Pros and Cons of Friction Stir Welding
Introduction
Friction Stir Welding (FSW) is a revolutionary solid-state welding process that has changed the way industries join materials, especially metals. Unlike traditional welding techniques, FSW does not involve melting the workpieces but instead relies on friction to generate heat. This process has both benefits and limitations, making it essential to weigh the pros and cons before deciding if it’s the right method for a specific application.
What is Friction Stir Welding?
Friction Stir Welding is a welding process that involves joining two metals by heating them with friction generated by a rotating tool. The tool moves along the joint between the workpieces, softening the material through heat without melting it, and stirs the material together. The process results in a solid, high-quality joint without the use of filler materials or shielding gas.
The key components of the FSW setup include:
- A non-consumable rotating tool
- A clamping system to hold the workpieces in place
- A base on which the workpieces are positioned
FSW is particularly popular in industries where lightweight, high-strength joints are required, such as aerospace and automotive manufacturing.
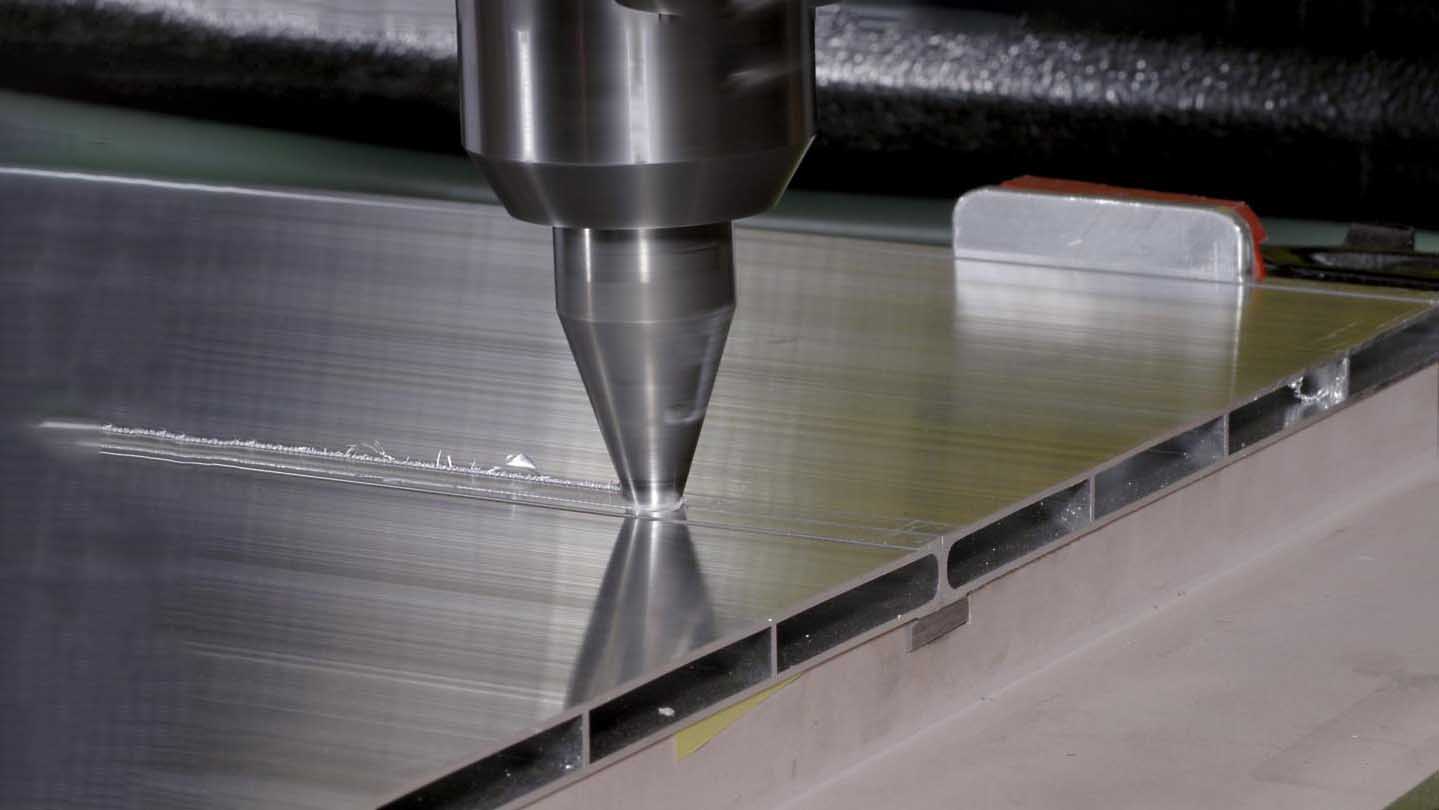
How Friction Stir Welding Works
The FSW process is fairly straightforward but involves several crucial steps. First, the materials to be welded are securely clamped together. Then, a rotating tool with a specially designed pin and shoulder is driven into the joint area between the materials. As the tool moves along the joint, friction generates heat, softening the materials. The softened material is stirred and mixed, resulting in a solid-phase bond.
This method utilizes heat from friction and plastic deformation, meaning the metals are softened but not melted, creating a strong weld. The result is a clean, seamless joint with fewer defects than traditional welding methods, which often involve melting and solidification.
Applications of Friction Stir Welding
FSW is used in a variety of industries, each benefiting from its ability to produce strong, defect-free welds. Here are some key applications:
- Aerospace Industry: Aircraft components require lightweight and high-strength materials, making FSW an ideal process for joining aluminum and other materials used in the industry.
- Automotive Sector: FSW is used in car manufacturing, particularly for aluminum body panels, helping to reduce weight and improve fuel efficiency.
- Marine and Railway Applications: The process is widely used for building ships and rail cars due to its ability to join long sections of material with minimal distortion.
- Emerging Industries: As FSW continues to evolve, it is finding applications in the electronics, energy, and military sectors, especially in battery enclosures and high-performance structures.
Pros of Friction Stir Welding
Friction Stir Welding comes with several advantages, making it a preferred choice in many sectors.
- High-quality welds with no filler materials: Since FSW is a solid-state process, it produces strong, defect-free joints without the need for filler materials or shielding gases. The result is a cleaner, more efficient weld.
- Energy-efficient process: FSW consumes less energy compared to traditional welding methods, as it doesn’t require high temperatures to melt the base materials.
- Minimal distortion and deformation: Because the materials aren’t melted, FSW minimizes distortion, shrinkage, and residual stresses. This is particularly beneficial for precision industries like aerospace.
- Environmentally friendly: The process does not produce harmful emissions or spatter, making it environmentally friendly. Additionally, the lack of consumable materials reduces waste.
- Superior mechanical properties in the weld zone: The welds created by FSW often have better mechanical properties than those made by conventional welding methods, thanks to the refined grain structure in the stir zone.
Cons of Friction Stir Welding
Despite its many benefits, FSW also has some limitations that must be considered.
- Limited to specific materials: FSW is most commonly used for materials like aluminum, copper, and their alloys. While research is being done to extend its application to other materials, it’s still not widely used for harder metals like steel.
- High initial equipment cost: FSW machines can be expensive, especially for small manufacturers. The initial investment may be a barrier for companies looking to adopt this technology.
- Tool wear and replacement: The rotating tool used in FSW is subject to wear, especially when welding harder materials. Regular replacement of the tool adds to maintenance costs.
- Not suitable for all thicknesses: While FSW works well for medium-thickness materials, it struggles with very thin or very thick sections. This limits its versatility for certain applications.
- Complex joint configurations can be challenging: The process works best with simple, linear joints. More complex joint configurations may require adjustments or alternative welding techniques.
Comparing FSW with Other Welding Techniques
When comparing FSW to other welding methods, its advantages become clearer, but so do its limitations.
- FSW vs. Traditional Welding Methods: Traditional methods like MIG and TIG welding involve melting the base materials, which can introduce defects like porosity and cracking. FSW, on the other hand, eliminates these issues but is limited to certain materials.
- FSW vs. Laser Welding: Laser welding is highly precise and can be automated for complex joint configurations. However, it is more expensive than FSW and may not produce as strong a weld in certain materials.
Is Friction Stir Welding the Future?
FSW is undoubtedly a forward-looking technology, with continuous advancements being made to expand its applications. Researchers are exploring ways to make FSW more versatile by extending its use to a broader range of materials, including harder metals like steel and titanium.
One of the key challenges that FSW faces is the development of tools that can withstand the demands of welding harder materials without excessive wear. As these technological hurdles are overcome, FSW could become a more widely adopted process across multiple industries.
FAQs
What materials can be welded using Friction Stir Welding?
FSW is typically used for materials like aluminum, copper, and their alloys. Research is ongoing to expand its use to harder materials like steel.
Is Friction Stir Welding suitable for high-volume production?
Yes, FSW is efficient and can be used for high-volume production, particularly in industries like automotive and aerospace.
How does FSW affect the mechanical properties of materials?
FSW often improves the mechanical properties in the weld zone due to the refined grain structure created by the stirring process.
What industries benefit most from Friction Stir Welding?
Industries like aerospace, automotive, and shipbuilding benefit the most from FSW, thanks to its ability to produce strong, lightweight joints.
Can FSW be automated for industrial use?
Yes, FSW can be fully automated, making it a highly efficient process for large-scale manufacturing operations.
Conclusion
Friction Stir Welding offers a blend of unique advantages and challenges. It excels in producing strong, defect-free joints without the need for filler materials or harmful emissions, making it a popular choice for industries like aerospace and automotive. However, its limitations, such as high equipment costs and material restrictions, cannot be ignored. As technology advances, FSW has the potential to revolutionize even more industries, but it will require overcoming significant challenges for broader adoption.