Weld Metal Dilution Rate
When you’re laying down a weld, there’s a quiet chemistry dance happening under the hood—the weld metal dilution rate. It might not sound too flashy at first, but trust me, understanding weld dilution can make or break your weld’s quality, strength, and life span.
What is Dilution in Welding?
In simple words, dilution refers to the amount of base metal that mixes with the filler metal during welding. The weld pool isn’t made up of just your filler rod or wire—it’s a blend. And the more of the base metal that melts and joins in, the higher the dilution.
Why is Dilution Important in Welding Processes?
Dilution affects everything—hardness, strength, corrosion resistance, and even how your weld looks under X-ray or ultrasonic testing. If you’re hardfacing, for example, you want your expensive wear-resistant alloy to stay intact, not get watered down by the base metal.
Factors Affecting Weld Metal Dilution Rate
Welding Process Type (SMAW, MIG, TIG, SAW, etc.)
Each process delivers heat differently:
SMAW (Stick Welding) tends to have moderate dilution.
TIG Welding offers low dilution, which is great for precise control.
SAW (Submerged Arc Welding) can result in high dilution due to deep penetration.
MIG (GMAW) sits somewhere in the middle.
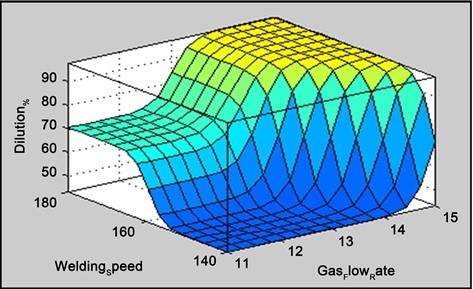
Heat Input and Travel Speed
More heat and slower travel mean the base metal stays molten longer—so, more dilution. On the flip side, faster travel and lower heat reduce mixing.
Electrode Diameter and Current Settings
Bigger electrodes and higher amperage dig deeper into the base metal. If your goal is low dilution, dial it down.
Position and Joint Design
Flat position welds generally have more heat buildup and thus higher dilution. Tight joint gaps or complex geometries can also mess with dilution levels.
Measuring and Calculating Weld Dilution
The Basic Formula for Dilution
The general formula goes like this:
Dilution (%) = (Weight of Base Metal in Weld / Total Weld Metal Weight) × 100
You can also use area or volume if that’s easier in your setup.
Practical Example with Calculation
Say your weld metal has 3 grams of filler and 1 gram of base metal melted in:
Dilution = (1 / 4) × 100 = 25%
That’s a decent dilution rate for general fabrication.
Lab Testing for Accurate Dilution Measurement
In critical industries, labs use spectroscopy or chemical analysis to nail down exact dilution rates, especially when alloy composition is vital.
Optimal Weld Dilution Levels for Different Processes
High vs. Low Dilution – Pros and Cons
High Dilution Pros: Strong fusion, good penetration, sometimes fewer passes needed.
High Dilution Cons: Can weaken alloy properties or cause cracking.
Low Dilution Pros: Maintains filler metal chemistry, especially important for hardfacing and cladding.
Low Dilution Cons: May require more passes or layers.
Ideal Ranges for Common Welding Processes
Process | Typical Weld Dilution Range |
---|---|
TIG | 5–15% |
MIG | 10–25% |
SMAW | 15–30% |
SAW | 25–45% |
Effects of Dilution on Weld Quality
Mechanical Properties of Weld Metal
Dilution impacts tensile strength, ductility, and toughness. For example, too much mild steel in a high-tensile filler metal weld weakens the overall joint.
Corrosion Resistance and Metallurgical Behavior
Alloy dilution can kill corrosion resistance. Especially in stainless or exotic alloys, even 5-10% extra dilution can ruin it.
Cracking and Other Weld Defects
Dilution can lead to hot cracking, porosity, or embrittlement if not kept in check—especially in multi-pass welds.
Controlling Weld Metal Dilution
Process Parameter Adjustment
To reduce dilution:
Use lower amperage
Increase travel speed
Use smaller electrodes
Filler Metal Selection Strategy
Choose filler metals with buffering elements to resist negative effects of base metal mixing.
Multi-pass vs. Single-pass Techniques
Using multiple passes can reduce dilution in each layer. For example, a butter layer can act as a barrier to protect final overlay properties.
Dilution in Hardfacing and Cladding Applications
Why Low Dilution is Crucial Here
Hardfacing relies on specific alloys for wear resistance. If the dilution is too high, those expensive materials lose their magic.
Strategies to Minimize Dilution in Cladding
TIG or Cold Wire TIG
Use buffer layers
Keep heat input low
Overlay multiple layers to “bury” the dilution zone
Applications and Case Studies
Structural Steel Fabrication
Too much dilution in high-strength steel welding can lead to brittle failures. Keeping dilution balanced ensures performance under load.
Pressure Vessels and Piping
Dilution impacts corrosion resistance and pressure ratings. In petrochemical applications, it’s a major QC checkpoint.
Offshore and Marine Welding
Saltwater is unforgiving. Dilution affects how long a weld survives in harsh marine environments.
Common Myths and Misunderstandings
“More Dilution Means Stronger Weld” – Not Always True
That’s like saying more sauce makes a better pizza. Not true if the sauce dilutes the flavor of everything else.
Misconceptions about Automatic Processes
Some believe robots always get it right. But automation doesn’t eliminate dilution—it just repeats it consistently. You still have to set it up correctly!
FAQs
What is the acceptable dilution range in welding?
It depends on the process, but generally 10–30% is acceptable for most applications.
How can I reduce dilution in my welds?
Use low heat input, faster travel speed, and smaller electrodes. Multi-pass welding also helps.
Does dilution affect weld strength?
Yes. It directly affects the mechanical and metallurgical properties of the weld.
Can dilution be controlled in automated welding?
Absolutely! But it depends on programmed settings, not just the machine. The operator still plays a crucial role.
Is dilution more critical in certain industries?
Yes—oil & gas, marine, aerospace, and nuclear industries are extremely sensitive to dilution levels due to performance and safety requirements.
Conclusion
Weld metal dilution rate might sound like a niche topic, but it’s at the heart of good welds. Whether you’re laying beads in a fab shop or working on critical infrastructure, knowing how dilution works gives you an edge. It’s not just about fusing metal—it’s about controlling the chemistry, ensuring strength, and building something that lasts. And that, my friend, is the difference between a welder and a welding expert.