Joining Dissimilar Materials: Methods and Techniques
Introduction
In the modern world, where innovation and functionality are key, the ability to join different materials is vital. By learning how to effectively join dissimilar materials, manufacturers can create products that are lighter, stronger, and more versatile than ever before.
What Does It Mean to Join Dissimilar Materials?
Joining dissimilar materials refers to the process of bonding two or more materials that differ in physical, chemical, or mechanical properties. These materials can range from metals and ceramics to polymers and composites, each bringing unique characteristics to the final product. Understanding the nature of these materials is the first step in choosing an appropriate joining method.
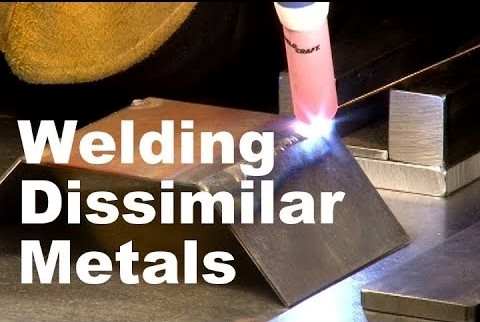
Importance and Applications of Joining Dissimilar Materials
Joining dissimilar materials is a crucial process in many industries. For instance:
- Aerospace: In aerospace, lightweight materials like aluminum and advanced composites are often joined to high-strength alloys, optimizing weight without compromising strength.
- Automotive: The automotive sector commonly joins metals and plastics to improve fuel efficiency by reducing vehicle weight.
- Electronics: Electronics manufacturing involves joining various metals, ceramics, and polymers to create reliable, compact, and efficient devices.
Challenges in Joining Dissimilar Materials
Joining different materials isn’t as simple as welding two pieces of the same metal together. Various challenges arise due to differences in properties, which must be addressed to achieve a reliable joint.
Physical and Chemical Differences
Dissimilar materials often have contrasting physical and chemical properties:
- Density and Hardness: Metals tend to be denser and harder than polymers, which may require adjustments in bonding techniques.
- Thermal and Electrical Conductivity: Metals generally conduct heat and electricity well, while polymers and ceramics may be insulators. These differences affect how materials respond to heat during the joining process.
- Chemical Reactivity: Some metals, when combined, can form brittle compounds or corrode over time. Incompatible polymers might not bond at all without a specialized adhesive or intermediary layer.
Thermal Expansion and Other Mechanical Challenges
When exposed to heat, materials expand and contract at different rates:
- Thermal Expansion: Metals like aluminum expand more than steel, which can cause warping or stress if bonded incorrectly. Mismatched expansion rates can lead to cracking, delamination, or joint failure under thermal cycling.
- Mechanical Properties: Differences in tensile strength, hardness, and elasticity can also impact joint stability. For example, a flexible polymer joined to a brittle ceramic may crack under load due to the unequal distribution of stress.
Common Methods for Joining Dissimilar Materials
A variety of methods are available, each suited to specific material combinations and applications. Let’s explore these common methods in more detail.
Welding Techniques for Dissimilar Materials
Welding is a versatile and widely used method, particularly with metals.
Fusion Welding
In fusion welding, materials are melted together to form a joint. However, fusion welding requires materials to have similar melting points to prevent one from vaporizing or degrading. With dissimilar materials, issues can arise, but techniques like the use of filler materials or intermediate layers can help bridge differences.
Friction Welding
Friction welding joins materials using heat generated by friction rather than melting. Two pieces are rubbed together under pressure, causing heat that bonds the materials when they cool. This method is suitable for metals with different melting points and even some metal-to-polymer joints, making it ideal for complex material combinations.
Brazing and Soldering Techniques
Brazing and soldering use a filler material that melts at a lower temperature than the base materials, bonding them without altering their properties significantly.
Advantages and Limitations of Brazing
Brazing involves using a filler metal like copper or silver alloy that melts and flows between the joint. It’s great for joining metals without significant thermal expansion issues but might not be as strong as a welded joint. Brazing is commonly used for components where high heat or stress is not a concern.
Soldering for Electronics and Other Applications
Soldering, which is similar to brazing but uses lower temperatures, is widely used in electronics. It creates connections between metals without the need for melting the base materials. Soldering provides sufficient strength for electrical contacts, though it is unsuitable for high-strength applications.
Adhesive Bonding
Adhesive bonding employs synthetic adhesives to bond diverse materials, including metals, plastics, and ceramics.
Types of Adhesives Used
Various adhesives are available, each with unique properties:
- Epoxies: Known for their strength and resistance to chemicals, epoxies are ideal for metal-to-metal or metal-to-ceramic bonds.
- Cyanoacrylates: Often called “super glue,” these provide quick bonds for small, light-duty applications.
- Urethanes: These offer flexibility and durability, making them suitable for applications where movement or vibration is a factor.
Preparing Surfaces for Adhesive Bonding
To ensure a strong adhesive bond, surface preparation is crucial. This may include cleaning to remove contaminants, sanding to increase surface area, or applying primers that improve adhesion. Proper preparation helps ensure the adhesive achieves maximum strength and longevity.
Advanced Methods for Joining Dissimilar Materials
Some applications demand advanced techniques to accommodate extreme conditions or specialized materials.
Diffusion Bonding
Diffusion bonding involves pressing materials together at high temperatures, allowing atoms to migrate across the bond line. This technique works well for metals and ceramics used in high-stress environments like aerospace components. Diffusion bonding creates joints that can withstand extreme temperatures and pressures.
Explosion Welding
This unique process uses controlled explosives to bond materials. The force of the explosion creates a high-energy bond without melting, making it possible to join metals with drastically different properties. Explosion welding is especially useful for creating corrosion-resistant cladding in marine applications.
Ultrasonic Welding
Ultrasonic welding employs high-frequency vibrations to generate heat and bond materials. Often used in electronics and medical device manufacturing, it’s particularly effective for joining plastics and metals. This process is rapid and doesn’t require additional adhesives or fillers, providing a clean and reliable bond.
Material Compatibility Considerations
Choosing compatible materials is crucial to prevent issues such as poor adhesion, corrosion, or joint failure over time.
Metallurgical Compatibility
Certain metals can form brittle compounds when bonded. For instance, aluminum and steel require a third material, like nickel, to form a stable bond. Incompatible metals may also corrode if exposed to certain environments, reducing joint strength over time.
Surface Treatments and Coatings
Surface treatments like anodizing, plating, or using primers can enhance compatibility. Coatings improve corrosion resistance, prevent oxidation, and promote adhesion. For instance, an oxide layer on aluminum can be removed or converted to a stable form to improve bonding with adhesives or other metals.
Selecting the Right Method for the Job
The ideal joining method depends on factors like the properties of the materials, environmental conditions, and the demands of the final product.
Factors to Consider in Method Selection
Key factors include:
- Strength Requirements: High-stress applications may require welding or advanced techniques like diffusion bonding.
- Environmental Exposure: Corrosive environments may need protective coatings or specific materials to prevent degradation.
- Cost and Complexity: Adhesive bonding may be simpler and more cost-effective for non-structural applications, while welding or explosion bonding could be justified for critical joints.
Case Studies and Examples
For example:
- Automotive Applications: Adhesive bonding is often used to join plastic to metal for lightweight parts. However, friction welding might be chosen for critical engine components requiring high strength.
- Electronics Manufacturing: Soldering is the go-to for electrical connections, but ultrasonic welding may be preferred for cases where adhesives or solder can’t be used.
Safety Considerations
Each technique involves specific safety measures, especially when high temperatures, chemicals, or explosive forces are involved.
Handling Hazardous Materials
Proper PPE, ventilation, and material handling protocols are essential to prevent exposure to harmful fumes, especially with adhesives and welding processes. Hazards include toxic fumes from adhesives, intense heat from welding, and handling flammable materials.
Precautions for Specific Techniques
For example:
- Explosion Welding: Requires stringent safety protocols due to the use of explosives. Professionals must handle explosive forces with extreme care, in controlled environments.
- Ultrasonic Welding: Generates high-frequency noise that can be harmful, necessitating ear protection for operators.
FAQs
What are some common examples of joining dissimilar materials?
Common examples include joining metals to plastics, metals to ceramics, and metals to composites.
How does thermal expansion affect the joining process?
Varying expansion rates can lead to joint stress and potential failure, requiring methods that accommodate these differences.
Is adhesive bonding as strong as welding?
While welding generally provides stronger bonds, adhesives can offer sufficient strength for many applications, particularly when flexibility is needed.
Can all metals be joined together?
Not all metals are easily joined; some may form brittle intermetallic compounds or corrode over time if improperly bonded.
What are the environmental considerations when joining materials?
Environmental factors include emissions, waste from adhesives, and the energy consumption required for high-temperature processes.
Conclusion
Joining dissimilar materials opens up a world of possibilities in modern manufacturing. By leveraging the strengths of various materials and using specialized joining techniques, manufacturers can create advanced, functional products. As technology progresses, methods for joining dissimilar materials will continue to evolve, allowing for even more groundbreaking innovations.