Tack Welding: A Comprehensive Guide
Introduction to Tack Welding
Tack welding is a critical step in the welding process, often overlooked due to its simplicity. However, without effective tack welds, entire welding projects can fall apart. Tack welds serve as temporary welds used to hold workpieces in place before final welding, ensuring alignment, fit-up, and dimensional accuracy. This process is essential across a variety of industries, including construction, automotive manufacturing, and heavy equipment production.
The importance of tack welding goes beyond just temporary fixing. It influences the quality, efficiency, and overall outcome of the welding project. In this comprehensive article, we’ll explore everything you need to know about tack welding, from its types and applications to its importance and best practices.
Importance of Tack Welding in the Welding Process
The primary role of tack welding is to ensure proper fit-up and alignment of components before completing the full weld. Without it, the structure could shift, deform, or lose its required tolerances. Here are some key reasons why tack welding is so important:
1. Maintains Proper Alignment: Tack welds hold pieces in the correct position until permanent welds are made. Without them, pieces could shift, making it impossible to achieve the necessary alignment for high-quality welds.
2. Prevents Distortion: Tack welding is a valuable tool for minimizing distortion caused by heat input. Distortion occurs when heat from welding causes metal to expand and contract. By placing tack welds strategically, welders can minimize these shifts.
3. Improves Final Weld Quality: Tack welds create a foundation for final welds. They ensure that the final weld will be uniform and continuous, reducing the chances of defects or imperfections.
4. Increases Welding Efficiency: By pre-aligning parts, tack welding helps speed up the welding process. This is particularly important in large-scale industrial projects, where efficiency is critical.
5. Prepares Components for Multi-Pass Welding: When welding thicker materials, tack welds provide initial holding power, ensuring that pieces stay securely in place as additional passes are completed.
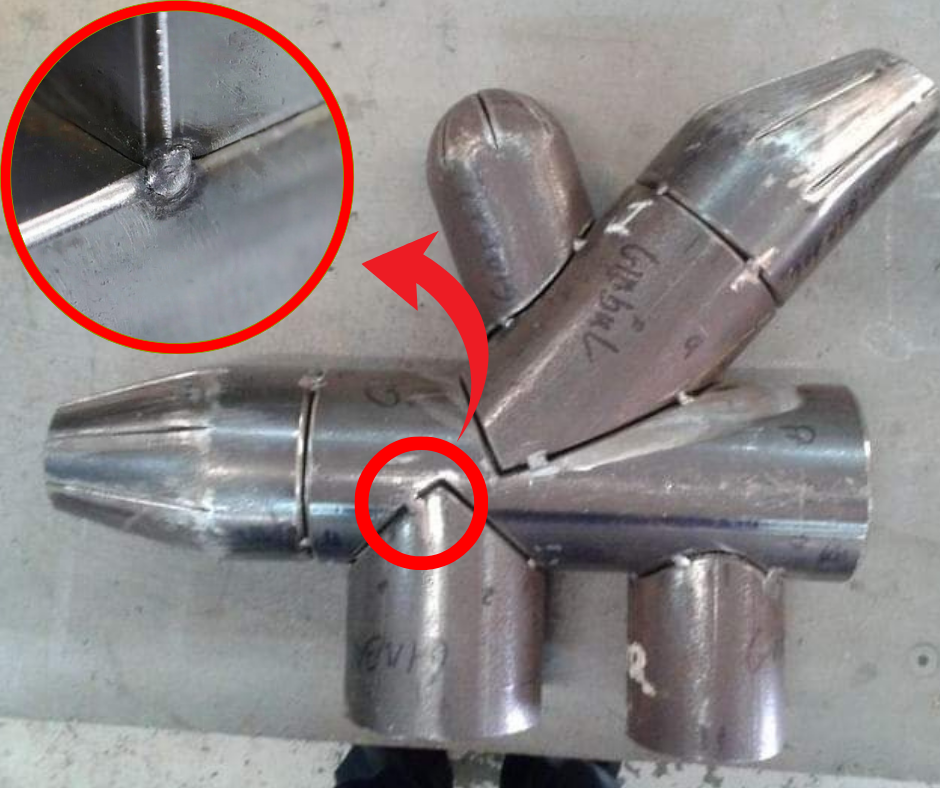
Types of Tack Welding
There are various types of tack welding, each suited to different materials, thicknesses, and joint configurations. Understanding the different types of tack welds helps in choosing the right one for your project.
1. Standard Tack Weld
Standard tack welds are the most common and are used to temporarily hold two or more pieces of metal together. These welds are typically small and short, designed to keep the materials in place until the final weld is made. Standard tack welds are widely used in fabrication, construction, and pipe welding.
2. Temporary Tack Weld
Temporary tack welds are used to hold the workpieces together but are often removed or ground down once the final welds are made. This type of tack welding is common when the appearance of the final product is critical, and tack welds cannot remain visible.
3. Permanent Tack Weld
In some cases, tack welds are left in place and become part of the final weld joint. This is often done in situations where the tack weld provides additional strength or when aesthetic considerations are less important. Permanent tack welds are commonly used in structural applications.
4. Bridge Tack Weld
Bridge tack welds are used when there is a gap between the materials being joined. Instead of directly welding the edges, a bridge is created using filler material to span the gap. This type of tack weld is often used in pipe welding and other applications where gaps are unavoidable.
5. Intermittent Tack Weld
Intermittent tack welding involves placing small welds at intervals along the joint. This method is used when long joints are involved, and continuous tack welding would be inefficient or unnecessary. Intermittent tack welds provide sufficient holding power without the need for a continuous weld.
Importance of Proper Tack Welding Placement
Tack weld placement plays a crucial role in ensuring that the final weld is free of defects and performs well in service. Improperly placed tack welds can result in misalignment, distortion, and other issues that affect the quality of the weld. Here are some key considerations when placing tack welds:
1. Positioning: Tack welds should be placed symmetrically along the joint to ensure even distribution of heat and minimize distortion. Asymmetrical placement can cause the material to warp or shift, leading to misalignment.
2. Size of Tack Welds: The size of the tack weld should be appropriate for the thickness and type of material being welded. Tack welds that are too small may not provide enough holding power, while overly large tack welds can lead to excessive heat input and distortion.
3. Spacing: The distance between tack welds depends on the length of the joint and the material being welded. Longer joints typically require more tack welds to prevent movement and misalignment. However, placing tack welds too closely can lead to unnecessary heat input, increasing the risk of distortion.
Tack Welding Techniques
There are several techniques used in tack welding to ensure proper fit-up and alignment. These techniques vary based on the type of joint, the materials being welded, and the final application of the weld.
1. Butt Joint Tack Welding
Butt joints are one of the most common types of joints in welding. In tack welding a butt joint, the tack welds are placed at regular intervals along the joint to hold the edges of the materials together. For long joints, additional tack welds may be added in the center to prevent movement.
2. Lap Joint Tack Welding
In a lap joint, one piece of material overlaps another. Tack welds are placed along the edges of the overlap to hold the two pieces together. Proper spacing of tack welds is crucial to ensuring that the final weld will be continuous and strong.
3. T-Joint Tack Welding
In a T-joint, one piece of material is welded at a right angle to another. Tack welds are placed at the ends of the joint and at regular intervals along the vertical piece to hold it in place. Tack welding in a T-joint is important to prevent the vertical piece from shifting during the welding process.
4. Pipe Tack Welding
Tack welding is especially important in pipe welding to ensure proper alignment of the pipes. Tack welds are placed at intervals around the circumference of the pipe to hold the pieces in place. In some cases, bridge tack welds may be used to span gaps between misaligned pipes.
Preventing Distortion in Tack Welding
One of the primary challenges in tack welding is preventing distortion caused by heat input. Distortion can occur when the material expands and contracts unevenly due to welding heat. Here are some strategies for preventing distortion during tack welding:
1. Use Small Tack Welds: Smaller tack welds produce less heat, reducing the risk of distortion. However, they must be strong enough to hold the materials in place.
2. Evenly Distribute Tack Welds: Tack welds should be placed symmetrically along the joint to ensure even distribution of heat. This helps prevent the material from warping or shifting.
3. Preheat the Material: Preheating the material before tack welding can reduce the risk of distortion by allowing the material to expand and contract more evenly.
4. Use Clamps or Fixtures: Clamps and fixtures can be used to hold the material in place during tack welding, reducing the risk of movement and distortion.
Removing Tack Welds
In some cases, tack welds may need to be removed before the final weld is made, especially if they are not part of the finished product. Tack welds can be removed using grinding, cutting, or chipping tools. Care must be taken to remove the tack welds without damaging the base material.
When removing tack welds, it’s important to ensure that the material remains aligned and that no gaps are created. In some cases, tack welds are removed after completing the root pass in multi-pass welding.
Safety Considerations in Tack Welding
Tack welding, like all types of welding, requires attention to safety. The use of protective equipment and adherence to safety procedures is essential to prevent accidents and injuries. Here are some key safety considerations in tack welding:
1. Wear Proper Protective Equipment: Welders should wear appropriate personal protective equipment (PPE), including welding helmets, gloves, and protective clothing, to protect against burns, sparks, and radiation.
2. Ventilation: Tack welding produces fumes that can be harmful if inhaled. Proper ventilation is necessary to ensure a safe working environment.
3. Fire Prevention: Sparks from tack welding can ignite flammable materials in the work area. Welders should ensure that the work area is free of flammable materials and that fire extinguishers are readily available.
Conclusion
Tack welding is an essential step in the welding process, providing the necessary alignment, fit-up, and stability for final welds. By understanding the types of tack welds, their applications, and best practices for placement and removal, welders can ensure high-quality, defect-free welds. Proper tack welding not only improves the efficiency of the welding process but also enhances the overall strength and durability of the final product. Whether in construction, manufacturing, or repair work, tack welding is a fundamental skill that every welder must master.