Different Types of Iron and Their Weldability
Introduction
Iron plays a pivotal role in a multitude of industries, serving as a fundamental building block for countless applications. From construction to manufacturing, transportation to infrastructure, the versatility of iron makes it an indispensable material. Understanding the weldability of different types of iron is paramount in ensuring the integrity and longevity of welded structures. This knowledge is especially critical for welders, engineers, and professionals involved in metalworking, as it influences the choice of welding processes and materials.
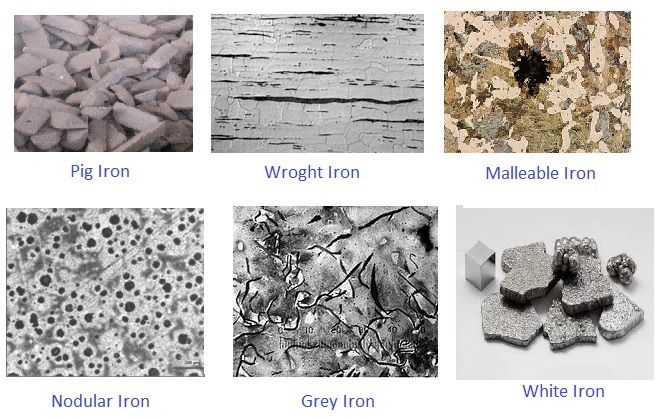
Purpose of Exploring Various Iron Types and Their Weldability
The exploration of various iron types and their weldability serves multiple purposes. First and foremost, it provides a comprehensive understanding of the diverse range of irons available in the market. Each type possesses distinct properties, strengths, and weaknesses, influencing their suitability for specific applications. By delving into the weldability of wrought iron, dead mild steel, medium carbon steel, and other variants, one can tailor welding approaches to the unique demands of each material.
Types of Iron
Wrought Iron
Overview of Properties
- Wrought iron is characterized by its fibrous grain structure, which imparts superior malleability.
- It typically has a low carbon content, making it resistant to corrosion.
- The presence of slag fibers contributes to its unique appearance and texture.
Industrial Uses
- Historically, wrought iron found widespread use in ornamental applications, including gates, railings, and decorative elements.
- Its malleability made it a preferred choice for traditional blacksmithing, enabling intricate and artistic designs.
- While less common in modern construction, wrought iron is still utilized in specialty applications due to its aesthetic and corrosion-resistant properties.
Weldability Considerations
- Wrought iron generally exhibits favorable weldability due to its low carbon content.
- Preheating may be necessary for larger sections to prevent cracking during welding.
- Proper selection of welding processes, such as shielded metal arc welding (SMAW) or gas metal arc welding (GMAW), is crucial for achieving quality welds.
Dead Mild Steel
Composition and Properties
- Dead mild steel is a low carbon steel variant, typically containing less than 0.15% carbon.
- Its composition provides excellent ductility and weldability.
- The low carbon content contributes to its malleability and ease of fabrication.
Common Uses
- Dead mild steel is commonly employed in the fabrication of sheet metal components.
- Applications include the manufacturing of automotive panels, household appliances, and general-purpose structural elements.
- Its versatility makes it suitable for various industries, especially where formability and weldability are critical.
Weldability Factors
- Weldability is high due to the low carbon content, allowing for ease of welding using processes such as MIG or TIG welding.
- Filler material selection is important to match the base metal properties and achieve strong welds.
- Post-weld treatments may be necessary to address any potential issues related to brittleness.
Mild Steel
Properties and Applications
- Mild steel is a low carbon steel variant known for its affordability, formability, and versatility.
- It is widely used in construction, automotive manufacturing, and general fabrication.
- Mild steel is characterized by its ease of machining, welding, and bending.
Weldability Considerations
- Weldability considerations for mild steel involve selecting appropriate welding methods based on material thickness.
- Common welding processes include MIG and TIG welding.
- Pre-cleaning of the material surface and post-weld treatments contribute to achieving optimal weld quality.
Distinction from Other Iron Types
- Mild steel is distinguished by its lower carbon content compared to medium and high carbon steels.
- Its lower hardness and increased ductility make it suitable for a wide range of applications where strength and formability are key.
Medium Carbon Steel
Alloying Elements and Characteristics
- Medium carbon steel contains a higher carbon content, typically between 0.3% and 0.6%.
- Alloying elements like manganese contribute to improved mechanical properties, including strength and hardness.
- It exhibits enhanced wear resistance compared to low carbon steels.
Industrial Applications
- Medium carbon steel finds applications in gears, shafts, and automotive components where increased strength and wear resistance are essential.
- Its versatility makes it suitable for various engineering and manufacturing applications.
Weldability Challenges and Solutions
- Challenges arise in welding medium carbon steel due to increased carbon content.
- Control of heat input and preheating are critical to prevent issues like cracking.
- Selection of suitable filler materials becomes crucial to maintain the desired mechanical properties in the welded joint.
High Carbon Steel
Properties and Uses
- High carbon steel has a significantly higher carbon content, often exceeding 0.6%.
- It is known for exceptional hardness and wear resistance, making it suitable for cutting tools, blades, and high-strength applications.
- The increased carbon content contributes to the material’s brittleness.
Weldability Issues
- Weldability of high carbon steel is challenging due to its susceptibility to cracking during welding.
- Precise control of heat input and welding parameters is necessary to mitigate the risk of cracking.
- Post-weld heat treatment may be required to restore or enhance the material’s properties.
Heat Treatment Effects on Weldability
- Heat treatment can impact the weldability of high carbon steel.
- Understanding the effects of heat treatment on the material is crucial for maintaining the balance between hardness and toughness.
Very High Carbon Steel
Characteristics
- Very high carbon steel contains an extremely high carbon content, often exceeding 1.0%.
- It exhibits extreme hardness and is used in specialized applications such as springs and high-strength wire.
- The material’s brittleness poses challenges in welding.
Specialized Applications
- Very high carbon steel finds applications where extreme hardness and resistance to deformation are critical.
- It is commonly employed in the production of components subjected to high stress and wear.
Welding Challenges and Precautions
- Welding challenges include the heightened risk of cracking due to the high carbon content.
- Precise control of heat input, preheating, and careful filler material selection are essential precautions in welding very high carbon steel.
Gray Cast Iron
Composition and Properties
- Gray cast iron is characterized by its graphite flakes embedded in a metallic matrix.
- It has excellent casting properties, allowing for intricate and complex shapes.
- The material often contains other elements such as silicon and manganese.
Common Applications
- Gray cast iron is widely used in applications where its excellent casting properties are advantageous.
- Common applications include engine blocks, pipes, and various industrial components.
- The material’s damping capacity also makes it suitable for certain vibration-damping applications.
Challenges in Welding Gray Cast Iron
- Challenges arise during the welding of gray cast iron due to its high carbon content.
- The presence of graphite flakes can lead to brittleness and cracking during welding.
- Preheating and post-weld stress relief annealing are crucial to minimize the risk of cracking and achieve a sound weld.
White Cast Iron
Overview of Properties
- White cast iron is characterized by its hard and brittle nature, resulting from the absence of graphite.
- It contains carbide structures, contributing to its high wear resistance.
- White cast iron is known for its hardness but lacks the ductility of other iron types.
Industrial Uses
- White cast iron is employed in applications requiring high wear resistance.
- Common industrial uses include the production of grinding balls, liners, and other components subjected to abrasion.
- The material’s hardness makes it suitable for wear-intensive environments.
Weldability Considerations
- Welding white cast iron is challenging due to its hardness and brittleness.
- Selecting appropriate welding processes and materials is crucial to avoid cracking.
- Post-weld heat treatments may be necessary to improve the ductility of the welded joint.
Malleable Cast Iron
Characteristics and Processing
- Malleable cast iron undergoes a heat treatment process called annealing to convert its brittle white iron structure into a more ductile form.
- This process forms nodules of graphite within the material, enhancing its malleability.
- Malleable cast iron retains good strength while exhibiting improved ductility.
Applications
- Malleable cast iron is utilized in applications where both strength and malleability are required.
- Common applications include the manufacturing of pipe fittings, agricultural equipment, and certain automotive components.
- The material’s ability to be shaped and formed makes it suitable for a range of fabrication processes.
Weldability Factors
- Weldability of malleable cast iron is generally good due to its improved ductility.
- Preheating may be required to prevent cracking, and suitable filler materials should be chosen to match the material’s properties.
- Post-weld treatments may be applied to relieve residual stresses and enhance the overall quality of the weld.
Factors Affecting Weldability
Weldability, the ease with which a material can be welded, is influenced by a variety of factors. Understanding these factors is crucial for achieving strong, reliable welds. Here, we explore the key elements affecting the weldability of different types of iron.
Carbon Content
The carbon content of iron significantly impacts its weldability. In general, low carbon content enhances weldability, as it reduces the likelihood of cracking during welding. However, high carbon content, as seen in certain types of steel, can introduce challenges. High carbon levels can lead to increased hardness and susceptibility to cracking, necessitating careful control of welding parameters, preheating, and post-weld treatments to ensure successful welds.
Alloying Elements
The presence of alloying elements in iron can both positively and negatively affect weldability. Alloying elements like manganese, silicon, and nickel are often added to improve specific properties of the material, such as strength or corrosion resistance. However, their impact on weldability varies. While some alloying elements may enhance the material’s ability to be welded, others can introduce challenges, such as increased susceptibility to cracking. Therefore, a thorough understanding of the specific alloying elements in the material is essential for selecting appropriate welding processes and techniques.
Heat Treatment Effects
Heat treatment is a critical factor influencing the weldability of iron. The heat treatment history of a material can alter its microstructure and mechanical properties, affecting how it responds to welding processes. For instance, materials that have undergone certain heat treatments may exhibit increased hardness, which can pose challenges during welding. Welders must be cognizant of the material’s heat treatment condition and adjust welding parameters accordingly to ensure optimal weldability.
Impurities and Contaminants
The presence of impurities and contaminants in iron can have significant repercussions on weldability. Inclusions, such as sulfur and phosphorus, can lead to the formation of undesirable compounds and increase the risk of weld defects. Proper cleaning and preparation of the material surface are crucial to remove impurities that could compromise the quality of the weld. Additionally, selecting suitable welding processes and filler materials is essential to minimize the impact of impurities on the weld.
Microstructure Considerations
The microstructure of iron, including the arrangement of grains and phases, plays a vital role in determining its weldability. Different types of iron exhibit varied microstructures, ranging from the fibrous structure of wrought iron to the graphite flakes in cast iron. Welders need to consider the material’s microstructure when planning and executing welding processes. The goal is to maintain or modify the microstructure in a way that preserves the material’s integrity and desired properties. Preheating, controlled cooling rates, and post-weld treatments may be employed to manage microstructure changes and enhance overall weldability.
Welding Processes for Different Iron Types
Welding processes are diverse, and their suitability varies depending on the type of iron being used. Here, we explore various welding methods and their applications across different types of iron.
Arc Welding
Arc welding is a widely used method that utilizes an electric arc to melt and fuse metals. Different arc welding processes are suitable for various types of iron:
Shielded Metal Arc Welding (SMAW)
- SMAW, commonly known as stick welding, is versatile and applicable to a broad range of iron types.
- It involves an electrode with a flux coating, creating a shield around the weld pool to protect it from atmospheric contamination.
- SMAW is suitable for welding wrought iron, mild steel, and certain cast irons.
Gas Metal Arc Welding (GMAW)
- GMAW, or MIG welding, uses a continuous wire electrode and a shielding gas to protect the weld.
- It is well-suited for welding mild steel and low carbon steel.
- GMAW offers high deposition rates and is commonly used in manufacturing and automotive applications.
Flux-Cored Arc Welding (FCAW)
- FCAW uses a tubular wire filled with flux, providing both shielding and deoxidizing agents.
- This process is suitable for high-strength steels and can be used in outdoor or windy conditions.
- FCAW is effective in welding medium to high carbon steels.
Gas Welding
Gas welding processes utilize the heat generated by a flame to melt and join metals. These methods are applicable to certain types of iron:
Oxy-Acetylene Welding
- Oxy-acetylene welding is a versatile process suitable for various types of iron, including wrought iron and mild steel.
- It is often used for fabrication, repairs, and maintenance work.
- Oxy-acetylene welding allows for precise control of heat and is suitable for thinner materials.
Oxy-Fuel Cutting
- Oxy-fuel cutting utilizes the exothermic reaction between oxygen and a fuel gas to cut through iron.
- It is commonly used for cutting thick sections of mild steel and cast iron.
- Oxy-fuel cutting is effective for shape cutting and can be employed in demolition and manufacturing processes.
Resistance Welding
Resistance welding involves the generation of heat by passing current through the workpieces, causing them to fuse. This method is particularly effective for certain iron types:
Spot Welding
- Spot welding is widely used in the automotive industry for joining sheets of mild steel.
- It involves applying localized pressure and electrical current to create a weld at a specific spot.
- Spot welding is fast and cost-effective for joining thin sections.
Seam Welding
- Seam welding is a continuous process where overlapping welds are created along the entire seam.
- It is suitable for joining sheets of wrought iron, mild steel, and certain cast irons.
- Seam welding is commonly used in the production of tanks, pipes, and automotive components.
Other Specialized Welding Processes for Specific Iron Types
Beyond the commonly used processes, specialized welding methods cater to specific iron types:
- Submerged Arc Welding (SAW): Effective for welding thick sections of steel, including mild and low alloy steels.
- Electroslag Welding (ESW): Suitable for joining thick sections of steel, particularly in vertical positions.
- TIG Welding (GTAW): Tungsten Inert Gas welding is versatile and suitable for welding various types of iron, providing precise control over the weld pool.
Challenges and Precautions in Welding Different Iron Types
Welding different types of iron presents unique challenges, and addressing these challenges requires careful consideration and the implementation of specific precautions. Here, we explore common challenges and the precautions necessary to ensure successful welding across various iron types.
Welding-Induced Stresses
- Challenge:
- The welding process introduces thermal stresses, leading to distortion and potential structural issues.
- Precautions:
- Controlled Welding Sequence: Gradual welding from the center outward helps distribute stresses evenly.
- Backstepping Technique: Welding in short increments and alternating sides minimizes stress accumulation.
- Preheating: Applying controlled preheating can reduce thermal gradients and mitigate stress.
Distortion and Warping
- Challenge:
- Rapid heating and cooling during welding can result in distortion and warping of the workpiece.
- Precautions:
- Fixture and Jig Usage: Securing the workpiece with fixtures and jigs helps control movement during welding.
- Symmetrical Welding: Maintaining symmetry in the welding process reduces the likelihood of distortion.
- Cooling Control: Controlled cooling rates and post-weld heat treatments prevent rapid contraction and minimize distortion.
Cracking and Brittleness
- Challenge:
- High carbon content in certain iron types can lead to cracking during welding, and brittleness may affect the integrity of the weld.
- Precautions:
- Preheating: Elevating the temperature before welding reduces the risk of cracking, especially in high carbon steels.
- Proper Filler Material: Selecting filler materials compatible with the base metal reduces the risk of cracking.
- Post-Weld Heat Treatment: Annealing or stress-relief treatments can enhance ductility and reduce brittleness.
Pre-weld and Post-weld Treatments
- Challenge:
- Inadequate preparation and post-weld treatments can compromise the quality and durability of the weld.
- Precautions:
- Surface Preparation: Thorough cleaning of the material surface removes contaminants and ensures proper fusion.
- Preheating: Controlled preheating minimizes thermal stresses and improves the overall weld quality.
- Post-Weld Stress Relief: Annealing or stress-relief treatments after welding enhance material properties and reduce residual stresses.
- Tempering (for high carbon steels): Heat treatment processes like tempering can improve the toughness of the weld.
Case Studies
Welding experiences in real-world applications provide valuable insights into challenges encountered, innovative solutions developed, and lessons learned. Here, we delve into case studies that highlight both successful and unsuccessful welding scenarios across specific iron types.
Real-World Examples of Welding Challenges and Solutions for Specific Iron Types
Case Study: Welding Wrought Iron Gates
- Challenge: Welding wrought iron gates, known for their ornate designs, presented challenges due to the material’s fibrous structure.
- Solution: A careful selection of welding processes, such as shielded metal arc welding (SMAW), allowed for precise control over the weld pool. Preheating was employed for larger sections to prevent cracking. The use of specialized filler materials compatible with wrought iron contributed to successful welds.
Case Study: Repairing Cracked Cast Iron Engine Blocks
- Challenge: Repairing cracked cast iron engine blocks posed challenges due to the material’s high carbon content and susceptibility to cracking.
- Solution: Preheating the engine blocks before welding, along with controlled cooling rates, minimized thermal stresses and reduced the risk of cracking. Nickel-based welding electrodes were employed to match the material properties and prevent brittleness. Post-weld heat treatments were applied to enhance the overall integrity of the repair.
Lessons Learned from Successful and Unsuccessful Welding Experiences
Lesson Learned (Successful):
- Adaptive Welding Techniques: In the repair of a historic wrought iron structure, successful welding outcomes were achieved by adapting welding techniques to the material’s unique fibrous structure. This involved a combination of SMAW and careful heat control, showcasing the importance of tailoring methods to specific iron types.
Lesson Learned (Unsuccessful):
- Overlooking Material Composition: In an unsuccessful welding attempt on a high carbon steel component, the failure to account for the material’s carbon content resulted in cracking during welding. The lesson learned emphasized the critical need to thoroughly understand the composition of the material being welded and adjust welding parameters accordingly.
Lesson Learned (Successful):
- Post-Weld Heat Treatment Importance: In a case involving the fabrication of large cast iron components, the successful outcome was attributed to meticulous post-weld heat treatments. This highlighted the significance of post-weld treatments in relieving residual stresses, reducing brittleness, and enhancing the overall quality of the weld.
Lesson Learned (Unsuccessful):
- Ignoring Preheating Requirements: An unsuccessful welding experience with medium carbon steel components revealed the consequences of overlooking preheating requirements. The lack of preheating led to increased susceptibility to cracking, underlining the importance of adhering to pre-welding procedures for specific iron types.
Conclusion
In conclusion, welding different types of iron demands a comprehensive understanding of material characteristics, welding techniques, and associated challenges. The judicious selection of welding methods, coupled with ongoing advancements in technology, ensures that practitioners can navigate complexities and achieve high-quality welds. As industries evolve, the synergy between traditional knowledge and cutting-edge innovations will remain instrumental in advancing the field of iron welding.