Welding Procedure Specifications (WPS)
Introduction
Welding is an intricate process that requires precision and adherence to specific guidelines to ensure the integrity of the weld. One of the most critical elements in the welding process is the Welding Procedure Specification (WPS). But what exactly is a WPS, and why is it so important in welding?
A Welding Procedure Specification (WPS) is a formal document that provides detailed instructions on how to perform a specific weld. It includes information about the materials, techniques, and parameters to be used during the welding process. The primary purpose of a WPS is to ensure that the welding work is done correctly, safely, and consistently, regardless of who performs the weld or where it is being done.
The significance of a WPS cannot be overstated. In industries such as construction, manufacturing, and pipeline welding, where the quality of a weld can mean the difference between success and catastrophic failure, having a well-defined WPS is essential. It serves as a blueprint for welders, providing them with the necessary guidelines to create strong, reliable, and defect-free welds.
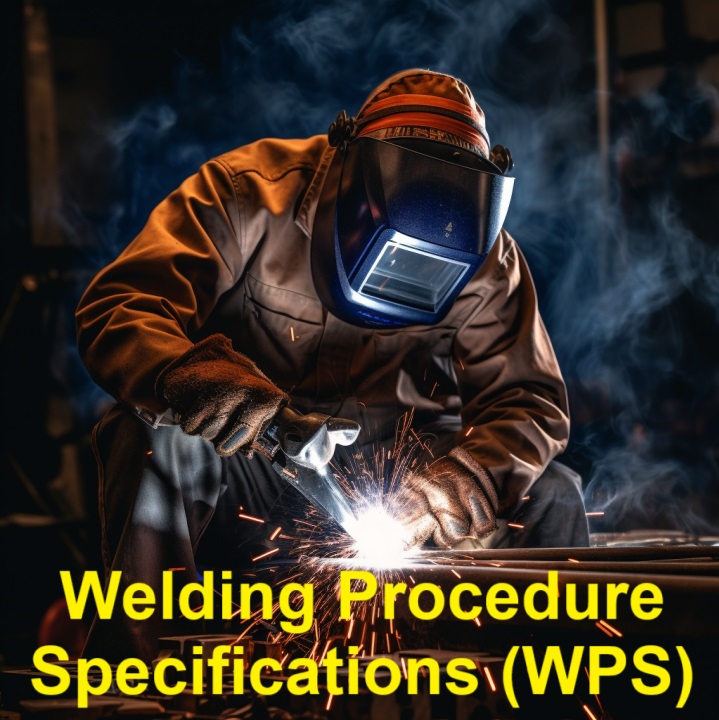
Key Components of a Welding Procedure Specifications
A WPS is a comprehensive document that covers various aspects of the welding process. Let’s break down some of the key components that make up a WPS:
Base Materials
The base material refers to the metals or alloys that are being joined together during the welding process. The WPS specifies the type and grade of base materials to be used, ensuring compatibility and proper bonding.
Filler Materials
Filler materials are used to fill the gap between the base materials being welded. The WPS details the type of filler material, such as electrodes or welding wire, that should be used to achieve the desired weld properties.
Welding Process
This section of the WPS outlines the specific welding process to be used, whether it’s MIG, TIG, Stick, or another method. It also includes details about the welding technique, such as the type of arc, voltage, and amperage settings.
Joint Design and Preparation
Proper joint design and preparation are crucial for a successful weld. The WPS provides instructions on how to prepare the joint, including bevel angles, root openings, and the cleaning of base materials.
Welding Position
Welding can be performed in various positions, such as flat, vertical, overhead, or horizontal. The WPS specifies the welding position that is appropriate for the task at hand, ensuring consistency and quality.
Types of Welding Procedure Specifications
WPSs can be categorized into different types based on how they are developed and used. Here’s a closer look at the main types:
Prequalified WPS
A Prequalified WPS is one that meets the requirements set by welding codes and standards without the need for additional testing. These WPSs are based on proven and established welding procedures that have a track record of success.
Qualified WPS
Unlike Prequalified WPSs, Qualified WPSs require testing and validation before they can be used. This involves creating a test weld, which is then inspected and tested to ensure it meets the necessary quality standards.
Standard WPS
A Standard WPS is a generic welding procedure that can be applied across multiple projects or industries. These are typically developed by industry organizations and can be used as a reference for developing project-specific WPSs.
The Process of Developing a Welding Procedure Specification
Creating a WPS is a meticulous process that involves several steps to ensure the final document is accurate and reliable. Here’s how it’s typically done:
Research and Data Collection
The first step in developing a WPS is gathering all the necessary information about the welding project. This includes details about the base materials, filler materials, and the welding process. Researching industry standards and codes is also crucial at this stage.
Testing and Validation
Once the data is collected, the next step is to perform test welds to validate the proposed welding procedure. These test welds are subjected to rigorous inspections and tests, such as tensile strength and bend tests, to ensure they meet the required quality standards.
Documentation and Approval
After the welding procedure is validated, the WPS is documented in a detailed and organized manner. The document is then reviewed and approved by the relevant authorities, such as a welding engineer or inspector.
How to Interpret a Welding Procedure Specification
Reading and understanding a WPS can be challenging, especially for those who are new to the field of welding. However, with a little practice, you can become proficient at interpreting these documents. Here’s a guide to help you get started:
Reading the WPS Document
A WPS is typically organized into sections, each covering a specific aspect of the welding process. Start by familiarizing yourself with the layout of the document and the information presented in each section.
Understanding Symbols and Codes
WPS documents often contain various symbols and codes that represent different welding parameters. Understanding these symbols is crucial for interpreting the WPS accurately. For example, symbols may indicate the type of weld, the position of the weld, and the type of filler material to be used.
Common Mistakes in Interpretation
One of the most common mistakes when interpreting a WPS is overlooking important details, such as the correct welding position or the specified amperage settings. It’s essential to pay close attention to every detail in the WPS to avoid errors during the welding process.
WPS and Welding Codes and Standards
Welding codes and standards play a critical role in the development and implementation of WPSs. These codes ensure that welding work meets the necessary safety and quality requirements. Here’s what you need to know:
Overview of Common Welding Codes
Several organizations set welding codes and standards, including the American Welding Society (AWS), the American Society of Mechanical Engineers (ASME), and the International Organization for Standardization (ISO). Each of these organizations has its own set of codes that cover different aspects of welding.
The Role of Standards in WPS
Standards provide a framework for developing WPSs, ensuring that the welding procedures are consistent with industry best practices. Adhering to these standards helps prevent welding defects and ensures the structural integrity of the welded components.
Compliance with Industry Regulations
Compliance with industry regulations is mandatory for many welding projects, especially those in critical industries like oil and gas, construction, and aerospace. A well-defined WPS ensures that the welding work complies with all relevant regulations, minimizing the risk of legal issues or project delays.
Challenges in Creating and Implementing WPS
While WPSs are essential for successful welding projects, creating and implementing them can be challenging. Here are some of the common challenges faced by welding professionals:
Technical Challenges
Developing a WPS that meets all the technical requirements can be complex, especially for projects involving new materials or welding techniques. It may require extensive testing and validation to ensure the WPS is accurate and reliable.
Human Factors and Training
Even the best WPS won’t be effective if the welders are not properly trained. Ensuring that all personnel understand and follow the WPS is crucial for achieving consistent and high-quality welds.
Cost and Time Considerations
Developing a WPS can be time-consuming and costly, especially for large or complex projects. However, the investment is often justified by the improved quality and reduced risk of weld failures.
Benefits of Using a Well-Defined WPS
Despite the challenges, the benefits of using a well-defined WPS are significant. Here’s why you should always have a WPS in place for your welding projects:
Enhanced Quality and Consistency
A WPS provides a clear set of guidelines that help ensure the welds are consistent and meet the required quality standards. This reduces the risk of defects and improves the overall reliability of the welded components.
Improved Safety
Welding can be dangerous if not done correctly. A WPS helps minimize the risk of accidents by specifying the correct procedures and safety measures to be followed during the welding process.
Cost Efficiency and Reduced Waste
A well-defined WPS ensures that the welding process is efficient, minimizing the use of materials and reducing the likelihood of rework due to welding defects. By following the guidelines set out in a WPS, you can save time and money, ultimately leading to a more cost-effective project.
FAQs
What is the difference between a Prequalified WPS and a Qualified WPS?
A Prequalified WPS is based on proven welding procedures that meet specific code requirements and do not require additional testing, while a Qualified WPS requires testing and validation to ensure it meets the necessary standards for the specific project.
How often should a WPS be reviewed or updated?
A WPS should be reviewed periodically, especially when there are changes in materials, welding processes, or industry standards. It’s good practice to review the WPS at the start of each new project.
Can a WPS be used across different projects?
While some WPSs, such as Standard WPSs, can be used across multiple projects, it’s essential to ensure that the WPS is appropriate for the specific materials and conditions of each project.
What are the consequences of not following a WPS?
Not following a WPS can lead to weld defects, safety hazards, project delays, and increased costs due to rework. In critical industries, it may also result in legal liabilities or regulatory penalties.
Who is responsible for creating and maintaining a WPS?
Typically, a welding engineer or a qualified welding professional is responsible for creating and maintaining a WPS. However, it’s a collaborative effort that may also involve input from inspectors, project managers, and other stakeholders to ensure compliance with industry standards and project requirements.
Conclusion
In the world of welding, a Welding Procedure Specification (WPS) is not just a document—it’s a critical tool that ensures the success of a welding project. By providing detailed instructions on every aspect of the welding process, a WPS helps achieve consistency, quality, and safety across the board. Whether you’re working on a small fabrication project or a large industrial installation, a well-prepared WPS can be the difference between a strong, reliable weld and a costly failure.