Welding of Stainless Steel 410 vs 316
Introduction
Welding stainless steel is a critical process in various industries, from construction to aerospace. Choosing the right grade of stainless steel is vital to ensure the longevity and integrity of the welded structures. In this article, we’ll delve into the specifics of welding two popular stainless steel grades: 410 and 316. We’ll explore their properties, applications, and the best welding techniques to use.
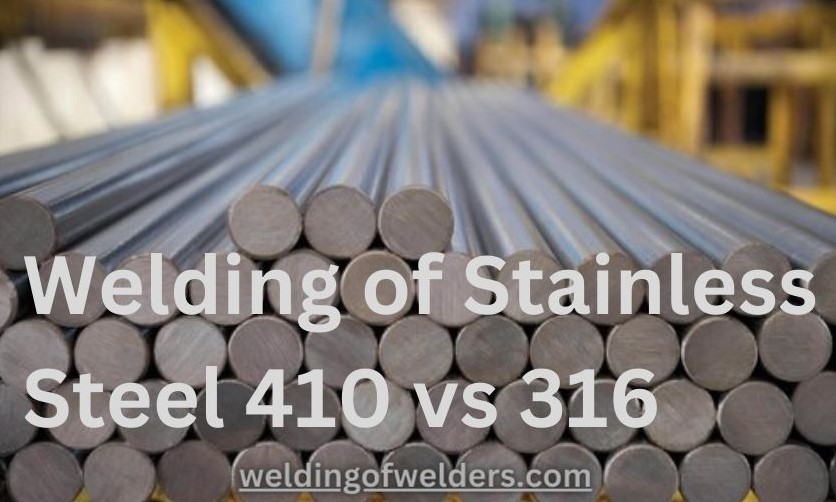
Understanding Stainless Steel 410
Composition and Properties
Stainless Steel 410 is a martensitic stainless steel known for its high strength and hardness. It contains about 11.5% to 13.5% chromium, which provides moderate corrosion resistance. The addition of carbon (up to 0.15%) enhances its hardness, making it suitable for applications requiring high mechanical strength.
Common Applications
SS 410 is widely used in cutlery, valves, pumps, and other applications where high strength and moderate corrosion resistance are required. Its ability to be hardened makes it ideal for tools and equipment exposed to wear and tear.
Advantages and Disadvantages
Advantages:
- High mechanical strength
- Good wear resistance
- Can be heat-treated for added hardness
Disadvantages:
- Lower corrosion resistance compared to austenitic stainless steels
- Brittle in nature, especially after welding
Understanding Stainless Steel 316
Composition and Properties
Stainless Steel 316 is an austenitic stainless steel that contains 16% to 18% chromium, 10% to 14% nickel, and 2% to 3% molybdenum. The addition of molybdenum enhances its corrosion resistance, especially against chlorides and other industrial solvents.
Common Applications
SS 316 is preferred in marine environments, chemical processing, and medical devices due to its superior corrosion resistance. It is also used in food processing and pharmaceutical equipment, where hygiene is crucial.
Advantages and Disadvantages
Advantages:
- Excellent corrosion resistance
- High ductility and formability
- Better performance in high-temperature environments
Disadvantages:
- Higher cost compared to other stainless steels
- Requires careful handling during welding to avoid contamination
Comparing Stainless Steel 410 and 316
Differences in Composition
The primary difference lies in their composition. SS 410 is a martensitic steel with higher carbon content, while SS 316 is an austenitic steel with added nickel and molybdenum for improved corrosion resistance.
Differences in Properties
SS 410 offers higher strength and hardness, but SS 316 excels in corrosion resistance and overall durability. SS 316 also maintains its properties at higher temperatures, making it suitable for more demanding environments.
Cost Comparison
SS 316 is generally more expensive than SS 410 due to its superior properties and the additional alloying elements like nickel and molybdenum.
Weldability of Stainless Steel 410
Pre-Weld Considerations
Before welding SS 410, it’s crucial to preheat the material to avoid cracking. Preheating to around 200-300°C helps reduce thermal stress.
Welding Techniques Suitable for SS 410
TIG (Tungsten Inert Gas) welding and stick welding are commonly used for SS 410. These methods provide better control over the welding process and help maintain the mechanical properties of the steel.
Post-Weld Treatments
Post-weld heat treatment (PWHT) is essential to restore the hardness and reduce brittleness. Typically, a tempering process is carried out at 600-700°C.
Weldability of Stainless Steel 316
Pre-Weld Considerations
SS 316 requires clean surfaces free of contaminants to prevent weld defects. No preheating is generally needed due to its stable austenitic structure.
Welding Techniques Suitable for SS 316
TIG and MIG (Metal Inert Gas) welding are ideal for SS 316. These methods ensure high-quality welds with minimal distortion and excellent corrosion resistance.
Post-Weld Treatments
Post-weld cleaning, such as pickling and passivation, is necessary to restore the corrosion resistance. These processes remove surface contaminants and oxide layers.
Welding Techniques for Stainless Steel
TIG Welding
TIG welding offers precise control and produces high-quality welds. It’s suitable for both SS 410 and SS 316.
MIG Welding
MIG welding is faster and more cost-effective, especially for SS 316. It provides good penetration and a clean finish.
Stick Welding
Stick welding is versatile and can be used in various environments, making it suitable for SS 410.
Comparison of Techniques
Each technique has its pros and cons. TIG welding is preferred for its precision, MIG for its speed, and stick welding for its versatility.
Electrodes for SS 410 and 316
Electrodes play a crucial role in welding by affecting the weld quality and properties. Selecting the right electrode is vital for achieving strong, defect-free welds.
Specific Electrodes for Stainless Steel 410
For welding Stainless Steel 410, commonly used electrodes include:
- AWS E410: Suitable for matching composition and properties of 410
- AWS E309L: Used for dissimilar welding or as a buffer layer to prevent cracking
Specific Electrodes for Stainless Steel 316
For welding Stainless Steel 316, appropriate electrodes include:
- AWS E316L: Provides excellent corrosion resistance and prevents sensitization
- AWS E308L: Sometimes used for welding 316 to 304 stainless steel
Challenges in Welding Stainless Steel
Thermal Conductivity Issues
Stainless steels have lower thermal conductivity, leading to localized overheating and distortion during welding.
Distortion and Warping
Controlling heat input is crucial to minimize distortion and warping. Using fixtures and clamps can help maintain the shape during welding.
Corrosion Resistance Considerations
Welding can introduce impurities that reduce corrosion resistance. Proper cleaning and post-weld treatments are essential to maintain the material’s properties.
FAQs
What is the main difference between SS 410 and SS 316?
SS 410 is a martensitic stainless steel known for its high strength and hardness, while SS 316 is an austenitic stainless steel with superior corrosion resistance due to the addition of nickel and molybdenum.
Can SS 410 be welded using the same techniques as SS 316?
While some welding techniques like TIG can be used for both, SS 410 requires preheating and post-weld heat treatment, which are not necessary for SS 316.
What are the common applications for SS 410 and SS 316?
SS 410 is used in applications requiring high strength and wear resistance, such as cutlery and pump shafts. SS 316 is preferred in marine, chemical, and food processing industries due to its excellent corrosion resistance.
How can I prevent corrosion when welding stainless steel?
Ensure clean surfaces, use appropriate welding techniques, and perform post-weld treatments like pickling and passivation to maintain corrosion resistance.
What safety measures should I take when welding stainless steel?
Wear protective equipment, ensure proper ventilation, and handle materials carefully to prevent contamination and exposure to harmful fumes.
Conclusion
Welding stainless steel 410 and 316 requires understanding their unique properties and selecting appropriate welding techniques. While SS 410 offers high strength and hardness, SS 316 excels in corrosion resistance. Proper pre-weld and post-weld treatments are crucial to achieving optimal results. By following best practices and considering application-specific needs, you can ensure the longevity and performance of your welded structures.