Understanding Weld Pool and Cooling Rates
Welding is an intricate process that involves the fusion of metals at high temperatures. Among the many factors that influence the final quality of a weld, two of the most critical elements are the weld pool and cooling rates. Understanding how these work can drastically improve the quality and longevity of your welds. In this article, we’ll break down what the weld pool is, the science behind its formation, how cooling rates impact welding, and what you can do to control both for optimal results.
Introduction
What is a Weld Pool?
The weld pool is the molten metal that forms when the welding arc melts the base metal and filler material. It’s essentially a “pool” of liquid metal that you create during the welding process, and the quality of this pool directly affects the integrity of the weld.
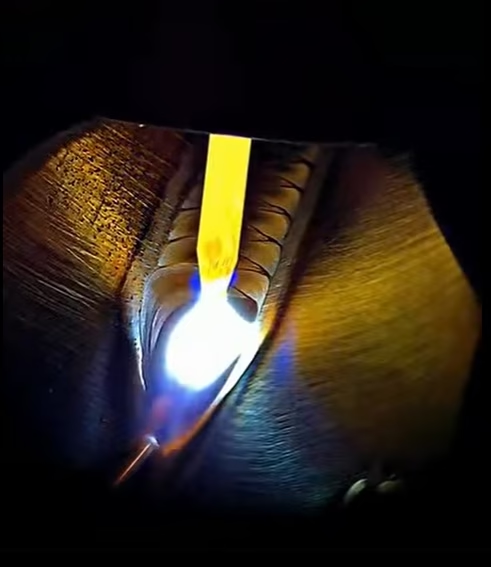
Why is the Weld Pool Crucial in Welding?
The weld pool is important because it determines the shape, strength, and overall durability of the weld. If the weld pool is poorly controlled, you might end up with issues like cracks, porosity, or weak bonding between the materials. The ability to manage the weld pool’s temperature, size, and cooling rate is critical to producing a high-quality weld.
The Science Behind Weld Pool Formation
How Does the Weld Pool Form?
When you begin welding, the heat generated by the welding arc melts both the base material and the filler material (if used). This creates a molten pool of metal. The molten metal is usually surrounded by solidified metal, creating a narrow and deep “V” or “U”-shaped groove. The cooling rate and the way this pool solidifies play a large role in determining the final quality of the weld.
Key Factors That Influence Weld Pool Size and Shape
Several factors contribute to how the weld pool forms, such as:
- Heat Input: Higher heat input creates a larger weld pool.
- Welding Speed: Slow welding speeds tend to produce deeper and wider weld pools.
- Weld Position: Vertical or overhead welding might create more challenging conditions for controlling the weld pool.
- Material Thickness: Thicker materials require more heat to create a weld pool of sufficient size.
Cooling Rates in Welding
What Are Cooling Rates in Welding?
Cooling rate refers to the speed at which the molten weld pool solidifies after the arc has passed. The rate of cooling can have a significant effect on the mechanical properties of the weld, such as hardness, tensile strength, and resistance to cracking. In welding, the cooling process isn’t instantaneous, and it’s crucial to control it to ensure that the weld metal solidifies properly.
How Cooling Rates Affect the Weld Pool
A fast cooling rate can lead to issues like brittle welds or internal stresses, while slow cooling can result in the formation of coarse grain structures, which might weaken the weld. Finding the right balance is key.
Factors Affecting Cooling Rates
Heat Input
The amount of heat applied during welding plays a direct role in how quickly the molten metal cools. More heat generally leads to slower cooling rates because the surrounding metal stays molten for longer.
Material Type
Different materials have different thermal conductivities. For example, steel cools slower than aluminum, meaning you need to adjust the cooling methods based on the material being welded.
Electrode Type and Size
The type of electrode you use can affect the cooling rate. Larger electrodes tend to deposit more filler metal, which increases the heat input and slows cooling. The material of the electrode also matters; some electrodes can help cool the weld more evenly.
Welding Process
The type of welding process you’re using impacts the cooling rate. For instance, processes like TIG welding produce more concentrated heat, leading to faster cooling rates compared to processes like stick welding, which spreads heat over a larger area.
Effects of Cooling Rate on Weld Quality
Impact on Weld Strength
The cooling rate directly affects the mechanical properties of the weld. Rapid cooling can increase hardness but may also induce brittleness and make the weld susceptible to cracking under stress. Slow cooling can lead to the formation of softer materials that are less prone to cracking but may not offer the same level of tensile strength.
The Role of Cooling Rate in Weld Defects
Cooling rates are also a key factor in the formation of weld defects such as:
- Cracking: Rapid cooling can result in thermal stresses that cause cracks.
- Porosity: Improper cooling can trap gases in the weld, creating voids or holes.
- Lack of Fusion: If the weld pool cools too quickly, it might not fuse properly with the base metal.
How Fast Is Too Fast?
Consequences of Rapid Cooling
While rapid cooling might seem like a good way to harden the weld, it can cause the formation of martensite, a brittle structure that’s more prone to cracking. If you’re welding high-strength materials, a fast cooling rate can lead to a weld that lacks the toughness required for certain applications.
Risks of Slow Cooling
On the other hand, slow cooling allows for the formation of coarse grain structures, which can reduce the strength of the weld. It can also promote the growth of undesirable microstructures that make the weld more susceptible to fatigue.
Weld Pool and Cooling Rate in Different Welding Processes
MIG Welding
MIG welding typically produces a higher heat input, which can lead to a slower cooling rate. This is generally beneficial because it allows for better penetration and less likelihood of cracking. However, the operator still needs to control the heat to avoid overheating the weld pool.
TIG Welding
TIG welding uses a more concentrated arc, leading to faster cooling rates. The welder needs to be particularly careful to manage this rate to avoid the formation of brittle microstructures while still achieving good weld penetration.
Stick Welding
Stick welding usually results in a slower cooling rate due to the wider arc. While this can help in controlling the solidification process, it also requires more heat input to maintain a proper weld pool.
Techniques to Control Cooling Rates
Pre-Heating the Material
One way to slow down the cooling rate is by pre-heating the material before welding. This method is particularly useful for thick sections of metal or materials with high thermal conductivity, such as aluminum.
Post-Weld Heat Treatment
After welding, heat treatment can be applied to control the cooling process. This might involve slowly cooling the weld in a controlled environment or using controlled cooling techniques such as water quenching or air cooling.
Use of Cooling Liquids
In some cases, welders use cooling liquids like water or specific gels to control the cooling rate. This can help improve the overall strength and appearance of the weld.
Best Practices
Proper Heat Control Techniques
To achieve an optimal weld pool and cooling rate, it’s essential to monitor and adjust heat input constantly. Keeping the heat within a controlled range ensures the correct cooling rate for the desired weld characteristics.
Monitoring Welding Parameters
Welders should always keep track of welding parameters such as voltage, amperage, and welding speed. These can directly impact the size of the weld pool and the cooling rate, making it crucial to adjust these factors throughout the welding process.
FAQs
What happens if the cooling rate is too slow during welding?
A slow cooling rate can lead to coarse grains in the weld, which reduces its strength and increases susceptibility to cracks.
How can I control the cooling rate in TIG welding?
Controlling the cooling rate in TIG welding involves adjusting heat input, controlling the welding speed, and using post-weld heat treatment if needed.
What’s the effect of a fast cooling rate on weld strength?
A fast cooling rate can increase hardness but may also lead to brittleness, making the weld more prone to cracking.
Why is cooling rate important in MIG welding?
In MIG welding, the cooling rate affects penetration, strength, and the overall quality of the weld. Rapid cooling can result in defects such as cracking.
What role does the material play in cooling rates during welding?
Different materials cool at different rates. Materials like steel and aluminum have distinct thermal properties that influence how fast or slow they cool during welding, which impacts the final weld quality.
Conclusion
The weld pool and cooling rates are two of the most crucial factors influencing the quality of a weld. By understanding how they work and how to control them, you can create stronger, more durable welds. Whether you’re working with steel, aluminum, or any other material, always consider the cooling rate to avoid defects and achieve the best possible weld.