Pressure Vessel Nozzle Welding
Pressure vessel nozzle welding plays a crucial role in industries ranging from oil and gas to chemical processing. These nozzles serve as essential components, allowing the safe passage of fluids, gases, or vapors in and out of the pressure vessel. Given the high-pressure environments they operate in, ensuring the integrity of these welds is paramount. Let’s dive deep into the fascinating world of pressure vessel nozzle welding and explore its nuances.
What Is Pressure Vessel Nozzle Welding?
Pressure vessel nozzle welding refers to the process of joining nozzles to the shell of a pressure vessel. Nozzles are openings or outlets that connect vessels to pipelines, instruments, or other equipment. They’re designed to withstand extreme pressure and temperature conditions while maintaining structural integrity.
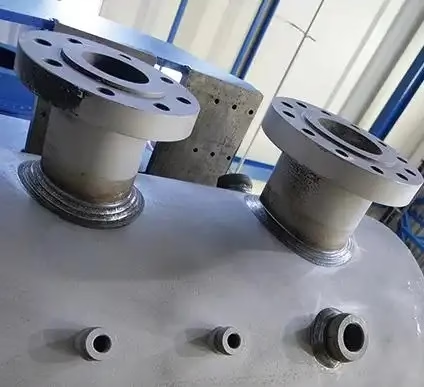
Types of Nozzles in Pressure Vessels:
- Inlet and Outlet Nozzles: For feeding materials into or out of the vessel.
- Inspection Nozzles: Allow access for internal inspection.
- Manway Nozzles: Provide entry for personnel during maintenance.
Materials Used in Pressure Vessel Nozzle Welding
Choosing the right materials is critical for the durability and functionality of pressure vessels.
Common Materials:
- Carbon Steel: Cost-effective and widely used for moderate pressure and temperature applications.
- Stainless Steel: Resistant to corrosion and suitable for harsh chemical environments.
- Alloy Steel: Ideal for high-pressure and high-temperature conditions.
Material Compatibility: Welders must ensure that the materials of the nozzle and the vessel are compatible to prevent issues like cracking or weakening under stress.
Welding Techniques for Pressure Vessel Nozzles
Several welding methods are used for nozzle welding, depending on the requirements of the vessel and the environment.
SMAW (Shielded Metal Arc Welding)
- Advantages: Easy to use, portable, and versatile.
- Limitations: Slower than other methods and may require more cleanup due to slag.
GTAW (Gas Tungsten Arc Welding)
- Benefits: Provides high precision and clean welds, ideal for critical applications.
- Applications: Commonly used for stainless steel and alloy steel nozzles.
GMAW (Gas Metal Arc Welding)
- Pros: Fast and efficient, suitable for large-scale industrial applications.
- Considerations: Requires a stable power source and shielding gas.
Challenges in Pressure Vessel Nozzle Welding
Nozzle welding comes with its own set of challenges, including:
- Defects: Issues like porosity, cracks, or undercut can compromise weld integrity.
- Stress Factors: High pressure and temperature can induce stress, leading to potential failures if not addressed properly.
Safety Measures in Nozzle Welding
Safety should always be a top priority during nozzle welding.
Key Practices:
- Use proper personal protective equipment (PPE), including helmets, gloves, and goggles.
- Ensure adequate ventilation to avoid inhaling harmful fumes.
- Follow industry standards and protocols strictly.
Inspection and Testing of Nozzle Welds
To ensure weld quality, thorough inspection and testing are essential.
Radiographic Testing (RT)
This method uses X-rays to detect internal flaws. It’s effective but requires careful handling to avoid radiation exposure.
Ultrasonic Testing (UT)
Ultrasound waves are used to detect subsurface defects. It’s non-invasive and provides accurate results.
Best Practices for High-Quality Nozzle Welding
Achieving high-quality nozzle welds involves meticulous preparation and follow-up.
Preparation Tips:
- Preheating: Helps minimize the risk of cracking by reducing temperature differences during welding.
- Joint Preparation: Clean and bevel edges for a better weld.
Post-Weld Heat Treatment (PWHT):
- Reduces residual stresses
- Improves the toughness of the welded joint
Applications of Pressure Vessel Nozzles
Pressure vessel nozzles are indispensable in various industries, including:
- Oil and Gas: For transporting and storing hydrocarbons.
- Chemical Processing: In reactors and distillation columns.
- Power Generation: Used in boilers and heat exchangers.
FAQs
What is the most commonly used welding technique for pressure vessel nozzles?
GTAW (Gas Tungsten Arc Welding) is often preferred for its precision and clean results, especially in critical applications.
Why is preheating important in nozzle welding?
Preheating reduces thermal stress and prevents cracking by ensuring even temperature distribution.
How are nozzle welds inspected for defects?
Methods like Radiographic Testing (RT) and Ultrasonic Testing (UT) are commonly used to detect flaws without damaging the weld.
What materials are suitable for pressure vessel nozzles?
Common materials include carbon steel, stainless steel, and alloy steel, chosen based on the vessel’s operating conditions.
What are the key challenges in welding nozzles for pressure vessels?
Challenges include addressing stress factors, avoiding defects, and maintaining material compatibility.
Conclusion
Pressure vessel nozzle welding is a specialized skill that demands precision, expertise, and adherence to safety standards. From choosing the right materials to employing the most suitable welding techniques, every step is critical to ensuring the safety and efficiency of pressure vessels. Mastering these practices not only prevents failures but also boosts operational reliability.