Welding Thin Pipes and Tubes: A Comprehensive Guide
Introduction
Welding thin pipes and tubes requires a unique set of skills and techniques to ensure a strong and reliable bond. Whether you’re a seasoned welder or just starting in the world of welding, this guide will provide you with valuable insights and practical advice to master the art of welding thin pipes and tubes. We’ll cover various aspects, from selecting the right equipment to addressing common challenges. So, let’s dive in and explore the fascinating world of welding thin pipes and tubes.
Understanding Thin Pipes and Tubes
Definition and Characteristics
Thin pipes and tubes, also known as thin-walled pipes and tubes, are defined by their relatively low wall thickness compared to their diameter. The specific criteria for considering a pipe or tube as “thin-walled” may vary by industry and application but typically involve a thickness-to-diameter ratio.
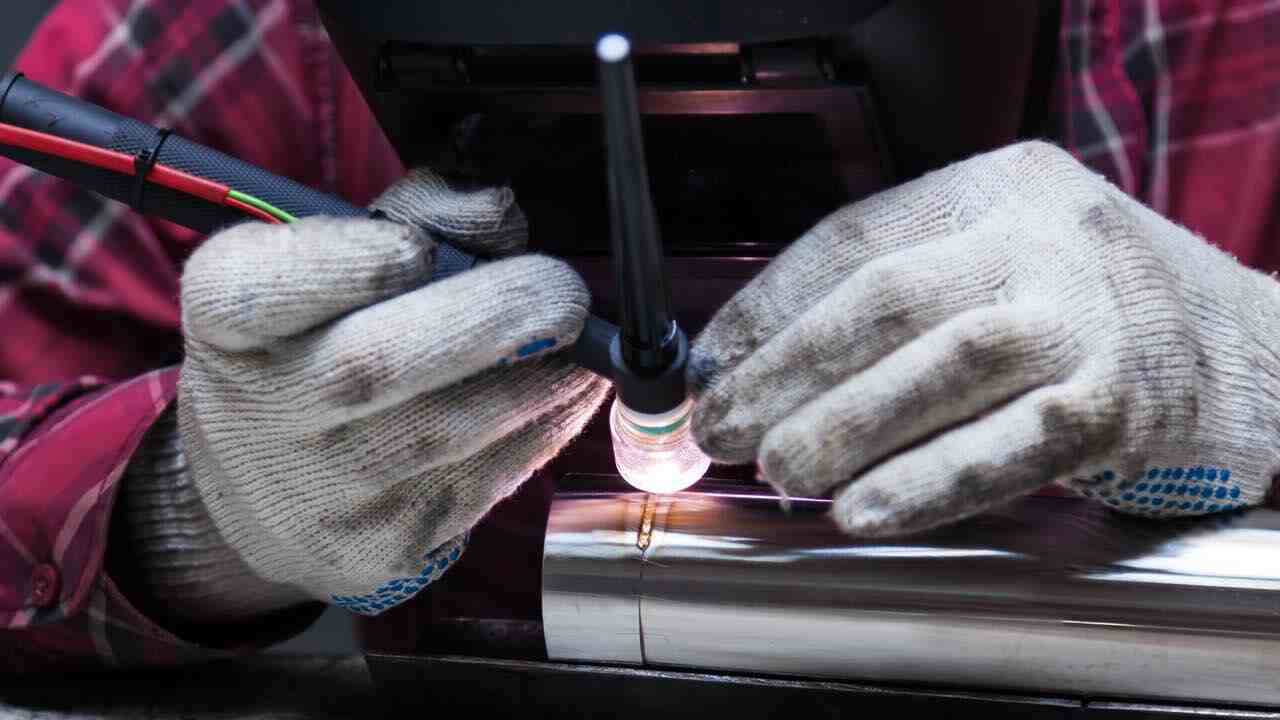
Characteristics of thin pipes and tubes include:
- Reduced Wall Thickness: Thin pipes and tubes have thinner walls compared to their larger diameter, which distinguishes them from their thicker counterparts.
- Lightweight: Due to their reduced material volume, thin-walled pipes and tubes are lighter, making them suitable for applications where weight is a concern.
- Increased Flexibility: Thin materials are more flexible and can be bent or manipulated to meet specific design requirements.
- Heat Conductivity: Thin materials have a higher rate of heat conductivity, which can influence their response to welding processes.
Common Applications of Thin Pipes and Tubes
Thin pipes and tubes find extensive use across various industries due to their unique characteristics. Common applications include:
- Automotive Industry: Thin-walled exhaust pipes and tubes are used to reduce vehicle weight and improve fuel efficiency. They also play a role in the construction of roll cages and structural components.
- Aerospace Industry: Thin-walled tubes are essential for constructing aircraft structures, including wings and fuselages, where weight savings are critical.
- Pharmaceutical and Chemical Industries: Thin tubes are used for transporting fluids and gases in pharmaceutical manufacturing and chemical processing, ensuring precise and controlled material flows.
- Electronics: In the electronics industry, thin-walled tubes are used for heat dissipation and cooling in electronic components.
- Medical Devices: Thin tubes are employed in the manufacture of medical devices such as catheters and stents, where precision and biocompatibility are essential.
- Construction: Thin-walled pipes and tubes are used for plumbing and HVAC (heating, ventilation, and air conditioning) systems, as well as for structural applications in buildings.
Importance of Precision and Quality in Welding Thin Materials
Welding thin pipes and tubes demands a high level of precision and a commitment to maintaining quality standards. This is critical for several reasons:
- Structural Integrity: Thin-walled materials, when used in critical applications, require welds with exceptional strength and integrity. Any welding defects or inconsistencies can compromise the structural stability of the final product.
- Leak Prevention: In industries like pharmaceuticals and chemicals, ensuring a leak-free connection is imperative. Welding must be precise to prevent leaks, which could lead to contamination or hazardous situations.
- Heat Control: Precise heat control is necessary to avoid overheating and warping of thin materials during welding. Distortion can affect the fit and function of components.
- Aesthetics: In applications where appearance matters, such as consumer electronics or architectural structures, the quality of welding plays a crucial role in the final product’s aesthetics.
- Cost Efficiency: Achieving high-quality welds in thin materials can reduce material waste, rework, and repair costs, making the welding process more cost-effective.
Preparing Thin Pipes and Tubes for Welding
Surface Preparation and Cleaning
Surface preparation is a critical step in ensuring successful welding of thin pipes and tubes. Proper cleaning and surface treatment help remove contaminants and ensure good weld quality. Key considerations include:
- Cleaning: Thoroughly clean the surfaces to be welded, removing dirt, rust, paint, grease, and other contaminants. Solvents, wire brushes, and abrasive materials can be used for cleaning.
- Deburring: Remove any sharp edges or burrs from the edges of the pipe or tube. These can interfere with fit-up and cause stress concentration points.
- Surface Condition: Ensure that the surface is smooth and free of defects. Any surface imperfections can result in weld defects and weaknesses.
- Material Compatibility: Use cleaning agents and techniques that are compatible with the material being welded to avoid contamination or adverse reactions.
Proper Fit-Up and Alignment
Proper fit-up and alignment are essential to achieving high-quality welds in thin pipes and tubes. Misalignment or poor fit can lead to welding defects and compromised structural integrity. Consider the following:
- Joint Gap: Maintain a consistent and appropriate gap between the pipes or tubes to be joined. The gap size depends on the welding process and material thickness.
- Alignment: Ensure that the pipes or tubes are aligned correctly to achieve the desired joint configuration. Misalignment can result in uneven welds and stress concentrations.
- Root Gap: In some cases, maintaining a small root gap between the parts can improve weld penetration and quality. This is especially important for butt joints.
- Clamping: Use clamps or tack welds to hold the components in place during welding. This prevents movement and helps maintain proper alignment throughout the welding process.
Use of Clamps and Fixtures to Secure the Workpiece
Securing the workpiece using clamps and fixtures is crucial when welding thin pipes and tubes. Thin materials are more susceptible to distortion and movement during welding. Here’s why clamps and fixtures are essential:
- Stability: Clamps and fixtures provide stability to the workpiece, preventing it from shifting or moving during welding. This is especially important for maintaining alignment.
- Minimizing Distortion: Thin materials are prone to warping and distortion when subjected to heat. Properly secured workpieces help minimize these effects.
- Consistency: Clamps and fixtures ensure that the components being welded maintain a consistent position and orientation, leading to uniform welds.
- Safety: Securely clamped workpieces reduce the risk of accidents or injuries caused by unexpected movement during welding.
Importance of Joint Design in Thin Materials
The joint design is a critical factor when welding thin pipes and tubes. The joint configuration influences the strength, durability, and ease of welding. Consider the following aspects of joint design:
- Joint Type: Select the appropriate joint type for the application. Common joint configurations for thin pipes and tubes include butt joints, lap joints, and fillet joints.
- Welding Position: Consider the welding position (e.g., flat, horizontal, vertical, overhead) when designing the joint. Some positions may be more challenging to weld in thin materials.
- Weld Preparation: Ensure that the edges of the joint are properly prepared, including beveling or chamfering if necessary. This promotes full penetration and a strong weld.
- Root Openings: Maintain consistent root openings to allow for proper penetration and fusion in butt joints. Inadequate root openings can result in incomplete fusion and reduced strength.
- Edge Preparation: Beveling or rounding the edges of the joint can reduce the risk of lack of fusion and improve overall weld quality.
Welding Processes for Thin Pipes and Tubes
Overview of Welding Processes Suitable for Thin Materials
Welding thin pipes and tubes requires careful consideration of the welding process to ensure precise and high-quality results. Here’s an overview of some welding processes suitable for thin materials:
TIG (Tungsten Inert Gas) Welding:
- TIG welding, also known as GTAW (Gas Tungsten Arc Welding), is a versatile process suitable for welding thin materials.
- It uses a non-consumable tungsten electrode and an inert gas (usually argon) to create the arc.
- TIG welding provides precise control over heat input and is known for producing clean and high-quality welds.
- It is commonly used for stainless steel, aluminum, and non-ferrous metals, making it suitable for many thin-walled applications.
MIG (Metal Inert Gas) Welding:
- MIG welding, or GMAW (Gas Metal Arc Welding), is another popular process for welding thin pipes and tubes.
- It utilizes a consumable wire electrode and a shielding gas (usually a mixture of argon and CO2) to create the arc.
- MIG welding is known for its speed and efficiency, making it suitable for high-production environments.
- It is often used for mild steel, stainless steel, and aluminum thin-walled materials.
Plasma Arc Welding:
- Plasma arc welding is a precision welding process that combines features of TIG and plasma cutting.
- It uses a non-consumable tungsten electrode and an ionized gas (plasma) to create the arc.
- Plasma arc welding offers high heat concentration and control, making it suitable for thin materials.
- It is commonly used for stainless steel, aluminum, and exotic alloys in applications requiring high precision.
Advantages and Disadvantages of Each Welding Process
TIG Welding:
- Advantages:
- Excellent control over heat input.
- High-quality, clean welds with minimal spatter.
- Suitable for a wide range of materials.
- Ideal for thin materials and precision welding.
- Disadvantages:
- Slower welding speed compared to MIG.
- Requires a high level of skill and experience.
- Limited to relatively thin materials.
- Advantages:
MIG Welding:
- Advantages:
- High welding speed and efficiency.
- Suitable for thin materials and thicker sections.
- Semi-automatic and automatic processes available.
- Good for high-production environments.
- Disadvantages:
- Less control over heat input compared to TIG.
- Potential for more spatter.
- Limited to certain materials and positions.
- Advantages:
Plasma Arc Welding:
- Advantages:
- High precision and control over the arc.
- Suitable for thin materials and exotic alloys.
- Good for applications requiring deep penetration.
- Minimal distortion and heat-affected zone.
- Disadvantages:
- Complex equipment and setup.
- Higher initial cost.
- Requires specialized training and expertise.
- Advantages:
Selection Criteria for Choosing the Appropriate Welding Process
Selecting the right welding process for thin pipes and tubes depends on various factors, including:
- Material Type: Consider the material being welded, as some processes are better suited for specific materials like stainless steel, aluminum, or carbon steel.
- Thickness: Thin materials typically favor TIG and MIG welding due to their ability to provide precise control over heat input.
- Application: The intended use of the welded components, such as structural, aesthetic, or functional requirements, should guide the choice of welding process.
- Skill Level: The expertise of the welder and the available workforce’s proficiency in a particular welding process play a significant role in the selection.
- Production Volume: High-production environments may lean towards MIG welding for efficiency, while low-volume or precision applications may favor TIG or plasma arc welding.
- Cost and Equipment: Consider the initial investment, equipment availability, and ongoing operational costs associated with each welding process.
Welding Techniques for Thin Pipes and Tubes
Controlling Heat Input and Minimizing Distortion
Controlling heat input is crucial when welding thin pipes and tubes to prevent distortion and maintain the integrity of the workpiece. Key considerations include:
- Amperage and Voltage Control: Adjust the welding machine settings to control the heat output. Lower amperage and voltage settings are often necessary for thin materials.
- Interpass Temperature: Limit the time between passes to allow for cooling and reduce the overall heat input. This helps prevent overheating and distortion.
- Tack Welding: Use tack welds or skip welding to distribute heat more evenly along the joint. This minimizes localized distortion and stress.
- Heat Sink: Employ heat sinks or copper backing bars to help dissipate heat away from the weld area, particularly for longer welds.
- Peening: In some cases, peening (gentle tapping with a hammer) can help relieve stress and reduce distortion.
Managing Filler Metal and Welding Speed
Proper management of filler metal and welding speed is essential to achieve strong and reliable welds in thin pipes and tubes:
- Filler Metal Selection: Choose the appropriate filler metal based on the material being welded and the joint design. Matching filler metal properties to the base metal is critical.
- Wire Diameter: Select the correct wire diameter for MIG welding or electrode size for TIG welding. Thinner wires/electrodes are often used for thin materials.
- Welding Speed: Maintain a consistent and controlled welding speed. Too fast can result in lack of fusion, while too slow can lead to excessive heat input and distortion.
- Weaving Technique: Use a weaving technique when welding to distribute heat evenly across the joint. The width and frequency of the weave should be adjusted for thin materials.
Proper Torch or Electrode Angle
The angle at which the welding torch or electrode is held during welding significantly affects the weld quality in thin pipes and tubes:
- TIG Welding Angle: For TIG welding, maintain a torch angle of around 15-20 degrees from vertical to ensure proper shielding and heat control.
- MIG Welding Angle: For MIG welding, maintain a slight lead angle in the direction of travel to promote good gas coverage and penetration.
- Electrode Angle: In SMAW (Shielded Metal Arc Welding), maintain a consistent electrode angle to control the weld pool and ensure proper fusion.
Welding Sequence and Pattern
The welding sequence and pattern can impact the overall quality and appearance of the weld on thin pipes and tubes:
- Sequence: Plan the sequence in which you’ll weld sections of the joint. Typically, it’s advisable to start at the center and work outward to minimize distortion.
- Pattern: Adopt a consistent welding pattern, such as straight lines or a zigzag motion, to ensure even distribution of heat and filler metal.
- Intermittent Welds: For long welds, consider using intermittent welds with short stitch lengths to control heat input and reduce distortion.
Back Purging Techniques for Preventing Oxidation
In applications involving reactive materials like stainless steel, it’s essential to use back purging techniques to prevent oxidation on the inside of the pipe or tube:
- Backing Gas: Introduce an inert gas (e.g., argon) into the interior of the pipe or tube to displace oxygen and prevent oxidation during welding.
- Purge Rate: Control the flow rate of the backing gas to ensure it maintains a protective atmosphere inside the pipe or tube.
- Purge Dams or Plugs: Use purge dams or inflatable plugs to create a sealed chamber within the pipe, allowing for effective purging of the weld zone.
Proper back purging is critical when welding reactive metals to maintain the corrosion resistance and integrity of the material on the inside of the pipe or tube.
Common Welding Defects in Thin Pipes and Tubes
Welding thin pipes and tubes can be challenging, and several common defects can occur during the welding process. Identifying these defects, understanding their causes, and knowing how to prevent or troubleshoot them is crucial for producing high-quality welds.
Overview of Common Defects
- Porosity:
- Porosity appears as small gas pockets or voids within the weld bead.
- It weakens the weld and reduces its integrity.
- Undercut:
- Undercut is a groove or depression along the edges of the weld bead.
- It can lead to stress concentration points and reduced strength.
- Lack of Fusion:
- Lack of fusion occurs when the weld metal fails to fuse adequately with the base material or previous weld pass.
- It results in weak, incomplete welds.
- Cracks:
- Cracks can manifest as hot cracks (solidification cracks), cold cracks (hydrogen-induced cracking), or stress cracks (due to welding-induced stress).
- Cracks compromise the structural integrity of the weld.
- Excessive Spatter:
- Spatter is the metal droplets expelled during welding. Excessive spatter can lead to rough weld surfaces and reduced aesthetics.
- Burn-Through:
- Burn-through happens when the welding arc penetrates completely through the thin material.
- It results in holes or craters in the weld, weakening the structure.
Causes of Welding Defects in Thin Materials
- Inadequate Heat Control:
- Rapid heating and cooling in thin materials can lead to defects like lack of fusion and cracking.
- Insufficient heat input can result in incomplete fusion and poor penetration.
- Excessive Heat Input:
- Too much heat input can cause burn-through, distortion, and excessive spatter.
- Thin materials are more susceptible to heat-related defects.
- Inadequate Welding Techniques:
- Poor welding techniques, such as incorrect travel speed or electrode angles, can lead to defects like undercut and lack of fusion.
- Improper Joint Preparation:
- Inadequate joint preparation, including poor fit-up or misalignment, can result in welding defects.
- Lack of Back Purging:
- When welding reactive materials like stainless steel, failure to use back purging can lead to oxidation and porosity on the inside of the pipe or tube.
- Welding Process Selection:
- Choosing the wrong welding process for thin materials can result in defects. For example, using a process with high heat input may lead to burn-through.
Prevention and Troubleshooting Tips
- Proper Welding Techniques:
- Train welders in proper techniques, including maintaining correct travel speed, electrode angles, and weaving patterns.
- Control Heat Input:
- Adjust welding parameters, such as amperage and voltage, to control heat input. Use lower settings for thin materials.
- Preheating and Post-Weld Heat Treatment:
- Consider preheating thin materials to reduce thermal stress and post-weld heat treatment to relieve residual stresses.
- Joint Preparation:
- Ensure proper fit-up and alignment of the joint. Use tack welds or clamps to secure components.
- Back Purging:
- Employ back purging techniques to prevent oxidation on the inside of the pipe or tube, particularly for reactive materials.
- Quality Control and Inspection:
- Implement thorough inspection processes, including visual inspection and non-destructive testing, to detect and address defects.
- Welder Qualification:
- Ensure welders are qualified and have the necessary skills and certifications for the specific welding processes and materials.
- Document and Analyze Defects:
- Maintain detailed records of welding procedures and defect analysis to identify trends and take corrective actions.
Post-Welding Processes
After completing the welding of thin pipes and tubes, several post-welding processes may be necessary to ensure the welds meet the desired quality, appearance, and performance standards. These processes play a critical role in enhancing the weld’s integrity and protecting it from environmental factors.
Grinding and Finishing
- Grinding: Grinding is often used to remove excess weld material, smooth out irregularities, and improve the appearance of the weld. It can also be used to blend weld seams into the surrounding material for a seamless look.
- Surface Finish: The choice of surface finish, whether it’s a smooth and polished finish or a textured finish, may depend on the intended use and aesthetic requirements of the welded components.
- Deburring: Remove any sharp edges or burrs that may have formed during welding or grinding to ensure the safety of handling and use.
Stress Relieving
- Heat Treatment: In some cases, stress-relieving heat treatments may be necessary to reduce residual stresses in the weld and base material. This is especially important when welding materials prone to distortion or cracking.
- Annealing: Annealing is a controlled heating and cooling process that can help relieve stresses and improve the mechanical properties of certain materials.
- Post-Weld Heat Treatment: Depending on the welding process and materials involved, post-weld heat treatment can help improve the weld’s mechanical properties and relieve residual stresses.
Surface Treatment and Coating
- Surface Cleaning: Ensure the weld and surrounding area are thoroughly cleaned to remove any contaminants, such as oils, grease, or residue from the welding process.
- Surface Protection: Consider applying surface protection methods such as coatings, paints, or plating to protect the weld from corrosion, oxidation, or other environmental factors.
- Passivation: Passivation is commonly used for stainless steel components to remove free iron and create a protective passive layer that enhances corrosion resistance.
- Anodizing and Plating: For aluminum or other non-ferrous materials, anodizing or plating can provide both protective and decorative surface finishes.
- Painting and Coating: In some applications, painting or coating the weld and surrounding area may be necessary to provide protection against corrosion, chemicals, or UV exposure.
- Electroplating: Electroplating can provide a durable and corrosion-resistant metal coating on the welded components, improving their longevity and performance.
Quality Control and Inspection
Quality control and inspection are integral parts of the welding process for ensuring the integrity and strength of welds in thin pipes and tubes. Effective inspection methods help identify defects and deviations from quality standards.
Non-destructive Testing Methods (e.g., X-ray, Ultrasonic Testing)
- X-ray Testing (Radiographic Testing):
- X-ray testing is a non-destructive testing method that uses X-rays or gamma rays to examine the internal structure of the weld and base metal.
- It is highly effective in detecting internal defects such as porosity, lack of fusion, and cracks.
- X-ray testing provides detailed images of the weld, allowing for precise evaluation.
- Ultrasonic Testing:
- Ultrasonic testing involves sending high-frequency sound waves into the material and measuring the time it takes for the waves to return.
- It is used to detect internal defects like cracks, inclusions, and lack of fusion.
- Ultrasonic testing is commonly used for assessing weld quality in thin materials.
- Magnetic Particle Testing:
- Magnetic particle testing is suitable for ferrous materials and is used to detect surface and near-surface defects.
- It involves applying a magnetic field to the material and applying magnetic particles. Discontinuities create magnetic fields that attract the particles, revealing defects.
- Liquid Penetrant Testing:
- Liquid penetrant testing is used to detect surface cracks, porosity, and other surface defects.
- A liquid penetrant is applied to the surface of the weld, penetrates into surface discontinuities, and is then revealed through a developer.
Visual Inspection and Weld Bead Appearance
- Visual Inspection:
- Visual inspection is a fundamental method for evaluating the weld’s external appearance, including bead profile, size, and alignment.
- Welders and inspectors visually examine the weld for defects such as cracks, incomplete fusion, porosity, and undercuts.
- Weld Bead Appearance:
- The appearance of the weld bead can provide valuable information about the quality of the weld.
- A well-executed weld bead should have consistent size and shape, smooth ripples, and minimal spatter.
- Irregularities or inconsistencies in the bead may indicate potential defects.
Ensuring Weld Integrity and Strength
- Destructive Testing:
- Destructive testing involves subjecting sample welds to mechanical or chemical tests to assess their strength and integrity.
- Common destructive tests include tensile testing, bend testing, and impact testing.
- These tests provide data on the weld’s mechanical properties, such as tensile strength, ductility, and impact resistance.
- Welding Procedure Qualification:
- Ensure that welding procedures are qualified and conform to industry standards and codes.
- This involves testing samples of the proposed welding procedure to verify that they meet specified criteria for weld quality and integrity.
- Documentation and Records:
- Maintain detailed records of welding procedures, inspection results, and any necessary repairs or rework.
- Documentation provides a traceable history of the welding process and helps ensure compliance with quality standards.
- Welder Qualification:
- Verify that welders are properly qualified and certified to perform welding on thin pipes and tubes.
- Welder qualification includes testing their skills and knowledge to ensure they meet industry standards.
- Quality Assurance Programs:
- Implement quality assurance programs that include regular audits, process monitoring, and continuous improvement efforts.
- These programs help maintain and improve welding quality over time.
FAQs
Can I use the same welding technique for all types of thin pipes and tubes?
It depends on the material. Different metals may require specific welding methods.
How can I prevent distortion when welding thin pipes?
Proper heat management and using clamps or fixtures can help minimize distortion.
What safety gear should I wear when welding thin pipes and tubes?
Always wear a welding helmet, gloves, flame-resistant clothing, and safety glasses.
Is TIG welding the best choice for all thin materials?
TIG welding is suitable for many thin materials, but it’s essential to consider the specific requirements of your project.
What are the common defects in welded thin pipes and tubes?
Common defects include porosity, cracks, and incomplete penetration. Regular inspection and testing can help identify and address these issues.
Conclusion
Welding thin pipes and tubes may seem challenging, but with the right knowledge and techniques, you can achieve strong and reliable welds. Remember to choose the appropriate equipment, practice precision, and address common challenges effectively. By mastering the art of welding thin materials, you’ll expand your welding skills and tackle a wider range of projects with confidence.