What is Cap Pass in Welding?
Welding, at its core, involves joining two or more pieces of metal to create a solid and durable structure. However, achieving this outcome requires more than just running a bead of molten metal along the joint. Different stages, or passes, contribute to the quality and longevity of the weld. Among these, the cap pass holds a unique and crucial role. This article explores what the cap pass is, why it’s important, and how to master it for optimal results.
Understanding Welding Passes
In welding, a pass refers to a single progression of welding along the joint. Depending on the joint type and thickness of the materials, multiple passes are often required. Each pass serves a specific purpose in building up a strong, functional weld. Let’s take a closer look at the different types of passes.
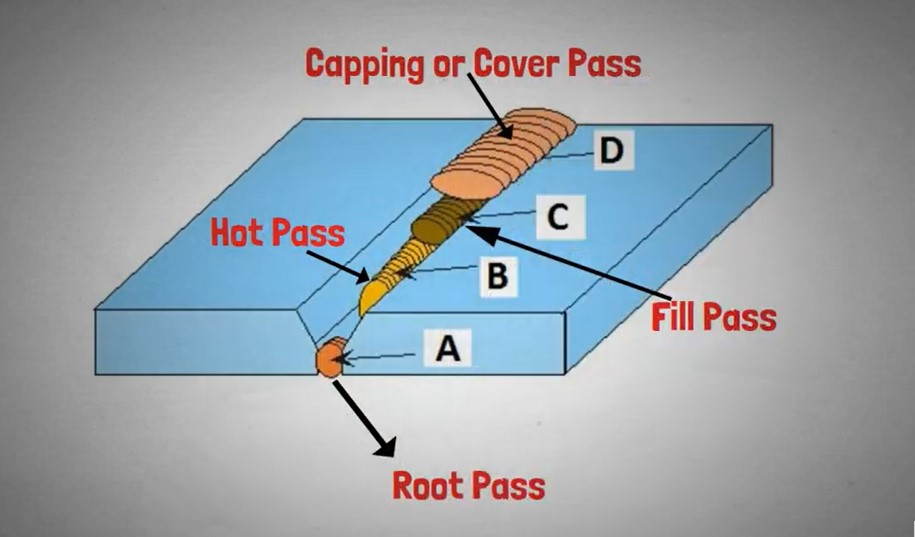
Root Pass
The root pass is the very first weld pass applied to the joint. It’s designed to penetrate deeply and ensure the base metals are properly fused at the root of the weld. Think of it as laying a strong foundation—without a solid root pass, the entire weld could fail.
Filler Pass
Once the root pass is complete, the filler pass (or passes) are added to fill the joint. These passes build up the weld’s thickness and strength. The number of filler passes depends on the joint’s thickness and the welding method used.
Cap Pass
The final layer in the welding process is the cap pass. This pass not only seals the weld but also provides a finished appearance, completing the weld’s structural and aesthetic requirements.
Defining Cap Pass in Welding
What is a Cap Pass?
The cap pass is the last weld bead applied in the multi-pass welding process. It sits on top of the filler passes, essentially “capping” the weld joint. This pass plays a critical role in ensuring the weld’s integrity and appearance.
Why is it Called a Cap Pass?
The name “cap pass” comes from its function. Just as a cap tops off a bottle, this pass tops off the weld, providing a protective layer while also completing the weld’s look.
Purpose and Importance of Cap Pass in Welding
Enhancing Weld Strength
While the root and filler passes establish the weld’s structural base, the cap pass adds an extra layer of reinforcement. This is particularly important for welds subjected to high levels of stress, as the cap pass helps distribute load forces more evenly.
Improving Aesthetic Appearance
The cap pass gives the weld its final, polished look. A smooth and uniform cap pass enhances the weld’s appearance, which is crucial in projects where the weld will be visible, such as in pipelines, structural frames, or automotive applications.
Providing Final Protection
The cap pass acts as a shield for the underlying layers. By sealing the joint completely, it protects the weld from external factors like moisture, contaminants, and oxidation, which can lead to corrosion or weakening over time.
Techniques for Applying a Cap Pass
Achieving a flawless cap pass requires skill and attention to detail. The technique you choose can significantly impact the quality of the cap pass.
Choosing the Right Welding Technique
Each welding method has its advantages and is suitable for specific applications:
- Stick Welding (SMAW): Known for its versatility, stick welding works well in outdoor environments or for thicker materials. It’s a reliable option for achieving a strong cap pass.
- MIG Welding (GMAW): This method is ideal for high-speed applications and thinner materials. MIG welding provides excellent control for a smooth cap pass.
- TIG Welding (GTAW): TIG welding offers precision and is preferred for applications that require a clean and aesthetically pleasing finish. It’s great for critical welds where quality is paramount.
Proper Welding Speed and Heat Control
Controlling your welding speed and heat input is vital. If the heat is too high, it can cause excessive warping or burn-through, while low heat can lead to incomplete fusion. Similarly, maintaining a consistent speed helps ensure a uniform bead profile.
Common Challenges in Cap Pass Welding
Even experienced welders face challenges when applying a cap pass. Identifying and addressing these issues is key to achieving a quality weld.
Issues with Undercut or Overlap
- Undercut: This occurs when the edge of the weld bead cuts into the base metal, creating a groove. It weakens the weld and can lead to failure.
- Overlap: This happens when the weld metal flows over the base metal without proper fusion. It creates a weak point in the weld and looks unprofessional.
Managing Weld Distortion
Excessive heat during the cap pass can cause the metal to warp or distort, especially in thinner materials. Using proper heat control techniques and allowing for cooling time between passes can help minimize distortion.
Tips for a Perfect Cap Pass
Preparing the Weld Joint
Preparation is crucial. Ensure the joint is clean and free from dirt, rust, and oil. Proper joint preparation not only helps in achieving a stronger weld but also makes the cap pass smoother and more uniform.
Correct Use of Tools and Equipment
Using the right tools and settings is equally important. Choose the correct electrode, nozzle size, and amperage for your welding process. Adjusting these settings according to the material type and joint configuration can greatly improve your cap pass results.
Cap Pass and Welding Standards
Welding standards ensure that welds meet industry-specific quality and safety requirements.
Meeting Industry Requirements
Whether you’re working in construction, shipbuilding, or pipeline welding, adhering to industry standards is non-negotiable. The cap pass must meet certain specifications to ensure the weld’s performance under various conditions.
Common Codes and Regulations
Standards like AWS (American Welding Society) and ASME (American Society of Mechanical Engineers) specify requirements for cap passes, including bead contour, width, and penetration. Following these guidelines ensures your welds are up to code.
Benefits of a Proper Cap Pass
Long-Lasting Welds
A well-executed cap pass enhances the weld’s durability, ensuring it holds up under stress and environmental exposure for a long time.
Better Resistance to Corrosion
By sealing the joint, the cap pass prevents moisture and other corrosive elements from penetrating the weld. This is especially important in environments where the weld is exposed to harsh conditions.
FAQs
What is the difference between a cap pass and a filler pass?
A filler pass builds up the weld’s thickness, while the cap pass adds the final layer for strength, protection, and aesthetics.
Can a weld be strong without a cap pass?
While a weld may hold without a cap pass, it lacks the added protection and polish that the cap pass provides, which could affect its long-term durability.
How do you ensure a smooth cap pass?
Consistency in speed, proper heat control, and choosing the right welding technique are essential for a smooth and uniform cap pass.
Which welding technique is best for cap passes?
TIG welding is best for precision and aesthetics, while MIG and stick welding are great for speed and outdoor conditions.
What happens if the cap pass is improperly done?
An improper cap pass can lead to weak joints, increased susceptibility to corrosion, and a poor visual finish, potentially compromising the weld’s integrity.
Conclusion
The cap pass is more than just the final step in welding—it’s the layer that ensures the strength, durability, and appearance of the weld. Whether you’re working on a critical structural project or a small repair job, mastering the cap pass is essential for producing high-quality welds. By understanding its purpose, refining your technique, and adhering to industry standards, you can take your welding skills to the next level.