Welding of Dissimilar Metals Challenges and Solutions
When it comes to welding, the process of joining two or more metal pieces together, working with similar metals is relatively straightforward. However, the real challenge arises when you have to weld dissimilar metals. Dissimilar metal welding involves joining two or more metals with significantly different physical, chemical, and metallurgical properties. This process is vital for creating structures and components that capitalize on the unique characteristics of each metal. The significance lies in the ability to combine materials with complementary attributes, such as strength, corrosion resistance, conductivity, and more, to achieve enhanced overall performance.
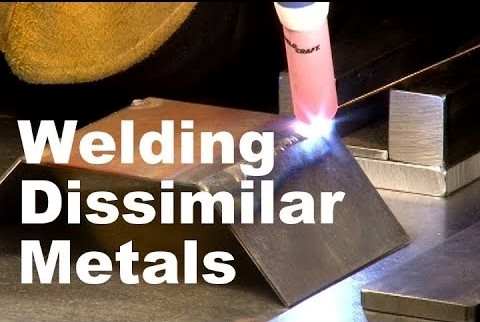
Challenges in Welding Dissimilar Metals
Metallurgical Incompatibility
- Differences in Melting Points, Thermal Expansion, and Conductivity: Dissimilar metals often have distinct melting points, thermal expansion coefficients, and thermal conductivities. During welding, these disparities can lead to uneven heating and cooling rates, causing thermal stresses and potential cracking at the joint interface.
- Formation of Brittle Intermetallic Compounds: When dissimilar metals are welded, intermetallic compounds may form at the interface due to diffusion processes. These compounds can be brittle and weak, compromising the overall strength and ductility of the joint. They can also increase susceptibility to cracking during service.
Mechanical Incompatibility
- Mismatch in Mechanical Properties: Dissimilar metals often possess varying mechanical properties such as yield strength, ductility, and hardness. Joining materials with drastically different properties can result in stress concentrations and uneven load distribution, potentially leading to premature failure.
- Risk of Residual Stresses and Distortion: During welding, rapid heating and cooling cycles can induce residual stresses within the joint. The mismatched properties of dissimilar metals exacerbate this issue, leading to distortion, warping, and even crack initiation in the welded structure.
Corrosion Compatibility
- Galvanic Corrosion Due to Electrochemical Potential Differences: When dissimilar metals are exposed to an electrolyte (e.g., moisture), galvanic corrosion can occur due to the electrochemical potential difference between the metals. This leads to accelerated corrosion at the interface, compromising the joint’s integrity and long-term durability.
- Risk of Accelerated Corrosion at the Interface: The formation of intermetallic compounds and microstructural changes at the joint interface can create preferential sites for corrosion initiation and propagation. This localized corrosion weakens the joint and reduces its lifespan.
Thermal Gradient Challenges
- Differential Cooling Rates Leading to Cracking and Distortion: Dissimilar metals have varying thermal conductivities, which can cause one metal to cool faster than the other during welding. This differential cooling can result in thermal stresses, cracking, and distortion in the welded joint.
- Management of Heat Input and Dissipation: Proper control of heat input is critical to avoid excessive thermal gradients. The challenge lies in achieving a balance between ensuring a sound weld and preventing overheating or excessive distortion due to excessive heat input.
Solutions to Dissimilar Metal Welding Challenges
Material Selection
- Matching Compatible Materials with Similar Properties: Careful selection of dissimilar metals with comparable physical and mechanical properties can reduce the challenges associated with differences in thermal expansion, conductivity, and mechanical behavior. This minimizes the risk of stress concentration and cracking.
- Use of Transition Materials to Mitigate Differences: In cases where direct welding of dissimilar metals isn’t feasible, using transition materials with intermediate properties can help create a gradual transition between the dissimilar metals. This aids in reducing abrupt changes in properties and potential failure points.
Pre-Welding Preparations
- Surface Preparation and Cleaning: Proper cleaning of the joint surfaces before welding is crucial to prevent contamination and improve bonding. Clean surfaces promote better metallurgical bonding and reduce the formation of weak spots.
- Use of Intermediate Layers or Interlayers to Improve Bonding: Interlayers of compatible materials can be introduced between the dissimilar metals. These layers serve as diffusion barriers, reducing the formation of brittle intermetallic compounds and enhancing joint integrity.
Process Selection
- Choice of Welding Techniques: Different welding techniques can be employed based on the specific requirements and challenges of the dissimilar metals. Fusion welding, solid-state welding (such as friction stir welding), and hybrid techniques (combining fusion and solid-state methods) offer different benefits and drawbacks.
- Proper Parameter Control to Balance Heat Input and Minimize Distortion: Precise control of welding parameters, such as heat input, travel speed, and filler material, helps manage thermal gradients. Balancing heat input minimizes distortion while maintaining adequate joint strength.
Post-Weld Heat Treatment
- Annealing, Stress-Relieving, and Tempering: Heat treatment processes can help relieve residual stresses and improve the joint’s mechanical properties. Annealing and tempering can refine microstructures and reduce the risk of cracking and distortion.
- Controlled Cooling to Prevent Cracking and Improve Microstructure: Gradual and controlled cooling rates after welding can prevent the formation of brittle phases and intermetallic compounds. This ensures a more favorable microstructure for mechanical strength.
Joint Design
- Tapered or Stepped Joints to Manage Thermal Gradients: Designing joints with gradual transitions can help mitigate thermal gradients by distributing heat more evenly. Tapered or stepped joints reduce the abrupt changes in material thickness.
- Use of Mechanical Fasteners or Adhesives in Conjunction with Welding: In cases where welding alone may not provide the desired joint integrity, mechanical fasteners or adhesives can be used in conjunction with welding to distribute loads and enhance overall joint strength.
Examples of Successful Dissimilar Metal Welding
Aerospace Industry
- Titanium to Aluminum Welding: In aerospace applications, joining titanium alloys with aluminum alloys is essential for lightweight structures with high strength. Advanced techniques like electron beam welding and laser welding have been successfully employed to create reliable joints by carefully managing heat input and minimizing intermetallic formation.
- Stainless Steel to Inconel Welding: Aerospace components often require the joining of stainless steel and Inconel, a superalloy known for high-temperature performance. Welding processes like gas tungsten arc welding (GTAW) with precise parameter control have been used to prevent cracking and ensure joint integrity.
Automotive Industry
- Aluminum to Steel Welding: The automotive sector frequently uses aluminum for weight reduction and steel for structural strength. Techniques like friction stir welding and laser welding have enabled successful joining of these dissimilar materials, maintaining structural integrity and crashworthiness.
- Magnesium to Steel Welding: Magnesium offers significant weight reduction potential in automotive components. Hybrid welding methods, such as laser-assisted arc welding, have been employed to create strong and reliable joints between magnesium and steel while managing heat input.
Oil and Gas Industry
- Duplex Stainless Steel Welding: The oil and gas industry often requires welding duplex stainless steels that combine austenitic and ferritic microstructures. Careful control of heat input and post-weld heat treatment is critical to avoid embrittlement and intermetallic phase formation.
- Inconel to Carbon Steel Welding: Joining Inconel, renowned for its corrosion resistance, with carbon steel used in structural components poses challenges. Welding techniques such as shielded metal arc welding (SMAW) and controlled preheat help prevent cracking and maintain the mechanical and corrosion properties of both materials.
Future Trends and Advancements
Emerging Welding Techniques
- Friction Stir Welding: This solid-state welding technique continues to evolve, offering advantages in joining dissimilar metals with minimal heat input. Its ability to create strong joints in challenging combinations makes it promising for various industries.
- Laser Welding: Advances in laser technology allow for more precise control over heat input and narrower heat-affected zones. This is particularly valuable for dissimilar metal welding, where controlling thermal gradients is crucial.
- Explosive Welding: This unconventional technique involves high-velocity impact to join metals. As it doesn’t involve melting, it’s suitable for materials with significantly different melting points and avoids issues like intermetallic formation.
Advancements in Materials Science
- Nanostructured Materials: Nanoengineering of materials can provide enhanced properties and compatibility, reducing the challenges associated with dissimilar metal welding. Nanocomposites and nanocoatings can improve mechanical strength, corrosion resistance, and thermal stability.
- Coatings: Developments in coatings can facilitate dissimilar metal welding by acting as diffusion barriers or stress-relief layers. These coatings can prevent the formation of brittle intermetallic compounds and improve joint quality.
Simulation and Modeling for Predicting Weld Performance
- Finite Element Analysis (FEA): Advanced simulation tools can predict temperature distribution, stress profiles, and distortion during dissimilar metal welding. This aids in optimizing welding parameters and joint design to achieve desired outcomes.
- Multi-Scale Modeling: Modeling techniques that encompass microscale and macroscale phenomena help understand the intricate interactions at different levels, leading to more accurate predictions of joint behavior.
Automation and Robotics in Dissimilar Metal Welding Processes
- Robotic Welding: Automation using robots equipped with advanced sensors and precision control enhances the consistency and accuracy of dissimilar metal welding. This is especially useful for large-scale production with complex geometries.
- Collaborative Robots (Cobots): Cobots can work alongside human operators to perform delicate welding tasks, ensuring the precision required for dissimilar metal joints while maintaining safety.
FAQs
What are the challenges of dissimilar welding?
Welding two metals with distinct compositions and properties, known as dissimilar welding, poses several challenges. One of the primary obstacles is the difference in melting points and thermal conductivities of the metals. When subjected to welding temperatures, these dissimilar metals can react differently, leading to cracks, weak joints, or even metallurgical incompatibilities.
What are the difficulties in welding dissimilar metals?
Welding dissimilar metals is fraught with difficulties, largely stemming from their diverse characteristics. Mismatched thermal expansion coefficients between the metals can result in residual stresses, distortion, and potential failure of the weld. Additionally, selecting an appropriate filler material that can bridge the gap between the dissimilar metals while ensuring compatibility can be a complex task.
What is the welding method for dissimilar metals?
To address the challenges of dissimilar metal welding, several advanced welding methods have emerged. Friction stir welding and laser beam welding are notable examples. Friction stir welding involves a rotating tool that generates heat and pressure to forge the metals together, reducing the heat-affected zone and minimizing defects. Laser beam welding utilizes a concentrated laser beam to achieve high precision and minimize thermal distortion.
Why is dissimilar metal welding important?
Dissimilar metal welding holds great significance in various industries. It enables the creation of composite structures that leverage the unique properties of different metals. For instance, combining aluminum and steel in the automotive industry results in lighter yet strong vehicle components. This technique also facilitates repairs and modifications in applications where metals with different properties are already in use.
What is the most challenging part of welding?
One of the most challenging aspects of welding, regardless of metal types, is achieving proper joint strength and integrity. Welding involves the localized melting and solidification of metals, which can introduce defects like cracks, porosity, and incomplete fusion. Maintaining consistent heat input, suitable welding parameters, and proper filler material selection are critical to producing sound welds.
What are the limitations of the welding process?
The welding process has its limitations, which become especially pronounced in dissimilar metal welding. The thermal stresses generated during welding can cause distortion, affecting the dimensional accuracy of the welded components. Additionally, the heat-affected zone (HAZ) adjacent to the weld may experience altered mechanical properties, reducing the overall strength of the joint. Proper post-weld heat treatment and careful material selection are necessary to mitigate these limitations.
Conclusion
In the realm of welding, tackling the challenges of dissimilar metal welding requires a combination of knowledge, expertise, and careful execution. While the differences in physical and chemical properties might seem daunting, they can be overcome through proper material selection, advanced welding techniques, and meticulous attention to welding parameters. By addressing the challenges head-on and employing suitable solutions, welders can achieve reliable and durable joints even when dealing with dissimilar metals.
For further insights into the intricacies of dissimilar metal welding, check out resources such as the American Welding Society’s publications and industry-specific research papers. These sources provide valuable information to assist welding students and professionals in mastering the art of joining dissimilar metals with confidence.