Welding Joints and Their Types: A Comprehensive Guide
Table of Contents
ToggleIntroduction
Welding joints are the specific configurations in which two or more pieces of metal or other materials are arranged and then fused together using a welding process. These joints are the foundational elements of any welded structure, forming the connections between different components. The choice of welding joint determines how the materials will be connected and influences the overall strength, durability, and functionality of the final product. Welding joints are crucial in various industries, including construction, automotive, aerospace, and manufacturing, where strong and reliable connections are essential.
Importance of Choosing the Right Welding Joint for the Application:
Selecting the appropriate welding joint is a critical decision in any welding project. The type of joint used directly impacts the structural integrity, load-bearing capacity, and longevity of the welded assembly. Each welding joint has its own set of characteristics, strengths, and weaknesses, making it suitable for specific applications but potentially problematic for others.
For instance, a butt joint may be ideal for creating a seamless connection between two flat pieces of metal, but it might not be the best choice for joining materials that will undergo significant stress or bending. Conversely, a lap joint may provide the necessary strength for overlapping materials but could result in increased weight and material usage.
The correct joint selection ensures that the welded structure can withstand the operational stresses and environmental conditions it will encounter. It also helps in optimizing the welding process, reducing material wastage, and ensuring that the final product meets safety and performance standards.
Brief Mention of Different Welding Techniques Used with These Joints:
Various welding techniques are employed to create these joints, depending on the materials being welded, the desired strength of the joint, and the specific application. Some common welding techniques include:
- Shielded Metal Arc Welding (SMAW): Also known as stick welding, this technique is versatile and can be used for many types of joints, especially in construction and repair work.
- Gas Metal Arc Welding (GMAW/MIG): Often used for precision work, MIG welding is popular for joining thin materials and is widely used in automotive and manufacturing industries.
- Gas Tungsten Arc Welding (GTAW/TIG): TIG welding provides high-quality, precise welds and is often used for intricate joints or when welding dissimilar metals.
- Flux-Cored Arc Welding (FCAW): Similar to MIG welding, this technique is often used in heavy manufacturing due to its deep penetration and high deposition rate.
- Submerged Arc Welding (SAW): Ideal for joining thick materials, this technique is often used in shipbuilding and pipeline construction.
Each of these techniques can be applied to different types of welding joints, with the choice of technique depending on factors such as material thickness, joint configuration, and the desired strength of the weld.
Purpose of the Article
To Provide a Detailed Understanding of Various Welding Joints:
This article aims to demystify the various types of welding joints by providing a comprehensive overview of each. By understanding the characteristics, applications, advantages, and disadvantages of different welding joints, readers will gain a solid foundation in the essential elements of welding. This knowledge is crucial for anyone involved in welding, whether they are beginners or experienced professionals, as it enables them to make informed decisions about which joint to use in specific scenarios.
To Help Welders and Professionals Choose the Appropriate Joint for Their Projects:
Selecting the right welding joint is not always straightforward, as it involves considering numerous factors, such as material properties, load requirements, environmental conditions, and welding technique compatibility. This article serves as a practical guide to help welders and professionals navigate these choices with confidence.
By breaking down the complexities of welding joints and providing clear, actionable insights, the article aims to empower readers to make decisions that will enhance the quality, safety, and efficiency of their welding projects. Whether the goal is to create a simple structure or a complex, high-stress component, understanding the nuances of welding joints will lead to better outcomes and more successful projects.
Types of Welding Joints
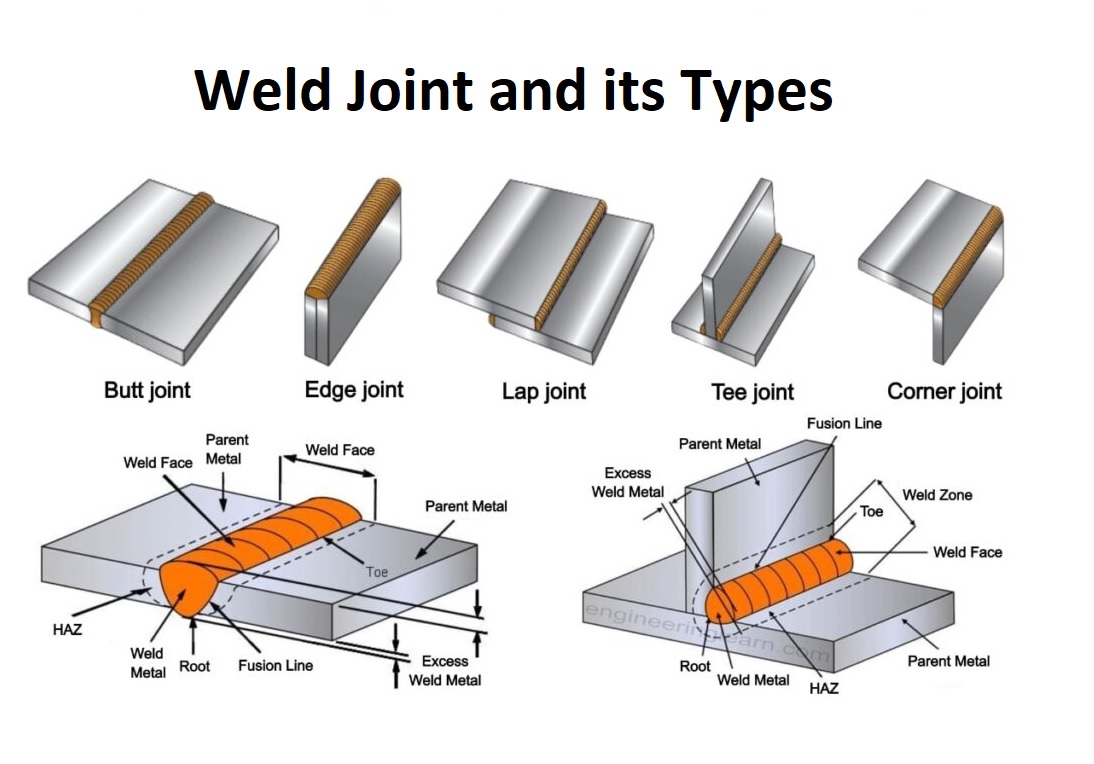
1. Butt Joint
Definition:
A butt joint is one of the simplest and most common types of welding joints. It is formed when two pieces of material, typically metal, are placed edge to edge and then welded together. The surfaces of the materials to be joined are usually parallel, and the weld is made along the seam where the edges meet. Butt joints are widely used in various industries due to their straightforward design and ease of execution.
Applications:
Butt joints are versatile and can be found in many applications, including:
- Pipelines: Butt joints are commonly used in the construction of pipelines, where sections of pipe are welded together end to end.
- Structural Frameworks: In construction, butt joints are often used to join beams and columns, forming the basic skeleton of a building.
- Frames and Enclosures: This joint is also used in fabricating frames and enclosures for machinery, vehicles, and other structures.
Advantages:
- Simplicity: The butt joint is easy to set up and execute, making it suitable for both beginners and experienced welders.
- Material Efficiency: Because the materials are joined edge to edge, there is minimal material waste, making this joint cost-effective.
- Strength: When properly executed, a butt joint can provide a strong and reliable connection, especially when reinforced with additional weld passes or backing strips.
Disadvantages:
- Edge Preparation: To achieve a strong weld, the edges of the materials must be properly prepared, which can require additional time and effort.
- Alignment: Precise alignment of the materials is crucial to ensure a strong and uniform weld. Misalignment can lead to weak spots or defects in the joint.
- Reinforcement: In some cases, especially with thicker materials, a butt joint may require reinforcement, such as a backing strip or multiple weld passes, to ensure adequate strength.
Variations:
- Square Butt Joint: The simplest form, where the edges of the materials are squared off and welded without any additional preparation.
- Single-Bevel Butt Joint: One of the edges is beveled, creating a V-shaped groove that allows for deeper penetration of the weld.
- Double-Bevel Butt Joint: Both edges are beveled, creating a wider groove and allowing for even greater weld penetration, typically used in thicker materials.
- Single-J Groove Butt Joint: One edge is prepared with a J-shaped groove, providing a combination of deep penetration and reduced weld volume.
- Double-J Groove Butt Joint: Both edges have J-shaped grooves, offering the same benefits as the single-J groove but with a wider area for welding.
2. Lap Joint
Definition:
A lap joint is created when two pieces of material are overlapped and then welded together along the edges of the overlap. This type of joint is commonly used when welding thin materials, such as sheet metal, where other joint configurations may not provide sufficient strength or stability.
Applications:
Lap joints are widely used in:
- Sheet Metal Work: This joint is ideal for joining thin sheets of metal, commonly found in the automotive and aerospace industries.
- Automotive Bodywork: Lap joints are frequently used in the assembly of car bodies, where large panels need to be securely joined.
- Fabrication of Thin Structures: When working with thin materials that cannot be edge-welded effectively, lap joints provide a strong and reliable connection.
Advantages:
- Strength: The overlapping nature of the joint provides increased strength, making it suitable for structures that need to withstand significant stress or load.
- Ease of Execution: Lap joints are relatively easy to set up and weld, even for beginners, and do not require extensive preparation.
- Tolerates Misalignment: Because the materials overlap, lap joints are more forgiving of slight misalignments, making them easier to execute in practice.
Disadvantages:
- Increased Material Usage: The overlap of the materials results in additional material usage, which can increase the weight and cost of the final product.
- Prone to Corrosion: The overlap creates a gap where moisture and contaminants can accumulate, leading to potential corrosion if not properly sealed or treated.
- Aesthetic Concerns: The overlap can result in a visible seam that may not be desirable in certain applications where appearance is important.
Variations:
- Single Lap Joint: The most basic form, where one piece of material overlaps another, and the weld is applied along the edges of the overlap.
- Double Lap Joint: In this variation, two pieces of material are sandwiched between a third piece, with welds applied to both overlapping edges. This provides additional strength and stability.
3. Corner Joint
Definition:
A corner joint is formed when two pieces of material are joined at an angle, typically 90 degrees, creating a corner. This type of joint is commonly used in the construction of frames, boxes, and other structures where two surfaces meet at a right angle.
Applications:
Corner joints are prevalent in:
- Frame Construction: Often used in building frames for structures, machinery, and enclosures, where components need to meet at right angles.
- Box and Case Fabrication: Corner joints are essential in the assembly of boxes, cases, and containers, where the edges of panels must be securely joined.
- Furniture Making: This joint is frequently used in the fabrication of metal and wooden furniture, providing strong and aesthetically pleasing connections.
Advantages:
- Strength: When properly executed, corner joints provide strong and stable connections, capable of withstanding significant stress.
- Versatility: Suitable for a wide range of materials and welding techniques, making it a versatile choice for many applications.
- Aesthetics: Corner joints can be visually appealing, especially when the welds are clean and smooth, making them suitable for applications where appearance matters.
Disadvantages:
- Alignment: Precise alignment is crucial for a strong corner joint, as any misalignment can weaken the connection and lead to defects.
- Difficulty in Tight Spaces: Welding in tight corners can be challenging, requiring skilled welders and specialized equipment to achieve quality results.
- Stress Concentration: The joint can be a point of stress concentration, particularly in load-bearing structures, which may require additional reinforcement.
Variations:
- Open Corner Joint: The edges of the materials are joined at a 90-degree angle, leaving the inside corner open. This is a common joint in light fabrication.
- Closed Corner Joint: The edges are butted together with no gap, forming a completely closed corner. This joint provides a smooth, finished appearance and is often used in furniture and enclosures.
- Half-Open Corner Joint: A variation where one piece of material is recessed or notched to fit into the other, creating a stronger and more stable joint.
4. Tee Joint
Definition:
A tee joint is formed when one piece of material is positioned perpendicular to another, resembling the shape of the letter “T.” The vertical piece, known as the web, is joined to the horizontal piece, known as the flange. This type of joint is commonly used in structural frameworks and reinforcement where two parts need to be connected at a right angle but are not aligned on the same plane.
Applications:
Tee joints are commonly used in:
- Structural Frameworks: Tee joints are essential in constructing frameworks for buildings, bridges, and other structures where strong, load-bearing connections are needed.
- Reinforcement: These joints are often used to reinforce beams, columns, and other components, providing additional support at critical points.
- Machinery and Equipment: In the assembly of machinery and equipment, tee joints are used to connect components such as brackets, supports, and gussets to the main structure.
Advantages:
- Strong Load-Bearing Capacity: Tee joints provide robust connections that can withstand significant stress, making them ideal for structural applications.
- Versatility: Tee joints can be used with various welding techniques and materials, offering flexibility in design and execution.
- Ease of Fabrication: Although alignment is crucial, tee joints are relatively straightforward to set up and weld, even in large-scale projects.
Disadvantages:
- Stress Concentration: The intersection of the web and flange can be a point of high stress, requiring careful weld design and execution to avoid cracks or failures.
- Potential for Warping: Due to the perpendicular arrangement, tee joints are susceptible to warping during welding, especially if the materials are thin or the weld is improperly balanced.
- Skilled Welding Required: Achieving a strong and defect-free weld in a tee joint often requires a skilled welder, particularly when dealing with thick materials or complex geometries.
Variations:
- Fillet Welded Tee Joint: The most common type, where a fillet weld is applied along the intersection of the web and flange. This variation provides a strong and straightforward connection.
- Bevel Groove Tee Joint: In cases where thicker materials are used, the edge of the web may be beveled to create a groove for the weld. This allows for deeper penetration and a stronger joint, suitable for heavy-duty applications.
5. Edge Joint
Definition:
An edge joint is formed when the edges of two pieces of material are placed side by side and welded along the same edge. This joint is typically used when the materials are too thin to be butt-welded or when additional support along the edge is required. Edge joints are common in sheet metal fabrication and are often used for joining thin plates or sheets in applications where the joint will not be subjected to heavy loads.
Applications:
Edge joints are frequently used in:
- Sheet Metal Fabrication: Ideal for joining thin sheets of metal in applications such as ductwork, enclosures, and panels.
- Fabrication of Tanks and Containers: Used in the assembly of tanks, containers, and other vessels where a continuous, leak-proof edge is required.
- Automotive and Aerospace Industries: Employed in situations where thin materials need to be joined without increasing the overall thickness or weight of the assembly.
Advantages:
- Minimal Material Preparation: Edge joints require little to no preparation, making them quick and easy to execute, particularly in high-volume production settings.
- Suitable for Thin Materials: This joint is ideal for thin materials that might otherwise be difficult to weld using other joint configurations.
- Continuous Weld Seam: The edge joint allows for a continuous weld seam, which can be beneficial in applications where a leak-proof or airtight seal is required.
Disadvantages:
- Limited Strength: Edge joints are not as strong as other joint types, making them unsuitable for applications where the joint will be subjected to significant stress or load.
- Precision Required: Proper alignment of the edges is crucial to achieving a strong weld, requiring careful setup and execution.
- Potential for Distortion: Thin materials are prone to distortion during welding, especially if the heat input is not carefully controlled.
Variations:
- Single Edge Joint: The simplest form, where two pieces of material are placed side by side and welded along one edge.
- Double Edge Joint: In this variation, the edges of both materials are beveled or grooved, allowing for a deeper weld penetration. This is often used when additional strength or sealing is required.
6. Plug/Slot Joint
Definition:
A plug or slot joint is created when one piece of material has a hole or slot cut into it, and a weld is made by filling this hole or slot with weld metal to join it to another piece beneath it. This type of joint is commonly used to join overlapping pieces of metal where access to the edges is limited or where a strong, localized weld is needed.
Applications:
Plug and slot joints are commonly found in:
- Automotive Industry: Used in bodywork and chassis assembly, particularly where panels overlap and need to be securely joined without visible welds.
- Aerospace Industry: Employed in aircraft manufacturing to join thin materials while maintaining aerodynamic smoothness.
- Fabrication of Sheet Metal Structures: Used in the assembly of cabinets, enclosures, and other sheet metal structures where overlapping joints are common.
Advantages:
- High Strength: By filling the hole or slot with weld metal, a strong and durable connection is created, capable of withstanding significant stress.
- Localized Weld: The weld is confined to a small area, minimizing heat distortion and preserving the integrity of the surrounding material.
- Aesthetic Appearance: Plug and slot welds are often hidden from view, providing a clean and smooth surface that is visually appealing.
Disadvantages:
- Precision Required: Accurate hole or slot preparation is essential for achieving a strong weld, requiring careful setup and execution.
- Time-Consuming: Preparing the holes or slots and executing the weld can be time-consuming, particularly in large-scale or high-volume production.
- Limited Access: This joint type requires access to only one side of the materials, which can be a limitation in some applications.
Variations:
- Circular Plug Weld: The most common form, where a circular hole is cut into one piece of material and filled with weld metal.
- Elongated Slot Weld: A variation where an elongated slot is cut into the material, allowing for a longer weld and increased strength. This is often used in applications where a larger contact area is needed.
7. Edge-Flange and Corner-Flange Joint
Definition:
An edge-flange joint is created when the edge of one piece of material is bent to form a flange, which is then welded to another piece of material. Similarly, a corner-flange joint involves bending the edge of a material to form a flange and welding it to another piece at a corner. These joints are commonly used in the automotive and HVAC industries, where complex shapes and lightweight structures are required.
Applications:
Edge-flange and corner-flange joints are commonly used in:
- Automotive Industry: These joints are widely used in car body panels, doors, and other components where lightweight yet strong connections are needed.
- HVAC Systems: Flange joints are used in ductwork and ventilation systems, providing secure connections with minimal air leakage.
- Appliance Manufacturing: Employed in the assembly of household appliances such as refrigerators, washing machines, and ovens, where metal panels are joined together.
Advantages:
- Strong Joint: The flange provides additional surface area for welding, resulting in a strong and secure connection.
- Efficient Use of Material: Flange joints allow for the use of thinner materials without sacrificing strength, reducing weight and material costs.
- Suitable for Complex Shapes: These joints are ideal for applications where materials need to be bent or shaped to fit a specific design.
Disadvantages:
- Precision Bending Required: The flange must be precisely bent to ensure a proper fit and strong weld, requiring specialized equipment and skilled workers.
- Potential for Distortion: The bending and welding processes can cause distortion, particularly in thin materials, which may require additional correction.
- Limited Flexibility: Once the flange is formed and welded, the joint offers little flexibility, making it difficult to adjust or modify the connection.
Variations:
- Flanged Corner Joint: The edge of one piece is bent to form a flange and welded to another piece at a corner, providing a strong and stable joint.
- Flanged Edge Joint: Similar to the corner-flange joint, but the flange is welded along the edge of the other piece, often used in the assembly of frames and enclosures.
8. Scarf Joint
Definition:
A scarf joint is created by beveling or tapering the edges of two pieces of material and then welding them together. The bevel or taper allows for a larger surface area to be welded, resulting in a strong and smooth connection. Scarf joints are commonly used in applications where the joined materials need to appear continuous or where high-strength connections are required.
Applications:
Scarf joints are used in:
- Pipeline Construction: Scarf joints are employed in pipeline welding, where long sections of pipe need to be joined with minimal disruption to the flow of fluids.
- Railway Tracks: This joint is used in welding railway tracks, providing a smooth, continuous surface for trains to travel on.
- Structural Steelwork: In the construction of large steel structures, scarf joints are used to join beams and columns, ensuring strong and seamless connections.
Advantages:
- Smooth, Continuous Surface: The beveled or tapered edges create a joint that is flush with the surrounding material, providing a smooth, continuous surface.
- High Strength: The increased surface area of the joint allows for a stronger weld, making scarf joints suitable for load-bearing applications.
- Minimized Stress Concentration: The gradual taper of the joint helps to distribute stress evenly, reducing the likelihood of cracks or failures.
Disadvantages:
- Complex Preparation: The beveling or tapering of the edges requires precise preparation, which can be time-consuming and requires specialized equipment.
- Skilled Welding Required: Achieving a strong and defect-free scarf joint often requires a skilled welder, particularly when dealing with thick materials or complex geometries.
- Limited Flexibility: Once welded, the joint offers little flexibility, making it difficult to adjust or modify the connection.
Variations:
- Single Scarf Joint: A simple bevel or taper is applied to one edge of each piece of material, creating a joint with a larger surface area for welding.
- Double Scarf Joint: Both edges of the material are beveled or tapered, creating a joint with an even larger surface area for welding. This variation is often used in heavy-duty applications where maximum strength is required.
Conclusion
Welding joints are a fundamental aspect of the welding process, and understanding the different types of joints is crucial for achieving strong, reliable, and durable welds. Each type of joint offers unique advantages and disadvantages, making it important for welders and professionals to select the appropriate joint for their specific application.
By considering factors such as material thickness, load-bearing requirements, and the intended use of the welded structure, welders can make informed decisions that ensure the success and longevity of their projects. Whether working on pipelines, structural frameworks, automotive bodywork, or any other welding project, a deep understanding of welding joints is essential for producing high-quality results.
This article has provided a detailed overview of the most common types of welding joints, including butt, lap, corner, tee, edge, plug/slot, edge-flange, and scarf joints. By exploring the definitions, applications, advantages, disadvantages, and variations of each joint, readers can gain valuable insights into the best practices for welding and joint selection.
For welders, professionals, and enthusiasts alike, mastering the different types of welding joints is a key step towards becoming a skilled and successful welder. With this knowledge, you can approach your projects with confidence, knowing that you have the expertise to choose the right joint for every situation.