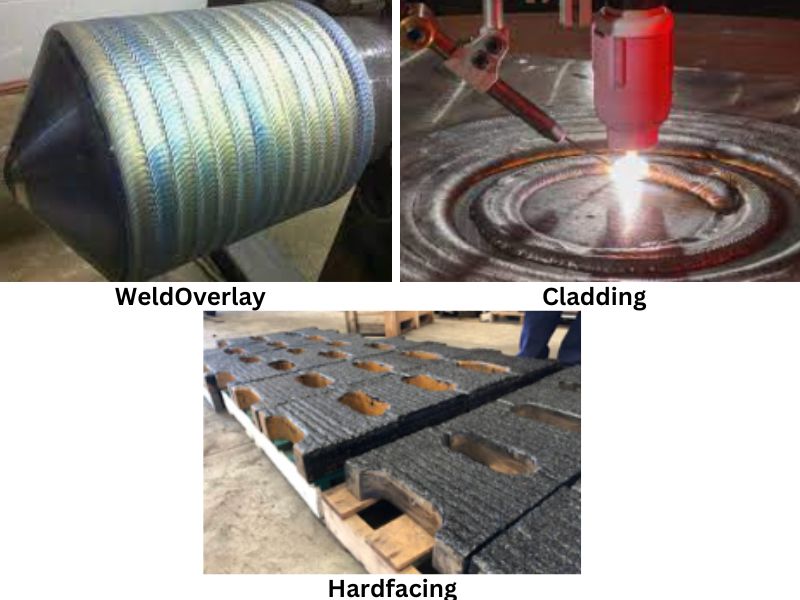
Objectives of Surfacing
Surfacing serves various purposes in industrial applications. Let’s break down its key objectives:
- Enhancing Wear Resistance:
Surfaces that experience constant abrasion or friction, such as conveyor belts or excavator teeth, are prone to wear. Surfacing adds a layer of hard material to withstand these forces, significantly extending the component’s life. - Restoring Worn-Out Components:
Machinery parts like shafts or rollers often lose their original dimensions due to wear. Instead of discarding them, surfacing restores these parts to their original state, saving time and money. - Improving Corrosion Resistance:
In industries like oil and gas or chemical processing, components are exposed to corrosive substances. A surfacing layer made of corrosion-resistant material shields the base metal from damage, ensuring longevity. - Modifying Surface Properties:
Surfacing allows manufacturers to tailor the surface of components to specific needs. For example, adding a layer of conductive material can improve electrical conductivity, while a heat-resistant layer can enhance thermal stability.
Classification of Surfacing in Welding
Hardfacing
Hardfacing is the process of applying a hard, wear-resistant layer to the surface of a component to protect it from wear and impact. This is particularly useful for machinery and tools exposed to abrasive or high-impact conditions.
Purpose: The primary goal of hardfacing is to extend the lifespan of components that experience significant wear due to friction, abrasion, or impact.
Process: A hard alloy or material is welded onto the base metal to create a tough surface. The material used is typically much harder than the base metal, such as chromium carbide or tungsten carbide.
Applications:
- Mining tools, such as drills and excavator buckets.
- Construction equipment, like bulldozer blades and loader buckets.
- Agricultural machinery, including plows and harrows.
- Industrial machinery parts, such as pump impellers and crusher hammers.
Cladding
Cladding involves depositing a corrosion-resistant material onto a base metal to protect it from chemical attack, high temperatures, or other harsh conditions. Unlike hardfacing, which focuses on wear resistance, cladding is primarily concerned with preventing corrosion.
Purpose: To create a surface layer that resists corrosion or chemical degradation while maintaining the structural integrity of the underlying material.
Process: The cladding material, such as stainless steel, Inconel, or Hastelloy, is welded onto the surface of the base metal using processes like Submerged Arc Welding (SAW) or Plasma Transferred Arc Welding (PTAW).
Applications:
- Pipelines and storage tanks in the oil and gas industry.
- Heat exchangers and pressure vessels.
- Chemical processing equipment exposed to corrosive substances.
Build-Up Surfacing
Build-up surfacing is used to restore worn-out components to their original dimensions. Over time, parts like shafts, gears, or rollers can lose material due to wear or corrosion. Instead of replacing the part, build-up surfacing rebuilds it, saving time and costs.
Purpose: To add material to worn-out areas, restoring the component to its original size and functionality.
Process: Layers of metal are applied through welding, often followed by machining or grinding to achieve precise dimensions. Commonly used materials include mild steel and stainless steel.
Applications:
- Shafts and spindles in industrial machinery.
- Gear teeth in mechanical systems.
- Rollers and tracks in conveyor systems.
Overlay Welding
Overlay welding is the process of depositing a layer of material over the base metal to enhance its properties. It is similar to cladding but is often more versatile and can be used to achieve specific surface properties beyond just corrosion resistance.
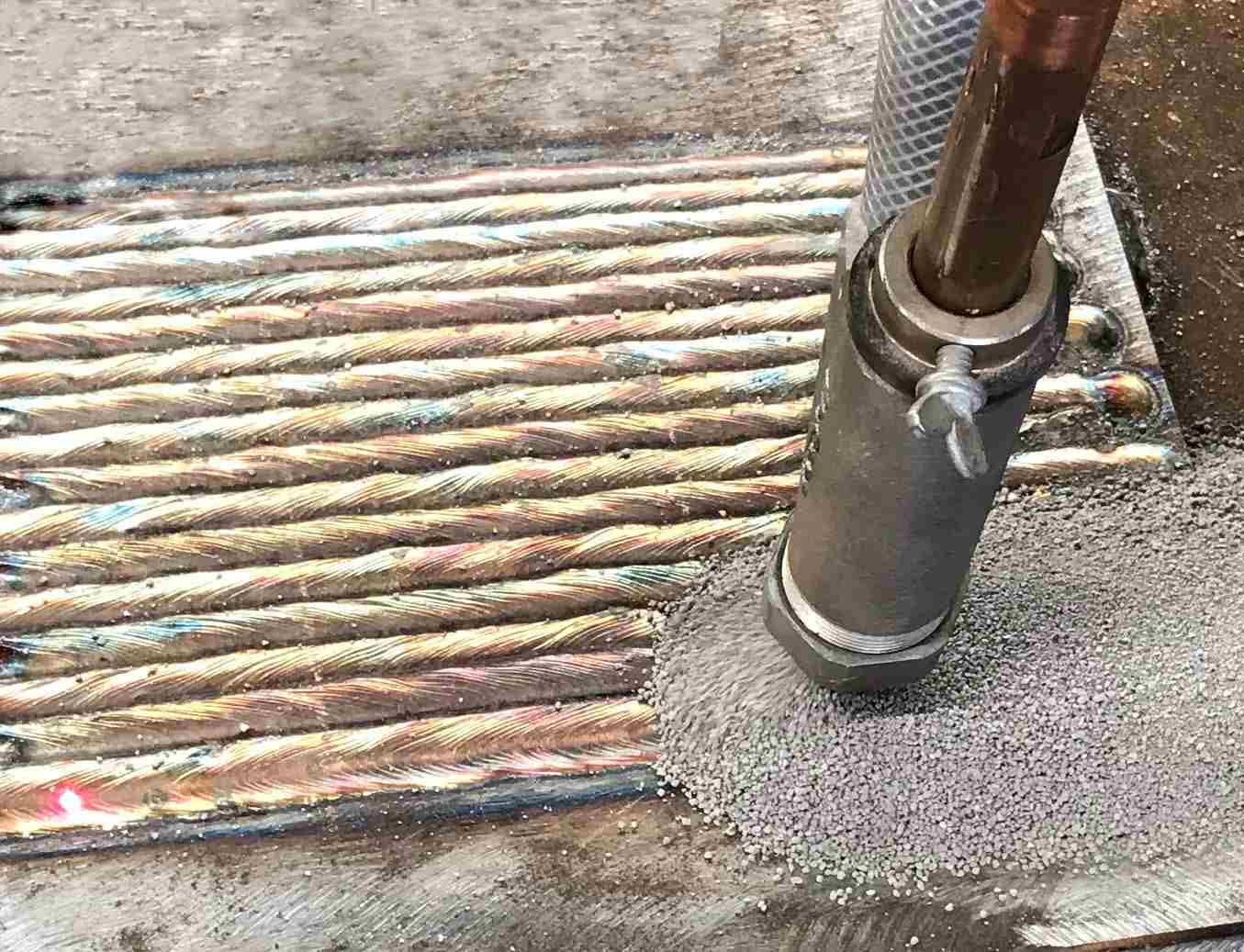
Purpose: To improve surface characteristics such as thermal resistance, hardness, or corrosion resistance, depending on the application.
Process: A layer of material is applied using welding techniques like Gas Metal Arc Welding (GMAW), Submerged Arc Welding (SAW), or Plasma Transferred Arc Welding (PTAW). Overlay welding often involves the use of specialized alloys tailored to the application’s needs.
Applications:
- Turbine blades exposed to high temperatures.
- Components in chemical plants requiring resistance to acidic or alkaline substances.
- Parts in the food processing industry needing non-reactive surfaces.
Buttering
Buttering is a specialized surfacing technique where a layer of material is deposited on the base metal to prepare it for further welding. It is primarily used when the base metal and filler material are not directly compatible.
Purpose of Buttering:
- To create a compatible surface layer between two dissimilar materials.
- To prevent cracking or other welding defects that might occur due to differences in metallurgical properties like thermal expansion rates.
Process of Buttering:
- A thin layer of compatible material is deposited on the base metal.
- Once the buttering layer is applied, the actual weld or subsequent surfacing layer is deposited over it.
- This process ensures the final weld or layer adheres well and maintains structural integrity.
Materials Used in Buttering:
- Nickel-based Alloys: Commonly used as an intermediary material due to their excellent bonding properties with dissimilar metals.
- Austenitic Stainless Steels: Often used for buttering carbon or low-alloy steels.
Applications of Buttering:
- Dissimilar Metal Welding: For example, welding carbon steel to stainless steel in pipelines or pressure vessels.
- Repair and Maintenance: Preparing a base metal surface for overlay welding or cladding, especially when dealing with degraded or old components.
- High-Stress Applications: Situations where metallurgical compatibility is critical to avoid thermal fatigue or cracking, such as in boilers or turbines.
Materials Used for Surfacing
The success of surfacing depends on the compatibility between the base material and the surfacing material.
Base Materials
Base materials are the foundation on which surfacing is applied. Commonly used base materials include:
- Carbon Steel: Widely used due to its affordability and versatility.
- Stainless Steel: Preferred for its corrosion resistance.
- Cast Iron: Often used in heavy machinery and automotive components.
Surfacing Alloys
- Hardfacing Alloys: These alloys, such as tungsten carbide and chromium carbide, are designed to resist wear and tear in high-friction environments.
- Corrosion-Resistant Alloys: Alloys like Inconel and Hastelloy are used to protect against rust and chemical degradation.
Welding Techniques for Surfacing
Different welding methods are used for surfacing, depending on the application and material.
Manual Metal Arc Welding (MMAW)
This is one of the oldest and most versatile welding methods, commonly used for hardfacing. It’s cost-effective and suitable for smaller-scale surfacing projects.
Gas Metal Arc Welding (GMAW)
Also known as MIG welding, GMAW offers high efficiency and precision. It’s ideal for applying surfacing layers in controlled environments.
Submerged Arc Welding (SAW)
SAW is a high-productivity method used for cladding large surfaces. The process involves a granular flux that covers the weld, ensuring minimal spatter and a clean finish.
Plasma Transferred Arc Welding (PTAW)
PTAW is a precision welding technique used for applying high-performance alloys. It’s commonly employed in industries requiring extreme wear or corrosion resistance.
Benefits of Surfacing in Welding
Why choose surfacing over replacing components? Here are the key benefits:
- Cost-Effectiveness: Surfacing is significantly cheaper than manufacturing or purchasing new components.
- Extended Lifespan: By protecting surfaces from wear and corrosion, surfacing extends the operational life of machinery.
- Enhanced Performance: Customized surfaces improve the efficiency and reliability of components.
Challenges in Surfacing
Despite its advantages, surfacing comes with challenges:
- Heat Management: Excessive heat during welding can weaken the base material or cause warping.
- Bonding Issues: Achieving a strong bond between the base metal and surfacing material is crucial for durability.
- Material Compatibility: Not all materials can be effectively combined, requiring careful selection.
Applications of Surfacing in Industries
Surfacing has applications across a wide range of industries:
- Mining and Construction: Components like crushers, conveyor belts, and loaders benefit from wear-resistant surfacing.
- Agriculture and Forestry: Plows, harrows, and saw blades are surfaced to withstand tough conditions.
- Oil and Gas Sector: Surfacing protects pipelines and storage tanks from corrosion and pressure.
- Manufacturing and Fabrication: Dies, molds, and machine tools are surfaced to enhance their durability.
Tips for Successful Surfacing
Want to achieve optimal results with surfacing? Follow these tips:
- Choose the Right Material: The surfacing material should be compatible with the base material and suited for the application.
- Proper Pre-Weld Preparation: Clean the surface thoroughly to remove contaminants and ensure a strong bond.
- Post-Weld Treatments: Heat treatment, machining, or polishing may be needed to refine the final product.
FAQs
What is the primary purpose of surfacing in welding?
Surfacing enhances surface properties like wear resistance and corrosion protection while restoring worn-out parts.
Which industries benefit most from surfacing?
Industries such as mining, agriculture, oil and gas, and manufacturing rely heavily on surfacing for cost savings and durability.
What materials are commonly used for surfacing?
Materials like carbon steel, stainless steel, tungsten carbide, and corrosion-resistant alloys are widely used.
How does surfacing enhance the lifespan of equipment?
By adding protective layers, surfacing shields components from wear, corrosion, and environmental damage.
What are the main challenges in surfacing?
Heat management, bonding quality, and material compatibility are some common challenges faced during the process.
Conclusion
Surfacing in welding is a versatile and valuable process that enhances the performance and lifespan of industrial components. From restoring worn-out parts to improving corrosion resistance, surfacing is a cost-effective solution for industries worldwide. With advancements in materials and techniques, surfacing continues to evolve, offering even more efficient and durable options for the future.