What is Narrow Gap Welding?
Definition and Overview:
Narrow gap welding (NGW) is a specialized technique tailored for welding thick materials by minimizing the width of the groove between the joint surfaces. This process significantly reduces the amount of filler material required and enhances efficiency. By creating a narrow groove, it optimizes weld integrity while reducing costs. This technique is particularly useful in applications requiring robust joints in challenging environments, such as shipbuilding or nuclear reactors.
History and Evolution of Narrow Gap Welding
Narrow gap welding was developed during the mid-20th century as industries seek efficient solutions for joining thick plates. Traditional welding methods often involved wide grooves, which consumed more filler material and time. Over decades, innovations like automation and advanced equipment have propelled NGW to the forefront of welding technology, making it a vital method for modern fabrication challenges.
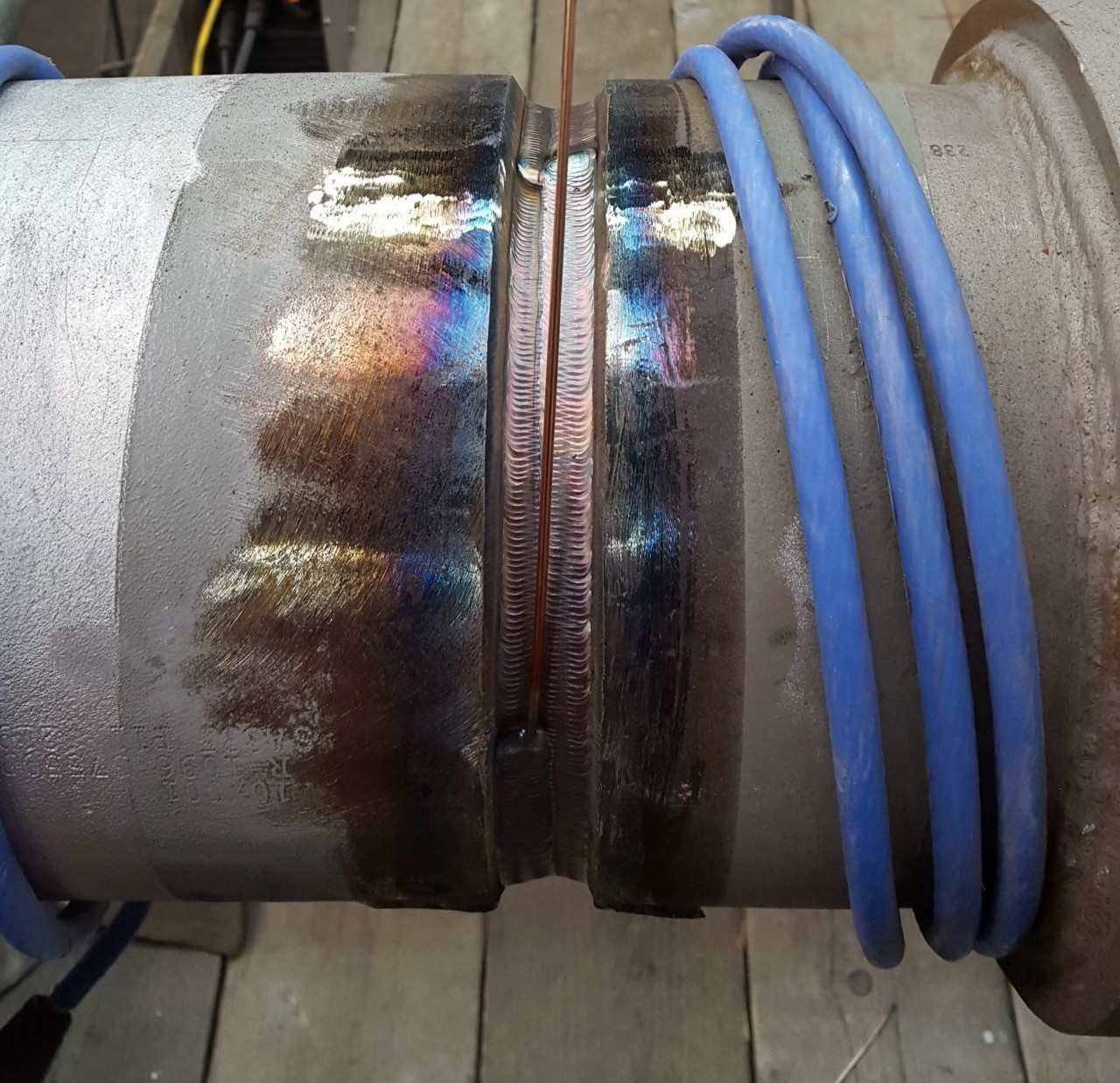
Why Use Narrow Gap Welding?
Advantages Over Conventional Welding Techniques
NGW offers multiple advantages over traditional methods. By reducing the groove width, it minimizes filler material usage and heat input, which reduces distortion. This results in a stronger, more precise weld. Additionally, it accelerates the welding process, cutting down on labor costs and project timelines. For industries prioritizing cost-efficiency and durability, NGW provides a highly advantageous alternative.
Applications in Various Industries
NGW is indispensable in industries dealing with thick materials and demanding safety standards. It’s widely used in power generation, shipbuilding, oil and gas, and construction of pressure vessels. For example, nuclear power plants rely on NGW for welding reactor components, as it ensures superior strength and minimal defects in critical areas.
How Does Narrow Gap Welding Work?
The Process Explained
The NGW process involves machining a narrow groove between the joint surfaces, typically ranging from 5 to 20 mm. The weld is deposited layer by layer, ensuring complete fusion with minimal heat input. This controlled approach prevents defects like porosity and ensures uniform weld penetration, creating a durable bond.
Key Equipment Used
Welding Power Source
A stable, high-quality power source is essential to maintain consistent arc characteristics. Advanced power sources enable precise control over parameters like voltage, current, and heat input.
Electrode and Filler Materials
The choice of filler material depends on the base material and application requirements. Matching the filler material to the parent metal ensures optimal strength and durability of the weld.
Role of Automation in Narrow Gap Welding
Automation has revolutionized NGW by increasing precision and reducing human error. Robotic systems can consistently follow the narrow groove, ensuring uniform weld quality. This is particularly beneficial for large-scale projects where consistency is paramount.
Types of Narrow Gap Welding Techniques
Submerged Arc Welding (SAW)
SAW is a highly efficient NGW method that uses a continuous wire electrode submerged under a blanket of flux. This protects the weld area from contamination and allows for deeper penetration, making it ideal for thick plates.
Gas Tungsten Arc Welding (GTAW)
Also known as TIG welding, GTAW is known for its precision. It uses a non-consumable tungsten electrode, providing clean and high-quality welds. This method is often employed in critical applications requiring minimal defects.
Plasma Arc Welding (PAW)
PAW provides excellent control over the welding arc by constricting it through a fine nozzle. This method delivers precise, high-quality welds, especially in applications where accuracy is critical.
Challenges in Narrow Gap Welding
Common Issues Faced
Despite its benefits, NGW presents challenges such as incomplete fusion, porosity, and difficulty in accessing the narrow groove. These issues can compromise weld quality if not addressed effectively.
Ways to Overcome Challenges
Proper preparation, advanced equipment, and skilled operators are key to overcoming NGW challenges. Preheating the material and using optimized welding parameters can also reduce defects and improve results.
Benefits of Narrow Gap Welding
Cost Savings
By reducing filler material usage and streamlining the welding process, NGW significantly lowers costs in large-scale projects, making it an economically viable solution.
Efficiency Improvements
The narrow groove design reduces welding time, allowing projects to be completed more quickly without sacrificing quality.
Enhanced Weld Quality
NGW’s precise approach ensures consistent and high-quality welds, which are crucial for applications where safety and durability are non-negotiable.
Tips for Successful Narrow Gap Welding
Preparing the Joint
Accurate machining of the groove is essential. Clean, well-prepared surfaces minimize the risk of contamination and defects.
Monitoring Parameters
Regularly monitoring parameters such as heat input, travel speed, and electrode positioning ensures optimal weld quality and prevents errors.
Ensuring Safety
Safety is critical in any welding process. Operators should use proper protective equipment and adhere to established safety protocols to avoid accidents and health hazards.
FAQs
What materials are best suited for narrow gap welding?
Steel, stainless steel, and high-strength alloys are commonly used in NGW due to their weldability and structural properties.
Can narrow gap welding be performed manually?
While possible, manual NGW is challenging and typically less efficient than automated methods due to the precision required.
What is the typical groove width in narrow gap welding?
The groove width generally ranges from 5 to 20 mm, depending on material thickness and application requirements.
How does narrow gap welding compare to traditional welding methods?
NGW offers superior efficiency, cost savings, and weld quality for thick materials compared to conventional techniques.
Are there specific certifications required for narrow gap welding operators?
Yes, certifications such as those from the American Welding Society (AWS) are often required to ensure operator proficiency.
Conclusion
Narrow gap welding is a transformative technique that addresses the challenges of welding thick materials. With its cost-saving benefits, enhanced efficiency, and superior weld quality, it stands out as a vital method in various industries. As technology evolves, NGW will continue to play a pivotal role in advancing industrial fabrication.