Steel Welding Rod ER309: Uses, Benefits, and Best Practices
Welding different metals together requires specialized filler materials to ensure strong, corrosion-resistant, and durable welds. One of the most commonly used welding rods for joining stainless steel to mild steel or other dissimilar metals is the ER309 welding rod. This comprehensive guide will explore everything about ER309, including its composition, applications, advantages, disadvantages, and best welding practices.
What is ER309 Welding Rod?
ER309 is a stainless steel welding filler metal designed primarily for welding dissimilar metals. It has a high chromium (23%) and nickel (13%) content, making it highly resistant to oxidation and corrosion. This rod is available in different forms, including:
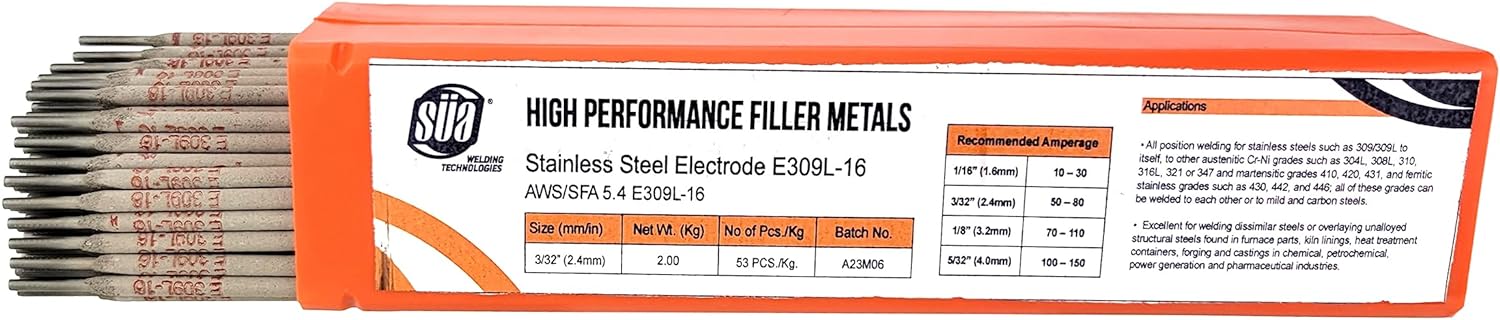
- MIG welding wire (ER309L)
- TIG welding filler rods (ER309)
- Stick electrodes (E309-XX)
It is commonly used in both TIG (GTAW) and MIG (GMAW) welding processes, as well as SMAW (stick welding) when using coated electrodes.
Chemical Composition of ER309 Welding Rod
The composition of ER309 provides its unique welding properties. The approximate chemical composition includes:
- Chromium (Cr): 22-24%
- Nickel (Ni): 12-14%
- Manganese (Mn): 1-2%
- Silicon (Si): 0.30-0.65%
- Carbon (C): 0.08% (or 0.03% for ER309L)
The high chromium and nickel levels enhance corrosion resistance, oxidation resistance, and ductility.
Applications of ER309 Welding Rod
ER309 is widely used across different industries due to its strength, versatility, and corrosion resistance. Some key applications include:
Welding Stainless Steel to Mild Steel
- Ideal for structural welds where stainless and carbon steel need to be joined.
- Commonly used in fabrication, piping, and automotive repairs.
Buffer Layers in Cladding
- Acts as an intermediate layer before applying another layer of stainless steel.
- Used in industries where wear resistance is necessary.
High-Temperature Applications
- Works well in environments that experience extreme heat and oxidation.
- Used in furnace parts, heat exchangers, and pressure vessels.
Maintenance & Repair Welding
- Suitable for repairing stainless steel parts and worn-out machine components.
- Prevents contamination and rust formation.
Advantages of ER309 Welding Rod
Using ER309 welding rods has multiple benefits, including:
Excellent Dissimilar Metal Joining
- Forms a strong, crack-resistant weld between stainless steel and carbon steel.
- Ideal for structural and industrial applications.
Superior Corrosion Resistance
- Withstands harsh environmental conditions, including chemical exposure.
- Used in food processing, marine, and chemical industries.
High Strength & Durability
- Produces tough welds with high tensile strength.
- Suitable for load-bearing and high-stress applications.
Good High-Temperature Performance
- Can handle extreme heat and thermal cycling.
- Great for welding furnace parts and exhaust systems.
Disadvantages of ER309 Welding Rod
While ER309 is highly versatile, it has some limitations:
Higher Cost than Standard Steel Electrodes
- More expensive than carbon steel welding rods.
- Used selectively for special applications.
Not Suitable for Pure Stainless Steel Welding
- If welding only stainless steel, ER308 is a better choice.
- ER309 is mainly used when welding stainless to mild steel.
Requires Specific Welding Parameters
- Heat input must be controlled to prevent warping or cracking.
- Shielding gas selection is crucial for TIG and MIG welding.
Best Welding Practices for ER309
To achieve the best weld quality, follow these tips when using ER309 welding rods:
Recommended Welding Processes
- MIG Welding (GMAW) – Requires ER309L wire with a shielding gas (Argon/CO2 mix).
- TIG Welding (GTAW) – Uses ER309 rods with 100% Argon gas.
- Stick Welding (SMAW) – Use E309 electrodes for easy field applications.
Welding Parameters for ER309
Welding Process | Amperage Range | Shielding Gas |
---|---|---|
TIG (1/16″) | 50-90A | 100% Argon |
TIG (3/32″) | 90-130A | 100% Argon |
MIG (0.035″) | 120-180A | 75% Argon / 25% CO2 |
Stick (E309) | 80-140A | None |
Pre-Weld Preparation
- Clean the base metal thoroughly to remove dirt, rust, or oil.
- Maintain proper fit-up to prevent excessive gaps.
- Use a backing plate if welding thin metal to prevent burn-through.
Post-Weld Cleaning
- Brush welds with a stainless steel wire brush to remove oxides.
- Pickling or passivation can help enhance corrosion resistance.
- Avoid contamination with carbon steel brushes.
ER309 vs. Other Welding Rods
ER309 vs. ER308
Feature | ER309 | ER308 |
Best For | Stainless to Mild Steel | Stainless to Stainless |
Corrosion Resistance | High | Moderate |
Nickel Content | 13% | 10% |
Strength | Higher | Lower |
ER309 vs. E309 Electrodes
Feature | ER309 | E309 |
Process | MIG/TIG | Stick Welding |
Gas Required | Yes | No |
Slag Formation | No | Yes |
Conclusion
The ER309 welding rod is an essential filler metal for joining stainless steel to mild steel, buffer layers, and high-temperature applications. Its high corrosion resistance, strength, and versatility make it a popular choice in various industries.
When using ER309, select the right process (MIG, TIG, or Stick), control heat input, and clean welds properly to achieve the best results. Whether you’re welding structural components, repair work, or industrial parts, ER309 ensures strong, long-lasting welds.