Welding Consumables: Everything You Need to Know
Introduction
Welding is an essential process in various industries, enabling the fabrication and repair of metal structures. One crucial aspect of welding is the use of welding consumables. These materials play a pivotal role in achieving high-quality welds and ensuring the durability of welded joints. In this comprehensive guide, we’ll delve into the world of welding consumables, exploring their types, applications, and benefits.
Understanding Welding Consumables
What are Welding Consumables?
Welding consumables refer to materials that are used during the welding process to add or improve certain properties of the weld joint. These materials are essential for achieving proper fusion and ensuring the integrity of the weld. Welding consumables include electrodes, filler metals, and fluxes.
Importance in Welding Process
Welding consumables are not mere accessories but critical components of the welding process. They determine the quality, strength, and longevity of the weld. Selecting the right consumables can significantly impact the outcome of the welding project.
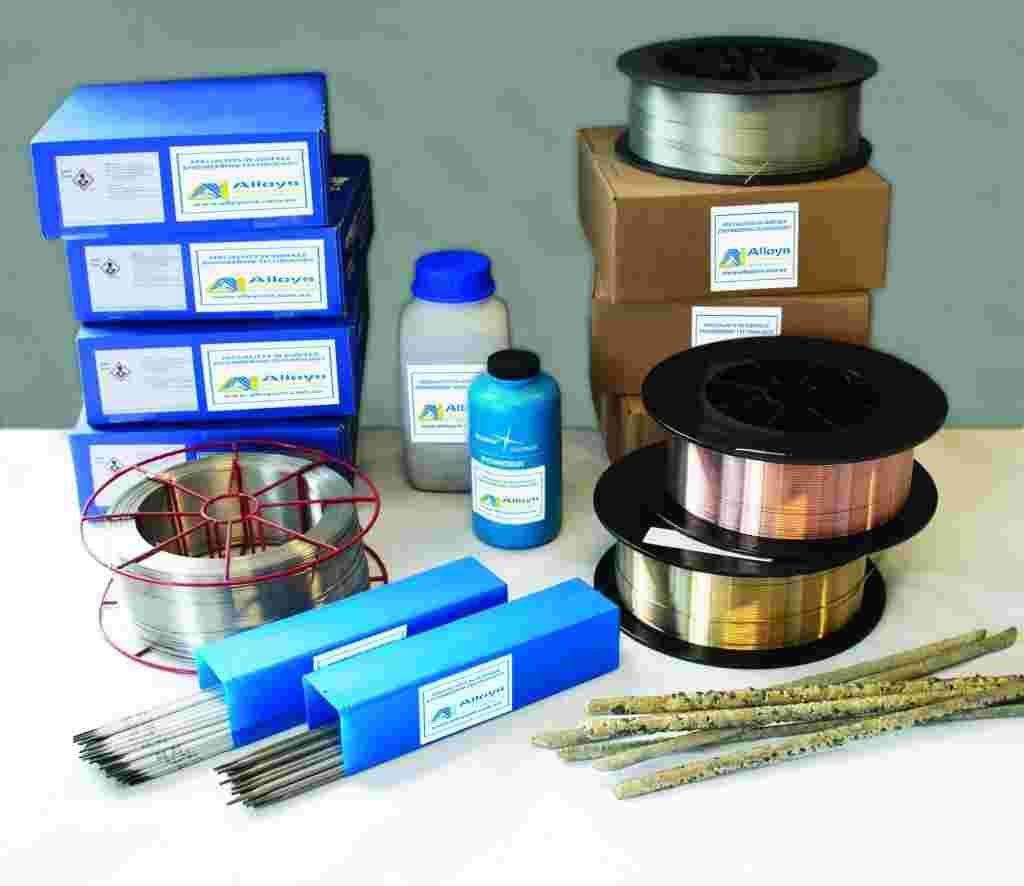
Types of Welding Consumables
Electrodes
Electrodes are welding consumables that provide the electrical current necessary to create an arc between the electrode and the base metal. They come in various types, such as coated electrodes for shielded metal arc welding (SMAW) and tungsten electrodes for tungsten inert gas (TIG) welding.
Filler Metals
Filler metals are used to fill the gap between two pieces of base metal during welding. They melt and fuse with the base metal to create a strong joint. Filler metals are commonly used in processes like gas metal arc welding (GMAW) and submerged arc welding (SAW).
Fluxes
Fluxes are substances that are used to protect the weld area from atmospheric contamination. They produce a protective gas shield that prevents oxidation and enhances the quality of the weld. Fluxes are often used in processes like flux-cored arc welding (FCAW).
Choosing the Right Welding Consumables
Matching Consumables to Base Materials
The choice of welding consumables depends on the type of base materials being welded. Matching the consumables to the base materials ensures a compatible and strong weld joint.
Considerations for Welding Techniques
Different welding techniques, such as MIG, TIG, and stick welding, require specific types of consumables. Understanding the requirements of each technique is essential for achieving optimal results.
Applications of Welding Consumables
Structural Welding
Welding consumables are widely used in the construction industry for creating strong and durable structures. Skilled welders utilize consumables to join beams, columns, and other components seamlessly.
Automotive Industry
In the automotive sector, welding consumables are crucial for assembling vehicle components. From the chassis to the exhaust system, consumables play a pivotal role in ensuring the safety and reliability of automobiles.
Shipbuilding
Shipbuilding relies heavily on welding consumables to create watertight and structurally sound vessels. These consumables help in connecting various parts of a ship’s hull and superstructure.
Benefits of Quality Welding Consumables
Improved Weld Integrity
High-quality consumables contribute to strong and durable welds that can withstand various stresses and conditions.
Reduced Defects and Failures
Using the right consumables decreases the likelihood of weld defects, minimizing the need for costly repairs and rework.
Enhanced Productivity
Quality consumables lead to smoother welding processes, reducing downtime and increasing overall productivity in welding projects.
Factors Affecting Welding Consumable Performance
Storage Conditions
Proper storage of consumables is essential to prevent moisture absorption and degradation, which can negatively affect weld quality.
Moisture Sensitivity
Some consumables are sensitive to moisture and must be stored and handled carefully to avoid compromising their performance.
Compatibility with Welding Equipment
Choosing consumables compatible with the welding equipment being used ensures consistent and efficient welding.
Welding Consumables for Different Welding Processes
MIG Welding
MIG welding consumables include solid wires and shielding gases that provide a stable arc and excellent weld bead appearance.
TIG Welding
TIG welding consumables, such as tungsten electrodes and filler rods, are used for precise and high-quality welds in various materials.
Stick Welding
Stick welding consumables, including coated electrodes, are versatile and suitable for a wide range of applications, making them a popular choice in many industries.
Industry Trends and Innovations
Advanced Coatings
Innovations in consumable coatings enhance the performance of welding materials, improving arc stability and reducing spatter.
Eco-Friendly Consumables
The industry is moving towards more sustainable options, with eco-friendly consumables that minimize environmental impact.
Digital Integration in Welding
Technological advancements are integrating digital tools into welding processes, enabling better monitoring and control of consumable usage.
Best Practices for Using Welding Consumables
Proper Storage
Store consumables in a dry and controlled environment to prevent degradation and ensure consistent performance.
Preheating Techniques
In certain applications, preheating the base material can enhance the effectiveness of welding consumables and reduce the risk of cracking.
Post-Weld Treatment
After welding, applying appropriate post-weld treatments can improve the strength and integrity of the weld joint.
Common Mistakes to Avoid
Using Incorrect Consumables
Choosing the wrong consumables can lead to weak welds and increased chances of weld defects.
Ignoring Manufacturer Recommendations
Manufacturers provide guidelines for using their consumables, and ignoring these recommendations can compromise weld quality.
Neglecting Safety Measures
Welding consumables emit fumes and require proper ventilation and safety equipment to protect welders from potential hazards.
Cost Considerations
Balancing Quality and Budget
While investing in high-quality consumables is important, it’s essential to find a balance that aligns with the project budget.
Long-Term Savings
Quality consumables may have a higher upfront cost but can lead to long-term savings by reducing the need for rework and repairs.
Environmental Impact
Recycling of Consumable Packaging
Many consumable manufacturers are focusing on recyclable packaging, reducing waste and promoting environmental responsibility.
Eco-Conscious Choices
Welders can make environmentally friendly choices by opting for consumables with minimal environmental impact.
Future of Welding Consumables
Advancements in Materials
Ongoing research is leading to the development of consumables with enhanced properties and performance.
Automation and Robotics
The integration of automation and robotics is reshaping the welding industry, with consumables playing a role in optimizing these processes.
Case Studies
Welding Consumables in Aerospace
Aerospace applications demand the highest standards of weld quality, making the choice of consumables critical for safety and performance.
Automotive Manufacturing Success
Successful automotive manufacturing relies on the use of appropriate consumables to ensure the durability of vehicle components.
FAQs
What are welding consumables?
Welding consumables are materials used during welding to enhance properties of welds and ensure joint integrity.
Why are welding consumables important?
Consumables determine weld quality and strength, impacting the success of welding projects.
How do I choose the right consumables for my project?
Consider base materials, welding technique, and manufacturer recommendations.
What are some benefits of quality welding consumables?
Quality consumables lead to improved weld integrity, reduced defects, and enhanced productivity.
What’s the future of welding consumables?
The future includes advanced materials, eco-friendly options, and integration with automation.
Conclusion
Welding consumables are the unsung heroes of the welding process, significantly influencing the quality and longevity of welded joints. By selecting the right consumables and following best practices, welders can create strong, reliable, and safe welds across various industries.