What is the Voltage Reduction Device (VRD) in a Welder
Welding is an essential skill in many industries, but it comes with its risks—especially when it comes to electrical safety. Have you ever wondered how welders stay safe from potentially dangerous electrical shocks? That’s where the Voltage Reduction Devices (VRD) steps in. In this article, we’ll dive deep into everything you need to know about VRDs, their importance, and how they work.
Why Safety Matters in Welding
Imagine working with high-voltage equipment day in and day out. Without proper safety measures, welding can become a hazardous job. Electrical shocks are one of the most common risks welders face, especially when handling wet surfaces or damp environments.
The Role of Voltage Reduction Devices (VRDs)
Voltage Reduction Devices are game-changers in the welding industry. They’re designed to minimize the risk of electrical shock by reducing open-circuit voltage when the welder isn’t actively welding. Sounds like magic, doesn’t it? Let’s break it down further.
Understand Voltage Reduction Devices (VRDs)
What is a VRD?
A Voltage Reduction Device is an advanced safety feature integrated into modern welding machines. Its primary function is to lower the open-circuit voltage to safer levels when the welder isn’t operating. This keeps welders safe during downtime or while setting up their equipment.
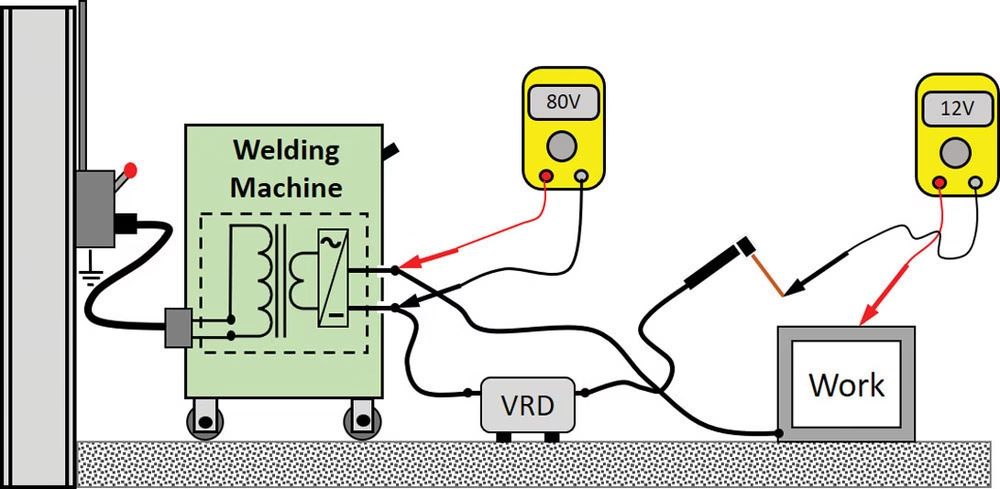
How Does a VRD Work?
Think of a VRD as a gatekeeper. When you’re not actively welding, it steps in and reduces the voltage output to prevent accidental shocks. Once you start welding, it allows full voltage to flow through for optimal performance.
Importance of VRDs in Welding
Protecting Welders from Electrical Shock
Welders often work under challenging conditions—wet floors, humid environments, and tight spaces. A VRD ensures that even if there’s accidental contact with electrodes or cables during setup, the voltage remains too low to cause harm.
Enhancing Workplace Safety
Safety isn’t just about individual protection; it’s about creating an environment where everyone feels secure. By incorporating VRDs into welding machines, companies can significantly reduce workplace accidents and improve overall safety standards.
Components of a Voltage Reduction Device
Key Parts of a VRD
A typical VRD consists of:
Voltage sensors
Control circuits
Signal processors
Each part plays its role in monitoring and adjusting voltage levels.
How These Components Function Together
These components work harmoniously to detect when the welder isn’t active and automatically reduce voltage output. It’s like having an automated safety guard watching over your equipment.
Types of Voltage Reduction Devices
Passive VRDs
Passive devices rely on simple mechanisms to reduce voltage without requiring external power sources. They’re cost-effective but may lack advanced features.
Active VRDs
Active devices use powered circuits for more precise control over voltage reduction. They’re ideal for high-performance welders who demand reliability and efficiency.
Benefits of Using VRDs in Welders
Improved Safety Standards
With a VRD installed, welders can focus on their craft without constantly worrying about electrical hazards. It’s like having peace of mind built into your machine.
Compliance with Regulations
Many industries mandate the use of safety features like VRDs to meet occupational health standards. Using them ensures compliance while boosting safety protocols.
How to Choose the Right VRD
Factors to Consider
When selecting a VRD, consider:
Compatibility with your welding machine
Type of welding jobs you perform
Budget constraints
Compatibility with Welding Machines
Not all welders are created equal! Ensure your chosen VRD aligns with your machine’s specifications for seamless integration.
Installation and Maintenance of VRDs
Proper Installation Guidelines
Installing a VRD requires precision. Follow manufacturer guidelines or consult professionals to ensure everything is set up correctly.
Tips for Maintenance and Troubleshooting
Regular inspections can keep your device functioning optimally. Look out for wear-and-tear signs or unusual behavior during operation.
Common Misconceptions About VRDs
Myth vs. Reality
Some people think that using a VRD might compromise welding performance or increase costs significantly. In reality, these devices are designed to enhance safety without affecting functionality—and they’re worth every penny!
FAQs
What are the main advantages of using a VRD in welding?
VRDs minimize electrical shock risks and improve overall workplace safety without compromising performance.
Can I retrofit a VRD to my existing welding machine?
Yes! Many manufacturers offer retrofit options compatible with older machines.
Are VRDs mandatory for all welders?
While not universally required, many industries strongly recommend them for compliance with safety regulations.
How do I know if my welder has a built-in VRD?
Check your machine’s specifications or consult the user manual—it should clearly indicate whether it includes this feature.
Do VRDs affect welding performance?
Not at all! They only reduce voltage during non-welding periods, ensuring optimal performance during actual operation.
Conclusion
Voltage Reduction Devices are essential tools that protect welders from electrical hazards while ensuring workplace safety standards are met. Whether you’re new to welding or an experienced professional, understanding how these devices work can make all the difference in creating safer environments.