Factors for Selecting Arc Welding Electrodes
Introduction
Arc welding is a critical process in the fabrication and manufacturing industries, essential for creating strong and durable joints in metals. Whether you’re welding a simple fence or constructing a complex machinery part, the quality of your weld is crucial. And a significant part of achieving high-quality welds lies in selecting the right welding electrode. But with so many options available, how do you choose the best one? Let’s dive into the factors that play a vital role in selecting arc welding electrodes.
Understanding Arc Welding Electrodes
Before we delve into the selection factors, it’s essential to understand what arc welding electrodes are. Electrodes are conductive rods used to create an electric arc between the welding machine and the materials being welded. This arc generates the heat necessary to melt the metal and form a strong joint.
There are two main types of electrodes:
- Consumable Electrodes: These electrodes melt and become part of the weld. Examples include stick electrodes (SMAW) and wire electrodes (GMAW).
- Non-Consumable Electrodes: These do not melt during the welding process. Tungsten electrodes used in TIG welding (GTAW) are a common example.
Each type has its specific applications and characteristics, making the selection process crucial to the success of your welding project.
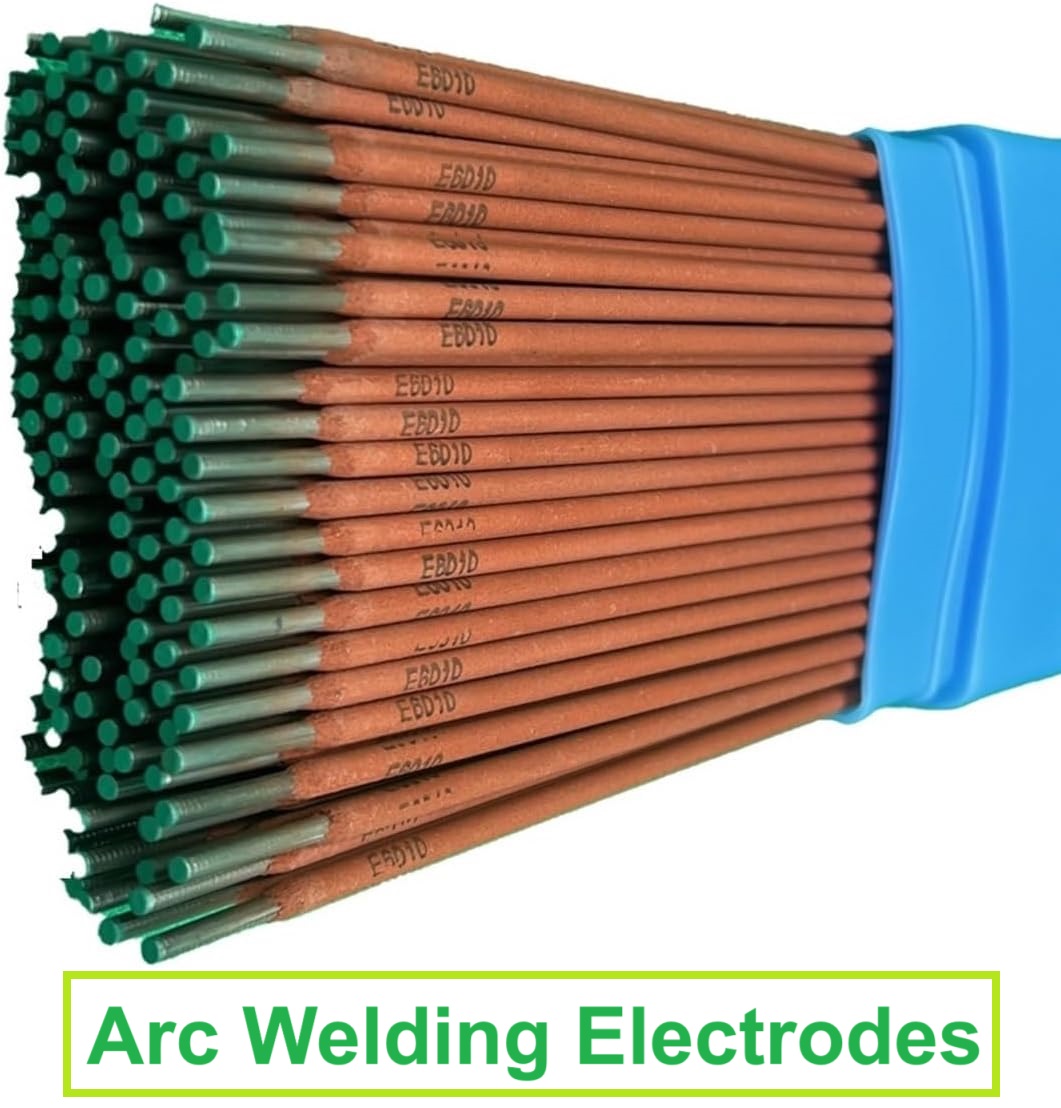
Factors for Selecting Arc Welding Electrodes
Material to be Welded
The first and foremost factor is the material you are welding. Matching the electrode material to the base metal is critical for achieving a strong and durable weld. For instance, if you’re welding mild steel, an E6010 or E7018 electrode might be appropriate. For stainless steel, an ER308L electrode would be a better choice.
Different metals require different electrodes due to their unique properties, such as melting points, thermal conductivity, and chemical composition. Using the wrong electrode can lead to weak welds, cracking, and other issues.
Welding Position
Welding position refers to the orientation of the weld joint relative to the welder and the ground. The common positions are flat, horizontal, vertical, and overhead. Some electrodes are versatile and can be used in multiple positions, while others are designed for specific positions.
For example:
- E6010: Excellent for vertical and overhead positions due to its fast-freezing slag.
- E7018: Suitable for flat and horizontal positions, providing smooth and strong welds.
Selecting the right electrode for your welding position ensures better control, less spatter, and higher-quality welds.
Thickness of Material
The thickness of the material you’re welding significantly affects your electrode choice. Thicker materials require electrodes that can penetrate deeply and provide enough heat. Conversely, thinner materials need electrodes that offer control to prevent burn-through.
For instance, thin sheet metal might require a smaller diameter electrode with low amperage, while thick structural steel would need a larger diameter electrode capable of higher currents.
Welding Current
The type of welding current (AC or DC) also influences electrode selection. Some electrodes are designed to work with AC (Alternating Current), while others are better suited for DC (Direct Current).
- AC Electrodes: Typically used in situations where stable arc performance is needed on materials like aluminum.
- DC Electrodes: Preferred for their consistent and steady arc, useful for a variety of metals including steel and stainless steel.
Matching the electrode to the appropriate current type is crucial for achieving the desired weld quality.
Joint Design and Fit-Up
The design of the joint and the fit-up quality are also vital factors. Different joints (butt, lap, corner, etc.) require different electrode characteristics. For example, a fillet weld in a lap joint might need an electrode with good penetration capabilities, such as an E6010.
Additionally, if the fit-up is not perfect, you might need an electrode that can bridge gaps effectively. Ensuring that your electrode choice aligns with your joint design will result in stronger and more reliable welds.
Welding Environment
Where you’re welding plays a significant role in electrode selection. Indoor welding offers controlled conditions, while outdoor welding can present challenges such as wind, moisture, and temperature variations.
- Indoor Welding: Allows for a broader range of electrodes since conditions are stable.
- Outdoor Welding: Often requires electrodes that can withstand environmental factors, like E6010 for its deep penetration and fast-freezing characteristics.
Choosing the right electrode for your environment ensures consistent weld quality regardless of external conditions.
Special Considerations
Code and Specification Requirements
Many industries have specific codes and standards that dictate the type of electrodes to be used. These codes ensure safety, quality, and performance. For example, the American Welding Society (AWS) provides classifications and specifications for different electrodes.
Understanding and complying with these requirements is crucial, especially in industries like construction, shipbuilding, and aerospace, where weld integrity is paramount.
Mechanical Properties
The desired mechanical properties of the finished weld, such as tensile strength, ductility, and impact resistance, should guide your electrode selection. For instance, if you need a weld with high tensile strength, an E7018 electrode would be appropriate.
These properties ensure that the weld will perform well under the expected loads and conditions.
Cost and Availability
Balancing cost with performance is a practical consideration. While some high-performance electrodes might offer excellent results, they can be expensive. Conversely, more affordable electrodes might not provide the desired quality.
It’s important to find a balance that meets your project requirements without exceeding your budget. Additionally, ensure that the electrodes you choose are readily available to avoid project delays.
Commonly Used Arc Welding Electrodes
Let’s look at some popular electrodes and their applications:
- E6010: Known for its deep penetration and ability to handle dirty or rusty surfaces. Ideal for pipeline welding and repair work.
- E7018: Offers smooth, strong welds with good mechanical properties. Commonly used in structural steel welding.
- ER308L: A stainless steel electrode perfect for welding similar alloys. It provides corrosion-resistant welds.
Each electrode has specific characteristics that make it suitable for particular applications, ensuring that you achieve the best results for your project.
Tips for Choosing the Right Electrode
Choosing the right electrode can be daunting, but these tips can help:
- Understand Your Project Requirements: Know the material, thickness, and joint type.
- Check Welding Position: Choose electrodes that match your welding position.
- Consider Environmental Conditions: Select electrodes suitable for indoor or outdoor use.
- Refer to Industry Standards: Ensure compliance with relevant codes and specifications.
- Balance Cost and Performance: Find an electrode that meets your needs within your budget.
Avoid common mistakes like using incompatible electrodes or neglecting environmental factors. Always read the manufacturer’s guidelines for the best results.
Maintaining Electrode Quality
Proper storage and handling of electrodes are essential to maintain their quality:
- Storage: Keep electrodes in a dry, cool place to prevent moisture absorption, which can lead to weld defects.
- Handling: Handle electrodes carefully to avoid damaging the flux coating.
Regularly inspect electrodes for any signs of damage or contamination and follow recommended storage practices to ensure their longevity.
FAQs
What is the best electrode for welding mild steel?
The E6010 and E7018 are commonly used electrodes for welding mild steel due to their versatility and strong weld properties.
Can the same electrode be used for different welding positions?
Yes, some electrodes like E6010 are versatile and can be used in multiple positions, but it’s essential to check the manufacturer’s specifications.
How does electrode diameter affect the welding process?
Electrode diameter influences the heat input and penetration. Thicker electrodes provide deeper penetration suitable for thicker materials, while thinner electrodes offer better control for thin materials.
What are the signs of using the wrong electrode?
Signs include poor weld appearance, excessive spatter, lack of penetration, and weld defects like cracking or porosity.
How do I store welding electrodes to ensure longevity?
Store electrodes in a dry, cool place, preferably in their original packaging or a sealed container, to prevent moisture absorption and contamination.
Conclusion
Selecting the right arc welding electrode is a multifaceted process that requires careful consideration of various factors such as the material, welding position, thickness, current, joint design, and environment. By understanding these factors and following best practices, you can achieve high-quality, durable welds that meet your project requirements.