Electron Beam Welding (EBW)
Introduction
Electron Beam Welding (EBW) is a high-tech welding process that utilizes a beam of electrons to generate heat and melt metal parts together. It is a highly precise and efficient process that produces high-quality welds with minimal distortion, making it a popular choice for a wide range of industrial applications.
The concept of using electrons for welding was first proposed in the early 1900s, but it wasn’t until the development of high-powered electron guns during the 1950s that the technology became practical. Today, EBW is widely used in industries such as aerospace, automotive, and medical, where the demand for high-quality, precise welds is critical.
In EBW, a beam of high-velocity electrons is generated and accelerated using an electron gun. The electrons are focused into a narrow beam using a series of magnetic lenses and then directed at the welding area. When the electron beam strikes the metal surface, it releases a large amount of energy, which causes the metal to melt and fuse together. The high energy density of the electron beam allows for deep penetration of the metal, producing strong and reliable welds.
One of the major advantages of EBW is its ability to produce high-quality welds with minimal distortion. This is because the process operates in a vacuum environment, which eliminates the risk of contamination and oxidation. Additionally, the high welding speed of EBW makes it a cost-effective choice for mass production applications.
Despite its many advantages, EBW also has some limitations. The process requires a vacuum environment, which can be expensive and time-consuming to maintain. The equipment used in EBW is also expensive and requires skilled operators to operate and maintain.
EBW is a highly advanced and efficient welding process that has revolutionized the manufacturing industry. Its ability to produce high-quality welds with minimal distortion has made it a popular choice for a wide range of applications, and its potential for further development makes it an exciting area of research for the future.
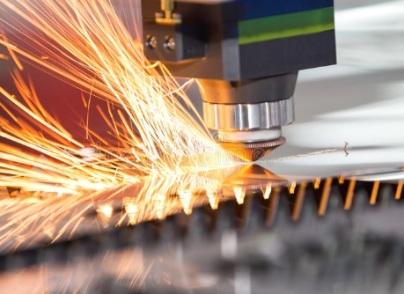
How Electron Beam Welding Works
Electron Beam Welding (EBW) is a welding process that utilizes a beam of high-velocity electrons to generate heat and melt metal parts together. In this section, we will discuss how EBW works, including the equipment used and the process of electron beam generation and acceleration.
Equipment Used in EBW
EBW requires specialized equipment to generate and accelerate the electron beam, as well as to maintain a vacuum environment. The key components of an EBW system include an electron gun, magnetic lenses, a beam deflection system, and a vacuum chamber.
- Electron Gun: The electron gun is the heart of the EBW system, responsible for generating and accelerating the electron beam. The gun typically consists of a cathode, which emits electrons when heated, and an anode, which accelerates the electrons using a high voltage potential.
- Magnetic Lenses: The magnetic lenses are used to focus the electron beam into a narrow, highly concentrated stream. These lenses are made up of a series of magnetic coils that produce a strong magnetic field, which deflects the path of the electrons.
- Beam Deflection System: The beam deflection system is used to direct the electron beam to the welding area. This is typically accomplished using an electromechanical scanning system, which uses a series of magnets and coils to deflect the electron beam in different directions.
- Vacuum Chamber: The vacuum chamber is an essential component of the EBW system, providing a clean and stable environment for the welding process. The chamber is typically made of stainless steel and is evacuated to a pressure of around 10^-5 torr to minimize the risk of contamination.
Process of Electron Beam Generation and Acceleration
The process of electron beam generation and acceleration involves several steps, including cathode heating, electron emission, and electron acceleration.
- Cathode Heating: The first step in generating an electron beam is to heat the cathode using an electric current. This causes the cathode to emit electrons through a process called thermionic emission.
- Electron Emission: Once the cathode is heated, it begins to emit electrons, which are attracted to the positively charged anode. As the electrons move towards the anode, they pass through a small aperture, which helps to focus the beam.
- Electron Acceleration: The electrons are accelerated by the high voltage potential between the cathode and anode, typically ranging from 50 to 150 kV. As the electrons travel towards the anode, they pass through a series of magnetic lenses, which focus and narrow the beam.
Characteristics of the Electron Beam
The electron beam used in EBW has several unique characteristics that make it an effective welding tool. These include:
- High Energy Density: The electron beam has a very high energy density, which allows it to rapidly heat and melt the metal being welded. This results in deep penetration and a strong, reliable weld.
- Low Heat Input: Because the electron beam is highly focused and concentrated, it delivers very little heat to the surrounding area, minimizing the risk of distortion and warping.
- Directional Control: The electron beam can be precisely directed and controlled using the magnetic lenses and beam deflection system, allowing for highly precise welds.
Advantages and Disadvantages of EBW
Electron Beam Welding (EBW) is a highly advanced welding process that offers a range of advantages and disadvantages. In this section, we will discuss the advantages and disadvantages of EBW in detail.
Advantages of EBW
- High Weld Quality: EBW offers high weld quality and reliability due to its high energy density and low heat input. The electron beam melts the metal parts together quickly and deeply, resulting in a strong, high-quality weld.
- Precise Welding: EBW provides highly precise welding capabilities due to the directional control of the electron beam. The magnetic lenses and beam deflection system allow for precise control of the electron beam, resulting in highly accurate welds.
- Minimal Distortion: EBW delivers very little heat to the surrounding area, minimizing the risk of distortion and warping. This makes it an ideal welding process for delicate or intricate parts that require minimal heat input.
- High Productivity: EBW is a highly efficient welding process that can be automated and integrated into manufacturing processes. This allows for high productivity and faster welding times compared to traditional welding processes.
- Wide Range of Materials: EBW can be used to weld a wide range of materials, including metals and alloys, and is particularly effective for high melting point materials such as titanium, nickel, and stainless steel.
Disadvantages of EBW
- High Cost: EBW is a highly advanced welding process that requires specialized equipment and a vacuum environment. As a result, it can be expensive to set up and maintain.
- Limited Thickness Range: EBW is most effective for welding thin to medium thickness materials, typically ranging from 0.1mm to 25mm. This makes it less suitable for welding thick materials or parts with complex geometries.
- Safety Concerns: The high voltage potential used to accelerate the electrons in EBW can pose safety concerns if not handled properly. This requires specialized training and safety measures to ensure that the equipment is used safely.
- Limited Access: The vacuum environment required for EBW makes it difficult to weld large or complex parts that cannot fit into the vacuum chamber. This can limit the range of parts that can be welded using this process.
Applications of Electron Beam Welding
Electron Beam Welding (EBW) is a highly advanced welding process that finds its application in a wide range of industries. In this section, we will discuss the various applications of EBW in detail.
- Aerospace Industry: EBW is widely used in the aerospace industry to weld high-performance metals such as titanium and nickel-based alloys. These materials are difficult to weld using traditional welding methods due to their high melting points and susceptibility to oxidation. EBW provides a precise and reliable welding solution for these materials, making it a popular choice in the aerospace industry.
- Automotive Industry: The automotive industry also relies on EBW for welding critical components such as engine parts and transmission components. The high-quality welds provided by EBW ensure that the parts have a long service life and can withstand the harsh operating conditions of automotive applications.
- Medical Industry: EBW is also used in the medical industry for welding surgical instruments, implants, and other medical devices. The high precision and accuracy of EBW ensure that the welded parts are safe and reliable for use in medical applications.
- Electronics Industry: The electronics industry also relies on EBW for welding delicate electronic components such as microchips, sensors, and other electronic devices. EBW provides a precise and reliable welding solution that ensures that the electronic components are not damaged during the welding process.
- Nuclear Industry: EBW is also used in the nuclear industry for welding critical components such as reactor vessels and fuel assemblies. The high precision and reliability of EBW ensure that the welded parts can withstand the harsh operating conditions of nuclear reactors.
- Research and Development: EBW is also used in research and development applications for welding experimental materials and prototypes. The high precision and accuracy of EBW allow researchers to create complex and intricate welds that are difficult to achieve using traditional welding methods.
In conclusion, EBW finds its application in a wide range of industries, including aerospace, automotive, medical, electronics, nuclear, and research and development. The high precision and accuracy of EBW make it an ideal welding process for welding critical components that require high-quality and reliable welds.
Comparison with Other Welding Processes
Electron Beam Welding (EBW) is a highly advanced welding process that offers several advantages over traditional welding processes. In this section, we will compare EBW with other welding processes in detail.
- Gas Tungsten Arc Welding (GTAW): Gas Tungsten Arc Welding, also known as TIG welding, uses a tungsten electrode to produce an electric arc that melts the metal parts together. Compared to EBW, GTAW has a lower energy density and requires a longer welding time, resulting in a slower welding process. However, GTAW is more versatile than EBW and can be used to weld a wider range of materials, including thicker materials.
- Gas Metal Arc Welding (GMAW): Gas Metal Arc Welding, also known as MIG welding, uses a consumable wire electrode and an inert gas to shield the welding area from atmospheric contamination. Compared to EBW, GMAW is faster and more productive, but it is also less precise and produces lower quality welds. GMAW is suitable for welding thicker materials and is commonly used in the automotive and construction industries.
- Laser Beam Welding (LBW): Laser Beam Welding uses a high-intensity laser beam to melt the metal parts together. Compared to EBW, LBW has a lower energy density and produces a wider heat-affected zone, resulting in more distortion and lower quality welds. However, LBW is more versatile than EBW and can be used to weld a wider range of materials, including thicker materials.
- Resistance Welding: Resistance Welding uses an electric current to generate heat and melt the metal parts together. Compared to EBW, Resistance Welding has a lower energy density and is less precise, resulting in lower quality welds. However, Resistance Welding is faster and more productive than EBW and is commonly used in the automotive and construction industries.
Future of Electron Beam Welding
Electron Beam Welding (EBW) has been a critical welding technology for several decades. As technology continues to evolve, the future of EBW looks promising. In this section, we will discuss some potential advancements in the future of EBW.
- Increased automation: EBW is already a highly automated process, but future advancements could further increase the automation and efficiency of the process. Robotics and artificial intelligence could be used to automate the entire welding process, including part positioning, beam alignment, and quality control.
- Integration with additive manufacturing: EBW is already used in conjunction with additive manufacturing technologies to produce complex parts with high accuracy and precision. In the future, EBW could be integrated with other additive manufacturing processes to produce parts with a combination of features such as strength, durability, and heat resistance.
- Improved precision: EBW already offers high precision and accuracy, but future advancements could further improve these capabilities. Advanced optics and beam control systems could be used to create even more precise and accurate welds, allowing for the creation of even more intricate and complex parts.
- Reduced costs: EBW is currently a relatively expensive welding process, and future advancements could help reduce its costs. Improved equipment designs and manufacturing processes could lead to more cost-effective systems. Additionally, advancements in electron beam sources could reduce the energy consumption required for the welding process.
- Increased use of EBW in emerging industries: EBW is already widely used in aerospace, automotive, and medical industries. Still, as new materials and industries emerge, the use of EBW could expand to a broader range of applications. For example, as the demand for sustainable energy sources increases, EBW could be used to weld components for wind turbines and other renewable energy technologies.
FAQs
What does EBW mean in welding?
EBW stands for Electron Beam Welding. It is a welding process that uses a high-velocity electron beam to join two materials together.
Why is most EBW electron beam welding done in a vacuum?
Electron beam welding is done in a vacuum to prevent the electrons in the beam from colliding with air molecules, which would cause scattering and reduce the effectiveness of the welding process.
What is electron beam welding used for?
Electron beam welding is commonly used for welding aerospace components, such as jet engine parts and rocket nozzles, as well as for welding components in the medical device and semiconductor industries.
What are the parameters of EBW welding?
The parameters of EBW welding include the beam current, beam voltage, beam focus, beam scanning speed, and workpiece speed.
What is ESW and EGW welding?
ESW stands for Electroslag Welding, which is a welding process that uses a consumable electrode and a conductive slag to create a molten pool and join two materials together. EGW stands for Electro Gas Welding, which is a welding process that uses a gas to create a plasma arc and join two materials together.
What is the principle of EBW?
The principle of EBW is that a high-velocity electron beam is focused onto the materials to be welded, creating a localized heat source that melts the materials and forms a weld joint.
What does EGW stand for in welding?
EGW stands for Electro Gas Welding, which is a welding process that uses a gas to create a plasma arc and join two materials together.
What is ESW welding?
ESW stands for Electroslag Welding, which is a welding process that uses a consumable electrode and a conductive slag to create a molten pool and join two materials together.
What is the difference between ERW and EFW in welding of pipes?
ERW stands for Electric Resistance Welding, which is a welding process that uses a high-frequency electrical current to heat the materials and join them together. EFW stands for Electric Fusion Welding, which is a welding process that uses heat generated by an electric arc to melt the materials and join them together. The main difference between the two is the heat source used to create the weld.
What is EAW welding?
I’m not aware of any welding process called EAW welding. It’s possible that this is a term used by a specific company or organization, but it’s not a commonly recognized welding process.
Conclusion
In conclusion, Electron Beam Welding (EBW) is a highly effective and precise welding process that has many advantages over other types of welding. One of the main advantages is its ability to produce high-quality welds with minimal distortion, which is particularly important in aerospace, automotive, and medical device industries where precision and accuracy are critical. Additionally, EBW is capable of welding a wide range of materials, including metals with high melting points, such as titanium and nickel alloys.
EBW also has some limitations, including its high cost and the requirement for a vacuum chamber, which can limit its use in certain applications. Moreover, the process requires specialized training and equipment, which can be a barrier to entry for some companies.
Despite its limitations, Electron Beam Welding (EBW) remains a valuable and widely used welding technique in various industries, particularly where precision and quality are paramount. With the growing demand for high-performance, lightweight, and complex components, EBW is likely to continue to play a vital role in the manufacturing of critical parts and components in the years to come.