How to Weld Titanium
Titanium is a metal known for its strength, lightweight, and corrosion resistance, making it highly valuable in various aerospace, medical, and automotive industries. Welding titanium, however, presents unique challenges due to its sensitivity to contamination and high reactivity at elevated temperatures. This article aims to guide you through the correct procedures and best practices to weld titanium, ensuring high-quality joints and structural integrity effectively.
Pre-Weld Preparation for Titanium
Cleaning and Surface Preparation
The success of a titanium weld significantly depends on the cleanliness of the surface. Titanium must be free from contaminants such as oils, greases, and oxides before welding. To prepare the surface, use a dedicated stainless steel wire brush and clean with solvents like acetone or alcohol. Ensure that the cleaning materials themselves are not contaminated.
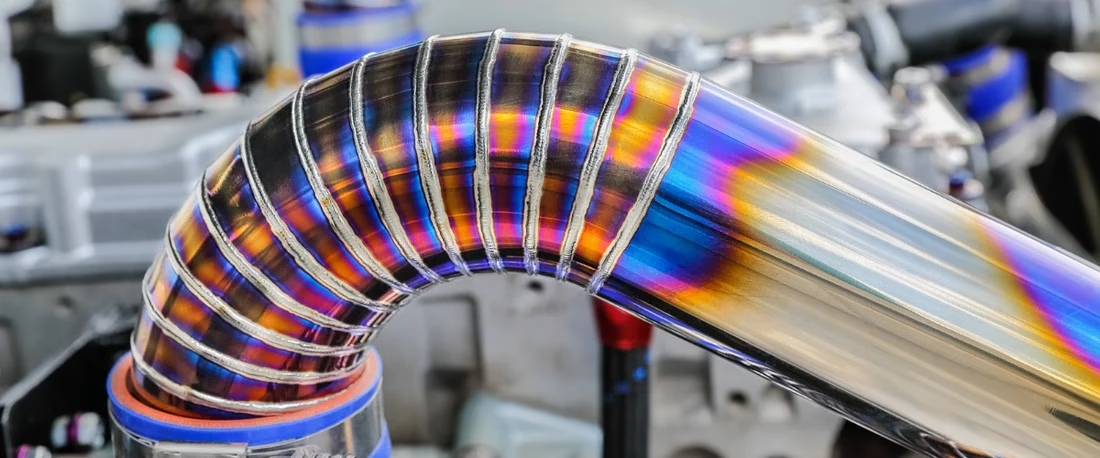
Assembly and Fixturing
Proper assembly and fixturing are crucial for maintaining alignment and preventing distortion during the welding process. Use fixtures made of materials that won’t react with titanium, such as stainless steel, and ensure they are also clean. Clamp the pieces securely and check alignment frequently as titanium can shift due to its low thermal conductivity.
Understanding Titanium Welding Techniques
TIG Welding of Titanium
TIG (Tungsten Inert Gas) welding is the most common method used for titanium due to its control over heat input and the quality of the weld it produces. Set up your TIG welder with a pure tungsten electrode and use argon as a shielding gas to protect both the weld pool and the heat-affected zones from atmospheric contamination. The welding process should be executed with precision, maintaining a short arc length and using a filler material compatible with titanium’s grade.
MIG Welding Techniques
MIG (Metal Inert Gas) welding can also be used for titanium, though it is less common due to its typically higher heat inputs. If using MIG, a similar setup to TIG can be employed but pay careful attention to the speed and power settings to avoid overheating the metal. Filler materials should again be matched to the specific titanium alloy being welded.
Best Practices for Welding Titanium
Controlling Heat Input
Managing heat input is critical when welding titanium to prevent warping and maintain mechanical properties. Use techniques such as pulse welding to minimize heat input while still ensuring good fusion. Pulse welding helps by intermittently applying heat, allowing the metal to cool slightly between pulses, reducing thermal stress.
Shielding Gas Selection
Argon is the preferred shielding gas for both TIG and MIG welding of titanium. Ensure a high flow rate and consider using trailing shields or additional side shields to protect the weld area from air contamination until it has cooled below 500 degrees Celsius, where titanium’s reactivity significantly decreases.
Common Challenges in Welding Titanium
Avoiding Contamination
Titanium is extremely prone to contamination from elements such as oxygen, nitrogen, and hydrogen at high temperatures. This sensitivity requires that the environment, tools, and handling equipment be meticulously clean. Store titanium in a clean, dry area and handle it with gloves to prevent oil transfer from the skin.
Dealing with Titanium’s Reactivity
Due to its reactivity, extra care must be taken when welding to ensure that the environment is controlled. Use back-purging techniques with argon to protect the backside of the weld, prevent oxidation, and maintain the integrity of the weld area.
Safety Measures for Welding Titanium
Personal Protective Equipment (PPE)
Welding titanium requires standard welding PPE such as a helmet with proper shade, fire-resistant clothing, gloves, and boots. Given titanium’s reactivity and the possibility of severe UV exposure, ensure that all skin is covered to prevent burns.
Ventilation and Fume Control
Proper ventilation is essential when welding titanium due to the possible release of titanium dioxide fumes, which can be harmful if inhaled. Set up adequate extraction systems or work in well-ventilated areas to ensure the safety of the welding environment.
Post-Welding Processes
Inspection and Testing of Titanium Welds
After welding, inspect the welds for any signs of contamination or defects using non-destructive testing methods such as X-ray or ultrasonic tests. This inspection helps ensure that the welds meet the required standards and maintain the structural integrity of the titanium.
Finishing and Cleaning
Once the weld is complete and has been inspected, perform any necessary finishing such as grinding or machining to achieve the desired surface finish. Finally, clean the welded area thoroughly to remove any marks or residues that could potentially lead to corrosion.
FAQs
What is the best type of titanium for welding?
Grade 2 titanium is commonly preferred for its balance of weldability, strength, and ductility.
How do you test titanium welds for integrity?
Titanium welds are typically tested using methods like X-ray inspection, ultrasonic testing, and visual examination.
Can titanium be welded without a shielding gas?
No, titanium must be welded with a shielding gas like argon to prevent contamination and ensure the integrity of the weld.
What are the signs of a poor titanium weld?
Signs include discoloration, cracks, porosity, and undercutting, which indicate compromised weld quality.
How can I improve my titanium welding skills?
Improve skills through formal training, consistent practice, and staying updated on welding techniques and titanium properties.
Conclusion
Welding titanium successfully requires understanding its unique properties, meticulous preparation, and precise execution. By following the guidelines and best practices outlined in this article, you can achieve strong, durable welds that meet the high standards required in critical applications.