Rusty Metal Welding: Techniques, Tips, and Challenges You Need to Know
Introduction
Rusty metal, with its reddish-brown patina, is a common sight, particularly in outdoor environments where exposure to moisture and oxygen accelerates the corrosion process. As metal structures age, they often succumb to rust, leading to weakened integrity and compromised functionality. However, with the right knowledge and techniques, welding rusty metal is not only possible but essential for restoring and reinforcing these structures.
Definition of Rusty Metal
Rusty metal refers to metal surfaces that have undergone oxidation, resulting in the formation of iron oxide, commonly known as rust. This reddish-brown coating forms when iron or its alloys, such as steel, react with oxygen and moisture in the air or water. Rust not only alters the appearance of metal but also weakens its structural integrity over time, making it susceptible to corrosion and eventual deterioration.
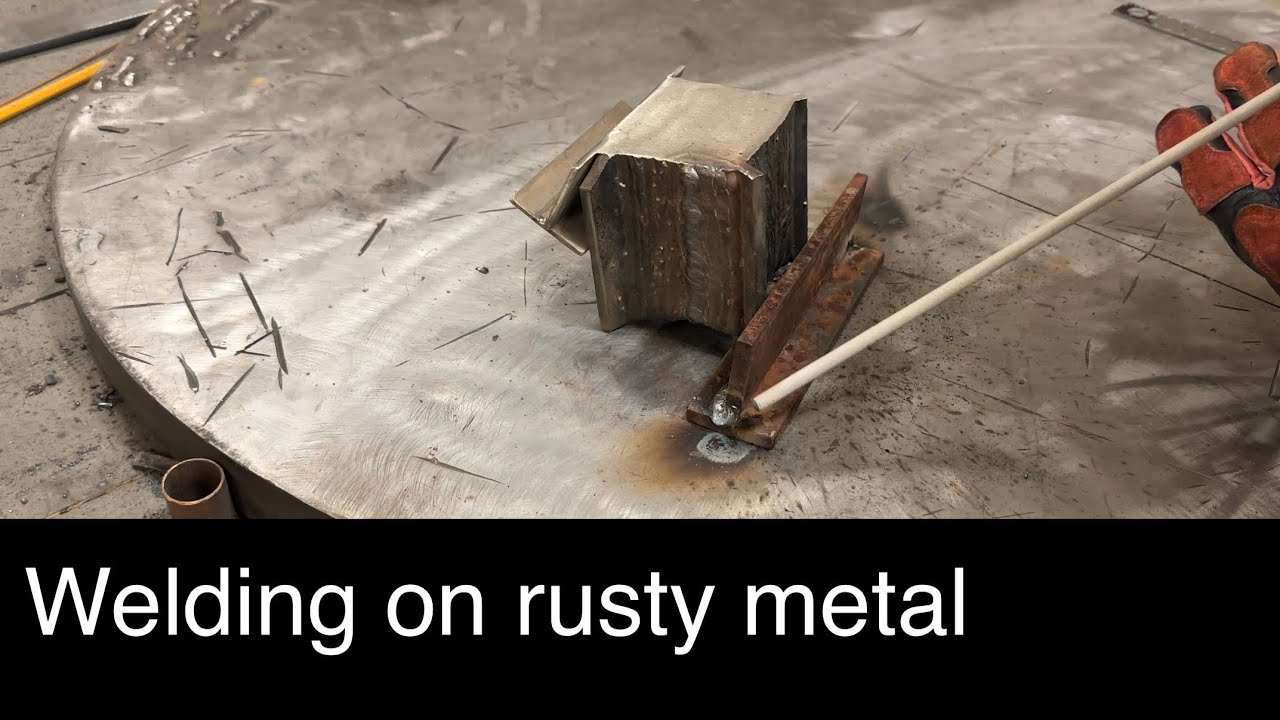
Understanding Rust
What Causes Rust?
To comprehend how to weld rusty metal effectively, it’s crucial to understand the underlying processes that lead to rust formation. Rust is the result of a chemical reaction known as oxidation, which occurs when iron or its alloys, such as steel, come into contact with oxygen and moisture. This reaction is accelerated in the presence of electrolytes, such as saltwater or acids, which further corrode the metal surface.
The process of rust formation can be broken down into several stages:
- Exposure to Oxygen: When metal surfaces are exposed to the air, oxygen molecules react with the iron atoms in the metal, initiating the oxidation process.
- Presence of Moisture: Moisture, whether from rain, humidity, or condensation, provides the necessary medium for the oxygen to react with the iron, speeding up the rusting process.
- Formation of Iron Oxide: As the iron atoms combine with oxygen molecules, they form iron oxide, commonly known as rust. Rust is characterized by its reddish-brown color and brittle, flaky texture.
- Continued Corrosion: Once rust begins to form, it can spread rapidly, compromising the structural integrity of the metal and leading to further deterioration if left unchecked.
Various factors influence the rate of rust formation, including environmental conditions, such as temperature, humidity, and exposure to corrosive substances. Understanding these factors can help welders anticipate and mitigate the effects of rust on metal surfaces, allowing for more effective welding and long-term durability.
Types of Rust
While rust is commonly associated with iron and steel, there are different types of rust that can affect metal surfaces:
- Red Rust: The most common type of rust, red rust, or iron oxide, forms on ferrous metals, such as iron and steel, when exposed to oxygen and moisture. It appears as a reddish-brown coating on the surface of the metal and can vary in thickness and texture.
- White Rust: White rust typically forms on zinc-coated or galvanized surfaces, such as galvanized steel or zinc-plated fasteners. It is caused by the oxidation of zinc, resulting in a powdery white substance that can compromise the protective coating and lead to corrosion.
- Black Rust: Also known as magnetite, black rust forms when iron oxide undergoes further oxidation, resulting in a black or dark gray coloration. While black rust is less common than red rust, it can still occur under certain conditions, particularly in environments with high temperatures and low oxygen levels.
Challenges of Welding Rusty Metal
Welding rusty metal presents a unique set of challenges that require careful consideration and specialized techniques to overcome. From weakened structural integrity to health and safety concerns, welders must be equipped with the knowledge and skills to navigate these obstacles effectively.
Weakened Structural Integrity
One of the primary challenges of welding rusty metal is dealing with compromised structural integrity. Rust weakens the metal surface by corroding and eroding its structure, making it more prone to fractures and failures. When welding rusty metal, the heat from the welding process can further exacerbate these weaknesses, leading to distortion or even collapse of the metal.
To address this challenge, welders must carefully assess the extent of rust damage and take appropriate measures to reinforce the affected areas. This may involve removing heavily corroded sections, strengthening weakened joints, or using additional support structures to compensate for the loss of integrity. Proper surface preparation, including thorough cleaning and rust removal, is essential to ensure a strong and durable weld that can withstand the stresses and strains placed on the metal.
Increased Difficulty in Achieving Strong Welds
Another challenge of welding rusty metal is the increased difficulty in achieving strong, reliable welds. Rust interferes with the welding process by contaminating the metal surface and inhibiting proper fusion between the base metal and the filler material. This can result in poor weld quality, including incomplete penetration, lack of fusion, and porosity, compromising the integrity of the weld joint.
To overcome these challenges, welders must employ specialized techniques and equipment designed for welding rusty metal. This may include using higher heat settings to compensate for heat loss due to rust, selecting appropriate filler materials that can penetrate and bond effectively with the corroded surface, and implementing preheating procedures to reduce the risk of cracking and distortion. Additionally, proper weld bead placement and manipulation techniques can help ensure thorough penetration and fusion, resulting in strong, durable welds that meet the required structural specifications.
Health and Safety Concerns
In addition to structural challenges, welding rusty metal poses health and safety concerns for welders and bystanders. Rust particles and fumes generated during the welding process can contain harmful substances, such as iron oxide, manganese, and other metals, which can cause respiratory irritation, lung damage, and other health problems if inhaled.
To mitigate these risks, welders must take appropriate precautions to minimize exposure to airborne contaminants. This includes wearing personal protective equipment (PPE), such as respirators, goggles, and gloves, to prevent inhalation of fumes and skin contact with rust particles. Adequate ventilation and exhaust systems should also be in place to remove welding fumes and maintain a safe working environment.
Techniques for Welding Rusty Metal
Successfully welding rusty metal requires a combination of proper surface preparation, selecting the appropriate welding method, and adjusting settings and techniques to accommodate the challenges posed by rust. By following these techniques, welders can achieve strong, durable welds on corroded surfaces.
Surface Preparation
- Cleaning: Before welding rusty metal, thorough cleaning of the surface is essential to remove dirt, grease, and other contaminants that can interfere with the welding process. This can be done using wire brushes, sandpaper, or solvent-based cleaners to ensure a clean, bare metal surface.
- Rust Removal: In addition to cleaning, rust removal is crucial to achieve optimal weld quality. Rust can be removed using mechanical methods such as wire brushing, sandblasting, or grinding, or chemical treatments such as rust converters or acid solutions. Care should be taken to remove all traces of rust from the welding area to ensure proper fusion between the base metal and the filler material.
Choosing the Right Welding Method
- Stick Welding (SMAW): Stick welding is a versatile welding process that can be used for welding rusty metal. It utilizes a consumable electrode coated in flux, which creates a protective gas shield around the weld pool, preventing contamination from rust and other impurities. Stick welding is suitable for outdoor and remote welding applications where portability and versatility are essential.
- MIG Welding (GMAW): MIG welding is another popular option for welding rusty metal. It uses a continuous wire electrode and a shielding gas to protect the weld from atmospheric contamination. MIG welding is known for its high welding speeds and ease of use, making it ideal for welding thin to medium-thickness metals with minimal cleanup.
- TIG Welding (GTAW): TIG welding is a precise and versatile welding process that can be used for welding rusty metal with excellent control over heat input and weld quality. It uses a non-consumable tungsten electrode and a separate filler material, if needed, to create clean, precise welds. TIG welding is suitable for welding a wide range of metals and thicknesses, making it ideal for intricate or high-quality welds.
Adjusting Settings and Techniques
- Heat Control: When welding rusty metal, it’s important to adjust the heat settings on the welding machine to compensate for heat loss due to rust. Higher heat settings may be necessary to achieve proper penetration and fusion, especially on heavily corroded surfaces. However, care should be taken to avoid overheating the metal, which can lead to distortion and weakening of the weld joint.
- Welding Speed: Controlling the welding speed is crucial for achieving consistent and high-quality welds on rusty metal. Welding too quickly can result in insufficient penetration, while welding too slowly can lead to excessive heat buildup and potential burn-through. Adjusting the welding speed based on the thickness of the metal and the extent of rust damage can help ensure optimal weld quality.
- Filler Material Selection: Selecting the right filler material is essential for welding rusty metal effectively. Filler materials with higher alloy content, such as stainless steel or nickel-based alloys, are often preferred for welding rusty or corroded surfaces due to their superior corrosion resistance and mechanical properties. Matching the filler material to the base metal and adjusting the welding technique accordingly can help achieve strong, durable welds on rusty metal.
Tips for Successful Rusty Metal Welding
Successfully welding rusty metal requires more than just technical skill—it also demands attention to safety, preparation, and ongoing maintenance. Here are some essential tips to ensure your rusty metal welding projects are a success:
Proper Ventilation
Proper ventilation is crucial when welding rusty metal to minimize exposure to harmful fumes and gases. Ensure that your workspace is well-ventilated, either by working outdoors or using exhaust fans and ventilation systems to remove welding fumes and maintain a clean, breathable atmosphere. Additionally, consider wearing a respirator with appropriate filters to protect yourself from inhaling potentially toxic contaminants released during the welding process.
Protective Gear
Welding produces intense heat, sparks, and UV radiation, making it essential to wear appropriate protective gear to prevent injury. Invest in high-quality welding helmets with auto-darkening filters to shield your eyes and face from harmful light and sparks. Wear flame-resistant clothing, leather gloves, and closed-toe boots to protect your skin from burns and abrasions. Additionally, use welding curtains or screens to create a safe work area and prevent bystanders from being exposed to welding hazards.
Practice on Scrap Metal
Before tackling a complex welding project on rusty metal, take the time to practice your welding techniques on scrap metal with similar properties and thickness. This allows you to familiarize yourself with the behavior of rusty metal during welding and refine your welding settings and techniques accordingly. Experiment with different welding methods, filler materials, and heat settings to determine the optimal parameters for achieving strong, reliable welds on corroded surfaces.
Regular Maintenance
Once you’ve completed your welding project on rusty metal, it’s essential to perform regular maintenance to ensure the integrity and longevity of the welds. Inspect the welded joints periodically for signs of corrosion, cracking, or fatigue, and address any issues promptly to prevent further damage. Apply protective coatings, such as paint or rust inhibitors, to the welded surfaces to prevent future rust formation and corrosion. By staying proactive with maintenance, you can extend the lifespan of your welds and keep your metal structures in optimal condition for years to come.
Common Mistakes to Avoid
While welding rusty metal presents its own set of challenges, certain mistakes can exacerbate these challenges and compromise the quality of the welds. Here are some common mistakes to avoid when welding rusty metal:
Neglecting Proper Surface Preparation
Proper surface preparation is crucial for achieving strong, durable welds on rusty metal. Neglecting this step can lead to contamination, poor fusion, and weakened weld joints. Ensure that you thoroughly clean and remove all rust, dirt, and contaminants from the welding area before starting the welding process. Use wire brushes, sandpaper, or chemical treatments to clean the surface effectively. Skipping or rushing through surface preparation can result in subpar welds that are prone to failure.
Overheating the Metal
Overheating the metal during welding can have detrimental effects on the integrity of the welds and the surrounding material. Excessive heat can cause distortion, warping, and even burn-through of the metal, leading to weakened weld joints and structural instability. To avoid overheating, carefully monitor the heat input and adjust the welding parameters accordingly. Use proper welding techniques, such as maintaining a consistent arc length and travel speed, to control the heat and prevent overheating. Additionally, consider preheating the metal to reduce the risk of thermal stress and distortion during welding.
Using Incorrect Welding Techniques
Using incorrect welding techniques can result in poor weld quality and compromised structural integrity. Different welding methods require specific techniques and parameters to achieve optimal results. Make sure you are familiar with the proper techniques for the welding method you are using, whether it’s stick welding, MIG welding, or TIG welding. Pay attention to factors such as electrode selection, welding polarity, travel speed, and heat input to ensure consistent and reliable welds. Experimenting with unfamiliar techniques or improvising can lead to welding defects and costly rework.
Safety Precautions
Welding, especially on rusty metal, involves inherent risks to the welder’s health and safety. Implementing proper safety precautions is essential to mitigate these risks and ensure a safe working environment. Here are some crucial safety measures to observe when welding rusty metal:
Respiratory Protection
Welding produces hazardous fumes and gases, including metal oxides, ozone, and nitrogen oxides, which can pose serious health risks if inhaled. Protect your respiratory system by wearing appropriate respiratory protection, such as a powered air-purifying respirator (PAPR) or a respirator equipped with high-efficiency particulate air (HEPA) filters. Ensure that your respirator fits snugly and is properly maintained to provide effective protection against welding fumes and airborne contaminants.
Eye Protection
Welding generates intense light and radiation, including ultraviolet (UV) and infrared (IR) radiation, which can cause eye injuries and vision damage if not adequately protected. Wear a welding helmet with a proper shade lens to shield your eyes from harmful UV and IR radiation during welding. Ensure that your helmet is equipped with an auto-darkening filter to automatically adjust the shade level based on the welding arc intensity. Additionally, wear safety glasses or goggles underneath your welding helmet to protect your eyes from flying debris and sparks.
Fire Prevention Measures
Welding operations can pose a fire hazard due to the presence of flammable materials, such as oils, paints, and gases, as well as sparks and hot metal particles generated during welding. Take proactive measures to prevent fires by clearing the work area of flammable materials and ensuring proper ventilation to remove combustible gases and fumes. Keep a fire extinguisher nearby and familiarize yourself with its operation in case of emergencies. Additionally, use welding blankets or fire-resistant barriers to protect surrounding surfaces and prevent accidental ignition.
FAQs
Can I weld rusty metal with a basic welding machine?
While basic welding machines can be used, it’s essential to ensure they provide sufficient power and heat control for welding rusty metal effectively.
Do I need to remove all rust before welding?
While thorough surface preparation is recommended, complete removal of rust may not always be feasible. However, it’s crucial to remove loose rust and contaminants to ensure proper weld penetration.
How can I protect myself from welding fumes when working with rusty metal?
Wearing a proper welding helmet with a respirator attachment and working in a well-ventilated area can help minimize exposure to welding fumes.
Can I weld rusty metal outdoors?
Welding outdoors presents additional challenges due to environmental factors such as wind and humidity. If welding outdoors, take extra precautions to protect against moisture and ensure adequate ventilation.
Is it possible to prevent rust from forming after welding?
Applying a suitable rust-inhibiting primer or coating after welding can help protect the welded area from future corrosion.
Conclusion
In conclusion, while welding rusty metal presents challenges, it is a feasible task with the right knowledge, techniques, and precautions. By understanding the effects of rust on metal, adequately preparing the surface, selecting appropriate welding methods, and prioritizing safety, welders can achieve strong and durable welds on rusty surfaces, prolonging the lifespan of metal components and structures.