Stick Welding: Uphill vs. Downhill Welding Techniques
Stick welding, also known as shielded metal arc welding (SMAW), is a versatile and widely used welding process. It involves using a consumable electrode covered in flux to protect the weld area from atmospheric gases. One of the critical aspects of stick welding is the direction in which you weld—uphill or downhill. Each technique has its advantages and challenges, and understanding these differences is crucial for achieving high-quality welds.
Introduction to Stick Welding
Stick welding is a fundamental technique in many industries, from construction to automotive repair. It’s favored for its simplicity and portability, making it ideal for both small-scale repairs and large-scale projects. However, mastering stick welding requires practice and a good understanding of the techniques involved.
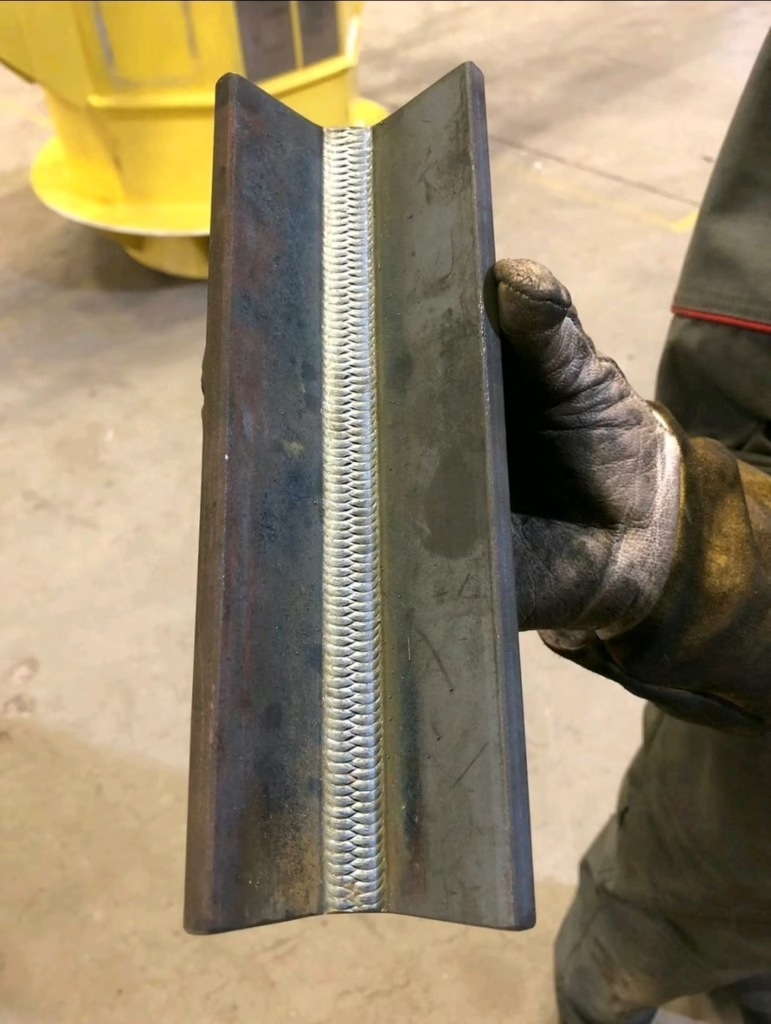
Uphill vs. Downhill Welding
Definition and Differences
Uphill Welding: This involves welding from the bottom of a joint upwards. It’s often used for thicker materials and when penetration is crucial. Uphill welding helps prevent the molten metal from flowing away from the weld pool, ensuring better penetration and a stronger bond.
Downhill Welding: This technique involves welding from the top of a joint downwards. It’s typically used for thinner materials and when speed is more important than penetration. Downhill welding can be faster but often results in less penetration and a weaker weld.
Advantages and Disadvantages
Uphill Welding Advantages:
- Better penetration and strength.
- Less risk of porosity and slag inclusions.
Uphill Welding Disadvantages:
- Requires more skill and control.
- Can be slower due to the need for precise technique.
Downhill Welding Advantages:
- Faster welding speed.
- Easier to manage for beginners.
Downhill Welding Disadvantages:
- Less penetration and weaker welds.
- Higher risk of porosity and slag inclusions.
Electrodes for Uphill and Downhill Welding
Types of Electrodes for Uphill Welding
For uphill welding, electrodes that provide deep penetration and strong welds are preferred. Some common types include:
E6010: Known for its deep penetration and is often used in structural steel welding.
E7018: Offers excellent strength and ductility, making it suitable for critical welds.
Types of Electrodes for Downhill Welding
For downhill welding, electrodes that allow for faster deposition rates and are more forgiving are typically used. Some common types include:
E6013: Provides a smooth, flat weld bead and is often used for cosmetic welds.
E7024: Known for its ease of use and fast deposition rate, making it ideal for thinner materials.
Why Downhill Welding is Considered Bad
Downhill welding is often considered less desirable due to several challenges:
Less Penetration: The molten metal can flow away from the weld pool, resulting in less penetration and a weaker bond.
Higher Risk of Defects: There’s a greater risk of porosity and slag inclusions due to the flow of molten metal.
Difficulty in Controlling the Weld Pool: It can be harder to maintain a consistent weld pool, leading to irregular weld beads.
Uphill Welding Techniques
To master uphill welding, follow these tips:
Maintain a Consistent Arc Length: This ensures consistent heat input and penetration.
Use the Right Electrode: Choose an electrode that provides the desired penetration and strength.
Keep the Weld Pool Small: This helps control the flow of molten metal and prevents it from flowing away.
Downhill Welding Techniques
For downhill welding, consider these tips:
Increase Welding Speed: Downhill welding is faster, so adjust your speed accordingly.
Use a Larger Weld Pool: This can help manage the flow of molten metal and reduce defects.
Monitor the Weld Bead: Ensure the weld bead is smooth and even to avoid irregularities.
Choosing the Right Equipment
The right equipment can make a significant difference in your welding experience:
Welding Machine: Choose a machine that can handle the type of electrode you’re using.
Electrode Holder: Ensure it’s comfortable and secure to prevent accidents.
Proper Ventilation: Always weld in a well-ventilated area to avoid inhaling fumes.
FAQs
What is the main advantage of uphill welding?
The main advantage of uphill welding is better penetration and strength, making it ideal for critical welds.
Why is downhill welding considered less desirable?
Downhill welding is considered less desirable because it often results in less penetration and a higher risk of defects like porosity and slag inclusions.
What type of electrode is best for uphill welding?
Electrodes like E6010 and E7018 are best for uphill welding due to their deep penetration and strength.
Can downhill welding be used for thicker materials?
While downhill welding can be used for thicker materials, it’s generally not recommended due to the risk of less penetration and weaker welds.
How important is safety gear in stick welding?
Safety gear, such as welding helmets and gloves, is crucial in stick welding to protect against UV radiation, sparks, and electrical shock.
Conclusion
Stick welding is a versatile technique that requires understanding and practice to master. Uphill welding offers better penetration and strength, making it ideal for critical applications. Downhill welding, while faster, often results in weaker welds and is more prone to defects. By choosing the right electrodes and techniques, you can achieve high-quality welds. Remember, safety and proper equipment are just as important as technique.