How to Choose the Right Welding Rod?
Welding is a versatile and indispensable process in various industries, from construction to automotive, and even in artistic endeavors. To achieve strong, durable, and visually appealing welds, it’s essential to choose the right welding rod for the job. Welding rods, also known as welding electrodes, come in various types, each designed for specific materials and applications. This guide will help you navigate the complex world of welding rods and make informed choices based on your welding needs.
The Importance of Choosing the Right Welding Rod
Welding rods play a pivotal role in the welding process. They serve as a consumable electrode that melts and forms the weld seam when an electric arc is struck between the rod and the workpiece. The choice of welding rod influences the weld’s quality, strength, and appearance. Using the wrong welding rod can lead to poor results, including weak welds, excessive splatter, and even safety hazards.
Here are some key reasons why choosing the right welding rod is essential:
- Material Compatibility: Different welding rods are designed to work with specific materials. Using a welding rod that is incompatible with your base metal can result in a weak bond or even damage the workpiece.
- Strength and Durability: The right welding rod will ensure that your welds are strong, durable, and capable of withstanding the intended load and environmental conditions.
- Weld Appearance: Some welding rods are better suited for achieving visually appealing welds, making them ideal for projects where aesthetics are important.
- Safety: Using the correct welding rod not only improves the quality of the weld but also reduces the risk of accidents, such as arc blow, splatter, or welding fumes.
Types of Welding Rods
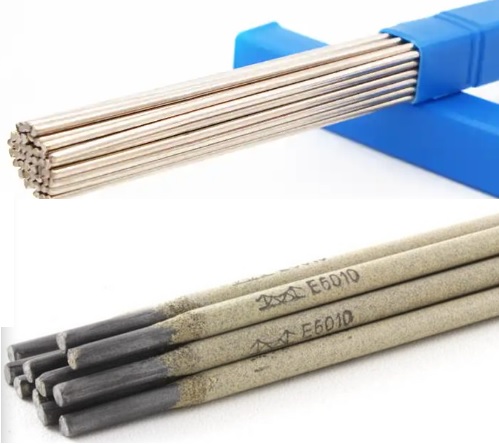
Welding rods are categorized into various types based on their composition, coating, and intended applications. It’s crucial to understand these different types to choose the right welding rod for your specific welding project. Here are some common types of welding rods:
Shielded Metal Arc Welding (SMAW) Electrodes:
Shielded Metal Arc Welding, commonly known as stick welding, uses SMAW electrodes. These electrodes have a metal core and are covered with a flux coating that provides a protective gas shield during the welding process. SMAW electrodes are versatile and can be used for various materials, including carbon steel, stainless steel, and cast iron.
Gas Metal Arc Welding (GMAW) Electrodes:
Gas Metal Arc Welding, or MIG welding, employs GMAW electrodes. These solid wire electrodes are used with a shielding gas, typically a mixture of argon and carbon dioxide. GMAW electrodes are well-suited for welding a wide range of materials, such as steel, aluminum, and stainless steel.
Flux-Cored Arc Welding (FCAW) Electrodes:
Flux-Cored Arc Welding uses FCAW electrodes, which are tubular wires filled with a flux material. FCAW electrodes can be used with or without shielding gas, making them suitable for outdoor and windy conditions. They are often used in applications like shipbuilding and construction.
Gas Tungsten Arc Welding (GTAW) Electrodes:
Gas Tungsten Arc Welding, or TIG welding, relies on GTAW electrodes, which are made of pure tungsten or tungsten alloys. TIG welding is primarily used for non-ferrous metals like aluminum and magnesium. These electrodes do not melt during the welding process but create an electric arc that melts the base metal.
Submerged Arc Welding (SAW) Electrodes:
Submerged Arc Welding employs SAW electrodes that are designed for high-speed, high-deposition welding. They are commonly used in applications where thick materials need to be joined quickly, such as in the fabrication of large steel structures.
Bare Electrodes:
Bare electrodes, as the name suggests, have no flux coating. They are mainly used in applications like gas welding, where a separate flux is added to protect the weld pool. These electrodes are less common than others and are typically used for specialized purposes.
Factors to Consider When Choosing a Welding Rod
Selecting the right welding rod involves considering various factors that are specific to your welding project. Here are the key factors to keep in mind:
Material Compatibility:
The first and most crucial consideration is the compatibility of the welding rod with the base material you’re working with. Different materials, such as carbon steel, stainless steel, aluminum, and cast iron, require specific types of welding rods. Consult the American Welding Society (AWS) classification system to ensure compatibility.
Electrode Diameter:
Welding rods come in various diameters, and the choice depends on the thickness of the material you’re welding. Thicker materials generally require thicker electrodes. A rule of thumb is to use an electrode diameter that is equal to or slightly smaller than the material thickness.
Welding Position:
Consider the welding position, whether it’s flat, horizontal, vertical, or overhead. Some welding rods are better suited for certain positions due to their flux composition and characteristics. Make sure the rod you choose is appropriate for the welding position you’ll be working in.
Welding Current:
Understanding the required welding current is essential for selecting the right welding rod. The current influences the melting rate of the rod and the penetration depth of the weld. Consult the manufacturer’s recommendations and adjust your welding machine accordingly.
Welding Environment:
The environment in which you’ll be welding also plays a role in rod selection. If you’re working outdoors or in a windy area, you may prefer flux-cored electrodes that are less sensitive to atmospheric conditions.
Weld Quality and Appearance:
Consider the desired quality and appearance of the weld. Some welding rods produce cleaner and smoother welds, making them ideal for applications where aesthetics matter. If appearance is critical, choose a rod that provides the desired finish.
Manufacturer Recommendations:
Always consult the manufacturer’s recommendations and specifications for the welding rod. Manufacturers provide valuable information about the rod’s properties, suitable applications, and welding parameters.
Cost and Availability:
While quality is essential, consider the cost and availability of the welding rod. Ensure that the rod you choose fits within your budget and is readily available for your project.
Safety Considerations:
Ensure that you are aware of the safety requirements and precautions associated with the welding rod you select. Some electrodes may produce more fumes or require additional safety measures, so it’s crucial to take these into account.
Recommendations for Different Welding Rods
As an Amazon Associate, We earn from qualifying purchases.
Now that you understand the importance of selecting the right welding rod and the factors to consider, let’s explore some specific recommendations for different welding rods based on common welding applications. Please note that these recommendations are for informational purposes only, and it’s essential to verify compatibility and suitability for your specific project.
1. For General Purpose Welding (Carbon Steel):
- Recommended Welding Rod: E6013
- Product Recommendation: Hobart 770466 6013 Stick, 1/8-10lbs
E6013 welding rods are a popular choice for general-purpose welding, especially when working with carbon steel. They are known for their ease of use and versatility, making them suitable for a wide range of applications. The Hobart 770466 6013 Stick Welding Rods, available in a 10-pound package, provide a reliable and consistent welding experience. These electrodes are designed to produce clean and smooth welds, making them an excellent choice for both beginners and experienced welders working with carbon steel. The link provided will take you to the product page on Amazon, where you can find more details and purchase the product for your welding needs.
2. For Stainless Steel Welding:
- Recommended Welding Rod: E308L-16
- Product Recommendation: Blue Demon E308L-16 X 1/8″ X 14″ X 5LB Plastic Stainless Steel Arc Welding Electrode
When working with stainless steel, it’s crucial to choose the right welding rod to prevent the formation of unwanted carbides that can weaken the material. E308L-16 is an excellent choice for welding stainless steel due to its low carbon content and ability to produce strong and clean welds.
3. For Aluminum Welding:
- Recommended Welding Rod: ER4043
- Product Recommendation: YESWELDER Aluminum TIG Welding Rod ER4043 3/32″x16″ 5LB
When welding aluminum, you should use a welding rod specifically designed for this material. ER4043 is a common choice for welding aluminum, providing good strength and resistance to corrosion. It’s suitable for both TIG and MIG welding.
4. For Cast Iron Welding:
- Recommended Welding Rod: ENiFe-CI
- Product Recommendation: Forney 30685 E7018 AC Welding Rod, 1/8-Inch, 5-Pound
Cast iron can be challenging to weld due to its high carbon content. ENiFe-CI electrodes are designed specifically for cast iron welding, and they provide a strong and durable bond. Be sure to preheat the cast iron piece to prevent cracking during welding.
5. For Outdoor and Windy Conditions:
- Recommended Welding Rod: E71T-1
- Product Recommendation: Hobart H222106-R22 10-Pound E71T-11 Carbon-Steel Flux-Cored Welding Wire, 0.030-Inch
When welding outdoors or in windy conditions, it’s essential to use a welding rod that can handle the challenges of the environment. E71T-1 is a flux-cored electrode that doesn’t require shielding gas and is less susceptible to atmospheric conditions, making it suitable for outdoor projects.
6. For High-Quality Welds and Aesthetics:
- Recommended Welding Rod: E7018
- Product Recommendation: Forney 30705 E7018 Welding Rod, 3/32-Inch, 5-Pound
If you need to produce high-quality, clean, and visually appealing welds, E7018 is an excellent choice. It’s known for its low hydrogen content, which results in welds with minimal porosity and excellent aesthetics. This rod is often used in applications where the appearance of the weld is essential.
7. For Maintenance and Repair Welding:
- Recommended Welding Rod: E6010
- Product Recommendation: E6010 3/32″-1/8″-5/32″ Stick electrodes welding rod 2 lb, 4 lb (2 lb, 1/8″)
E6010 welding rods are suitable for maintenance and repair welding, especially when working on dirty, rusted, or painted surfaces. They provide deep penetration and can be used in various positions. E6010 is an excellent choice for jobs where you need to join or repair different types of metal.
Conclusion
Choosing the right welding rod is crucial for achieving strong, durable, and aesthetically pleasing welds. To make an informed choice, consider factors such as material compatibility, electrode diameter, welding position, current, and the welding environment. Always consult manufacturer recommendations and adhere to safety precautions.
Different welding rods are designed for specific applications, and by selecting the right one, you can ensure the success of your welding project. Whether you’re working with carbon steel, stainless steel, aluminum, or other materials, there’s a welding rod tailored to your needs.
Keep in mind that the welding rod recommendations provided here are general guidelines. Be sure to verify the compatibility and suitability of the welding rod for your specific project and consult with welding professionals or experts if you have any doubts. Safety should always be a top priority in welding projects, so follow safety guidelines and wear the necessary protective equipment.
To get started with your welding projects, consider the product recommendations listed in this article, which are available on Amazon. These products are selected based on their quality and customer reviews. By choosing the right welding rod and using high-quality materials, you can achieve professional results in your welding endeavors.