Welding Stainless Steel Tube and Pipe
Welding stainless steel tubing and pipes is a critical process in industries ranging from food and beverage to petrochemicals and oil and gas. Ensuring corrosion resistance while boosting productivity can significantly improve the quality and cost-effectiveness of these applications. By evolving traditional methods and adopting best practices, welders can achieve these objectives without compromising the integrity of the stainless steel.
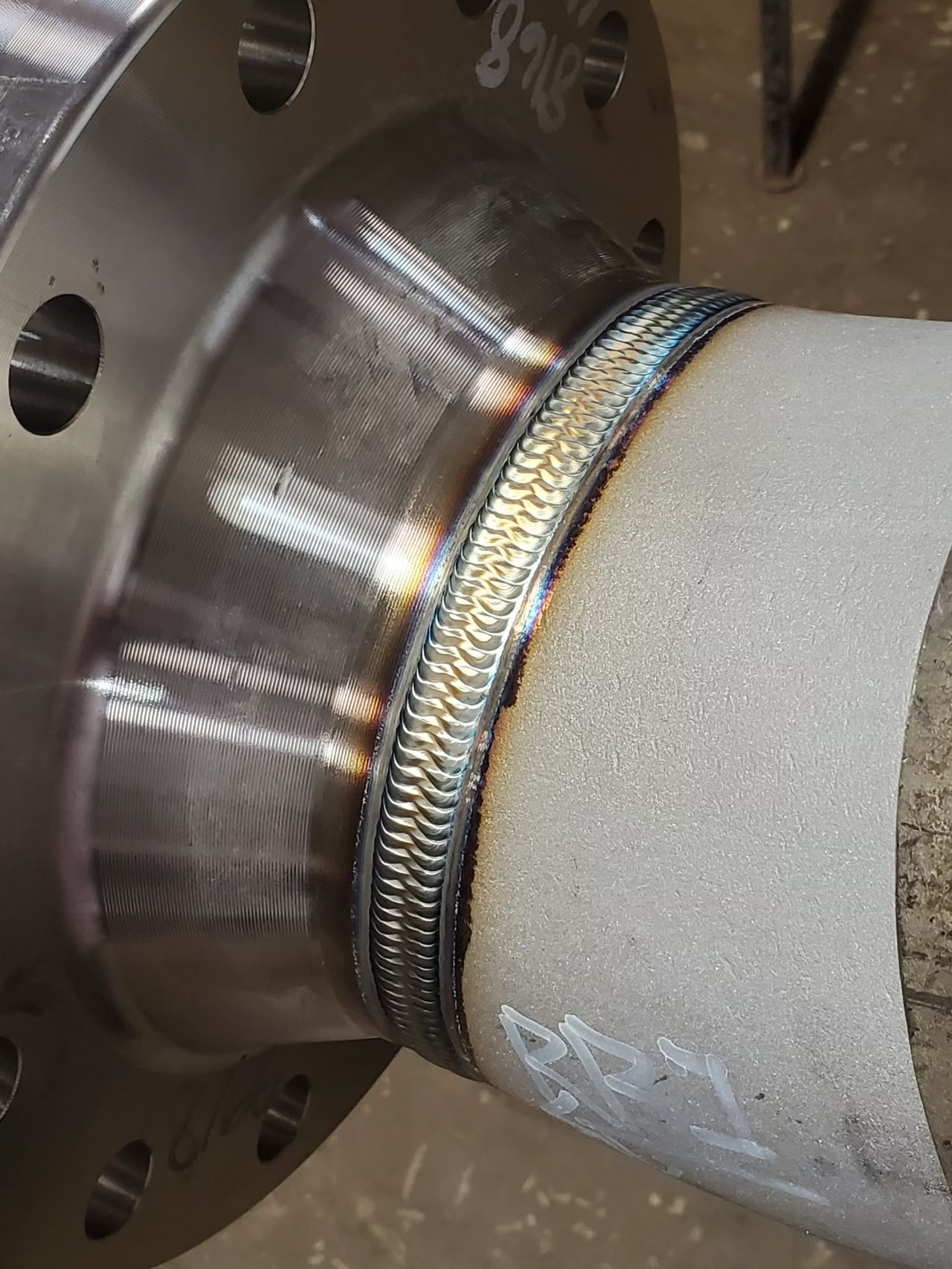
Introduction
Stainless steel is a widely used material known for its excellent corrosion resistance and mechanical properties. In applications involving stainless steel tubing and pipes, the welding process plays a vital role in maintaining these properties. But why is corrosion resistance so important? Imagine pipes in a food processing plant developing rust—this not only compromises safety but can also halt operations.
The challenge lies in balancing corrosion resistance with productivity. Traditional methods often focus heavily on quality but might slow down production. By revisiting these methods and integrating new techniques, we can achieve both quality and efficiency.
Choosing the Right Filler Metals
Low Carbon vs. High Carbon Fillers
When welding stainless steel, selecting the appropriate filler metal is essential. Fillers with an “L” designation, like ER308L, are designed for low carbon content. This helps maintain the corrosion resistance of low-carbon stainless steel alloys. For example, welding 304L base metal with a standard 308 filler metal can inadvertently raise carbon levels, increasing corrosion risks.
Conversely, fillers with an “H” designation, such as ER308H, are used in high-temperature environments where additional strength is required. For applications involving dissimilar metals, ER309LSi offers enhanced weld puddle fluidity and improved tie-ins.
Impact of Trace Elements on Corrosion Resistance
Trace elements like tin, antimony, and sulfur can negatively impact corrosion resistance. Opt for filler metals with minimal trace elements to ensure the longevity and performance of your welds.
Sensitization and How to Prevent It
Sensitization occurs when chromium in stainless steel reacts with carbon to form chromium carbides, depleting the material’s corrosion resistance. It’s like stealing the “stainless” out of stainless steel.
Strategies to Minimize Sensitization
- Use Low-Carbon Materials: Choose base and filler metals with low carbon content.
- Control Heat Input: Keep interpass temperatures low and reduce time in the sensitization temperature range (500–800°C).
- Add Special Alloys: Incorporate elements like titanium or niobium to prevent chromium-carbide formation.
Role of Shielding Gas
Back Purging with Argon
Argon back purging is a staple for maintaining corrosion resistance in stainless steel welding. For critical applications, pure argon ensures no contaminants compromise the weld.
Alternative Gases and Their Trade-Offs
In non-critical applications, nitrogen can be a cost-effective alternative. However, it may form nitrides that slightly reduce corrosion resistance. For processes like MIG, gas mixtures with low carbon dioxide levels are preferred to minimize carbon contamination.
Preparation and Fit-Up
Importance of Cleanliness in Welding
Cleanliness is paramount. Use dedicated tools for stainless steel to avoid contamination from carbon steel or aluminum. Even tiny impurities can lead to corrosion or weld defects.
Achieving Accurate Fit-Up
Precise fit-up minimizes gaps, reducing the need for excessive filler metal and lowering heat input. This is especially critical for sanitary and high-purity applications.
Optimizing Heat Input and Cooling
Managing Heat-Affected Zones (HAZ)
Heat input directly influences the size of the HAZ. Smaller HAZs retain more of the material’s original properties, ensuring better corrosion resistance and strength.
Benefits of High-Speed TIG Pulsing
Modern TIG inverters allow pulsing at up to 500 pulses per second, reducing heat input and distortion. This technology not only speeds up the process but also enhances weld penetration.
MIG Processes for Stainless Steel
The Role of RMD (Regulated Metal Deposition)
RMD improves upon traditional MIG methods by controlling metal transfer and heat input. This process reduces training time and increases productivity, with speeds ranging from 6 to 12 inches per minute.
Eliminating Back Purging in Certain Applications
While not suitable for high-purity applications, RMD enables back-purge-free welding in some scenarios, saving time and reducing costs.
Applications and Case Studies
High-Purity Industries:
These industries demand impeccable weld quality and corrosion resistance. TIG welding remains the gold standard for these applications.
Oil and Gas:
In oil and gas, combining RMD for root passes with pulsed MIG for fill and cap passes optimizes speed and cost-efficiency.
FAQs
Why is back purging necessary for stainless steel welding?
Back purging prevents oxidation on the weld’s underside, maintaining corrosion resistance.
Can I use nitrogen instead of argon for back purging?
Yes, but only in non-critical applications where slight reductions in corrosion resistance are acceptable.
What is sensitization in stainless steel?
Sensitization is the depletion of chromium due to carbide formation, leading to reduced corrosion resistance.
How does TIG pulsing improve welding?
TIG pulsing reduces heat input, minimizes distortion, and increases travel speeds.
What industries benefit most from RMD welding?
RMD is ideal for oil and gas, compressed air systems, and other less critical stainless steel applications.
Conclusion
Welding stainless steel tubes and pipes is both an art and a science. By understanding material properties, selecting the right consumables, and leveraging modern techniques, you can achieve superior results. Whether you’re fabricating for high-purity applications or large-scale industrial projects, balancing corrosion resistance with productivity is the key to success.