Welding Techniques for Copper and Copper Alloys
Introduction
Copper and its alloys are welded using various methods tailored to specific needs. Tungsten Inert Gas (TIG) welding ensures precision, making it ideal for thin copper sections, while Gas Metal Arc Welding (GMAW) or MIG welding is preferred for thicker components due to its higher deposition rates. Resistance spot welding is efficient for mass-producing copper sheet joints, applying localized heat and pressure. Laser welding and electron beam welding, with their high energy density, offer precision and efficiency in joining copper and its alloys. The choice of welding method depends on factors like material thickness and the desired properties of the final product, highlighting the versatility of these techniques in crafting reliable structures.
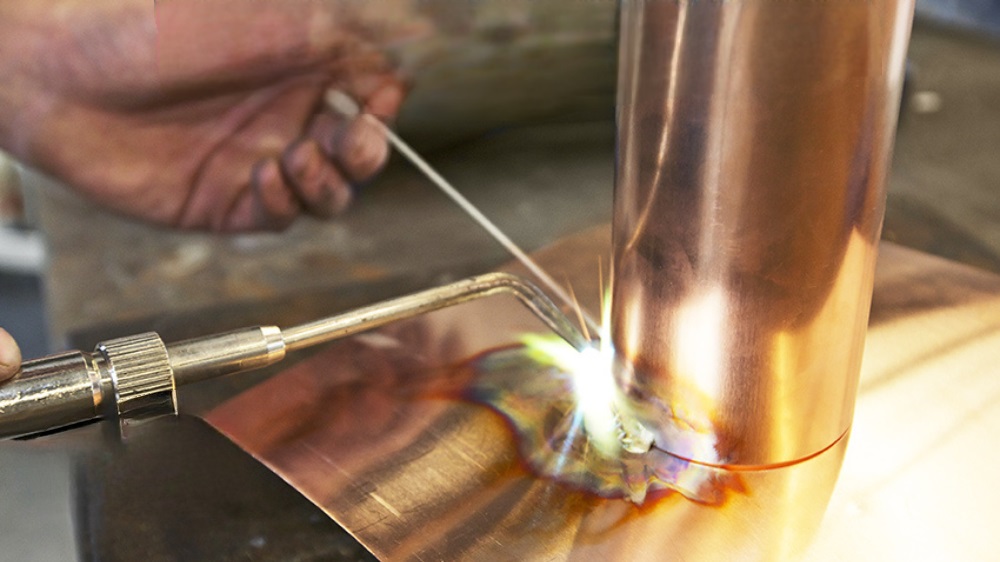
Properties of Copper and Copper Alloys
Copper, a versatile metal, and its alloys are prized for their unique combination of mechanical, electrical, and thermal properties. Understanding these properties is fundamental to successful welding processes, ensuring that the inherent characteristics of copper are leveraged effectively.
Overview of Copper and Its Alloys
Copper, in its pure form, exhibits exceptional conductivity, malleability, and corrosion resistance. However, in various industrial applications, copper is often alloyed with other elements to enhance specific properties. Common copper alloys include brass (copper and zinc), bronze (copper and tin), and cupronickel (copper and nickel).
These alloys are tailored to meet the requirements of diverse industries, providing solutions with varying hardness, strength, and corrosion resistance. The selection of a specific alloy depends on the intended application and the desired combination of properties.
Key Properties Affecting Welding Processes
Thermal Conductivity
One of the defining features of copper is its outstanding thermal conductivity. While this property is advantageous in many applications, it poses challenges during welding. The high thermal conductivity of copper leads to rapid heat dissipation, making it challenging to maintain a stable welding temperature.
Welders must carefully manage heat input and use appropriate welding techniques to prevent overheating and ensure proper fusion of the material. Employing welding processes with precise control, such as Gas Tungsten Arc Welding (GTAW), becomes crucial to manage the effects of high thermal conductivity.
Melting Point
Copper has a relatively high melting point, approximately 1,984 degrees Fahrenheit (1,085 degrees Celsius). This characteristic requires careful consideration during the welding process to prevent overheating and potential damage to the material. Welders must optimize parameters such as welding current, travel speed, and heat input to achieve a successful weld without compromising the structural integrity of the copper or its alloys.
Ductility
Ductility, or the ability of a material to deform without breaking, is another critical property of copper and its alloys. While this characteristic contributes to the ease of fabrication, it requires careful handling during welding to avoid issues such as distortion or cracking. Welding procedures must be designed to accommodate the ductility of copper, ensuring that the material retains its integrity and structural strength after the welding process is completed.
Common Welding Processes for Copper and Copper Alloys
Welding copper and its alloys demands precision and expertise due to their unique properties. Various welding processes are employed to achieve strong and reliable joints, each with its own set of advantages, limitations, and considerations.
Gas Tungsten Arc Welding (GTAW)
Explanation of the Process
Gas Tungsten Arc Welding (GTAW), commonly known as TIG welding, involves the use of a non-consumable tungsten electrode to produce the weld. A shielding gas, often argon, protects the weld pool from atmospheric contamination. GTAW is a precise and clean process suitable for welding thin sections and intricate joints.
Advantages and Limitations
Advantages:
- High precision and control over the welding process.
- Minimal spatter and clean welds.
- Suitable for welding non-ferrous metals like copper due to its non-consumable electrode.
Limitations:
- Slower welding speed compared to some other processes.
- Requires skilled operators for optimal results.
Applicability to Different Thicknesses and Joint Types
GTAW is particularly well-suited for thin materials and intricate joint configurations. Its ability to provide precise control makes it suitable for welding copper alloys with varying thicknesses, ensuring a high-quality and aesthetically pleasing weld.
Gas Metal Arc Welding (GMAW)
Overview of GMAW
Gas Metal Arc Welding (GMAW), or MIG welding, uses a consumable wire electrode fed through a welding gun. The electrode melts to form the weld pool, while a shielding gas protects the molten metal from atmospheric contamination. GMAW is known for its efficiency and versatility.
Specific Considerations for Copper and Copper Alloys
Considerations:
- Selection of appropriate filler wire is crucial.
- Shielding gas selection is vital to prevent oxidation of the copper.
- Proper wire feed and voltage settings to manage heat input.
Welding Parameters and Techniques
Adjusting welding parameters, such as wire feed speed, voltage, and shielding gas flow, is essential for achieving high-quality welds in copper and its alloys. GMAW provides a faster welding speed compared to GTAW, making it suitable for various joint types and thicknesses.
Resistance Welding
Description of Resistance Welding
Resistance welding involves passing an electric current through the materials to be joined, generating heat at the interface. The heat causes the materials to melt and fuse together when pressure is applied. This process is widely used for joining copper and copper alloys in specific applications.
Spot Welding and Seam Welding Applications
Spot Welding:
- Used for joining overlapping sheets or components.
- Common in the automotive and electronic industries.
Seam Welding:
- Continuous weld along the joint, suitable for long seams or cylindrical components.
- Applied in the manufacturing of pipes and containers.
Challenges and Solutions
Challenges:
- High thermal conductivity of copper requires precise control of welding parameters.
- Potential for electrode wear in resistance welding.
Solutions:
- Optimization of welding parameters to manage heat input.
- Regular maintenance of electrodes to ensure consistent performance.
Pre-welding Considerations
Efficient pre-welding preparations are critical for achieving successful welds, particularly when working with copper and copper alloys. This involves meticulous attention to surface preparation and thoughtful joint design to ensure optimal welding conditions and the integrity of the final weld.
Surface Preparation
Cleaning and Degreasing
Ensuring a clean and contaminant-free surface is paramount for successful welding. Copper and its alloys are susceptible to oxidation and contamination, which can negatively impact the quality of the weld. Therefore, thorough cleaning and degreasing of the welding surfaces are essential.
Cleaning Techniques:
- Use of solvents to remove oils, greases, and other contaminants.
- Mechanical methods like wire brushing or abrasive cleaning for oxide removal.
- Acid cleaning for specific applications, with careful consideration of material compatibility.
Surface Finish Requirements
The surface finish of the materials to be welded significantly influences the quality of the weld. Smooth and well-prepared surfaces promote better fusion and reduce the risk of defects.
Surface Finish Considerations:
- Removal of mill scale, oxides, and other impurities.
- Achieving a consistent surface profile for improved weld penetration.
- Selecting appropriate surface finishes based on the specific welding process and application requirements.
Joint Design
Butt, Fillet, and Lap Joint Considerations
The choice of joint design depends on the application, material thickness, and structural requirements. Understanding the characteristics of each joint type is crucial for achieving optimal weld quality.
Joint Types:
- Butt Joint:
- Suitable for welding two pieces of material in a straight-line configuration.
- Commonly used in structural applications where strength is a primary consideration.
- Fillet Joint:
- Involves the joining of two materials at an angle to form a triangular cross-section.
- Provides increased strength and is commonly used in T-joints and corner joints.
- Lap Joint:
- Overlapping of two materials, often with fillet welds at the edges.
- Common in sheet metal applications and provides good load distribution.
Bevel Angles and Root Openings
Optimizing bevel angles and root openings is crucial for achieving proper penetration and weld strength. These considerations are particularly important when welding thicker sections of copper and copper alloys.
Bevel Angles and Root Openings:
- Determining appropriate bevel angles based on material thickness and welding process.
- Ensuring proper root openings to allow for adequate filler material penetration.
- Implementing joint configurations that facilitate complete fusion and minimize the risk of defects like lack of fusion.
Welding Equipment and Consumables
Ensuring the right welding equipment and consumables are used is crucial for achieving successful and reliable welds, especially when working with copper and copper alloys. Each element, from the welding machine to the consumables, plays a pivotal role in the welding process.
Welding Machines Suitable for Copper
Selecting an appropriate welding machine is essential to accommodate the specific characteristics of copper and its alloys. Different welding processes require distinct types of welding machines.
Welding Processes and Machines:
- Gas Tungsten Arc Welding (GTAW):
- TIG welding machines are commonly used for their precise control and suitability for non-ferrous metals like copper.
- Machines should have advanced control features to manage the challenges posed by copper’s high thermal conductivity.
- Gas Metal Arc Welding (GMAW):
- MIG welding machines are suitable for copper welding.
- Machines with adjustable voltage settings and synergic controls are preferred for versatility.
- Resistance Welding:
- Resistance welding machines, such as spot welders or seam welders, are employed for specific applications.
- The machine should be capable of delivering the necessary current and pressure for effective welding.
Electrodes and Filler Materials
Choosing the right electrodes and filler materials is crucial for achieving proper fusion, minimizing defects, and ensuring the mechanical properties of the weld.
Electrodes and Fillers for Copper Welding:
- Gas Tungsten Arc Welding (GTAW):
- Use a non-consumable tungsten electrode, often containing thorium or cerium for enhanced performance.
- Filler materials should match the composition of the base metal for optimal results.
- Gas Metal Arc Welding (GMAW):
- Employ solid copper or copper alloy filler wires to match the base metal.
- Selection of appropriate wire diameter and composition based on the application and joint configuration.
- Resistance Welding:
- Electrodes should be made of materials with high electrical conductivity and resistance to wear, such as copper or copper alloys.
- Filler materials may not be used in resistance welding as the process relies on the heat generated by the electric current.
Shielding Gases for Copper Welding
Shielding gases play a crucial role in protecting the weld pool from atmospheric contamination, ensuring a clean and sound weld.
Shielding Gases for Copper Welding:
- Gas Tungsten Arc Welding (GTAW):
- Typically, pure argon or a helium-argon mix is used as a shielding gas.
- Selection depends on the welding conditions and desired penetration.
- Gas Metal Arc Welding (GMAW):
- Argon or a mixture of argon and helium is commonly used to shield the welding arc.
- The choice of shielding gas influences arc stability and metal transfer characteristics.
Challenges and Solutions
Welding copper and copper alloys presents specific challenges due to the unique properties of these materials. Addressing these challenges effectively is crucial for producing high-quality welds. Here, we explore three significant challenges and propose strategies for overcoming them.
Thermal Conductivity Challenges
Challenge:
Copper’s high thermal conductivity poses difficulties in maintaining a stable welding temperature. The rapid dissipation of heat can result in incomplete fusion and potential defects in the weld.
Solutions:
- Precise Heat Control:
- Utilize welding processes with precise heat control, such as Gas Tungsten Arc Welding (GTAW).
- Adjust welding parameters, such as current and travel speed, to manage heat input effectively.
- Preheating:
- Consider preheating the material to a specific temperature to counteract the effects of high thermal conductivity.
- Preheating helps maintain an optimal welding temperature throughout the process.
- Back Purging:
- Employ back purging with an inert gas to shield the backside of the weld from oxidation and control the cooling rate.
- This technique is particularly useful for preventing incomplete fusion in joints with limited access.
Oxidation and Contamination Issues
Challenge:
Copper is susceptible to oxidation, and the presence of oxides on the material surface can lead to weld defects and reduced mechanical properties.
Solutions:
- Effective Cleaning:
- Thoroughly clean and degrease the welding surfaces to remove oxides, oils, and other contaminants.
- Mechanical methods like wire brushing or abrasive cleaning can be employed for oxide removal.
- Use of Flux:
- Apply a suitable flux to the joint area to protect the molten metal from atmospheric contamination.
- Flux helps in preventing the formation of oxides and ensures a clean weld.
- Inert Gas Shielding:
- Employ inert gases, such as argon, during welding to create a shielding atmosphere that prevents oxidation.
- Proper selection and control of shielding gases are crucial for minimizing oxidation issues.
Strategies for Minimizing Heat Input
Challenge:
Excessive heat input during welding can lead to distortion, reduced mechanical properties, and even melting in thin sections.
Solutions:
- Optimize Welding Parameters:
- Adjust parameters like welding current, voltage, and travel speed to control heat input.
- Conduct test welds to determine the optimal settings for the specific copper alloy and joint configuration.
- Pulsed Welding:
- Consider using pulsed welding processes, which provide intermittent high and low currents.
- Pulsed welding helps control heat input, especially in applications with varying thicknesses.
- Heat Sinks:
- Use heat sinks or fixtures to absorb excess heat and minimize distortion.
- Proper fixturing helps distribute heat evenly and prevents localized overheating.
Applications and Industries
Welding of copper and copper alloys finds widespread application across various industries due to the unique properties of these materials. From electrical conductivity to corrosion resistance, copper’s versatility makes it a valuable choice in numerous sectors.
Overview of Industries Using Copper Welding
- Electronics and Electrical:
- Applications: Wiring, connectors, printed circuit boards.
- Importance: Copper’s excellent electrical conductivity makes it indispensable in the electronics industry.
- Construction:
- Applications: Roofing, plumbing, HVAC systems.
- Importance: Copper’s corrosion resistance and durability make it a preferred material in construction projects.
- Automotive:
- Applications: Radiators, heat exchangers, electrical components.
- Importance: Copper’s thermal conductivity and malleability are valuable in automotive applications.
- Aerospace:
- Applications: Heat exchangers, fuel systems, electrical components.
- Importance: Copper alloys contribute to lightweight yet robust components in aerospace engineering.
- Manufacturing:
- Applications: Precision instruments, machinery components.
- Importance: Copper’s machinability and formability are beneficial in manufacturing diverse products.
Specific Applications for Welded Copper Components
- Electrical Transformers:
- Applications: Copper windings in transformers.
- Importance: Efficient electrical conductivity and low resistivity contribute to the effectiveness of transformers.
- Heat Exchangers:
- Applications: Copper tubes for heat exchangers in HVAC systems.
- Importance: Copper’s high thermal conductivity enhances heat transfer efficiency.
- Plumbing Systems:
- Applications: Welded copper pipes for plumbing.
- Importance: Copper’s corrosion resistance ensures longevity and reliability in plumbing applications.
- Electronic Devices:
- Applications: Welded connections in electronic devices.
- Importance: Precision welding is crucial for the reliability of electronic components.
Case Studies Illustrating Successful Welding Techniques
- High-Speed Electronics Manufacturing:
- Application: Welding copper connectors in the production of high-speed electronics.
- Technique: Gas Tungsten Arc Welding (GTAW) with precise control to avoid overheating and ensure optimal conductivity.
- Aerospace Component Fabrication:
- Application: Welding copper alloys for aerospace components.
- Technique: Gas Metal Arc Welding (GMAW) with meticulous control of welding parameters for joint integrity.
- Efficient HVAC Systems:
- Application: Welding copper tubes for heat exchangers in HVAC systems.
- Technique: Gas Metal Arc Welding (GMAW) with proper shielding to prevent oxidation and ensure optimal heat transfer.
FAQs
Can I use the same welding technique for all types of copper alloys?
No, different alloys may require specific welding techniques tailored to their properties.
Is copper welding environmentally friendly?
Implementing sustainable practices, such as recycling, can enhance the environmental friendliness of copper welding.
What safety precautions should I take when welding copper?
Ensure you have proper protective gear, including helmets and gloves, and work in a well-ventilated area.
Are there any advancements in copper welding technology on the horizon?
Yes, ongoing advancements in technology may introduce new and improved welding techniques for copper in the future.
Can I weld copper without using a filler metal?
While possible in certain cases, using a suitable filler metal generally results in stronger and more durable welds.
Conclusion
In conclusion, mastering welding techniques for copper and copper alloys is essential for achieving robust and reliable joints. Whether you’re working on electrical projects, plumbing installations, or intricate constructions, understanding the properties of copper and employing the right welding methods ensures success.