Welding of Nickel and Nickel Alloys
Introduction
Nickel and nickel alloys are widely used in various industries due to their exceptional properties, including corrosion resistance, high-temperature strength, and ductility. Welding of Nickel and Nickel Alloys materials requires careful consideration of their unique characteristics and the selection of appropriate welding processes and techniques.
Welding is a crucial fabrication process in industries where nickel and nickel alloys are utilized. Whether it’s for chemical processing equipment, aerospace components, or electrical applications, welding plays a significant role in joining these materials to create complex structures and parts.
Properties of Nickel and Nickel Alloys
Nickel and its alloys exhibit a diverse range of properties that make them highly valuable in numerous industrial applications. Understanding these properties is essential for effectively utilizing these materials in various engineering and manufacturing processes.
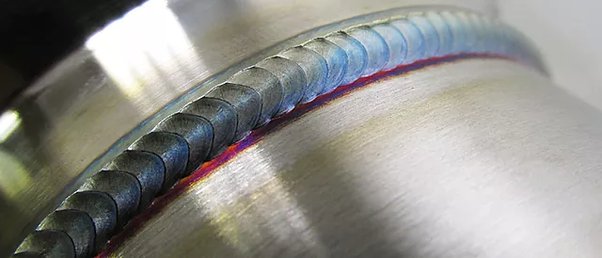
Chemical Properties
Nickel, with its atomic number 28 and chemical symbol Ni, belongs to the transition metal group in the periodic table. It possesses excellent chemical stability, displaying resistance to corrosion and oxidation in various environments. Nickel’s inherent chemical properties make it suitable for applications where exposure to corrosive substances or extreme conditions is common.
Nickel alloys, which are composed of nickel along with other elements such as chromium, molybdenum, and iron, inherit these chemical properties while also incorporating additional features tailored to specific applications. For example, the addition of chromium enhances the corrosion resistance of nickel alloys, making them suitable for use in aggressive chemical environments.
Mechanical Properties
Nickel and nickel alloys exhibit remarkable mechanical properties, including high strength, toughness, and ductility. These materials possess excellent tensile strength and fatigue resistance, allowing them to withstand high mechanical loads and cyclic stresses without experiencing failure.
Moreover, nickel alloys can maintain their mechanical properties over a wide range of temperatures, from cryogenic conditions to elevated temperatures exceeding 1000°C (1832°F). This exceptional temperature stability makes nickel alloys particularly well-suited for applications in aerospace, power generation, and chemical processing, where exposure to extreme temperatures is common.
Thermal Properties
In addition to their impressive mechanical properties, nickel and nickel alloys display excellent thermal conductivity and thermal expansion characteristics. These materials conduct heat efficiently, making them suitable for applications where heat dissipation or thermal management is critical.
Nickel-based superalloys, renowned for their high-temperature strength and creep resistance, are extensively used in gas turbine engines for aerospace propulsion and power generation. Their exceptional thermal properties enable these alloys to withstand the extreme temperatures and thermal cycling conditions encountered in such demanding applications.
Corrosion Resistance
One of the most notable properties of nickel and nickel alloys is their exceptional corrosion resistance. Nickel exhibits inherent resistance to corrosion in various environments, including acidic, alkaline, and saline conditions. This resistance is further enhanced in nickel alloys through the addition of alloying elements such as chromium, molybdenum, and copper.
Nickel-based alloys, such as Inconel and Hastelloy, are widely utilized in chemical processing, marine engineering, and oil and gas industries due to their superior corrosion resistance. These alloys offer unparalleled protection against pitting, crevice corrosion, and stress corrosion cracking, ensuring the longevity and reliability of critical components in harsh operating environments.
Types of Nickel and Nickel Alloys
Nickel and its alloys encompass a diverse range of compositions and properties, each tailored to specific applications and industries. Understanding the various types of nickel and nickel alloys is crucial for selecting the most suitable material for a given application.
Pure Nickel
Pure nickel, also known as nickel 200 or nickel 201, consists primarily of nickel with minimal alloying elements. It exhibits excellent corrosion resistance in a wide range of environments, including acidic and alkaline solutions. Pure nickel is particularly valued for its high electrical and thermal conductivity, making it ideal for electrical and electronic applications, as well as in the manufacturing of chemical processing equipment.
Nickel-Copper Alloys
Nickel-copper alloys, commonly referred to as Monel alloys, contain nickel as the predominant element along with a significant proportion of copper. These alloys exhibit exceptional corrosion resistance, particularly in marine and chemical environments. Monel alloys are renowned for their resistance to seawater corrosion and erosion, making them suitable for marine engineering, offshore oil platforms, and chemical processing equipment.
Nickel-Chromium Alloys
Nickel-chromium alloys, also known as Nichrome alloys, are composed of nickel and chromium as the primary constituents, with small additions of other elements such as iron and silicon. These alloys offer excellent high-temperature strength and oxidation resistance, making them ideal for applications in heating elements, electric furnaces, and thermocouples. Nichrome alloys are extensively utilized in the aerospace, automotive, and electrical industries for their superior performance at elevated temperatures.
Nickel-Molybdenum Alloys
Nickel-molybdenum alloys, such as Hastelloy alloys, combine nickel with molybdenum and other elements to impart exceptional corrosion resistance in highly corrosive environments. These alloys exhibit resistance to a wide range of corrosive substances, including acids, chlorides, and oxidizing agents. Hastelloy alloys find widespread use in chemical processing, pharmaceutical manufacturing, and pollution control equipment due to their superior resistance to corrosion and chemical attack.
Nickel-Iron Alloys
Nickel-iron alloys, such as Invar and Kovar, consist of nickel with varying proportions of iron. These alloys exhibit low coefficients of thermal expansion, making them suitable for applications requiring dimensional stability over a wide temperature range. Invar alloys, for example, are utilized in precision instruments, optical devices, and aerospace components where minimal dimensional changes with temperature fluctuations are critical.
Welding Techniques and Procedures
Achieving successful welds in nickel and nickel alloy applications requires careful consideration of welding techniques and procedures. Various factors, including equipment setup, welding parameters, shielding gases, filler metal selection, welding positions, and heat input control, contribute to the quality and integrity of the welded joint.
Setup and Equipment
Proper setup and selection of welding equipment are essential for ensuring the efficiency and effectiveness of the welding process. This includes choosing the appropriate welding machine, power source, welding torch or gun, and accessories such as welding clamps and fixtures. Additionally, ensuring the equipment is calibrated and maintained in good working condition is crucial for consistent and reliable weld performance.
Welding Parameters
Optimizing welding parameters, such as voltage, current, welding speed, and travel angle, is essential for achieving the desired weld bead geometry, penetration, and fusion. These parameters may vary depending on factors such as material thickness, joint configuration, and welding position. Fine-tuning welding parameters through experimentation and process qualification helps optimize weld quality and productivity.
Shielding Gases
Selecting the appropriate shielding gas is critical for protecting the weld pool from atmospheric contamination and ensuring proper arc stability and weld quality. For welding nickel and nickel alloys, inert gases such as argon and helium are commonly used due to their non-reactive nature and ability to provide effective shielding. Gas mixtures containing a combination of argon and helium may also be utilized to achieve specific welding characteristics, such as increased arc stability or improved penetration.
Filler Metal Selection
Choosing the correct filler metal is essential for matching the chemical composition and mechanical properties of the weld metal to those of the base metal. For welding nickel and nickel alloys, filler metals with similar compositions, such as ERNiCr-3 for welding Inconel alloys, are typically used to ensure compatibility and maintain desired weld properties. Additionally, selecting filler metals with appropriate alloying elements can enhance weld strength, corrosion resistance, and other performance characteristics.
Welding Positions
Understanding and selecting the appropriate welding positions—such as flat, horizontal, vertical, and overhead—is essential for achieving optimal weld quality and productivity. Each welding position presents unique challenges and requires adjustments to welding techniques and parameters to ensure proper penetration, fusion, and bead appearance. Proper positioning of the workpiece and weld joint also facilitates accessibility and operator ergonomics during welding.
Heat Input Control
Controlling heat input during welding is critical for preventing overheating, distortion, and metallurgical changes in the base metal and weld metal. Techniques such as preheating, interpass temperature control, and manipulation of welding parameters help regulate heat input and minimize the risk of welding defects such as cracking, porosity, and distortion. Maintaining proper heat input control is essential for achieving consistent weld quality and ensuring the integrity of the welded joint.
Applications of Welded Nickel and Nickel Alloys
Nickel and nickel alloys find extensive applications in various industries due to their unique combination of properties and excellent weldability. Welded nickel components play a crucial role in enhancing performance, reliability, and efficiency across a wide range of applications.
Aerospace Industry
In the aerospace industry, welded nickel and nickel alloy components are utilized in critical applications requiring high strength, corrosion resistance, and temperature stability. These include aircraft engines, gas turbine components, exhaust systems, and structural elements. Welded nickel alloys such as Inconel and Hastelloy are prized for their ability to withstand extreme temperatures, corrosive environments, and mechanical stresses, making them indispensable for aerospace propulsion systems and airframe structures.
Chemical Processing
Welded nickel and nickel alloy equipment are widely used in the chemical processing industry for handling corrosive fluids, high temperatures, and aggressive environments. These include reactors, vessels, piping systems, heat exchangers, and filtration units. Nickel alloys such as Monel, Hastelloy, and Inconel offer superior corrosion resistance to a wide range of acids, alkalis, and corrosive gases, making them ideal for chemical processing applications in industries such as petrochemicals, pharmaceuticals, and specialty chemicals.
Power Generation
In the power generation sector, welded nickel components are employed in steam turbines, gas turbines, boilers, heat exchangers, and nuclear reactors. Nickel alloys exhibit excellent high-temperature strength, oxidation resistance, and thermal stability, making them well-suited for power generation applications subjected to elevated temperatures and harsh operating conditions. Welded nickel alloys such as Inconel and Nimonic are utilized in turbine blades, combustion chambers, and heat recovery systems to improve energy efficiency and reliability in power plants.
Oil and Gas Industry
The oil and gas industry relies on welded nickel and nickel alloy components for exploration, production, refining, and transportation operations. These include offshore platforms, subsea pipelines, pressure vessels, valves, and instrumentation systems. Nickel alloys provide excellent resistance to corrosion, erosion, and sour gas environments encountered in oil and gas processing facilities, enhancing equipment longevity and safety. Welded nickel alloys such as Inconel, Monel, and Hastelloy are extensively utilized in the oil and gas industry for their reliability and performance in demanding offshore and onshore applications.
Electronics and Electrical Components
Welded nickel and nickel alloy components play a vital role in the electronics and electrical industry for applications requiring high conductivity, magnetic properties, and corrosion resistance. These include electrical contacts, connectors, sensors, and magnetic shielding. Nickel-based alloys such as Kovar and Invar offer low electrical resistance, thermal expansion matching with electronic substrates, and magnetic properties suitable for electronic packaging and device assembly. Welded nickel components are essential for ensuring reliable electrical performance and signal integrity in electronic systems and devices.
Automotive Industry
In the automotive industry, welded nickel and nickel alloy components are used in various applications requiring high strength, corrosion resistance, and temperature stability. These include exhaust systems, catalytic converters, fuel injection systems, and battery components. Nickel alloys such as Inconel and Monel offer excellent resistance to heat, oxidation, and corrosion, making them suitable for automotive applications subjected to high temperatures and harsh operating conditions. Welded nickel components contribute to improved durability, efficiency, and environmental performance in modern vehicles.
FAQs
What are the advantages of welding nickel alloys?
Nickel alloys offer excellent corrosion resistance, high-temperature strength, and ductility, making them suitable for demanding applications in various industries.
How do I prevent cracking when welding nickel?
To prevent cracking, it’s essential to control heat input, use proper shielding to protect the weld from oxidation, and employ preheat and post-weld heat treatment as needed.
Can nickel alloys be welded to other metals?
Yes, nickel alloys can be welded to other metals using suitable welding techniques and filler materials designed for compatibility with both base metals.
What industries commonly use welded nickel components?
Industries such as chemical processing, aerospace, electronics, and power generation frequently utilize welded nickel components for their superior performance and reliability.
Are there specific safety considerations for welding nickel alloys?
Yes, safety considerations for welding nickel alloys include proper ventilation to control fume exposure, use of personal protective equipment, and awareness of potential hazards associated with handling hot metal and welding processes.
Conclusion
The welding of nickel and nickel alloys plays a critical role in numerous industries, providing essential components with superior properties and performance. This article has highlighted key points regarding the welding of nickel and nickel alloys, emphasized the importance of proper welding techniques, and discussed the future outlook for this field.