Welding Stainless Steel Flanges
Welding stainless steel flanges is a critical task in many industries, from petrochemical plants to food processing facilities. These flanges are essential components that connect pipes and ensure leak-proof operations, making their integrity paramount. In this article, we’ll dive deep into the techniques, challenges, and best practices for welding stainless steel flanges, ensuring you achieve strong, durable welds every time.
Introduction
Welding stainless steel flanges is not just about joining two metal parts—it’s about precision, accuracy, and understanding the unique properties of stainless steel. Stainless steel’s corrosion resistance, strength, and temperature tolerance make it an excellent choice for flanges. However, welding stainless steel requires special techniques and attention to detail to preserve its properties.
Stainless steel flanges are widely used in industries where corrosion resistance and durability are critical. From oil pipelines to chemical plants, these flanges allow for seamless connections and easy maintenance. But poor welding techniques can compromise their integrity, leading to expensive downtime or dangerous leaks.
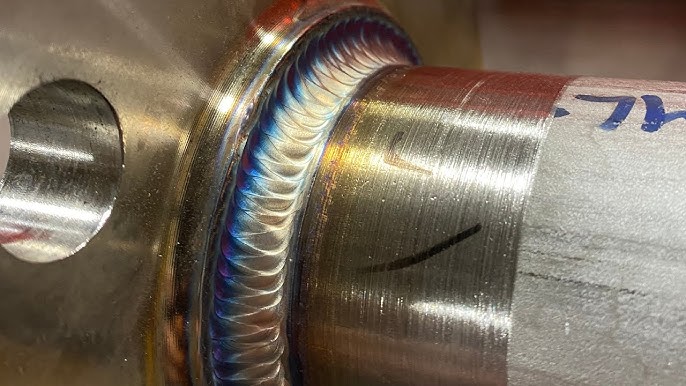
Understanding Stainless Steel Flanges
Before diving into the welding process, it’s essential to understand the types of stainless steel flanges and the grades of stainless steel typically used.
Types of Stainless Steel Flanges
There are several types of stainless steel flanges, each designed for specific applications. Some of the most common types include:
- Slip-On Flanges: These are easy to align and install, as they slip over the pipe before welding. They are generally used in low-pressure applications where the risk of stress or extreme temperatures is minimal. While easier to work with, slip-on flanges need to be welded both inside and outside to ensure a strong connection.
- Weld Neck Flanges: These are designed for high-stress environments. The tapered neck provides extra support and reduces the risk of fatigue at the base of the flange. Weld neck flanges are commonly used in applications involving high pressure and temperature.
- Blind Flanges: These flanges are used to close off the ends of piping systems. Since they don’t have a bore, they’re ideal for terminating the flow in a system or performing maintenance. Welding a blind flange requires careful technique to ensure the seal is completely tight.
- Socket Weld Flanges: Typically used in high-pressure systems with small diameters, socket weld flanges offer a high level of strength and durability. They require fillet welding, and proper cleaning is essential to avoid contamination.
Grades of Stainless Steel Used for Flanges
Stainless steel flanges are made from a variety of grades, each with specific properties suited for different environments:
- 304 Stainless Steel: This is the most commonly used grade for general-purpose applications. It offers good corrosion resistance and is relatively easy to work with. However, it may not be suitable for environments with high levels of chemical exposure.
- 316 Stainless Steel: Known for its superior resistance to corrosion, especially from chemicals and seawater, 316 is often used in more aggressive environments. This grade is ideal for chemical plants, marine applications, and food processing environments.
- 321 Stainless Steel: This grade is valued for its ability to withstand high temperatures and is often used in aerospace and heat exchanger applications. Its high thermal tolerance makes it a good option for welding flanges that will be exposed to extreme heat.
Preparation for Welding Stainless Steel Flanges
The success of a weld starts with proper preparation. Before you even strike an arc, make sure you have the right tools, equipment, and safety protocols in place.
Tools and Equipment Needed
- Welding Machine (TIG, MIG, or Stick Welder): The choice of welding machine depends on the type of weld required.
- Protective Gear: Welding stainless steel produces UV light and fumes. Ensure you have a proper welding helmet, gloves, and protective clothing.
- Filler Material: Use a filler rod that matches the stainless steel grade you’re welding.
- Argon Gas Cylinder: Argon is typically used as a shielding gas to protect the weld from oxidation.
Safety Precautions to Follow
- Always ensure proper ventilation, as welding stainless steel can release harmful fumes.
- Wear fire-resistant clothing and protect your skin from UV rays.
- Ensure your workspace is free of flammable materials.
- Never weld without eye protection, as arc flashes can cause serious injury.
Welding Techniques for Stainless Steel Flanges
Stainless steel flanges can be welded using several techniques, but some are more suited to this material than others.
TIG (Tungsten Inert Gas) Welding
TIG welding is widely regarded as the best method for welding stainless steel flanges due to its precision and control. It uses a tungsten electrode that doesn’t melt, while the heat of the arc melts the stainless steel and filler rod, forming the weld.
MIG (Metal Inert Gas) Welding
MIG welding is faster than TIG welding and is often used for thicker materials. However, it’s not as precise as TIG, and controlling heat input can be challenging, which might lead to warping in thinner flanges.
Stick Welding
Stick welding is less commonly used for stainless steel flanges due to the higher likelihood of contamination and less precise control. However, it can be useful in field applications where portability is necessary.
Challenges in Welding Stainless Steel Flanges
Welding stainless steel flanges comes with its unique set of challenges that can affect the quality of the weld if not addressed properly.
Heat Distortion
One of the biggest challenges when welding stainless steel is managing heat input. Stainless steel has a low thermal conductivity, which means that heat tends to stay localized. This can cause the material to warp or distort, especially when welding thinner sections. Controlling the heat input is essential to prevent these issues.
Maintaining Corrosion Resistance
Stainless steel’s primary advantage is its resistance to corrosion, but this can be compromised if the material is overheated or contaminated during welding. When exposed to excessive heat, stainless steel can lose its chromium content, which is responsible for its corrosion resistance. To avoid this, it’s important to control heat input and use proper shielding gases.
Avoiding Contamination
Contamination is a major concern when welding stainless steel. Even minor contact with carbon steel or other materials can introduce contaminants that lead to rust or corrosion. It’s essential to use tools and materials dedicated solely to stainless steel and to thoroughly clean the flange before welding.
Best Practices for Welding Stainless Steel Flanges
To overcome these challenges, follow these best practices for flawless stainless steel flange welding.
Preheating and Post-Weld Heat Treatment
Preheating the flange can reduce the risk of cracking, especially with thicker materials. Post-weld heat treatment helps relieve internal stresses and improves the durability of the weld.
Cleaning and Preparing the Flange
Always clean the flange thoroughly before welding. Dirt, oil, or rust can contaminate the weld and lead to failure. Use a stainless steel wire brush to clean the surfaces.
Choosing the Right Filler Material
Make sure your filler rod matches the grade of stainless steel you’re welding. Using the wrong filler material can lead to weld failure, reduced corrosion resistance, and strength issues.
Common Mistakes to Avoid
Mistakes during welding can be costly, both in terms of time and materials. Avoid these common pitfalls to ensure a successful weld.
Overheating the Material
Excessive heat is one of the most common mistakes made when welding stainless steel. Overheating can cause warping, burn through the material, or degrade the chromium oxide layer that provides corrosion resistance. Always monitor your heat input and use a lower amperage when possible.
Improper Alignment
If the flange is not properly aligned before welding, it can cause stress concentrations that could lead to cracking or joint failure down the road. Use alignment tools and take your time to ensure everything is properly positioned before starting the weld.
Poor Gas Coverage
Good gas coverage is essential for protecting the weld from oxidation. If the shielding gas is disrupted or inadequate, it can lead to oxidation or contamination of the weld, compromising its strength and appearance. Always ensure your gas flow is consistent and covers the weld area completely.
Quality Testing and Inspection
Once the weld is complete, it’s important to perform quality checks to ensure the weld meets industry standards.
Non-Destructive Testing Methods
Non-destructive tests like dye penetrant testing, magnetic particle testing, and ultrasonic testing can detect surface cracks and internal flaws without damaging the flange.
Visual Inspection and Radiographic Testing
A thorough visual inspection should be the first step, followed by radiographic testing to check for hidden defects in the weld.
Ensuring Weld Integrity
Regular inspections and proper testing ensure the weld’s integrity and longevity, helping prevent costly failures down the line.
FAQs
Why is TIG welding preferred for stainless steel flanges?
TIG welding provides precise control over heat and produces high-quality, clean welds, making it ideal for stainless steel. It allows you to maintain the material’s corrosion resistance and ensures minimal distortion.
How do you prevent corrosion in welded stainless steel flanges?
To prevent corrosion, it’s important to clean the flange thoroughly before welding, use the correct filler material, and ensure proper shielding gas coverage to protect the weld from oxidation.
What is the best way to clean stainless steel flanges before welding?
Use a stainless steel wire brush and ensure the surface is free of dirt, oil, or contaminants. Avoid using tools that have been used on carbon steel to prevent cross-contamination.
What are the signs of a bad weld in stainless steel flanges?
Signs of a bad weld include cracks, porosity, discoloration, undercuts, and warping. These defects can weaken the weld and reduce the flange’s overall performance.
Can stainless steel flanges be welded without preheating?
Yes, thinner stainless steel flanges typically don’t require preheating. However, thicker materials or those prone to cracking may benefit from preheating to reduce thermal stress.
Conclusion
Welding stainless steel flanges may seem daunting, but with the right preparation, techniques, and attention to detail, you can produce strong, durable welds that stand the test of time. By following best practices and avoiding common mistakes, you ensure the longevity and performance of the flanges, which are essential components in countless industrial applications.