Radiographic Testing – NDT Inspection
Introduction
Radiographic testing (RT) is a non-destructive testing (NDT) technique that uses electromagnetic radiation, typically X-rays or gamma rays, to produce an image of the internal structure of an object. Radiographic testing is commonly used in a variety of industries, including welding technology, to ensure the quality and integrity of materials and components. Radiographic testing is a non-destructive testing technique used to examine the internal structure of an object using X-rays or gamma rays. It is used to detect internal defects or anomalies in materials or weldments, such as porosity, cracks, inclusions, or other forms of discontinuities. During radiographic testing, an X-ray or gamma-ray source is positioned on one side of the object, and a detector or film is positioned on the opposite side. The radiation passes through the object and is absorbed differently by different materials, resulting in an image that reveals the internal structure and any defects or discontinuities.
Welding is a critical process in many industries, including construction, aerospace, and manufacturing. It involves joining two or more pieces of material together by melting them at high temperatures and allowing them to solidify. The quality and integrity of welded joints are essential for ensuring the safety and reliability of the finished product. Welding defects or discontinuities, such as cracks, porosity, or incomplete fusion, can compromise the strength and durability of the weld, leading to catastrophic failures. Radiographic testing is a valuable tool for detecting and assessing these defects and ensuring the quality of the weld. It allows welders and inspectors to see inside the weld and identify any potential flaws that could compromise its integrity.
The primary purpose of radiographic testing is to ensure the quality and integrity of materials and weldments. It is used to detect internal defects or anomalies that could compromise the strength and durability of the finished product. Radiographic testing is typically used during the manufacturing or fabrication process to identify and correct defects before the finished product is put into service. It can also be used for in-service inspections of critical components to ensure their continued safety and reliability.
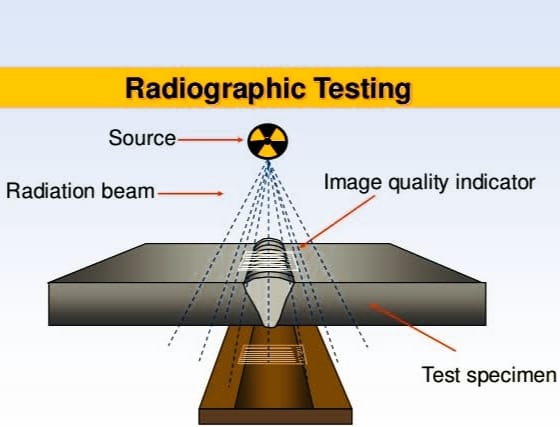
Types of Radiographic Testing
Radiographic testing is a non-destructive testing technique used to examine the internal structure of an object using electromagnetic radiation, typically X-rays or gamma rays. There are several types of radiographic testing methods, including X-ray radiography, gamma radiography, and digital radiography. Each method has its advantages and disadvantages, and the choice of method depends on several factors, such as the type of material being tested, the size of the object, and the sensitivity required.
X-ray Radiography
X-ray radiography is one of the most commonly used methods of radiographic testing. It involves using an X-ray machine to produce high-energy electromagnetic radiation, which is then directed towards the object being tested. The radiation passes through the object and is detected on the opposite side, where it creates an image of the object’s internal structure.
X-ray radiography is particularly useful for detecting defects in materials such as metals, plastics, and composites. It is also commonly used in medical imaging. One of the main advantages of X-ray radiography is that it is relatively fast and can provide detailed images of internal structures.
Gamma Radiography
Gamma radiography involves using gamma rays, which are produced by the decay of radioactive isotopes, to produce an image of the object’s internal structure. The gamma rays are directed towards the object being tested, and the radiation that passes through the object is detected on the opposite side.
Gamma radiography is particularly useful for testing objects with thick walls or complex geometries, such as pipelines, pressure vessels, or welds. One advantage of gamma radiography is that it can penetrate thicker materials than X-rays, making it useful for testing thicker components.
Digital Radiography
Digital radiography, also known as computed radiography, is a newer method of radiographic testing that uses digital sensors to produce images of the object’s internal structure. It involves directing X-rays or gamma rays towards the object being tested, and the radiation that passes through the object is detected by a digital sensor.
Digital radiography offers several advantages over traditional film-based radiography, such as faster image processing, greater sensitivity, and the ability to enhance and manipulate images. It is also more environmentally friendly since it does not require the use of chemicals to develop the images.
Radiographic Equipment
- X-ray Machine An X-ray machine is a medical device that produces X-rays, which are used for diagnostic and therapeutic purposes. It consists of an X-ray tube that generates the radiation, a control panel that regulates the X-ray exposure, and a table or stand where the patient lies or sits. The X-ray machine is commonly used for imaging the bones and organs in the body to detect injuries, abnormalities, or diseases.
- Gamma Ray Source A gamma ray source is a device that emits gamma radiation, which is a highly energetic form of electromagnetic radiation. Gamma rays are used for a variety of applications, including medical imaging, cancer treatment, and industrial processes. Gamma ray sources can be made from radioactive isotopes or through the use of specialized equipment such as linear accelerators.
- Digital Radiography Scanner A digital radiography scanner is a medical imaging device that captures X-ray images digitally. It replaces traditional film-based radiography, and it is more efficient and environmentally friendly. The scanner consists of a flat panel detector that converts X-rays into digital signals and a computer that processes and displays the images. Digital radiography is widely used in hospitals, clinics, and dental offices.
- Film Radiography Film radiography is a traditional method of capturing X-ray images on photographic film. The X-ray machine sends radiation through the body, and the film captures the image. The film is then developed using chemicals to produce a visible image. While film radiography is still used in some medical facilities, it has largely been replaced by digital radiography due to the convenience, efficiency, and cost-effectiveness of digital imaging.
Radiographic Image Interpretation
Evaluation of the radiographic image is a crucial step in determining the quality of welded materials. The radiographic image provides a visual representation of the internal structure of the weld, and defects can be identified based on their size, shape, location, and density. Defects that can be identified in radiographic images include cracks, porosity, incomplete fusion, lack of penetration, and undercutting. Each defect has its own unique characteristics, and identifying them requires experience and expertise. Once defects have been identified, the next step is to determine whether the welded materials should be accepted or rejected. The acceptance or rejection criteria are typically determined by industry standards and codes, and they vary depending on the type of weld and the application.
In general, if the defects are minor and do not affect the structural integrity or function of the weld, the welded materials may be accepted. However, if the defects are significant and could compromise the safety or performance of the welded materials, they may need to be rejected. Ultimately, the evaluation of radiographic images and the acceptance or rejection of welded materials require a combination of technical knowledge, experience, and judgment. It is important to work with qualified professionals who have the expertise to make accurate assessments and ensure the quality and safety of welded materials.
Advantages and Disadvantages of Radiographic Testing
Advantages of Radiographic Testing:
- Radiographic testing is a non-destructive testing method, meaning that it does not damage the material being tested. This allows for inspection of critical components without causing any harm to them.
- Radiographic testing can provide a highly accurate and detailed image of the internal structure of the material being inspected, allowing for the detection of even small defects.
- Radiographic testing can cover a large area of a material in a single image, making it an efficient and effective method for inspecting large components.
- Portable radiographic testing equipment is available, making it possible to perform inspections in remote or hard-to-reach locations.
- Radiographic testing can be used to inspect a wide range of materials, including metals, plastics, and composites.
Disadvantages of Radiographic Testing:
- Radiographic testing involves the use of ionizing radiation, which can be hazardous to human health. Proper safety precautions must be taken to protect workers and the public from radiation exposure.
- Radiographic testing equipment can be expensive, and the cost of operation and maintenance can be high.
- Radiographic testing requires access to both sides of the material being inspected, which may not always be possible or practical.
- Interpreting radiographic images requires specialized training and expertise, which may not be readily available in all locations.
- The disposal of radioactive materials used in radiographic testing can be an environmental concern, and strict regulations must be followed to ensure proper disposal.
Radiographic Testing Standards
Radiographic testing is a non-destructive testing (NDT) method used to detect internal flaws and defects in materials using X-rays or gamma rays. There are several codes and standards that specify the requirements and procedures for radiographic testing.
ASME Codes and Standards: The American Society of Mechanical Engineers (ASME) has several codes and standards related to radiographic testing, including the Boiler and Pressure Vessel Code (BPVC) Section V, which covers non-destructive examination techniques, including radiography, for pressure vessels, piping, and other components.
API Codes and Standards: The American Petroleum Institute (API) has several standards related to radiographic testing, including API RP 2X, which covers the inspection and testing of offshore structures, and API 1104, which covers welding of pipelines and related facilities.
ASTM Codes and Standards: The American Society for Testing and Materials (ASTM) has several standards related to radiographic testing, including ASTM E94, which covers the standard guide for radiographic examination, and ASTM E142, which covers the standard method for determining the grain size of metals by the comparison method.
Radiographic Testing Procedure
Radiographic testing is a non-destructive testing method that uses X-rays or gamma rays to detect internal flaws and defects in materials. The following are the general steps involved in radiographic testing procedure:
Preparation for radiographic testing:
Before radiographic testing, it is essential to prepare the equipment, personnel, and the work area. The following are some of the important steps that need to be taken:
- Ensure that the radiographic equipment is functioning properly and calibrated to the correct settings.
- Select the appropriate radiation source and film for the test, based on the material being tested and the required sensitivity.
- Establish safety procedures to protect personnel and the public from radiation exposure.
- Identify the test object and mark it appropriately.
- Set up the work area to ensure proper positioning of the test object and the radiographic equipment.
Performing radiographic testing:
The following are the general steps involved in performing radiographic testing:
- Position the test object and the radiation source according to the established procedures and safety guidelines.
- Expose the film to radiation by activating the radiation source.
- Develop the exposed film using appropriate techniques and equipment.
- Interpret the developed film to identify any defects or flaws in the material.
Post-radiographic testing procedures:
After the radiographic testing is completed, it is essential to perform the following steps:
- Evaluate the results of the test and determine if any further testing is necessary.
- Record the results of the test and maintain accurate records of the test procedure, equipment used, and the results obtained.
- Properly dispose of any contaminated materials or equipment to ensure public safety and environmental protection.
- Ensure that all personnel involved in the test are properly debriefed and informed of the results.
Safety Measures for Radiographic Testing
Radiographic testing involves the use of X-rays or gamma rays to detect internal flaws and defects in materials. As such, it is important to take necessary safety measures to protect personnel and equipment from radiation exposure. The following are some of the safety measures that should be taken during radiographic testing:
- Radiation safety
- Ensure that the radiographic equipment is in good working condition and properly calibrated to minimize radiation exposure.
- Use appropriate shielding to protect personnel and the public from radiation exposure.
- Restrict access to the work area during radiographic testing.
- Monitor radiation levels during the testing process using appropriate equipment.
- Follow established radiation safety guidelines and regulations, such as those set forth by the International Atomic Energy Agency (IAEA) or the Nuclear Regulatory Commission (NRC).
- Provide appropriate training for personnel involved in the testing process.
- Protection of personnel and equipment
- Use appropriate personal protective equipment (PPE), such as gloves, aprons, and eye protection, to minimize radiation exposure.
- Use appropriate equipment, such as radiation detectors and dosimeters, to monitor radiation levels and ensure that personnel are not exposed to excessive radiation.
- Properly label and store radiation sources when not in use.
- Perform regular maintenance and inspection of the radiographic equipment to ensure that it is functioning properly.
- Properly dispose of contaminated materials and equipment to minimize the risk of radiation exposure.
FAQs
What is NDT in radiography?
NDT stands for non-destructive testing, and in radiography, it refers to a method of testing materials for flaws or defects using X-rays or gamma rays without damaging the material being tested.
What is radiography material testing?
Radiography material testing is a non-destructive testing method that uses X-rays or gamma rays to detect internal flaws or defects in materials, such as welds or structural components.
What is radiographic testing in welding?
Radiographic testing in welding is a non-destructive testing method that uses X-rays or gamma rays to detect internal flaws or defects in welds.
Where is radiographic testing used?
Radiographic testing is used in a variety of industries, such as aerospace, automotive, construction, manufacturing, and oil and gas, to detect internal flaws or defects in materials, such as welds or structural components.
What is the process of radiography testing?
The process of radiography testing involves preparing the equipment and materials, positioning the test object, exposing the object to X-rays or gamma rays, developing the film or digital image, and analyzing the results for any flaws or defects.
What is difference between RT and UT?
RT (radiographic testing) and UT (ultrasonic testing) are both non-destructive testing methods used to detect internal flaws or defects in materials. The main difference is that RT uses X-rays or gamma rays to create an image of the internal structure, while UT uses high-frequency sound waves to detect flaws or defects.
What are the types of radiological tests?
There are several types of radiological tests, including radiography, computed tomography (CT), magnetic resonance imaging (MRI), ultrasound, and nuclear medicine imaging.
Why is radiographic testing important?
Radiographic testing is important because it can detect internal flaws or defects in materials that may not be visible to the naked eye, allowing for early detection and repair before they cause larger issues or failures.
What is the thickness limit for RT?
The thickness limit for RT (radiographic testing) can vary depending on the type of material being tested and the equipment being used. Generally, RT is most effective for materials with thicknesses ranging from 2mm to 300mm.
How many types of radiography are there?
There are several types of radiography, including conventional radiography, computed radiography, digital radiography, and film radiography.
What is the minimum thickness for radiography test?
The minimum thickness for radiography testing can vary depending on the type of material being tested and the equipment being used. Generally, radiography testing is most effective for materials with a minimum thickness of 2mm.
What is the purpose of radiography?
The purpose of radiography is to detect internal flaws or defects in materials, such as welds or structural components, that may not be visible to the naked eye, allowing for early detection and repair before they cause larger issues or failures.
Conclusion
In welding technology, radiographic testing is a widely used non-destructive testing method to detect internal flaws and defects in welds. Radiographic testing involves the use of X-rays or gamma rays to create an image of the internal structure of the weld, which is then analyzed for defects and discontinuities.
The radiographic testing procedure involves preparing the equipment, personnel, and work area, performing the test, and evaluating the results. Safety measures, such as radiation safety and protection of personnel and equipment, are essential to ensure safe and reliable testing.
Future trends and developments in radiographic testing technology are focused on improving the accuracy and efficiency of the testing process. These developments include the use of digital radiography, which provides faster results and eliminates the need for film development, and the use of automated radiographic testing, which reduces the risk of human error and increases the consistency of results.