Welding in Confined Spaces
Welding is an essential industrial process that joins materials using heat and pressure, but it becomes a significantly more challenging task when performed in confined spaces. Confined spaces, such as tanks, boat hulls, containers, or pipes, present unique safety hazards and require careful consideration of best practices to ensure the well-being of welders and the quality of the work.
In this comprehensive guide, we’ll explore the various aspects of welding in confined spaces, including the dangers involved, air quality and respiratory safety concerns, and the best practices that welders should follow to mitigate risks and work effectively. Whether you’re an experienced welder or someone new to the field, this article will provide valuable insights to keep you safe and productive in confined spaces.
Understanding the Dangers of Welding in Confined Spaces
Welding, by its nature, involves intense heat, sparks, and potentially hazardous fumes. When conducted in confined spaces, these dangers are magnified, and additional risks emerge. Here’s a closer look at the common hazards associated with welding in confined spaces:
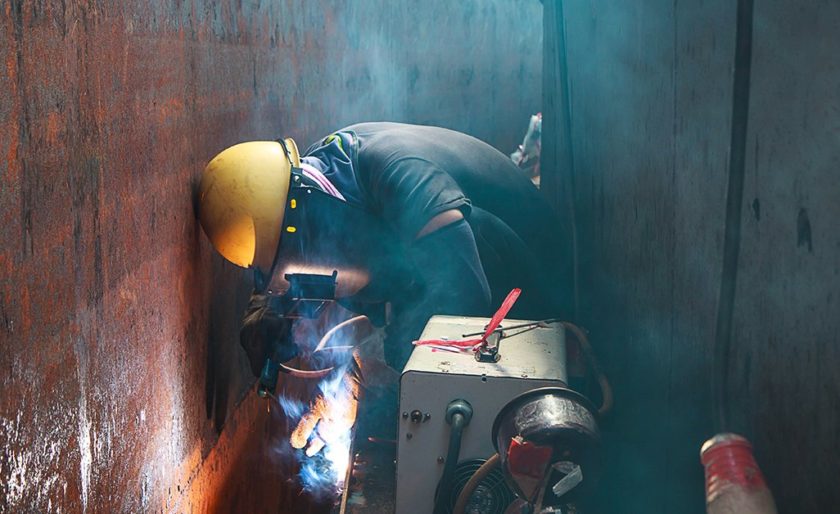
1. Increased Air Pollution
Confined spaces often lack sufficient natural ventilation. Welding in such an environment can lead to a rapid accumulation of welding fumes, gases, steam, and dust, which can result in dangerous levels of air pollution. This jeopardizes the respiratory health of welders and can have long-term consequences.
2. Fires and Explosions
The build-up of gases, steam, and dust within a confined space can create a combustible atmosphere. Welding activities, with their sparks and open flames, can ignite this mixture, leading to fires and explosions. It’s imperative to take precautions to prevent the accumulation of flammable substances.
3. Suffocation
Confined spaces may suffer from a shortage of oxygen due to poor ventilation. Welders working in such conditions are at risk of suffocation. It’s crucial to monitor and maintain appropriate oxygen levels in these spaces.
4. Additional Heat
In confined spaces, heat generated during welding can accumulate because there are limited outlets for heat dissipation. This can create an uncomfortable and potentially dangerous working environment.
5. Electrical Hazards
The use of electric lighting, tools, welding equipment, and other electrical devices in confined spaces can expose welders to excessive contact voltage. Proper insulation and labeling of power sources are vital to prevent electrical accidents.
6. Limited Space and Mobility
One of the significant challenges in confined spaces is the restricted room for movement. Welders may find themselves in uncomfortable positions for extended periods, which can lead to fatigue and increased injury risks.
Prioritizing Air Quality and Respiratory Safety
Air quality is a paramount concern when welding in confined spaces. The lack of natural ventilation makes it crucial to ensure that welders have access to healthy and breathable air throughout the work. Here are key considerations for maintaining air quality and respiratory safety in confined spaces:
1. Ventilation
In confined spaces, where natural ventilation is often lacking, mechanical ventilation becomes necessary. Ensure that the confined space is equipped with a ventilation system capable of maintaining an oxygen content of at least 19.5%. Regular monitoring of air quality is essential to detect any deviations.
2. Respiratory Equipment
Welders working in confined spaces should be equipped with appropriate respiratory safety gear. Given the likelihood of increased air pollution, a welding helmet with a powered air purifying respirator (PAPR) is recommended. PAPR units filter out 99.9% of dangerous fumes and particles, allowing welders to breathe more easily in areas with lower oxygen levels while also providing cooling.
3. Oxygen Supply
In spaces with low oxygen levels or none at all, provisions must be made for additional oxygen supply. PAPR units, though effective at filtering out contaminants, do not produce oxygen. Adequate oxygen levels must be maintained to support respiration.
4. Clean Air Access
Welders should have easy access to clean air during work. Properly fitted PAPRs, in conjunction with appropriate personal protective equipment (PPE), help ensure that welders are shielded from harmful particulates and maintain a consistent flow of clean air.
Best Practices for Welding in Confined Spaces
While welding in confined spaces poses significant challenges and risks, adherence to best practices can make the process safer and more efficient. Each confined space may present unique conditions, and additional safety precautions might be necessary. Here are the essential best practices to follow when welding in confined spaces:
1. Workspace Preparation
- Clear the confined space of any dangerous working materials and gases as much as possible.
- Identify and label electrical sources to prevent electrical hazards. Use insulating layers like rubber matting or wooden grating to enhance safety.
- Turn off gas emissions during breaks or when not in use to prevent the build-up of combustible gases.
2. Safety Approvals
- Obtain written approvals and safety precautions specific to the confined space. These should be followed rigorously.
3. Supervision
- Designate a dedicated supervisor responsible for ensuring that all defined safety measures are adhered to during the work.
4. Safety Posts
- Assign a reliable safety post, which maintains visual or voice contact, or signal lines with the welder. This individual should be trained in safety and rescue operations and seek help if any doubts or emergencies arise.
5. Exit Strategy
- Establish an exit strategy for emergencies, ensuring that precautions are taken for a quick evacuation from the confined space.
6. Clear Escape Routes
- Maintain clear and unobstructed escape routes to enable swift egress in case of unexpected situations.
7. Personal Protective Equipment (PPE)
- Ensure that all workers wear appropriate PPE, including gloves, clothing, footwear, respiratory gear, and other welding protection.
8. Welding Helmet Selection
- In confined spaces, consider using a welding helmet with a powered air purifying respirator (PAPR). This combination offers optimal protection against fumes and particles, allowing for easier breathing in low-oxygen environments while helping to regulate temperature.
Choosing the Right Equipment
When it comes to welding in confined spaces, having the right equipment can make a significant difference in safety and efficiency. One such recommended tool is the Tecmen 820 with Freflow Respirator, known for its slimline design, true color vision, and long-life respirator battery. Greg from Bladerunner boats highly recommends this equipment for confined space welding.
In conclusion, welding in confined spaces is a challenging endeavor that demands strict adherence to best practices and safety measures. By prioritizing air quality, respiratory safety, and the proper use of equipment, welders can mitigate the risks and work effectively in these challenging conditions. Whether you’re an experienced professional or new to confined space welding, always prioritize safety to ensure a successful and secure working environment.
Remember, the well-being of welders and the quality of the work should never be compromised, even in the most challenging of circumstances. Stay safe, and weld with confidence in confined spaces.
Training and Certification
In addition to following best practices and using the right equipment, it’s crucial for welders to receive proper training and certification, especially when working in confined spaces. Training should cover not only the technical aspects of welding but also the specific safety protocols for confined space work.
Welders should be knowledgeable about the unique risks associated with confined spaces and how to identify and mitigate potential hazards. In some industries, such as construction or shipbuilding, there may be specific certifications or licenses required for welding in confined spaces. These certifications often involve rigorous training and testing to ensure that welders are well-prepared for the challenges they may encounter.
Communication and Coordination
Clear communication is vital in confined space welding. As part of safety measures, it’s essential to maintain communication between the welder inside the confined space and those outside. This is typically achieved through visual or voice contact, signal lines, or communication devices.
Having a designated safety post or another worker responsible for this communication is crucial. The safety post’s primary role is to keep track of the welder’s status and provide assistance in case of emergencies. When working in a confined space, the ability to call for help or report any issues promptly can be a lifesaver.
Emergency Response Plan
Every confined space welding operation should have a well-defined emergency response plan in place. This plan should detail what actions to take in various emergency scenarios, including fires, explosions, medical emergencies, or equipment malfunctions.
The plan should include instructions on how to evacuate the confined space safely and swiftly, with designated meeting points and procedures for accounting for all personnel. Emergency response drills and simulations should be conducted regularly to ensure that all team members are well-prepared for potential emergencies.
Regular Inspections and Maintenance
Confined spaces often present unique challenges in terms of access and maintenance. Regular inspections of the confined space and its safety equipment are crucial to identify any potential issues. Ensure that safety equipment, such as respiratory gear and communication devices, is in good working order and up to date.
In addition, confined spaces may accumulate hazards over time due to changes in the environment or the materials stored within. Regular inspections and preventive maintenance can help to minimize these risks.
Continuous Improvement
Welding in confined spaces is a dynamic field with evolving safety standards and technologies. To stay at the forefront of safety, it’s essential for professionals and organizations to embrace continuous improvement. This involves staying informed about the latest safety regulations, equipment innovations, and best practices.
Collaborating with industry peers, attending safety seminars, and participating in safety audits can all contribute to creating a safer work environment for welders in confined spaces. By fostering a culture of continuous improvement, we can enhance safety while ensuring that the welding work is of the highest quality.
FAQs
Which type of ventilation is most effective for welding in confined space?
The most effective ventilation for welding in confined spaces is mechanical ventilation. This typically involves using exhaust fans and ducts to remove welding fumes and maintain a safe level of oxygen in the confined space.
How do you weld in tight spaces?
Welding in tight spaces requires careful planning, the right equipment, and adherence to safety practices. Essential steps include preparing the workspace, using appropriate personal protective equipment, and ensuring clear communication with a safety post or outside team.
What are the safe practices of welding?
Safe welding practices involve using proper protective gear, maintaining a clean and well-ventilated workspace, following established safety protocols, receiving adequate training, and regularly inspecting equipment for safety.
What are the general ventilation requirements for welding or cutting in a confined space?
General ventilation requirements for welding or cutting in confined spaces include ensuring sufficient oxygen levels (typically above 19.5%), using mechanical ventilation systems to remove fumes, and having a clear exit strategy in case of emergencies.
How do you prevent weld shrinkage?
To prevent weld shrinkage, it’s crucial to use proper welding techniques, avoid excessive heat input, and control the cooling rate of the weld. Preheating the base metal can also help reduce shrinkage.
How do you weld a hole closed?
Welding a hole closed involves properly preparing the hole’s edges, selecting the appropriate welding method (such as plug welding or seam welding), and using the right welding equipment and technique to create a strong and leak-free weld.
What is closure welding?
Closure welding refers to the process of sealing or closing a gap or seam in a metal structure by welding. It ensures the structural integrity and safety of the welded component.
How do you fix a hole in metal without welding?
If you need to fix a hole in metal without welding, you can use alternative methods such as brazing, soldering, or using epoxy adhesives to bond a patch over the hole. The choice of method depends on the type of metal and the specific application.
Why does my welder keep burning through metal?
If your welder keeps burning through metal, it may be due to excessive heat, incorrect welding settings, or inadequate welding techniques. Adjusting the settings, using the right type of electrode or filler metal, and practicing proper welding skills can help prevent burning through the metal.
Conclusion
Welding in confined spaces is a demanding and risky task that requires strict adherence to safety protocols. By understanding the unique dangers associated with this work, prioritizing air quality and respiratory safety, and following best practices, welders can mitigate the risks and maintain a safe and productive working environment.
Remember that proper training, clear communication, an emergency response plan, and regular inspections are all essential components of confined space welding safety. The continuous pursuit of improvement in safety measures and equipment is key to safeguarding the well-being of welders and the quality of their work.
In the end, success in confined space welding is about more than just the final weld. It’s about ensuring that welders return home safely after a day’s work and that the structures they create stand as a testament to their skill and dedication. Safe and successful confined space welding is the result of unwavering commitment to best practices and the highest safety standards.