Infrared Thermography Testing – NDT Inspection
Infrared Thermography Testing (IRT) is a powerful method in the realm of Non-Destructive Testing (NDT) used to evaluate materials, components, or systems without causing any damage. It’s like having X-ray vision for heat, enabling professionals to detect flaws, inconsistencies, or defects in welded joints with unmatched precision. But what makes IRT so special in the world of welding? Let’s dive in.
Introduction to NDT Methods
NDT encompasses various techniques that ensure the safety and quality of materials or structures without altering their usability. In industries like aerospace, construction, and manufacturing, NDT serves as the backbone of quality assurance.
Importance of Non-Destructive Testing (NDT)
Imagine constructing a building or designing an aircraft without knowing if the materials are defect-free. Sounds risky, right? NDT mitigates such risks by allowing for early detection of flaws, ensuring longevity and safety.
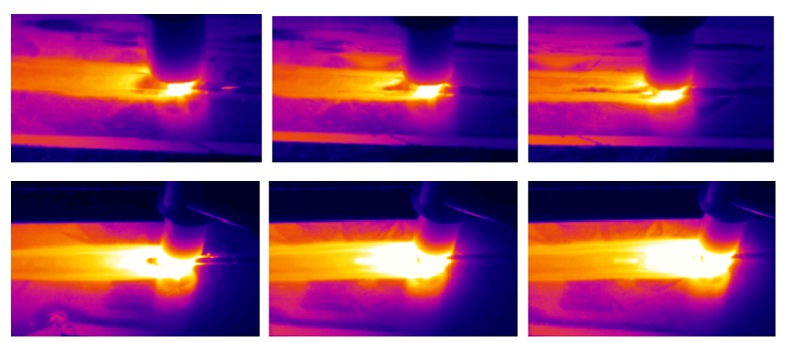
Role of Infrared Thermography in NDT
Infrared Thermography shines (pun intended) in NDT by providing a visual representation of heat distribution. Welded joints, critical in structural integrity, can be inspected for cracks, voids, and other defects through thermal patterns, making it a go-to tool for many industries.
How Infrared Thermography Works
IRT leverages the science of heat and infrared radiation to reveal surface and subsurface anomalies. Here’s how it all comes together.
Basics of Infrared Radiation
Infrared radiation is emitted by objects based on their temperature. This radiation, invisible to the naked eye, is captured by thermal cameras and converted into visible thermal images.
Heat Patterns and Thermal Imaging
Thermal imaging devices detect heat differences, creating a visual map that highlights anomalies like cracks or improper welds. Areas with irregular heat flow often indicate potential defects.
Equipment Used in Infrared Thermography
The primary tools include infrared cameras, thermal imaging software, and sometimes heat sources to stimulate thermal contrast. Advanced systems can even integrate with drones for large-scale inspections.
Understanding the Science Behind It
Detection of Temperature Anomalies
Defects in welds often cause uneven heat distribution. Infrared thermography pinpoints these irregularities, enabling inspectors to act swiftly.
Capturing Surface and Subsurface Defects
Not all defects are visible on the surface. IRT can uncover issues beneath the surface by detecting slight temperature variations caused by subsurface flaws.
Applications of Infrared Thermography in Welding
IRT is incredibly versatile when it comes to inspecting welded joints and monitoring welding processes.
Inspection of Welded Joints
Welded joints are critical in various structures, and even the tiniest flaw can lead to catastrophic failures.
Identifying Cracks and Flaws
Infrared thermography highlights discontinuities like cracks, porosity, or voids that compromise the integrity of welds.
Preventing Weld Failures
By detecting issues early, IRT ensures that corrective actions are taken before welds fail under stress.
Monitoring Welding Processes
IRT isn’t just for post-weld inspections—it’s also useful during the welding process itself.
Real-Time Thermal Monitoring
Thermal imaging can monitor temperature consistency in real-time, ensuring uniform weld quality and reducing the chances of defects.
Advantages of Infrared Thermography Testing
Why is IRT such a popular choice for NDT? The benefits speak for themselves.
Non-Intrusive Testing
IRT doesn’t require physical contact with the material, making it ideal for delicate or hard-to-reach components.
Rapid Data Acquisition
Thermal images are captured instantly, enabling quick analysis and decision-making.
Wide Range of Applications
From aerospace to automotive, IRT is a valuable tool across various industries.
Limitations of Infrared Thermography
Despite its many advantages, IRT isn’t perfect.
Dependence on Surface Accessibility
IRT works best when the surface is accessible and free from obstructions that could interfere with thermal readings.
Sensitivity to Environmental Conditions
External factors like wind, rain, or extreme temperatures can impact the accuracy of thermal imaging.
Cost and Training Requirements
High-quality thermal imaging equipment is expensive, and operators require specialized training to interpret data correctly.
Steps Involved in Infrared Thermography Testing
Executing IRT involves meticulous planning and execution to ensure accurate results.
Pre-Inspection Preparations
Before starting, the inspection area is cleaned, and the equipment is calibrated.
Thermal Imaging Setup
The infrared camera is positioned at the optimal distance and angle to capture accurate thermal data.
Post-Inspection Data Analysis
Thermal images are analyzed using specialized software to identify and evaluate defects.
FAQs
What are the primary benefits of infrared thermography for weld inspection?
It’s non-intrusive, quick, and capable of detecting both surface and subsurface defects with precision.
Can infrared thermography detect defects in inaccessible areas?
Yes, as long as the defects cause temperature anomalies that are detectable from the surface.
How does infrared thermography compare with other NDT methods?
While it’s faster and non-intrusive, it may not be as effective for certain deep internal defects compared to methods like ultrasonic testing.
What industries use infrared thermography for quality control?
Aerospace, automotive, construction, oil and gas, and energy sectors frequently use IRT.
Is infrared thermography testing suitable for all types of welding materials?
Most materials work well with IRT, but highly reflective surfaces may require special considerations.
Final Thoughts
Infrared Thermography Testing is a game-changer in the world of NDT. Its ability to detect surface and subsurface defects without causing damage makes it invaluable for inspecting welded joints. While it has its limitations, technological advancements are rapidly addressing these challenges. For industries reliant on flawless welds, IRT isn’t just an option—it’s a necessity.