Weldability of Aluminum Alloys
Aluminum alloys have become integral to various industries due to their unique combination of lightweight, strength, and resistance to corrosion. However, welding these alloys poses certain challenges due to their distinct properties. This article explores the weldability of aluminum alloys, covering the factors that affect their weldability, the pre-welding preparations required, the availability of different aluminum alloys, and the best practices for achieving strong, reliable welds.
Understanding Aluminum Alloys
Overview of Aluminum Alloys
Aluminum alloys are created by adding alloying elements like copper, magnesium, silicon, and zinc to pure aluminum. These alloys are classified into different series based on their primary alloying element and the resultant mechanical properties. The most common series include:
- 1xxx Series: Pure aluminum with a minimum of 99% aluminum content. Highly resistant to corrosion but low in strength. Used in electrical applications and chemical equipment.
- 2xxx Series: Alloyed primarily with copper. High strength but less corrosion-resistant. Commonly used in aerospace applications.
- 3xxx Series: Alloyed with manganese. Good corrosion resistance and moderate strength. Widely used in automotive and building applications.
- 5xxx Series: Alloyed with magnesium. Excellent corrosion resistance and good weldability. Used in marine and automotive industries.
- 6xxx Series: Alloyed with magnesium and silicon. Good strength, corrosion resistance, and weldability. Popular in structural applications.
- 7xxx Series: Alloyed with zinc. Very high strength but susceptible to stress corrosion cracking. Used in aerospace and military applications.
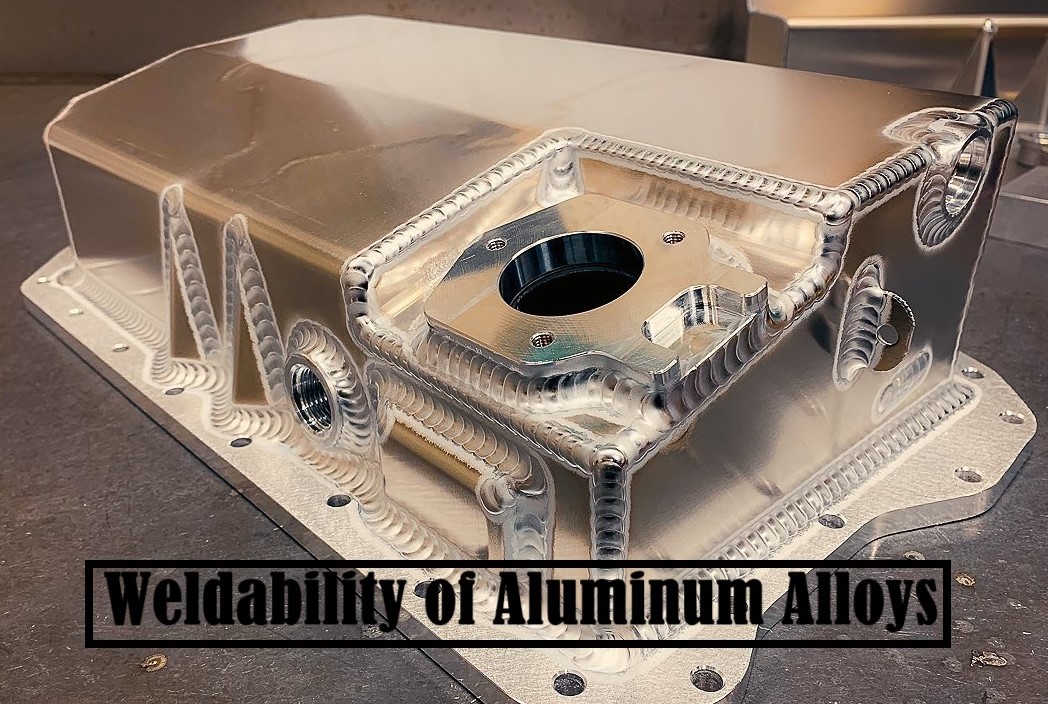
Common Aluminum Alloys and Their Weldability
6061 Aluminum Alloy
6061 is one of the most versatile and commonly used aluminum alloys. It is part of the 6xxx series and is known for its good weldability, corrosion resistance, and strength. 4043 and 5356 filler wires are typically used for welding 6061 aluminum, depending on the specific application and desired properties of the weld.
5052 Aluminum Alloy
5052 is a 5xxx series alloy, highly valued for its excellent corrosion resistance, particularly in marine environments. It offers good weldability and is commonly used in applications such as boat hulls, fuel tanks, and chemical containers. 5356 filler wire is often used for welding 5052 aluminum, providing strong, corrosion-resistant welds.
7075 Aluminum Alloy
7075 is a high-strength alloy from the 7xxx series, primarily used in aerospace and military applications. While it offers exceptional strength, its weldability is more challenging due to its susceptibility to stress corrosion cracking. For welding 7075, 5356 filler wire is commonly used, although post-weld heat treatment is often required to improve the weld’s mechanical properties.
2024 Aluminum Alloy
2024 is another high-strength alloy, part of the 2xxx series, widely used in the aerospace industry. It has lower corrosion resistance and is prone to cracking during welding, making it more difficult to weld than other aluminum alloys. 2319 filler wire is typically used for welding 2024 aluminum, providing a good balance between strength and crack resistance.
5083 Aluminum Alloy
5083 is a 5xxx series alloy known for its exceptional resistance to corrosion in marine environments. It offers good weldability and is often used in shipbuilding, offshore structures, and chemical tanks. 5356 filler wire is the preferred choice for welding 5083 aluminum, ensuring strong and durable welds that can withstand harsh environments.
Factors Affecting the Weldability of Aluminum Alloys
Thermal Conductivity
Aluminum has high thermal conductivity, which means it dissipates heat rapidly during welding. This property requires higher heat input during welding to ensure proper fusion, but it can also lead to issues such as distortion or incomplete penetration if not managed correctly.
Oxide Layer
Aluminum naturally forms a thin oxide layer on its surface when exposed to air. This oxide layer has a higher melting point than aluminum itself, which can interfere with the welding process. If not properly removed, it can lead to poor weld quality and defects such as porosity.
Hot Cracking
Certain aluminum alloys, particularly those in the 2xxx and 7xxx series, are prone to hot cracking during welding. This occurs due to the alloy’s susceptibility to solidification cracking, which can compromise the integrity of the weld. Controlling the welding parameters and filler material selection is crucial to minimize this risk.
Porosity
Porosity is a common issue in aluminum welding, often caused by the entrapment of gases during the welding process. Factors such as moisture, contamination, and improper shielding gas can contribute to porosity, leading to weak welds.
Pre-Welding Preparations for Aluminum Alloys
Surface Cleaning
Cleaning the surface of aluminum alloys before welding is essential to remove the oxide layer, oils, and contaminants that can affect weld quality. Mechanical cleaning methods, such as wire brushing or grinding, are commonly used to remove the oxide layer. Additionally, chemical cleaning with solvents like acetone can remove oils and grease.
Preheating Techniques
Preheating aluminum alloys before welding can reduce thermal stresses and minimize the risk of hot cracking. Preheating is particularly important for thicker materials or alloys that are prone to cracking, such as those in the 2xxx and 7xxx series. The recommended preheat temperature typically ranges between 200°F to 300°F (93°C to 149°C).
Pre-Welding Joint Preparation
Proper joint preparation is crucial for aluminum welding, especially for alloys that are prone to cracking or have high thermal conductivity. Beveling the edges of thick materials helps ensure complete penetration, and using appropriate joint designs, such as a V-groove or double-V groove, can improve weld quality. Proper fit-up is also important to minimize gaps and ensure consistent welds.
Electrodes and Filler Wires for Welding Aluminum Alloys
4043 Filler Wire
4043 is a versatile filler wire commonly used for welding 6xxx series aluminum alloys. It contains silicon, which helps improve fluidity and reduce cracking during welding. 4043 is ideal for applications where good corrosion resistance and ease of welding are required.
5356 Filler Wire
5356 is an all-purpose filler wire suitable for welding 5xxx series aluminum alloys. It contains magnesium, which provides high strength and excellent corrosion resistance. 5356 is commonly used in marine, automotive, and structural applications where strength and durability are critical.
2319 Filler Wire
2319 is specifically designed for welding 2xxx series aluminum alloys, such as 2024. It contains copper, which helps match the mechanical properties of the base alloy, providing high strength and crack resistance. 2319 is often used in aerospace applications where the integrity of the weld is paramount.
4047 Filler Wire
4047 is similar to 4043 but contains a higher silicon content, providing even better fluidity and crack resistance. It is used for welding both 6xxx series and other aluminum alloys, particularly in applications where reduced cracking is essential, such as in automotive and aerospace industries.
Welding Techniques for Aluminum Alloys
TIG Welding (GTAW)
Tungsten Inert Gas (TIG) welding is commonly used for welding aluminum alloys, especially when high precision and control are required. TIG welding provides excellent control over the heat input and allows for precise welds with minimal spatter. It is ideal for thin materials and applications where aesthetics are important, such as in the aerospace and automotive industries.
MIG Welding (GMAW)
Metal Inert Gas (MIG) welding is another popular method for welding aluminum alloys. MIG welding offers faster welding speeds and is suitable for thicker materials. It is widely used in automotive and structural applications due to its ability to produce strong, consistent welds. However, proper shielding gas selection and wire feed settings are crucial to prevent porosity and other defects.
Friction Stir Welding (FSW)
Friction Stir Welding (FSW) is a solid-state welding process that is particularly effective for joining aluminum alloys. FSW involves rotating a non-consumable tool along the joint line, which generates frictional heat to soften the material and create a weld without melting the base metal. This technique is ideal for joining dissimilar aluminum alloys or creating long, continuous welds with minimal distortion.
Laser Beam Welding
Laser Beam Welding is a high-precision method that uses a focused laser beam to melt and fuse aluminum alloys. It is suitable for thin materials and applications where minimal heat input is required. Laser welding offers high welding speeds and produces welds with excellent aesthetics and minimal distortion, making it ideal for electronics, automotive, and aerospace applications.
Post-Welding Considerations
Post-Weld Heat Treatment
After welding, certain aluminum alloys, particularly those in the 2xxx and 7xxx series, may require post-weld heat treatment to restore their original mechanical properties. This process involves heating the welded area to a specific temperature and then cooling it at a controlled rate. Heat treatment can relieve internal stresses, reduce the risk of cracking, and improve the overall strength of the weld.
Inspection and Testing
Inspecting and testing the weld is crucial to ensure it meets the required standards. Visual inspections can reveal surface defects like cracks, porosity, or incomplete fusion. Non-destructive testing methods, such as ultrasonic testing or X-ray inspection, can be used to identify internal defects that are not visible on the surface.
Addressing Common Defects
If defects are identified during inspection, they must be addressed before the weld is put into service. This may involve re-welding, grinding, or applying additional passes to correct issues like porosity, cracking, or incomplete penetration. Ensuring that the weld is free from defects is vital for the safety and reliability of the final product.
Applications of Welded Aluminum Alloys
Automotive Industry
Aluminum alloys are increasingly used in the automotive industry to reduce vehicle weight and improve fuel efficiency. Components like engine blocks, transmission housings, and body panels are often made from welded aluminum alloys. Their excellent weldability makes them ideal for producing complex shapes and structures in automotive manufacturing.
Aerospace Industry
The aerospace industry relies heavily on aluminum alloys for their high strength-to-weight ratio and corrosion resistance. Aircraft structures, fuel tanks, and landing gear components are commonly made from aluminum alloys, with welding playing a crucial role in their fabrication. The ability to produce strong, lightweight welds is essential for the safety and performance of aerospace components.
Construction and Structural Applications
In construction, aluminum alloys are used for structural elements like beams, columns, and frames. Their corrosion resistance makes them particularly suitable for outdoor and marine environments. Welding allows for the creation of large, complex structures that are both strong and lightweight, contributing to the durability and efficiency of modern buildings.
Marine Applications
Aluminum alloys are widely used in the marine industry for shipbuilding, offshore structures, and recreational boats. Their resistance to corrosion in saltwater environments makes them ideal for these applications. Welding is commonly used to join aluminum components in the construction of hulls, decks, and other structural elements, ensuring that the final product is both lightweight and durable. Popular aluminum alloys in the marine industry include the 5xxx series, such as 5052 and 5086, which offer excellent weldability and corrosion resistance.
Electronics and Electrical Applications
Aluminum’s excellent electrical conductivity and lightweight properties make it a popular choice in the electronics and electrical industries. Welded aluminum is used in components like heat sinks, electrical enclosures, and connectors. The ability to produce precise, clean welds with minimal heat input is crucial for these applications, ensuring that the electrical properties of the material are not compromised.
FAQs
What is the best method for welding aluminum alloys?
The best method for welding aluminum alloys depends on the specific alloy and application. TIG welding is ideal for thin materials and applications requiring precision, while MIG welding is better suited for thicker materials and faster welding speeds.
Why is preheating important when welding aluminum alloys?
Preheating helps reduce thermal stresses and the risk of cracking during welding, especially for thicker materials or alloys prone to cracking, such as those in the 2xxx and 7xxx series.
What are common challenges when welding aluminum alloys?
Common challenges include managing aluminum’s high thermal conductivity, removing the oxide layer, preventing hot cracking, and avoiding porosity in the weld.
Which aluminum alloy is most commonly used in the aerospace industry?
7075 aluminum alloy is widely used in the aerospace industry due to its high strength, although it requires careful welding techniques to prevent stress corrosion cracking.
Can aluminum alloys be welded to other metals?
Yes, aluminum alloys can be welded to other metals, but it requires specialized techniques such as explosive welding, friction welding, or using a transition layer to ensure a strong bond between dissimilar materials.
Conclusion
Welding aluminum alloys presents unique challenges, but with the right techniques, preparation, and filler materials, it is possible to achieve strong, reliable welds. Understanding the properties of different aluminum alloys and how they respond to welding is crucial for selecting the appropriate welding method and ensuring high-quality results. Whether in automotive, aerospace, marine, or construction applications, aluminum alloys continue to play a vital role, offering a combination of lightweight, strength, and corrosion resistance that is unmatched by other materials.