MIG Consumables
Introduction
MIG Welding, also known as Gas Metal Arc Welding (GMAW), is a widely used welding process that employs a continuous solid wire electrode heated and fed into the weld pool from a welding gun. The process relies heavily on various consumables, which are critical components that ensure the welding operation runs smoothly and efficiently. This article provides an overview of essential MIG consumables, their importance in the welding process, and best practices for maintaining and replacing them to ensure optimal welding performance. By understanding and properly managing these consumables, welders can achieve superior weld quality, enhance equipment longevity, and ensure safety in their welding operations.
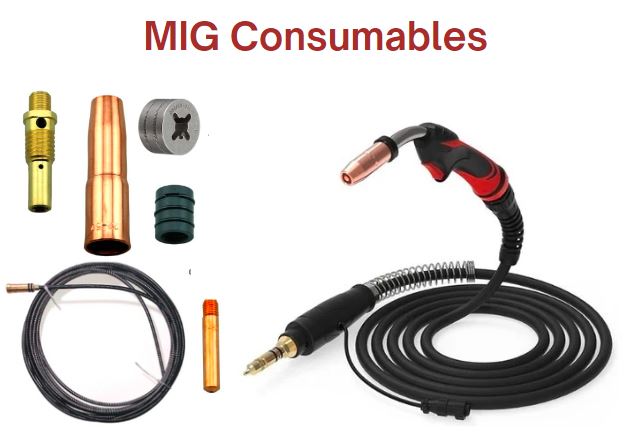
Types of MIG Consumables
1. Contact Tips
Contact tips are vital components in the MIG welding process as they are responsible for transferring electrical current to the welding wire, creating the arc necessary for welding. They are typically made from copper or copper alloys due to their excellent conductivity and durability under high-heat conditions.
Importance:
- Consistent Arc Formation: The contact tip’s primary function is to ensure a stable and consistent arc, which is crucial for producing high-quality welds.
- Electrical Conductivity: Copper and its alloys are chosen for their superior ability to conduct electricity, which is essential for maintaining a steady arc.
Maintenance and Replacement:
- Wear and Tear: Over time, contact tips wear out due to the intense heat and friction generated during welding. This can lead to erratic arcs and poor weld quality.
- Regular Replacement: It is important to inspect contact tips regularly and replace them when signs of wear, such as pitting or deformation, become evident. Regular replacement helps maintain consistent welding performance and prevents defects.
2. Nozzles
Nozzles play a crucial role in directing the shielding gas around the weld area, which protects the molten weld pool from atmospheric contamination. They are typically made from copper or brass and come in various shapes and sizes to suit different welding applications.
Importance:
- Shielding Gas Flow: Nozzles ensure that the shielding gas is properly directed to cover the weld area, which is essential for preventing oxidation and other forms of contamination.
- Material Choice: Copper and brass are used for their durability and ability to withstand high temperatures without deforming.
Maintenance and Replacement:
- Regular Inspection: Nozzles should be inspected regularly for blockages or spatter buildup. A blocked nozzle can disrupt gas flow, leading to contamination and poor weld quality.
- Cleaning: Regular cleaning of nozzles is necessary to remove spatter and debris. This ensures an unobstructed gas flow and consistent weld quality.
- Replacement: If a nozzle becomes significantly damaged or blocked and cannot be cleaned effectively, it should be replaced.
3. Diffusers
Diffusers are located inside the nozzle and are responsible for evenly distributing the shielding gas around the weld area. They are typically made from materials that can withstand high temperatures and harsh welding environments.
Importance:
- Even Gas Distribution: Diffusers ensure that the shielding gas is evenly dispersed, which is critical for protecting the weld pool from atmospheric contamination.
- High-Temperature Resistance: The materials used in diffusers are chosen for their ability to endure the intense heat generated during welding.
Maintenance and Replacement:
- Signs of Wear: Inconsistent gas flow or visible damage to the diffuser indicates it is time for replacement. Regular checks can help identify these issues early.
- Replacement Guidelines: Follow manufacturer guidelines for replacing diffusers to maintain optimal gas flow and weld quality.
4. Liners
Liners are essential for guiding the welding wire from the wire feeder through the welding gun to the weld pool. They are available in various materials, such as steel and nylon, depending on the type of welding wire being used.
Importance:
- Smooth Wire Feeding: Liners ensure the welding wire moves smoothly through the gun, which is crucial for consistent welding.
- Material Selection: The choice of liner material depends on the type of wire being used. For instance, steel liners are typically used for steel wires, while nylon liners might be used for softer wires like aluminum.
Maintenance and Replacement:
- Regular Replacement: Liners should be replaced periodically to prevent feeding issues. Signs that a liner needs replacement include erratic wire feeding and increased friction.
- Maintenance: Regular cleaning of liners can help extend their lifespan and ensure smooth wire feeding. Use compressed air to remove debris and ensure the liner is clear of obstructions.
5. Drive Rolls
Drive rolls are responsible for feeding the welding wire through the gun and into the weld pool. They come in various configurations, such as knurled, smooth, or V-groove, to accommodate different wire types and sizes.
Importance:
- Wire Feeding: Drive rolls ensure consistent and smooth feeding of the welding wire, which is essential for maintaining a stable arc and high-quality welds.
- Configurations: The choice of drive roll configuration depends on the type of wire being used. Knurled rolls are often used for flux-cored wires, while smooth rolls are suitable for solid wires.
Maintenance and Replacement:
- Regular Cleaning: Drive rolls should be cleaned regularly to remove any buildup of debris or spatter that can affect wire feeding. Use a brush or compressed air to clean the rolls.
- Tension Adjustment: Proper tension adjustment is crucial to avoid wire slippage or deformation. Check and adjust the tension according to the manufacturer’s specifications.
- Replacement: If the drive rolls show signs of significant wear, such as grooves or uneven surfaces, they should be replaced to ensure consistent wire feeding and prevent wire damage.
MIG consumable kits
MIG consumable kits are indeed available on Amazon, and they typically include various components that are essential for MIG welding. When looking for MIG consumable kits on Amazon, you can find a variety of options from different brands and for different MIG welding machine models. It’s important to check compatibility with your specific MIG welder and to consider the types of materials you typically work with to ensure you select the right kit.
Importance of MIG Consumables Maintenance
Impact on Weld Quality Maintaining consumables ensures consistent electrical contact and proper gas flow, both crucial for producing high-quality welds. Worn or damaged consumables can lead to defects and contamination, compromising the weld’s integrity.
Equipment Longevity Proper maintenance reduces wear and tear on the welding gun, extending its lifespan and preventing costly repairs. Regular inspection and timely replacement of consumables are key to avoiding unnecessary downtime.
Safety Considerations Using well-maintained consumables helps prevent contamination and defects that could lead to structural failures. Ensuring all components function correctly also protects the operator from potential hazards associated with malfunctioning equipment.
Best Practices for Managing MIG Consumables
Regular Inspection and Cleaning Regularly inspect consumables for signs of wear, such as pitting or deformation. Cleaning techniques vary: use wire brushes for nozzles, and compressed air for diffusers and liners. Replace consumables showing significant wear or damage.
Timely Replacement Establish a replacement schedule based on usage frequency and manufacturer recommendations. Replacing consumables before they fail helps maintain weld quality and prevents unexpected downtime.
Proper Storage Store consumables in a clean, dry environment to prevent contamination and damage. Organize them systematically for easy access, ensuring you can quickly replace worn components when needed.
Conclusion
In summary, essential MIG consumables such as contact tips, nozzles, diffusers, liners, and drive rolls play a pivotal role in the efficiency and quality of the welding process. Proper maintenance and timely replacement of these components are crucial for achieving consistent and high-quality welds. Implementing best practices, including regular inspection, cleaning, and proper storage, not only extends the life of the welding equipment but also ensures the safety of the operator. By prioritizing the upkeep of MIG consumables, welders can maintain optimal welding performance and avoid costly downtimes, ultimately leading to successful and efficient welding operations.