Boiler Welding Electrodes
Introduction
Boiler welding electrodes play a crucial role in the construction and maintenance of boilers, ensuring strong and durable welds. These electrodes are essential for creating the high-quality welds necessary to withstand the extreme pressures and temperatures that boilers endure. Understanding the types, applications, and best practices for using boiler welding electrodes can significantly impact the longevity and efficiency of boiler systems.
Types of Boiler Welding Electrodes
When it comes to boiler welding, selecting the appropriate electrode is critical. Here are the primary types of electrodes used in boiler welding:
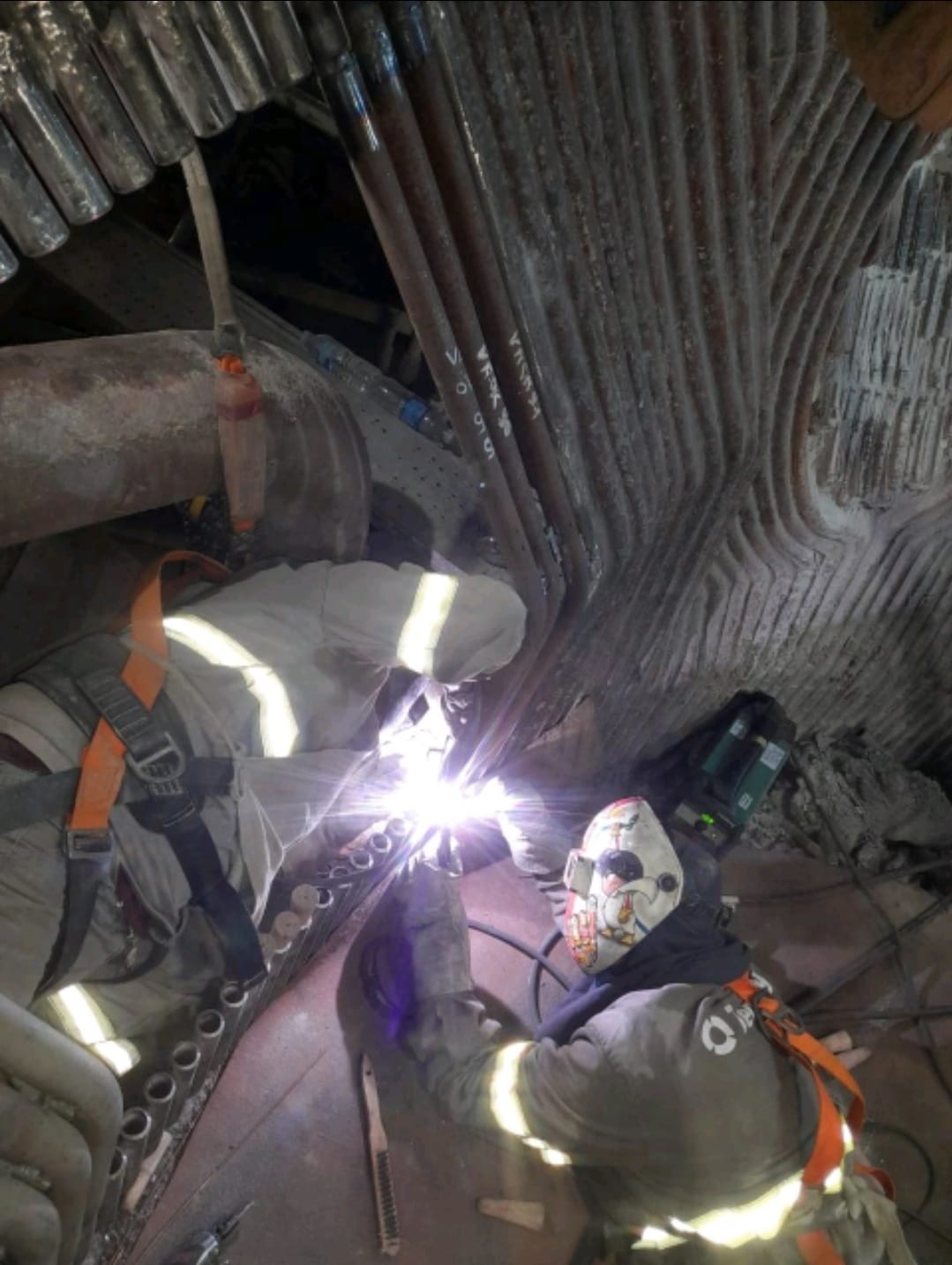
Carbon Steel Electrodes
Carbon steel electrodes are commonly used due to their versatility and cost-effectiveness. They are suitable for welding low to medium carbon steels and are often employed in the construction of boiler components.
Low Alloy Steel Electrodes
Low alloy steel electrodes are designed for welding steels with specific alloying elements, such as molybdenum or chromium. These electrodes provide enhanced mechanical properties and resistance to high temperatures and corrosion, making them ideal for certain boiler applications.
Stainless Steel Electrodes
Stainless steel electrodes are used for welding stainless steels, which are known for their corrosion resistance and strength. These electrodes are essential in environments where the boiler is exposed to corrosive substances or high temperatures.
Choosing the Right Electrode
Selecting the appropriate electrode involves considering several factors, including the base material, welding position, and desired weld properties. Matching the electrode type to the base material ensures optimal weld quality and performance.
Popular Electrodes for Boiler Welding
E7018
E7018 electrodes are known for their low hydrogen content, which reduces the risk of weld cracking. They produce smooth, strong welds with excellent mechanical properties.Ideal for welding carbon steel and low-alloy steel in high-stress environments, such as boilers.
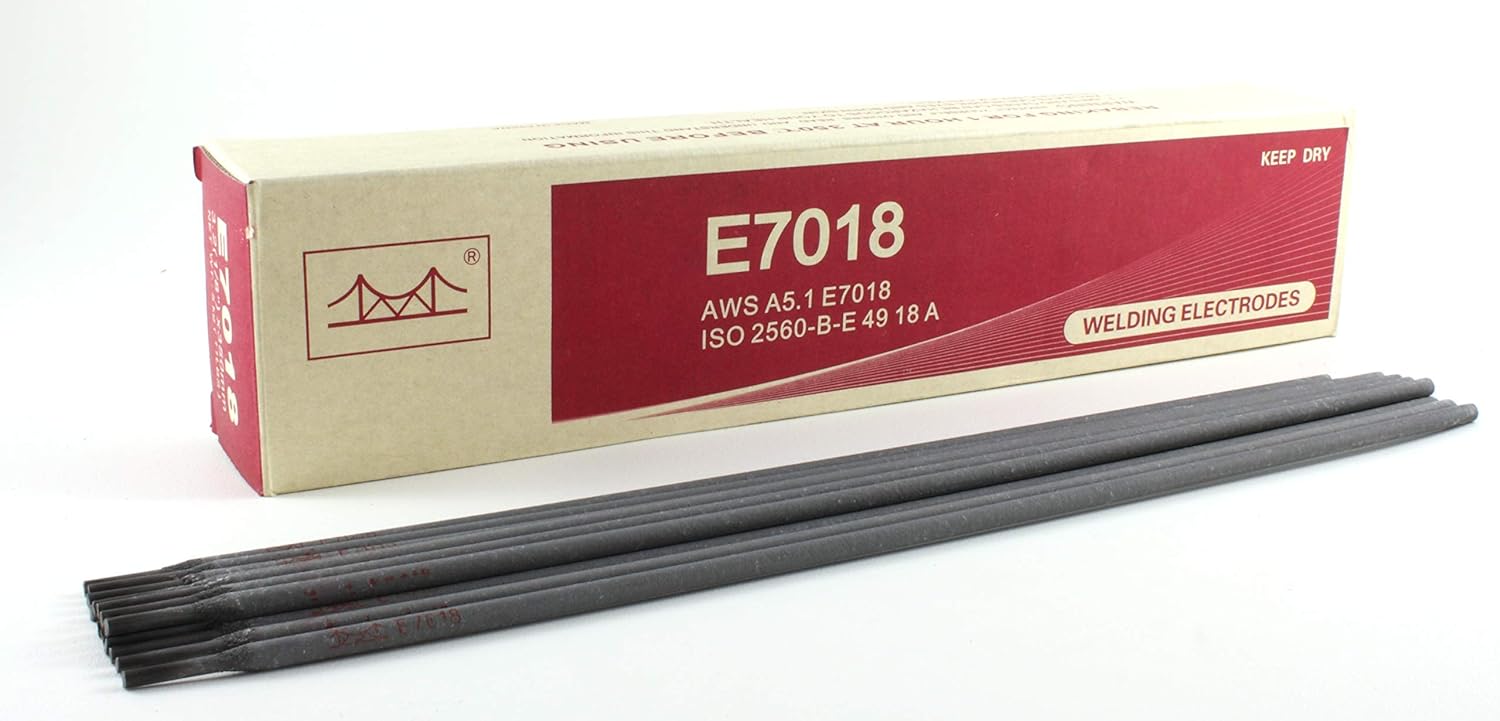
E6010
E6010 electrodes provide deep penetration and are excellent for welding in all positions. They are known for their fast-freezing slag and ease of use. Frequently used for root pass welds in boiler construction due to their penetration capabilities.
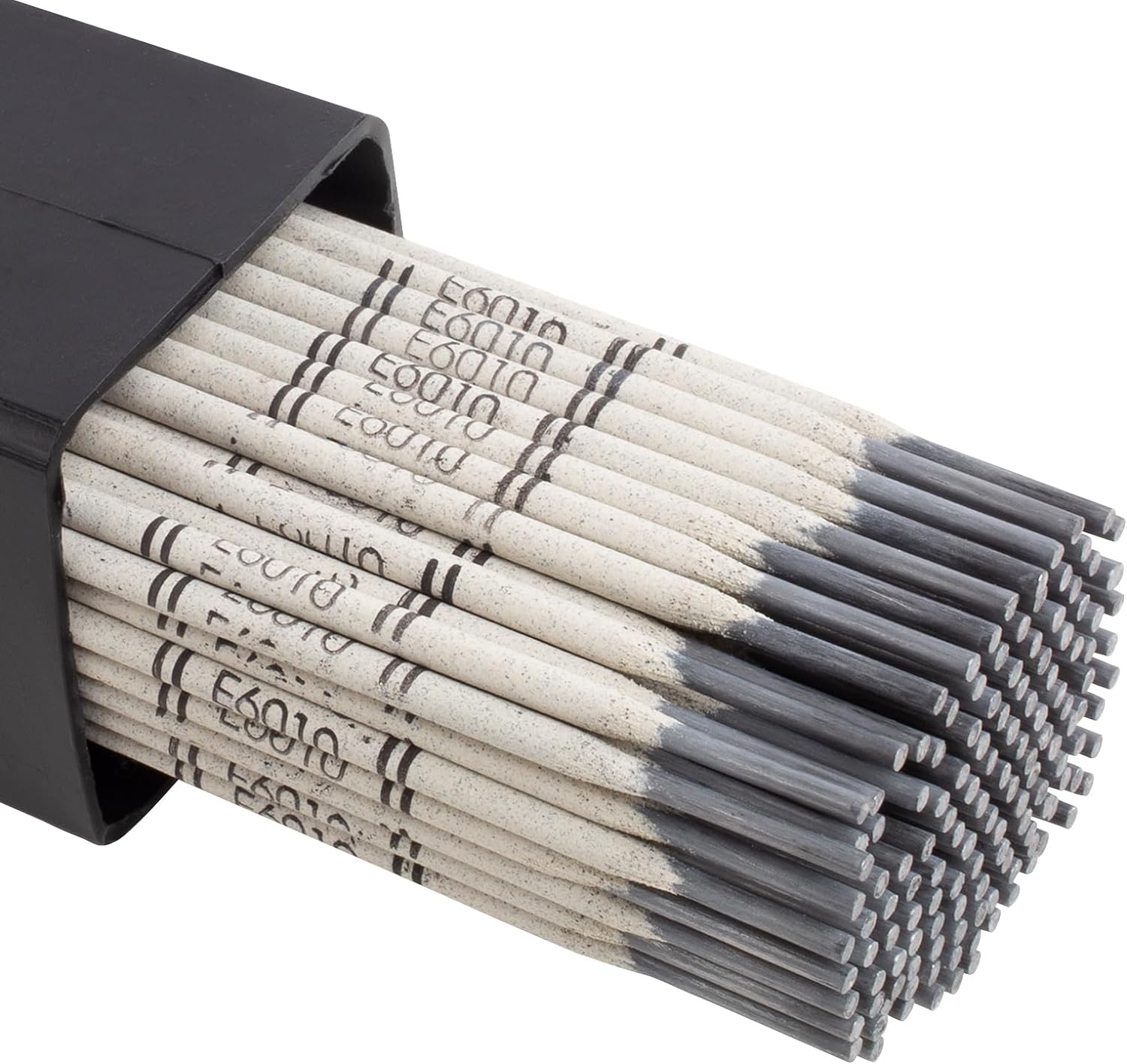
E6011
Similar to E6010 but with better arc stability and smoother finishes. E6011 electrodes can be used with AC and DC currents.Suitable for welding rusty or dirty surfaces, making them versatile for boiler repairs.
E309L-16
E309L-16 electrodes are designed for welding stainless steels and dissimilar metals. They offer excellent corrosion resistance and high-temperature strength.Used for joining stainless steel components in boilers and other high-temperature applications.
Carbon Steel Electrodes
Carbon steel electrodes have distinct characteristics that make them suitable for specific applications:
- Characteristics: High tensile strength, good ductility.
- Common Applications: General fabrication, structural welding.
- Advantages: Cost-effective, easy to use.
- Disadvantages: Limited corrosion resistance.
Low Alloy Steel Electrodes
Low alloy steel electrodes offer enhanced properties for demanding applications:
- Characteristics: Improved mechanical properties, better heat resistance.
- Common Applications: High-temperature service, pressure vessels.
- Advantages: Superior strength and durability.
- Disadvantages: Higher cost, more complex welding process.
Stainless Steel Electrodes
Stainless steel electrodes are essential for specific high-performance applications:
- Characteristics: Excellent corrosion resistance, high strength.
- Common Applications: Chemical plants, power generation.
- Advantages: Long-lasting welds, resistant to harsh environments.
- Disadvantages: Higher cost, requires careful handling.
Electrode Coating Types
Electrode coatings play a significant role in the welding process. The main types include:
- Cellulosic: Fast freezing, good for vertical and overhead welding.
- Rutile: Smooth welds, easy slag removal, suitable for all positions.
- Basic: High-quality welds, good mechanical properties, requires controlled storage.
Electrode Storage and Handling
Proper storage and handling of electrodes are vital to maintain their quality. Recommended practices include keeping electrodes in a dry, temperature-controlled environment and using heated storage containers for moisture-sensitive types.
Welding Techniques for Boilers
Effective welding techniques ensure the integrity of boiler welds. Key techniques include:
- Preheating: Reduces thermal shock and prevents cracking.
- Post-Weld Heat Treatment (PWHT): Relieves stresses and improves weld properties.
- Techniques for Different Positions: Adjusting techniques for flat, vertical, overhead, and horizontal positions.
Common Challenges in Boiler Welding
Welding boilers presents several challenges, including:
- Hydrogen-Induced Cracking: Prevented by using low-hydrogen electrodes and proper preheating.
- Porosity: Avoided by using clean materials and appropriate welding parameters.
- Slag Inclusions: Minimized by ensuring proper slag removal and using the correct technique.
Safety Measures in Boiler Welding
Safety is paramount in boiler welding. Essential measures include:
- Personal Protective Equipment (PPE): Helmets, gloves, and protective clothing.
- Ventilation and Fume Extraction: Prevents exposure to harmful fumes.
- Fire Safety: Ensures a safe working environment.
Inspection and Testing of Welds
Ensuring weld quality involves rigorous inspection and testing methods:
- Visual Inspection: Initial check for obvious defects.
- Non-Destructive Testing (NDT) Methods: Techniques such as radiography and ultrasonic testing to detect internal flaws.
FAQs
What are the main types of boiler welding electrodes?
The main types are carbon steel, low alloy steel, and stainless steel electrodes.
How do I choose the right electrode for my boiler?
Consider the base material, welding position, and desired weld properties.
What are common issues faced during boiler welding?
Common issues include hydrogen-induced cracking, porosity, and slag inclusions.
Why is electrode storage important?
Proper storage maintains electrode quality and prevents moisture-related issues.
What are the latest innovations in boiler welding electrodes?
Innovations include new high-performance materials and advanced electrode coatings.
Conclusion
Boiler welding electrodes are integral to the construction and maintenance of robust boiler systems. By understanding the types, proper selection, and best practices for using these electrodes, welders can ensure the longevity and efficiency of boiler operations. As technology advances, staying updated on new materials and techniques will further enhance weld quality and performance.