Introduction to Destructive Weld Testing: Ensuring Strong and Reliable Joints
Introduction
Welding is a vital process in various industries, from construction and manufacturing to automotive and aerospace. The quality and reliability of welded joints play a crucial role in ensuring the structural integrity and safety of the finished product. To assess the strength and integrity of welds, destructive weld testing is conducted. This article explores the intricacies of destructive weld testing, its significance, and the methods involved to obtain accurate and reliable results.
What is Destructive Weld Testing?
Destructive weld testing refers to a set of techniques employed to assess the mechanical properties and performance of welds by subjecting them to controlled stress or strain until they fail. Unlike non-destructive testing methods that aim to detect defects without causing any damage, destructive testing involves intentionally breaking or damaging the test specimens to evaluate their strength, ductility, and other relevant properties.
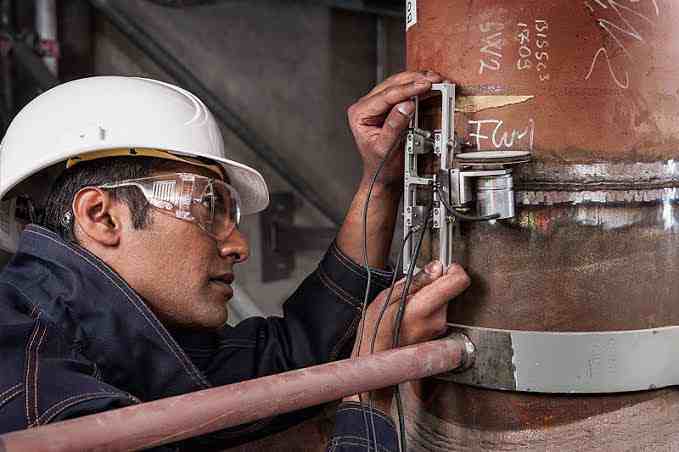
Why is Destructive Weld Testing Important?
Destructive weld testing is essential for several reasons. Firstly, it helps ensure that welded joints meet the required specifications and standards for the specific application. By subjecting the welds to extreme conditions, it allows engineers and inspectors to identify potential weaknesses or defects that could compromise the integrity of the structure.
Moreover, destructive weld testing provides valuable data on the mechanical properties of the welds, such as tensile strength, hardness, impact resistance, and fatigue life. This information is crucial for engineers to optimize the welding process, select appropriate materials, and design structures capable of withstanding the expected loads and environmental conditions.
Common Methods of Destructive Weld Testing
There are several commonly used methods of destructive weld testing, each focusing on evaluating specific aspects of the weld’s performance. These methods include:
Tensile Testing
Tensile testing involves applying an axial load to a welded test specimen until it fractures. This test measures the maximum tensile strength, yield strength, and elongation of the weld, providing insights into its ductility and ability to withstand pulling forces.
Bend Testing
Bend testing assesses the weld’s resistance to cracking and deformation by subjecting it to bending forces. This test helps identify any defects, such as lack of fusion or cracks, which may be hidden within the weld joint.
Charpy Impact Test
The Charpy impact test evaluates the weld’s ability to withstand sudden impact or shock loads. It involves striking a notched specimen with a pendulum, measuring the energy absorbed during fracture. This test is particularly important for assessing the weld’s resistance to brittle fracture.
Hardness Testing
Hardness testing measures the weld’s resistance to indentation or penetration by using a hardness tester. It helps determine the weld’s strength and can indicate the presence of potential defects, such as excessive hardness or soft spots.
Visual Examination and Macroscopic Evaluation
Visual examination involves visually inspecting the weld joint for any visible defects, such as cracks, porosity, or lack of fusion. Macroscopic evaluation, on the other hand, involves observing the cross-section of the weld to assess the quality and integrity of the joint.
Benefits of Destructive Weld Testing
Destructive weld testing offers several benefits in ensuring the quality and reliability of welded joints. These advantages include:
- Accurate Assessment: Destructive testing provides precise and quantitative data regarding the mechanical properties and performance of welds, allowing for accurate assessment and validation.
- Quality Control: By subjecting welds to extreme conditions and intentionally causing failure, destructive testing helps identify defects, such as cracks, inclusions, or lack of fusion. This aids in quality control and ensures that welds meet the required standards.
- Optimization of Welding Process: The data obtained from destructive testing enables engineers to optimize the welding process, such as adjusting parameters, selecting appropriate filler materials, or modifying pre- and post-weld heat treatments.
- Enhanced Safety: By identifying potential weaknesses or defects in welds, destructive testing contributes to enhanced safety by preventing catastrophic failures and accidents.
The Process of Destructive Weld Testing
The process of destructive weld testing involves several steps, ensuring accurate and reliable results. These steps include:
- Test Specimen Preparation: The weld specimen is carefully prepared according to the applicable standards, ensuring it represents the joint to be evaluated accurately.
- Test Selection: Depending on the desired information and evaluation criteria, the appropriate destructive testing methods are selected, such as tensile testing, bend testing, or impact testing.
- Execution of Tests: The selected tests are performed on the prepared test specimens, following the specific testing procedures and standards.
- Data Collection: During the testing process, various measurements and observations are made to collect data on the weld’s mechanical properties, performance, and any defects encountered.
- Data Analysis and Interpretation: The collected data is analyzed, and the results are interpreted to determine the weld’s quality, conformity to standards, and any necessary corrective actions.
Preparing for Destructive Weld Testing
Proper preparation is crucial to ensure accurate and meaningful results from destructive weld testing. The following steps are essential for effective preparation:
- Specification Review: Thoroughly review the specifications and standards that apply to the weld to understand the required properties and acceptance criteria.
- Sample Selection: Select representative samples that accurately represent the weld joints under evaluation, considering factors such as material type, thickness, and joint configuration.
- Sample Preparation: Carefully prepare the test specimens, ensuring they are free from surface defects, properly machined, and aligned according to the test requirements.
- Documentation: Maintain detailed records of the sample preparation process, including information on the welding procedure, material specifications, and any modifications made.
Conducting Tensile Testing
Tensile testing is a widely used method for evaluating the strength and ductility of welds. It involves subjecting a test specimen to an axial load until it fractures. The following steps outline the process of conducting tensile testing:
- Sample Preparation: Prepare the test specimen according to the applicable standards, ensuring it has the required dimensions and features, such as a specific gauge length and grip section.
- Mounting the Specimen: Securely grip the test specimen in the testing machine, ensuring proper alignment and contact between the grips and the specimen.
- Application of Load: Begin applying a steadily increasing axial load to the specimen until it fractures. During the test, record the load and deformation data.
- Fracture Analysis: Examine the fracture surfaces to determine the type and location of failure, such as ductile, brittle, or a combination of both. This analysis provides insights into the weld’s behavior under tension.
- Data Analysis: Calculate the tensile strength, yield strength, and elongation of the weld specimen based on the load-deformation data obtained during the test.
- Comparison to Standards: Compare the test results to the specified acceptance criteria or industry standards to assess the weld’s conformity.
Evaluating Bend Testing Results
Bend testing is commonly used to assess the weld’s resistance to cracking and deformation. It helps detect defects that may be hidden within the joint. The following steps outline the evaluation process for bend testing results:
- Visual Inspection: Visually examine the bent specimen for any visible defects, such as cracks, lack of fusion, or excessive porosity.
- Defect Measurement: Measure the dimensions and characteristics of any detected defects, such as crack length, width, and depth.
- Acceptance Criteria: Compare the measured defects to the specified acceptance criteria to determine if the weld passes or fails the bend test.
- Documentation: Maintain accurate records of the bend test results, including defect measurements, photographs, and any additional observations.
Analyzing Charpy Impact Test
The Charpy impact test is used to evaluate the weld’s ability to withstand sudden impact or shock loads. It measures the energy absorbed during fracture and provides insights into the weld’s resistance to brittle fracture. The following steps outline the process of analyzing Charpy impact test results:
- Test Execution: Conduct the Charpy impact test by striking a notched specimen with a pendulum, recording the absorbed energy.
- Fracture Analysis: Examine the fracture surface to determine the type of failure, such as ductile or brittle. This analysis helps assess the weld’s ability to absorb energy and resist sudden impact.
- Energy Absorption Calculation: Calculate the energy absorbed by the specimen during fracture based on the pendulum swing and the recorded data.
- Comparison to Standards: Compare the measured energy absorption to the specified acceptance criteria or industry standards to evaluate the weld’s performance.
- Documentation: Maintain comprehensive records of the Charpy impact test results, including energy absorption values, fracture analysis, and any additional observations.
Understanding Hardness Testing
Hardness testing provides valuable information about the weld’s strength and resistance to indentation or penetration. It helps identify potential defects and variations in material properties within the joint. The following steps outline the process of understanding hardness testing:
- Sample Preparation: Prepare the test specimen by grinding or polishing the surface to remove any irregularities or contaminants.
- Indentation: Apply a known load to the specimen using a hardness tester, creating an indentation on the surface.
- Hardness Measurement: Measure the dimensions of the indentation, typically the diagonal length or depth, using a microscope or specialized equipment.
- Hardness Calculation: Calculate the hardness value using the appropriate hardness scale, such as Brinell, Rockwell, or Vickers, based on the indentation dimensions and the applied load.
- Comparison to Standards: Compare the measured hardness value to the specified acceptance criteria or industry standards to evaluate the weld’s hardness characteristics.
- Documentation: Maintain detailed records of the hardness testing process, including indentation measurements, hardness values, and any relevant observations.
Visual Examination and Macroscopic Evaluation
Visual examination and macroscopic evaluation are crucial steps in the destructive weld testing process. These methods involve inspecting the weld joint visually and examining the cross-section to assess the quality and integrity of the weld. The following steps outline the process of visual examination and macroscopic evaluation:
- Visual Inspection: Visually examine the weld joint for any visible defects, such as cracks, porosity, lack of fusion, or excessive spatter. Use proper lighting and magnification tools if necessary.
- Cross-Section Preparation: Prepare the cross-section of the weld joint by cutting, grinding, or polishing the specimen to reveal the internal structure.
- Macroscopic Examination: Examine the cross-section of the weld joint using a microscope or visual inspection tools. Look for indications of defects, such as incomplete penetration, improper fusion, or segregation of alloying elements.
- Defect Identification: Identify and characterize any defects or anomalies found within the weld joint, such as cracks, inclusions, porosity, or improper grain structure.
- Documentation: Document the visual examination and macroscopic evaluation findings, including photographs, defect measurements, and any additional observations.
Benefits of Destructive Weld Testing
Destructive weld testing offers several benefits in ensuring the quality and reliability of welded joints. These advantages include:
- Accurate Assessment: Destructive testing provides precise and quantitative data regarding the mechanical properties and performance of welds, allowing for accurate assessment and validation.
- Quality Control: By subjecting welds to extreme conditions and intentionally causing failure, destructive testing helps identify defects, such as cracks, inclusions, or lack of fusion. This aids in quality control and ensures that welds meet the required standards.
- Optimization of Welding Process: The data obtained from destructive testing enables engineers to optimize the welding process, such as adjusting parameters, selecting appropriate filler materials, or modifying pre- and post-weld heat treatments.
- Enhanced Safety: By identifying potential weaknesses or defects in welds, destructive testing contributes to enhanced safety by preventing catastrophic failures and accidents.
FAQs
Q1: What is destructive weld testing?
Destructive weld testing is a method used to evaluate the quality and integrity of welds by subjecting them to extreme conditions that intentionally cause failure. This testing involves techniques such as tensile testing, bend testing, impact testing, and hardness testing to assess the weld’s mechanical properties, performance, and any potential defects.
Q2: How does destructive weld testing differ from non-destructive testing?
Destructive weld testing involves intentionally causing failure in the weld specimen to gather data about its properties and behavior under extreme conditions. Non-destructive testing, on the other hand, aims to evaluate the weld without causing any damage or alteration. Non-destructive testing methods include radiographic testing, ultrasonic inspection, and visual examination, among others.
Q3: What are the common destructive testing methods used for weld evaluation?
Some common destructive testing methods used for weld evaluation include tensile testing, bend testing, impact testing, hardness testing, visual examination, macroscopic evaluation, radiographic testing, and ultrasonic inspection. These methods provide valuable insights into the weld’s mechanical properties, structural integrity, and potential defects.
Why is it important to conduct destructive weld testing?
Destructive weld testing is important for several reasons:
- It ensures that welds meet the required standards and specifications, ensuring the overall quality and integrity of the welded joints.
- By intentionally causing failure, destructive testing helps identify potential defects or weaknesses within the weld, such as cracks, porosity, or lack of fusion.
- The data obtained from destructive testing allows engineers to optimize the welding process, adjust parameters, and select appropriate materials to improve the quality and performance of the welds.
Are there any limitations or drawbacks to destructive weld testing?
While destructive weld testing provides valuable information, it also has limitations and drawbacks:
- Destructive testing requires the use of dedicated test specimens, which may not fully represent the actual welded component or structure.
- It involves the destruction of the test specimen, making it unsuitable for evaluating in-service components or structures.
- Destructive testing can be time-consuming and costly, especially when multiple tests or repetitions are necessary.
Conclusion
In conclusion, destructive weld testing plays a vital role in evaluating the quality, integrity, and performance of welded joints. Through methods such as tensile testing, bend testing, impact testing, hardness testing, visual examination, macroscopic evaluation, radiographic testing, and ultrasonic inspection, engineers can gather valuable data about the weld’s mechanical properties, detect defects, and optimize the welding process. By ensuring the welds meet the required standards and specifications, destructive testing contributes to improved quality, reliability, and safety in various industries that rely on welded structures and components.