Plasma Arc Thermal Spraying
Introduction
Plasma arc spraying is a cutting-edge technology in the welding field, offering a robust solution for applying protective coatings to various materials. This process plays a critical role in enhancing the durability and performance of components in a wide range of industries. But what exactly is plasma arc spraying, and why is it so vital? Let’s dive into the details and explore this fascinating process.
How Plasma Arc Spraying Works
The science behind plasma arc spraying is both complex and fascinating. At its core, the process involves generating a high-temperature plasma jet that melts the coating material, which is then sprayed onto the surface of the workpiece. The key components of the plasma arc spraying setup include a plasma torch, gas supply, powder feeder, and control systems. The process begins with the ionization of gas in the plasma torch, creating a plasma jet that can reach temperatures exceeding 10,000°C. This intense heat melts the coating material, which is then propelled toward the substrate, forming a dense and uniform layer.
The steps involved in plasma arc spraying include surface preparation, plasma generation, coating application, and post-processing. Each step is crucial in ensuring the quality and effectiveness of the final coating.
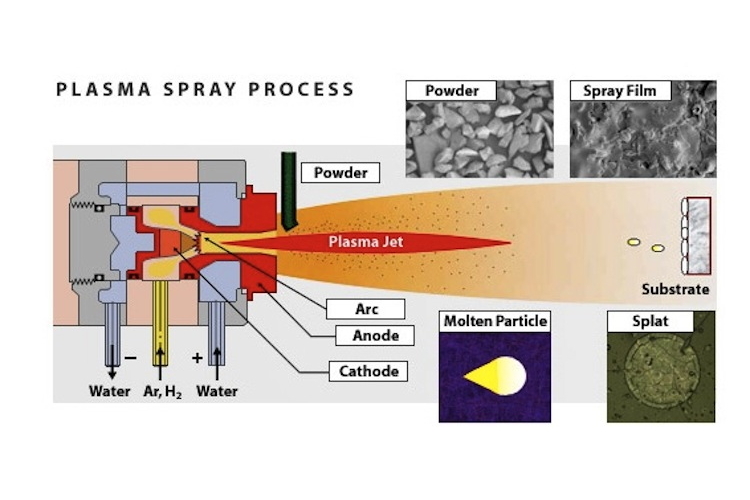
Types of Materials Used in Plasma Arc Spraying
One of the strengths of plasma arc spraying is its versatility in terms of the materials that can be used. Common materials include metals, ceramics, and composite powders. The choice of material depends on the specific application and desired properties of the coating. For example, ceramic coatings are often used for their excellent thermal and wear resistance, while metallic coatings provide corrosion protection.
Selecting the right material for plasma arc spraying involves considering factors such as the operating environment, mechanical stresses, and compatibility with the substrate. The wide range of materials available makes plasma arc spraying suitable for a variety of applications, from aerospace to automotive industries.
Advantages of Plasma Arc Spraying
Plasma arc spraying offers several advantages over other coating methods. One of the most significant benefits is the ability to apply coatings with high precision and control, resulting in superior quality and performance. The process allows for the deposition of coatings with excellent adhesion, density, and thickness control, which are essential for critical applications.
Another advantage is the versatility of plasma arc spraying, which can be used on a wide range of materials and substrates. This flexibility makes it a preferred choice for industries that require high-performance coatings, such as aerospace, automotive, and power generation.
The durability and performance improvements offered by plasma arc spraying are unmatched, making it a reliable solution for extending the lifespan of components and reducing maintenance costs.
Applications of Plasma Arc Spraying
Plasma arc spraying is widely used across various industrial sectors due to its ability to enhance the properties of components. In the aerospace industry, for example, it is used to apply thermal barrier coatings to turbine blades, protecting them from extreme temperatures and extending their service life. In the automotive industry, plasma arc spraying is employed to coat engine components, improving their wear resistance and performance.
Other applications include coating medical implants to enhance biocompatibility, applying wear-resistant coatings to industrial machinery, and providing corrosion protection for offshore structures. The versatility and effectiveness of plasma arc spraying make it an indispensable tool in modern manufacturing and engineering.
Challenges and Limitations
Despite its many advantages, plasma arc spraying also presents some challenges and limitations. One common issue is the need for precise control of process parameters, as variations can lead to defects such as porosity, cracking, or inadequate adhesion. Additionally, the high temperatures involved in the process can cause thermal stresses in the substrate, potentially leading to distortion or damage.
Another limitation is the cost of plasma arc spraying equipment, which can be a significant investment for small to medium-sized enterprises. However, the long-term benefits of improved component performance and reduced maintenance costs often outweigh the initial investment.
Addressing these challenges requires a deep understanding of the process and careful optimization of parameters to achieve the desired results. Advances in technology and process control are helping to mitigate these challenges, making plasma arc spraying more accessible and reliable.
Plasma Arc Spraying vs. Other Thermal Spraying Techniques
Plasma arc spraying is one of several thermal spraying techniques, each with its own set of advantages and limitations. Compared to flame spraying, for example, plasma arc spraying offers higher temperatures and better control over the coating process, resulting in coatings with superior properties. Similarly, compared to HVOF (High-Velocity Oxygen Fuel) spraying, plasma arc spraying allows for the application of a wider range of materials, including ceramics and composites.
However, each technique has its place, and the choice of method depends on the specific application requirements. Plasma arc spraying is often preferred for applications where high-performance coatings are required, and where the benefits of precision and material versatility outweigh the higher costs.
Safety Measures in Plasma Arc Spraying
Safety is a critical consideration in plasma arc spraying, given the high temperatures and potentially hazardous materials involved. Operators must follow strict safety protocols to protect themselves and ensure a safe working environment. This includes wearing appropriate personal protective equipment (PPE) such as heat-resistant gloves, face shields, and protective clothing.
In addition to PPE, proper training is essential for operators to understand the risks and how to mitigate them. Equipment must be regularly inspected and maintained to prevent malfunctions that could lead to accidents. Ventilation systems should be in place to remove any harmful fumes or particles generated during the process.
Following these safety measures not only protects the operators but also ensures the quality and consistency of the plasma arc spraying process.
Future Trends in Plasma Arc Spraying
The future of plasma arc spraying looks promising, with ongoing innovations and technological advancements driving the field forward. One exciting development is the integration of automation and robotics into plasma arc spraying systems, which can improve precision, repeatability, and efficiency. Additionally, advancements in materials science are leading to the development of new coating materials with enhanced properties, opening up new possibilities for applications.
Another trend is the growing focus on sustainability, with research being conducted into more environmentally friendly processes and materials. As industries continue to demand higher performance and longer-lasting coatings, plasma arc spraying will likely play an increasingly important role in meeting these needs.
FAQs
What is plasma arc spraying?
Plasma arc spraying is a thermal spraying process used to apply protective coatings to various materials by generating a high-temperature plasma jet that melts the coating material and sprays it onto the substrate.
What are the benefits of plasma arc spraying?
Plasma arc spraying offers precise control, superior coating quality, material versatility, and significant improvements in the durability and performance of components.
Which materials are commonly used in plasma arc spraying?
Common materials include metals, ceramics, and composite powders, selected based on the specific application and desired coating properties.
How does plasma arc spraying differ from other thermal spraying methods?
Plasma arc spraying allows for higher temperatures, better control, and the use of a wider range of materials compared to other thermal spraying techniques.
What safety precautions are necessary for plasma arc spraying?
Safety measures include wearing appropriate PPE, undergoing proper training, regular equipment maintenance, and ensuring proper ventilation to remove harmful fumes or particles.
Conclusion
Plasma arc spraying is a powerful and versatile tool in the welding field, offering numerous advantages for applying high-performance coatings. Despite its challenges, the process’s benefits in terms of durability, precision, and material versatility make it an indispensable technique in various industries. As technology continues to advance, plasma arc spraying is set to become even more efficient and widely used, cementing its place as a critical component of modern manufacturing and engineering.