Overlap in Welding – How to Prevent It
Introduction
Welding is a critical skill in metalworking, essential for creating strong, durable joints. However, one common issue that welders face is welding overlap. Preventing welding overlap is crucial for ensuring the quality and longevity of the weld. In this article, we’ll explore what welding overlap is, why it happens, and how you can prevent it. Whether you’re a novice or an experienced welder, understanding these concepts will help you improve your welding skills and produce cleaner, more effective welds.
Understanding Welding Overlap
What is Welding Overlap?
Welding overlap occurs when the weld metal extends beyond the intended weld area and lies on the base metal without proper fusion. This defect is not just an aesthetic issue but can also compromise the structural integrity of the welded joint.
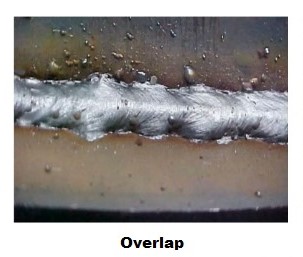
Common Causes of Welding Overlap
- Incorrect Welding Speed: Moving the welding torch too slowly can cause excessive weld metal to pool and overlap.
- Improper Welding Angle: Using the wrong angle can direct the weld metal to areas where it isn’t needed, leading to overlap.
- Inadequate Heat Settings: Too much heat can cause the weld pool to spread uncontrollably, resulting in overlap.
Signs of Welding Overlap
- Visual Inspection: Uneven and excessive weld metal around the edges of the weld.
- Touch Test: Feeling for raised edges or lips around the weld bead.
- Performance Issues: Weaker welds that are more prone to failure under stress.
The Consequences of Welding Overlap
Structural Integrity Issues
Welding overlap can significantly weaken the weld joint, making it susceptible to cracking and breaking under pressure. This can be particularly problematic in load-bearing structures where strength is critical.
Aesthetic Problems
Overlap can make a weld look messy and unprofessional, which is particularly problematic in applications where appearance matters, such as in decorative metalwork or automotive repair.
Increased Repair Costs
Fixing welding overlap often requires additional time and resources. The affected areas may need to be ground down and re-welded, increasing the overall cost of the welding project.
Techniques to Prevent Welding Overlap
Proper Training and Certification
Ensuring that welders are well-trained and certified is crucial. Proper training helps welders understand the correct techniques and parameters to use, reducing the likelihood of overlap.
Using the Right Equipment
Using high-quality welding equipment that is appropriate for the job can make a significant difference. Equipment that allows for precise control over welding parameters helps prevent overlap.
Correcting Welding Parameters
Adjusting the welding parameters, such as heat settings, speed, and angle, is essential. Finding the right balance is key to preventing overlap and achieving strong, clean welds.
Choosing the Right Welding Technique
MIG Welding
Metal Inert Gas (MIG) welding is versatile and relatively easy to learn, making it a good choice for many applications. However, careful control of speed and angle is necessary to prevent overlap.
TIG Welding
Tungsten Inert Gas (TIG) welding offers greater control and precision, which can help prevent overlap, especially on thin materials.
Stick Welding
Stick welding is robust and effective for heavy-duty applications, but it requires careful technique to avoid overlap, particularly on thinner materials.
Material Considerations
Different Materials and Their Properties
Different materials respond differently to welding. For example, aluminum requires different settings and techniques compared to steel. Understanding the properties of the materials you’re working with is essential to prevent overlap.
Material Thickness and Overlap
Thicker materials require more heat, which can increase the risk of overlap. Proper parameter adjustments are crucial to ensure the weld pool doesn’t spread excessively.
Welding Position and Overlap
Flat Position Welding
Welding in the flat position is generally easier and reduces the risk of overlap compared to other positions. This position allows gravity to help control the weld pool.
Horizontal Position Welding
Maintaining the right angle is crucial to avoid overlap in horizontal welding. The horizontal position can make it challenging to control the weld pool, leading to potential overlap.
Vertical Position Welding
Vertical welding requires precise control of speed and heat to prevent overlap. In this position, welders need to adjust their techniques to counteract gravity pulling the weld pool downward.
Overhead Position Welding
Overhead welding is challenging and requires expertise to avoid issues like overlap. In this position, welders need to ensure that the weld pool doesn’t drip or spread beyond the intended area.
Role of Welding Speed
Optimal Welding Speed
Finding the optimal speed for your specific welding project helps ensure that the weld pool does not spread too much, preventing overlap. The right speed depends on the material, thickness, and welding process used.
Effects of Too Fast or Too Slow Welding
Welding too fast can lead to weak joints, while welding too slow can cause excessive overlap. Balance is key. If you move too quickly, the weld may not penetrate properly; if you move too slowly, the weld pool can become too large and spread out of control.
Importance of Welding Angles
Ideal Welding Angles
Using the correct welding angle directs the weld metal where it is needed, preventing overlap. The ideal angle varies depending on the welding process and position but generally falls between 10 to 15 degrees from vertical.
Adjusting Angles to Prevent Overlap
Sometimes, small adjustments to the welding angle can make a big difference in avoiding overlap. If you notice the weld pool starting to spread too much, adjusting your angle can help control it better.
FAQs
What is welding overlap?
Welding overlap occurs when the weld metal extends beyond the intended weld area, resulting in excess material lying on the base metal without proper fusion.
How can I identify welding overlap?
You can identify welding overlap through visual inspection, touch tests for raised edges, and observing performance issues in the weld joint.
What are the best practices to prevent welding overlap?
To prevent welding overlap, ensure proper training, use the right equipment, adjust welding parameters correctly, and choose the appropriate welding technique for the material and position.
Can welding overlap be fixed?
Yes, welding overlap can be fixed through methods such as grinding off the excess material, re-welding the area, and applying corrective techniques to ensure proper fusion.
Conclusion
Preventing welding overlap is crucial for ensuring the strength, durability, and aesthetic quality of welds. By understanding the causes and consequences of overlap and implementing the right techniques and parameters, welders can significantly reduce the risk of this common issue. Continuous learning, proper equipment, and attention to detail are key to achieving high-quality welds free from overlap.