Underwater Welding Procedure, Working and Safety
Introduction
Underwater welding, also known as subaqueous welding, is a specialized field that involves the use of welding techniques to join metal structures below the surface of the water. The process is used in a variety of industries such as shipbuilding and repair, offshore oil and gas, and dam and hydroelectric power construction. It is considered a challenging and demanding field, requiring a unique set of skills and qualifications, as well as a strong understanding of the marine environment.
The work of an underwater welder requires not only strong welding skills, but also the ability to work in difficult and hazardous conditions, often while wearing heavy diving gear and working at depths of hundreds of feet. Despite the challenges, a career in underwater welding can be highly rewarding, offering diverse job opportunities and the chance to work on exciting and cutting-edge projects.
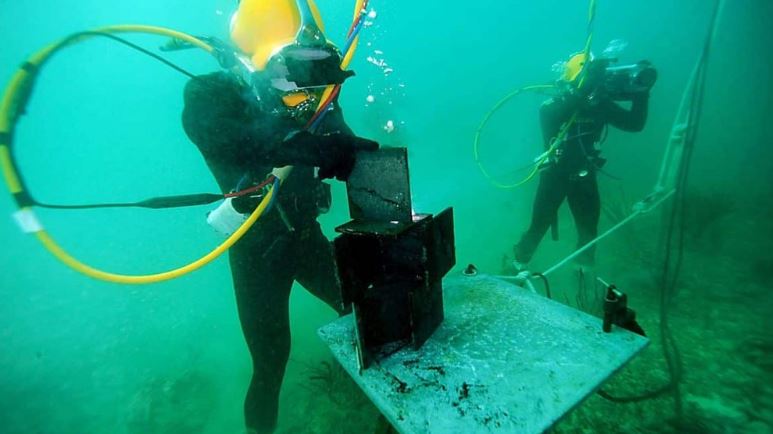
Types of Underwater Welding
There are two main types of underwater welding: wet welding and dry welding.
Wet Welding is a method of welding where the metal surfaces to be joined are coated with a flux, which is a chemical substance that helps to remove impurities and prevent oxidation during the welding process. The flux also helps to create a protective shield of gas around the welding area, which can improve the quality of the weld and make it easier to control the weld pool. Wet welding is typically done with a gas shielded welding process, such as Gas Tungsten Arc Welding (GTAW) or Gas Metal Arc Welding (GMAW).
Dry Welding, on the other hand, is a method of welding where the metal surfaces to be joined are not coated with a flux. Instead, the welding process is typically done in a controlled atmosphere, such as an inert gas, to prevent oxidation and other impurities from contaminating the weld pool. Dry welding is typically done with a gas shielded welding process, such as Gas Tungsten Arc Welding (GTAW) or Gas Metal Arc Welding (GMAW).
Working of Underwater Welding
Underwater welding is a specialized form of welding that is used to repair and maintain structures that are located underwater. The process is similar to traditional welding, but it requires specialized equipment and techniques to ensure the safety of the welders and the integrity of the weld.
The first step in underwater welding is to prepare the area for welding by cleaning and preparing the surface of the structure to be repaired. This may involve removing any rust, corrosion, or other debris from the surface. Next, a diver will use a cutting torch to shape the metal and prepare it for welding.
Once the surface is prepared, the diver will use a specialized welding machine to make the weld. The welding machine will be powered by a generator on the surface, and the diver will use a special underwater welding cable to connect the welding machine to the metal being welded. The cable will also provide the diver with communications, lighting and other necessary equipment.
The diver will use a shielding gas, such as argon, to protect the weld from contamination by water. The shield gas is delivered to the weld area through hoses, while the diver uses a TIG or MIG welding process to make the weld.
Underwater Welding Procedures
There are several techniques used in underwater welding, including:
- Shielded Metal Arc Welding (SMAW): Also known as “stick welding,” this is one of the most common techniques used in underwater welding. The welder uses a stick electrode that is coated in flux, which helps protect the weld from the surrounding water. This method is versatile and can be used on a variety of materials, including steel, aluminum, and titanium.
- Gas Tungsten Arc Welding (GTAW): This method, also known as “Tig welding,” uses a non-consumable tungsten electrode to create the weld. A shielding gas, such as argon, is used to protect the weld from the surrounding water. This method is typically used for more precise and thinner materials, such as stainless steel and aluminum.
- Gas Metal Arc Welding (GMAW): Also known as “Mig welding,” this method uses a wire electrode that is fed through a gun and into the weld. A shielding gas is used to protect the weld from the surrounding water. This method is typically used for welding thicker materials, such as steel.
- Submerged Arc Welding (SAW): this method uses a submerged welding electrode that is fed through a tube, and the arc is formed between the electrode and the workpiece. The method is typically used for welding heavy thicknesses of materials.
Equipment and Tools for Underwater Welding
The equipment and tools needed for underwater welding vary depending on the technique being used, but generally include:
- Welding machine: A power source that provides the necessary electrical current to create the weld.
- Electrodes: The consumable material that is used to create the weld.
- Welding torch: The tool used to direct the welding current to the workpiece.
- Shielding gas: Used to protect the weld from the surrounding water.
- Dive gear: Including a wet suit, diving helmet, and underwater communication equipment.
- Safety gear: including gloves, goggles, and a welding helmet
- Special welding equipment: including underwater welding gun, and lance.
Underwater Welding Risks
Underwater welding presents several risks, including:
- Water pressure: The increased pressure at depth can make it more difficult to create a stable weld.
- Contamination: Water can easily contaminate the weld, causing it to be weak or porous.
- Visibility: Limited visibility underwater can make it difficult to see the weld and the surrounding area.
- Temperature: Cold water can cause the metal to contract, making it more difficult to weld.
- Safety concerns: Divers must take extra precautions to ensure their safety while working underwater, including using proper dive gear and following established safety procedures.
Working in Underwater Welding
Skills and Qualifications
To become an underwater welder, an individual should have a solid foundation in welding techniques and have experience in welding in challenging conditions. They should be certified in welding, scuba diving and have a basic understanding of the marine industry. A certification from the American Welding Society (AWS) or the Association of Diving Contractors International (ADCI) is also typically required.
Work Environment and Conditions
Underwater welders work in a variety of conditions, including both fresh and saltwater environments, and at depths ranging from shallow to hundreds of feet deep. They are required to wear heavy diving gear and may be required to work in darkness, strong currents, and low visibility conditions. They may also be required to work on offshore oil platforms or at other remote locations.
Career Opportunities
Career opportunities for underwater welders include positions in the commercial diving industry, shipbuilding and repair, offshore oil and gas, and dam and hydroelectric power construction. Underwater welders may also work as self-employed contractors, and may advance to supervisory or management positions in their field. There are also other career opportunities such as being a welding engineer, diving supervisor, welding inspector, welding instructor, etc.
Safety in Underwater Welding
Safety is a critical aspect of underwater welding, as the underwater environment presents several unique hazards such as drowning, decompression sickness, hyperbaric welding, electrical hazards and confined spaces. To minimize these hazards, divers use specialized dive gear, safety equipment and follow safe diving procedures, and emergency procedures. Proper training and certification are essential for underwater welders to safely perform their job, and they should be trained not only in welding but also in diving and safety procedures.
Hazards Associated with Underwater Welding
Underwater welding presents several unique safety hazards that are not typically encountered in land-based welding, including:
- Drowning: Divers are at risk of drowning if their equipment fails or if they become incapacitated while working underwater.
- Decompression sickness: Also known as “the bends,” this condition can occur when a diver ascends too quickly and nitrogen bubbles form in the bloodstream.
- Hyperbaric welding: This condition can occur when a diver is exposed to high-pressure environments for extended periods of time, which can lead to a variety of health problems.
- Electrical hazards: Underwater welding presents a risk of electric shock, which can be fatal if proper precautions are not taken.
- Confined spaces: Welders may work in tight and restricted spaces, which can lead to difficulty in escaping in case of emergency.
Safety Precautions and Protocols
To minimize these hazards, several safety precautions and protocols are used in underwater welding, including:
- Dive gear: Divers use specialized gear, such as wet suits and diving helmets, to protect themselves from the water and the pressure.
- Safety equipment: Divers use personal protective equipment (PPE), such as gloves, goggles, and a welding helmet, to protect themselves from hazards such as flying sparks and heat.
- Safe diving procedures: Divers follow established safety procedures for diving, such as performing a pre-dive check and using dive tables to determine safe dive times and depths.
- Emergency procedures: Divers and team have in place emergency procedures to follow in case of an incident.
- Specialized equipment: Welders use equipment that is specifically designed for underwater use, such as dry chambers and remotely operated welding equipment, to minimize the risks associated with working underwater.
Proper Training and Certifications
Proper training and certifications are essential for underwater welders to safely perform their job. They should be trained and certified not only in welding but also in diving and safety procedures. Welders should be aware of the hazards associated with working underwater and know how to safely use the equipment and procedures. The training should cover topics such as the use of dive tables, dive planning, emergency procedures, and the safe use of specialized underwater welding equipment.
FAQs
Conclusion
Underwater welding is a specialized and potentially dangerous field that requires specialized equipment and techniques. The equipment needed for underwater welding includes a welding machine, electrodes, a welding torch, shielding gas, dive gear, safety gear, and special welding equipment. Underwater welding presents several unique challenges such as water pressure, contamination, visibility, temperature, and safety concerns. To overcome these challenges, divers use specialized equipment and techniques, such as dry chambers and remotely operated welding equipment, and follow established safety procedures.