Understanding Welding Rod Amperage 6010
The 6010 welding rod is an electrode commonly used in shielded metal arc welding (SMAW), or stick welding. Its designation follows the American Welding Society (AWS) system, where each digit has a specific meaning:
- “60” refers to the tensile strength of the weld, which is 60,000 psi. This strength ensures the weld can handle heavy loads and stresses.
- “1” indicates that it can be used in all positions: flat, horizontal, vertical, and overhead.
- “0” denotes the type of coating, which is cellulose-based, and its compatibility with DC (direct current) polarity.
This rod is highly favored for its ability to penetrate deeply into the base material, creating strong welds even on corroded, painted, or dirty surfaces. It’s especially useful in industries like construction and pipeline welding.
Why is the 6010 Popular Among Welders?
The 6010 rod is a staple in the welding world due to its versatility and performance. Its aggressive arc is ideal for tasks requiring deep penetration and quick slag freezing, allowing welders to work efficiently in vertical and overhead positions. Despite its demanding technique, experienced welders appreciate its ability to deliver robust welds even under challenging conditions.
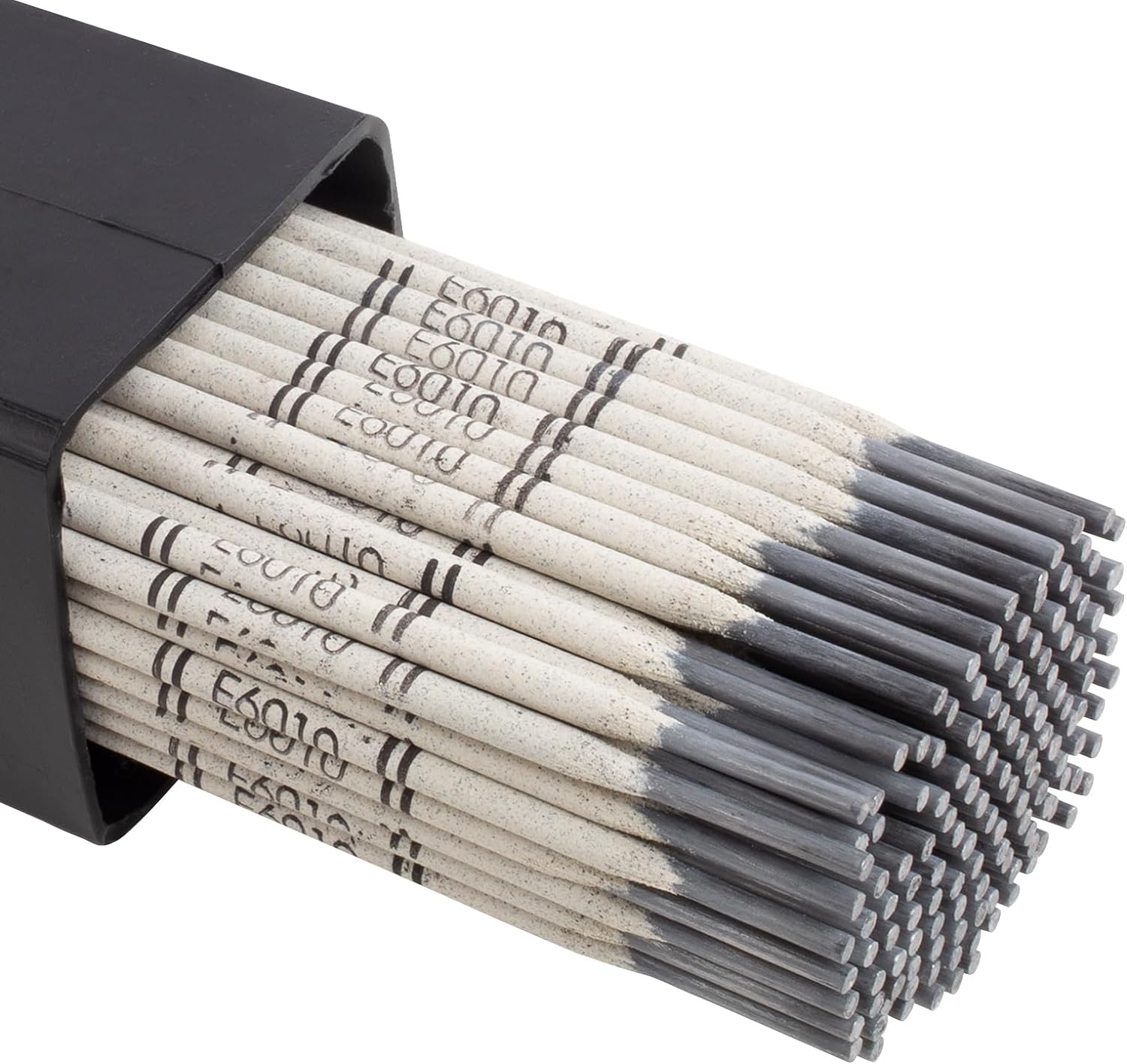
Check Price on Amazon
Basics of Welding Amperage
What is Amperage in Welding?
Amperage in welding refers to the electrical current that flows through the electrode and base metal, generating heat to melt the materials. It’s a critical factor because it determines the weld’s depth of penetration and overall quality. Higher amperage produces more heat, enabling deeper penetration, while lower amperage is suited for thinner materials or fine welding.
How Does Amperage Affect Welding Performance?
The right amperage setting ensures a balance between penetration and weld bead quality:
- Low amperage: Results in insufficient heat, weak welds, and poor fusion.
- High amperage: Causes excessive heat, spatter, and potential burn-through.
- Proper amperage settings vary based on rod diameter, material thickness, and welding position.
Ideal Amperage Range for 6010 Rods
Standard Amperage Settings for Different Rod Sizes
To achieve optimal results, follow these general amperage guidelines based on rod diameter:
- 3/32-inch rod: Best used between 40-90 amps. Suitable for thin materials and precise welds.
- 1/8-inch rod: Requires 75-125 amps. This size is versatile and commonly used for general purposes.
- 5/32-inch rod: Operates well at 115-160 amps, ideal for heavy-duty projects like thick structural welds.
Adjustments might be necessary based on the material’s condition, position, or specific requirements.
Factors That Influence Amperage Choices
Several factors can influence the amperage setting:
- Material Thickness: Thicker metals require higher amperage for adequate penetration.
- Welding Position: Overhead or vertical welds often need slightly lower amperage to control the molten pool.
- Rod Condition: Damp rods or poor storage conditions may require adjustments to amperage.
- Power Source: Compatibility with AC or DC and its voltage stability can impact amperage settings.
Practical Applications of 6010 Rods
Common Uses of 6010 Welding Rods
The 6010 rod is a workhorse in several industries:
- Pipe Welding and Structural Work: Its deep penetration makes it perfect for pipe joints and load-bearing structures where strength is crucial.
- Repairs and Maintenance Jobs: The rod’s ability to cut through rust, oil, or dirt without extensive prep work is invaluable for repairs in the field.
Advantages of Using 6010 Rods
- Deep Penetration and Flexibility: It delivers consistent welds on challenging joints, making it ideal for critical applications.
- Compatibility with Various Power Sources: The 6010 rod works seamlessly with DC, offering stable arcs even in less-than-ideal environments.
Troubleshooting and Best Practices
Common Challenges with 6010 Rods
Even experienced welders encounter difficulties with 6010 rods:
- Porosity: Can occur if the arc length is too long or if the base metal isn’t clean enough.
- Inconsistent Beads: Often caused by improper travel speed or incorrect settings.
- Excessive Spatter: A sign of too high amperage or improper arc control.
- Overheating Issues: Can weaken the weld and damage the rod’s coating.
Tips for Achieving Optimal Welds
- Prepping the Metal and Setting the Machine Correctly: Clean the workpiece and double-check the machine settings before welding.
- Perfecting Your Welding Technique: Practice maintaining a consistent arc length and travel speed to create smooth, uniform welds. Using a “whipping” or “circling” motion with the rod often helps improve bead quality.
Safety and Maintenance
Safety Tips When Welding with 6010 Rods
Safety should always be a priority:
- Protecting Yourself from Fumes and Heat: Ensure proper ventilation to avoid inhaling harmful fumes. Wear flame-resistant clothing and high-quality welding gloves.
- Avoiding Electrical Hazards: Regularly inspect cables and connections to prevent accidents.
Storing and Maintaining Your 6010 Rods
Proper care extends the life and performance of your rods:
- Proper Storage to Prevent Moisture Absorption: Keep rods in a dry environment, away from humidity. Moisture can weaken the coating and lead to poor weld quality.
- Ensuring Longevity of the Welding Rods: Use a rod oven for storage if necessary, especially in damp conditions.
FAQs
What happens if I use the wrong amperage with 6010 rods?
Using incorrect amperage can lead to weak welds, excessive spatter, or even material damage. Always test on a scrap piece to find the right setting.
Are 6010 rods suitable for beginners?
6010 rods can be challenging for beginners due to their aggressive arc and fast-freezing slag. With practice and guidance, they can be mastered.
Can 6010 rods be used for TIG welding?
No, 6010 rods are designed exclusively for stick welding and are not suitable for TIG welding processes.
How can I reduce spatter when using 6010 rods?
To minimize spatter, use the correct amperage, clean the base metal thoroughly, and maintain a steady hand during welding.
Is it okay to weld vertically with 6010 rods?
Absolutely! The 6010 rod is specifically designed for all-position welding, including vertical and overhead tasks. Its fast-freezing slag makes it ideal for these applications.
Final Thoughts
Mastering the 6010 welding rod involves understanding its characteristics, choosing the correct amperage, and following best practices for safety and maintenance. With its exceptional penetration and versatility, it’s a valuable tool for welders tackling challenging projects. By fine-tuning your technique and equipment, you can achieve professional-quality welds every time.