Cobot vs. Robot – Welding Automation
Introduction
Understanding Welding Automation
Welding automation has revolutionized the manufacturing industry, making processes faster, more efficient, and more precise. But what exactly is welding automation? It involves using automated machines to perform welding tasks traditionally done by human welders. The use of these machines can significantly reduce errors, increase production speed, and enhance overall quality.
The Evolution of Welding Automation
Welding automation has come a long way since its inception. Initially, welding robots were introduced to handle repetitive and hazardous tasks. Over time, advancements in technology have given rise to collaborative robots, or cobots, which work alongside human operators, making welding processes even more flexible and efficient.
Importance of Welding Automation in Modern Industry
In today’s competitive market, welding automation is crucial for maintaining high standards of production. It not only improves efficiency and accuracy but also ensures the safety of workers by handling dangerous tasks. This has led to increased adoption of welding automation in various industries, from automotive to aerospace.
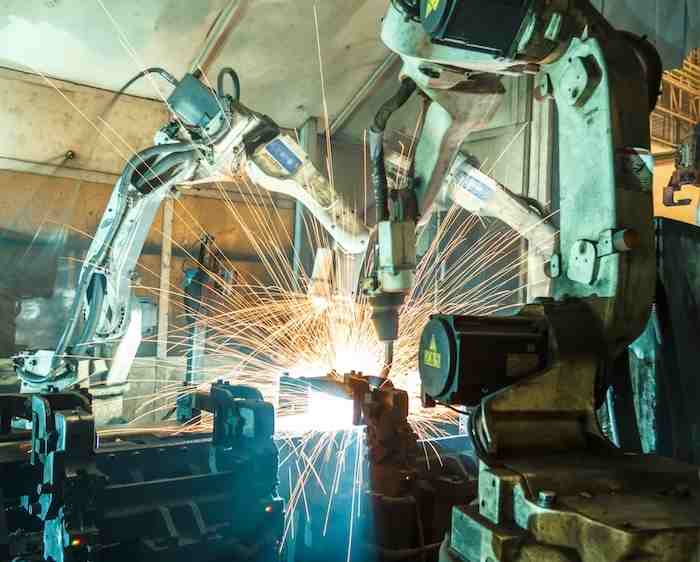
What is a Robot?
Definition and Characteristics of Robots
Robots are automated machines designed to perform specific tasks with high precision and consistency. They are programmed to carry out repetitive actions and can work tirelessly without fatigue. In welding, robots are often used for their ability to produce consistent welds and handle heavy workloads.
Applications of Robots in Welding
Types of Robots Used in Welding
There are several types of robots used in welding, including articulated robots, gantry robots, and SCARA robots. Each type has its own set of features and is suited for different welding tasks. For instance, articulated robots have multiple joints, making them highly flexible and ideal for complex welding operations.
Advantages of Using Robots in Welding
Robots offer numerous advantages in welding, such as increased productivity, improved weld quality, and reduced labor costs. They can work continuously without breaks, ensuring high output levels. Additionally, robots can operate in hazardous environments, reducing the risk of injury to human workers.
What is a Cobot?
Definition and Characteristics of Cobots
Cobots, or collaborative robots, are designed to work alongside human operators. Unlike traditional robots, cobots are equipped with advanced sensors and safety features that allow them to interact safely with humans. They are easy to program and can be quickly reconfigured for different tasks, making them highly versatile.
Applications of Cobots in Welding
Types of Cobots Used in Welding
There are various types of cobots used in welding, including lightweight cobots and heavy-duty cobots. Lightweight cobots are ideal for delicate welding tasks that require precision, while heavy-duty cobots can handle more robust welding operations. The flexibility of cobots makes them suitable for a wide range of welding applications.
Advantages of Using Cobots in Welding
Cobots offer several benefits in welding, such as enhanced flexibility, ease of use, and improved safety. They can be easily integrated into existing workflows and quickly adapted to new tasks. Cobots also reduce the need for extensive safety measures, as they are designed to work safely alongside human operators.
Comparing Cobots and Robots in Welding
Cost Comparison
When it comes to cost, cobots generally have a lower upfront cost compared to traditional robots. This makes them an attractive option for small to medium-sized businesses. However, the total cost of ownership, including maintenance and operational costs, should be considered when making a decision.
Safety Considerations
Safety is a critical factor in welding automation. Cobots are designed with safety features that allow them to operate alongside humans without causing harm. Traditional robots, on the other hand, often require safety cages and extensive safety protocols to prevent accidents.
Flexibility and Adaptability
Cobots are known for their flexibility and adaptability. They can be easily programmed and reprogrammed for different tasks, making them ideal for dynamic production environments. Robots, while also flexible, may require more complex programming and setup.
Efficiency and Productivity
Both robots and cobots can significantly enhance efficiency and productivity in welding operations. Robots excel in high-volume, repetitive tasks, while cobots are better suited for tasks that require human oversight and adaptability. The choice between the two depends on the specific needs of the production process.
Maintenance and Support
Maintenance and support are important considerations when choosing between cobots and robots. Cobots tend to have simpler maintenance requirements due to their design and functionality. Robots, being more complex, may require more extensive maintenance and specialized support.
Future Trends in Welding Automation
Innovations in Cobot Technology
The future of cobots looks promising with advancements in AI and machine learning, making them smarter and more adaptable. Enhanced sensors and better human-robot interaction interfaces will further improve their safety and usability.
Innovations in Robot Technology
Robots are also evolving with increased precision, speed, and connectivity. Integration with IoT and advanced analytics allows for real-time monitoring and optimization, pushing the boundaries of what’s possible in welding automation.
Impact on the Welding Industry
As technology advances, the distinction between cobots and robots may blur, with hybrid systems offering the best of both worlds. The welding industry is set to benefit from these advancements, leading to higher efficiency, improved safety, and reduced costs.
FAQs
What is the main difference between a robot and a cobot in welding?
The main difference lies in their design and functionality. Robots are typically used for high-volume, repetitive tasks and often require safety cages. Cobots, on the other hand, are designed to work alongside humans and come with advanced safety features that allow for safe interaction.
Which is more cost-effective, a robot or a cobot?
Cobots generally have a lower upfront cost compared to traditional robots, making them more cost-effective for small to medium-sized businesses. However, the total cost of ownership, including maintenance and operational costs, should also be considered.
Are cobots safe to work alongside human workers?
Yes, cobots are equipped with advanced sensors and safety features that allow them to operate safely alongside human workers. They are designed to stop or slow down if they detect an obstacle, ensuring a safe working environment.
Can both robots and cobots be used for complex welding tasks?
Yes, both robots and cobots can be used for complex welding tasks. Robots are ideal for tasks that require high precision and consistency, while cobots are better suited for tasks that require flexibility and human oversight.
What should I consider when choosing between a robot and a cobot for welding?
When choosing between a robot and a cobot for welding, consider factors such as cost, safety, flexibility, efficiency, and maintenance. Assessing the specific needs of your production process will help you make the best choice for your business.
Conclusion
In the debate between cobots and robots for welding automation, there is no one-size-fits-all answer. The choice depends on your specific needs, including production volume, task complexity, and budget. Both technologies have their strengths and can significantly enhance your welding operations when applied correctly. As the industry evolves, staying informed about the latest advancements will ensure you remain competitive and efficient.