AWS A5.1 Standard Challenges
When it comes to welding, standards are the backbone of quality and safety. One such critical standard is the AWS A5.1, which governs the specifications for carbon steel electrodes used in shielded metal arc welding (SMAW). But what exactly is this standard, and why is it so important? Let’s break it down.
What is the AWS A5.1 Standard?
Definition and Purpose
The AWS A5.1 standard, established by the American Welding Society (AWS), outlines the requirements for carbon steel electrodes. These electrodes are used in SMAW, a popular welding method known for its versatility and simplicity. The standard ensures that electrodes meet specific mechanical and chemical properties, guaranteeing consistent performance and safety in welding applications.
Importance in Welding Industry
Imagine building a skyscraper without a blueprint. Sounds chaotic, right? That’s what welding without standards like AWS A5.1 would be like. This standard ensures that welders, engineers, and manufacturers are on the same page, reducing errors and enhancing the reliability of welded structures.
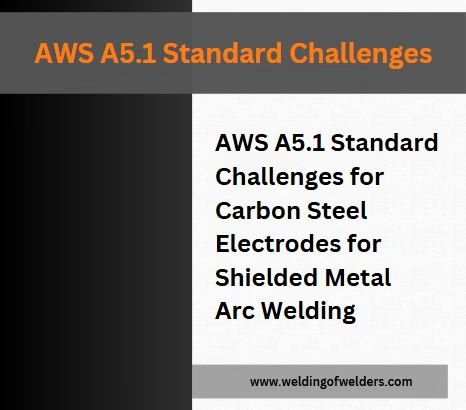
Key Components of AWS A5.1
Electrode Classification
AWS A5.1 classifies electrodes based on their tensile strength, welding position, and type of coating. For example, an E6013 electrode has a tensile strength of 60,000 psi, can be used in all positions, and has a rutile coating. Understanding these codes is crucial for selecting the right electrode for your project.
Mechanical and Chemical Properties
The standard also specifies the mechanical properties (like tensile strength and elongation) and chemical composition of the electrodes. These properties ensure that the electrodes can withstand the stresses of welding and produce durable welds.
Common Challenges in Implementing AWS A5.1
While the AWS A5.1 standard is a game-changer, implementing it isn’t always a walk in the park. Let’s dive into some of the most common challenges welders face.
Electrode Selection Difficulties
Matching Electrodes to Base Metals
One of the biggest headaches is selecting the right electrode for the base metal. Not all electrodes are created equal, and using the wrong one can lead to weak welds or even catastrophic failures. For instance, using a low-hydrogen electrode on a high-carbon steel might not yield the desired results.
Understanding Electrode Codes
The alphanumeric codes on electrodes can feel like deciphering hieroglyphics. What does E7018 mean? How is it different from E6010? Misinterpreting these codes can lead to poor electrode selection, affecting the quality of your welds.
Welding Process Complications
Arc Stability Issues
Ever experienced an erratic arc while welding? It’s frustrating, right? Arc stability is crucial for producing clean, strong welds. However, factors like improper electrode storage or incorrect welding parameters can destabilize the arc, leading to defects like porosity or spatter.
Slag Removal Problems
Slag, the byproduct of welding, needs to be removed to inspect the weld. But sometimes, slag sticks stubbornly to the weld bead, making removal a tedious task. This not only slows down the process but can also hide underlying defects.
Quality Control and Compliance
Meeting AWS A5.1 Specifications
Ensuring that your welds meet AWS A5.1 specifications is no small feat. From electrode storage to welding techniques, every step must align with the standard. Any deviation can result in non-compliant welds, leading to rework or rejection.
Ensuring Consistency in Welds
Consistency is key in welding. However, achieving uniform welds across large projects can be challenging. Variations in welding speed, electrode angle, or even environmental conditions can affect the final outcome.
Overcoming AWS A5.1 Standard Challenges
Now that we’ve identified the challenges, let’s explore how to tackle them head-on.
Best Practices for Electrode Selection
Consulting Welding Charts and Guides
When in doubt, refer to welding charts and guides. These resources provide valuable insights into which electrodes work best with specific base metals and welding conditions.
Testing Electrodes Before Full-Scale Use
Before committing to a large project, test the electrodes on a small scale. This helps identify any compatibility issues and ensures that the electrodes perform as expected.
Optimizing Welding Techniques
Adjusting Welding Parameters
Fine-tuning parameters like voltage, current, and travel speed can significantly improve weld quality. Experiment with different settings to find the sweet spot for your specific application.
Proper Storage and Handling of Electrodes
Electrodes are sensitive to moisture and contamination. Store them in a dry, temperature-controlled environment and follow the manufacturer’s guidelines for handling.
Enhancing Quality Control Measures
Regular Training for Welders
A well-trained welder is your best asset. Regular training sessions can help welders stay updated on the latest techniques and standards, ensuring consistent quality.
Implementing Advanced Inspection Methods
Incorporate advanced inspection methods like ultrasonic testing or radiographic testing to detect hidden defects. These methods provide a deeper insight into the weld’s integrity, ensuring compliance with AWS A5.1.
FAQs
What is the AWS A5.1 standard primarily used for?
The AWS A5.1 standard specifies the requirements for carbon steel electrodes used in shielded metal arc welding (SMAW), ensuring consistent performance and safety.
How do I choose the right electrode under AWS A5.1?
Refer to welding charts and guides, understand electrode codes, and test electrodes on a small scale before full-scale use.
What are the most common welding issues related to AWS A5.1?
Common issues include electrode selection difficulties, arc stability problems, slag removal challenges, and ensuring compliance with specifications.
How can I ensure compliance with AWS A5.1 standards?
Regular training, proper electrode storage, and advanced inspection methods can help ensure compliance with AWS A5.1 standards.
Are there any alternatives to AWS A5.1 for welding electrodes?
While AWS A5.1 is widely used, other standards like ISO 2560 may apply depending on the region and application. Always consult project specifications for guidance.
Conclusion
The AWS A5.1 standard is a cornerstone of the welding industry, ensuring quality, safety, and consistency. However, implementing it comes with its own set of challenges, from electrode selection to quality control. By understanding these challenges and adopting best practices, you can overcome them and achieve welds that meet the highest standards.