What is Smut in Aluminum Welding?
Aluminum welding is widely valued for creating strong, lightweight, and corrosion-resistant joints. However, a significant welding defect known as “smut” can occur, compromising the weld’s aesthetic and mechanical integrity. Smut in welding is typically a blackened, sooty residue that accumulates on the weld surface, caused by various factors specific to aluminum’s unique properties.
In this article, we’ll explore the nuances of smut in aluminum welding, including its causes, effects, prevention strategies, and removal methods. By understanding each of these aspects, welders can produce clean, high-quality welds without the downsides of smut.
Understanding Aluminum Welding: Basics and Challenges
The Unique Properties of Aluminum
Aluminum is distinct from other metals due to its low weight, high strength-to-weight ratio, and excellent resistance to corrosion. However, these properties also make it more challenging to weld. For example:
- High Thermal Conductivity: Aluminum conducts heat faster than other metals, which means it requires careful control of heat input during welding to avoid overheating.
- Oxide Layer Formation: When aluminum is exposed to air, it forms a thin, hard oxide layer almost immediately. This oxide layer has a higher melting point than aluminum itself, often requiring extra cleaning and specific welding techniques to handle effectively.
These characteristics necessitate different preparation, techniques, and equipment compared to metals like steel.
Why Welding Aluminum Is More Challenging than Other Metals
Welding aluminum can be tricky because of the metal’s propensity to react with air and heat. Without proper preparation, aluminum’s oxide layer can interfere with the welding arc, leading to defects such as smut, porosity, and cracks. The high thermal conductivity also increases the risk of overheating, which can lead to burn-through and surface contamination.
What is Smut in Welding?
Smut refers to a dark, soot-like residue that forms on the weld’s surface, especially when welding aluminum. Smut results from specific reactions that occur due to the high temperatures involved in welding aluminum. It can range from slight darkening of the metal to thick layers of blackened material.
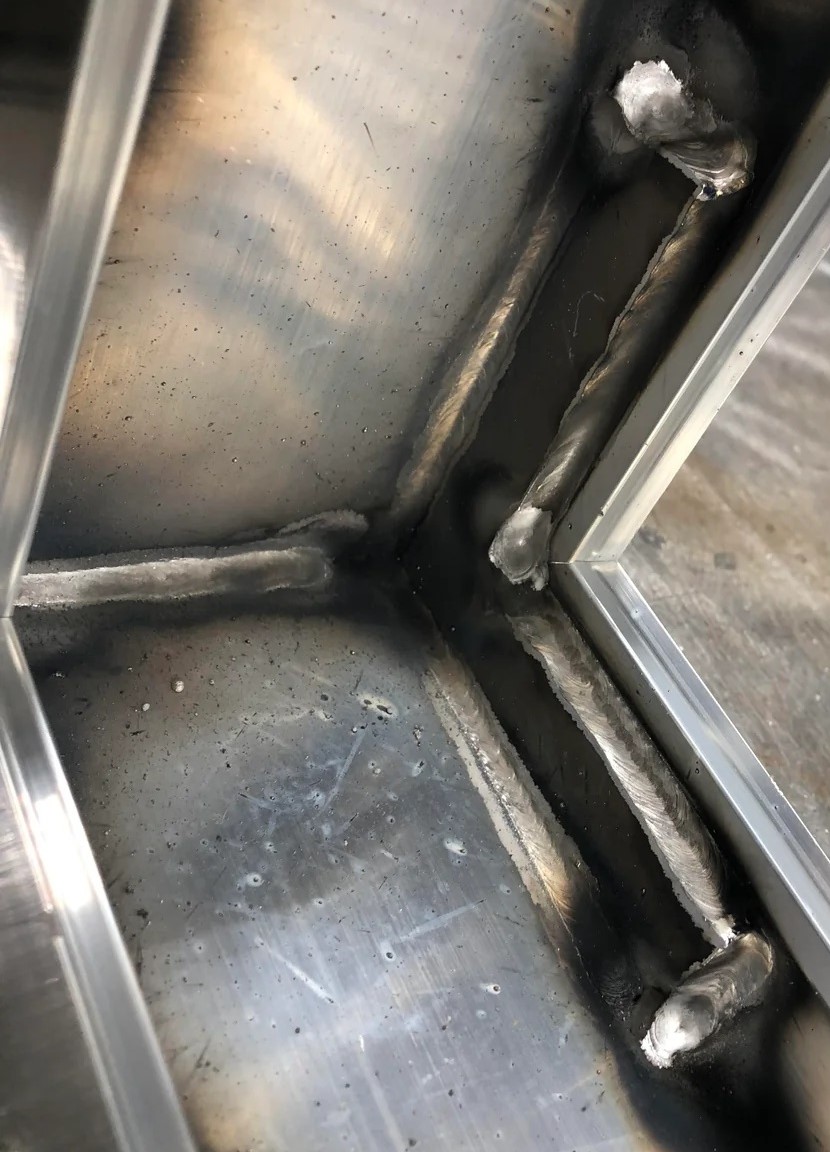
Difference Between Smut and Other Welding Contaminants
While smut is a form of contamination, it is specifically related to surface oxidation and carbonization, distinct from other welding contaminants like slag or porosity:
- Smut: Primarily affects the appearance of the weld surface and can be caused by oxidation and hydrocarbons.
- Porosity: Caused by gas entrapment within the weld metal, which compromises structural integrity.
- Slag: Typically found in welding processes like stick or flux-cored arc welding, but not common in aluminum welding.
Understanding this difference is essential, as smut usually forms on the surface rather than inside the weld, although it can still impact weld quality if left untreated.
Causes of Smut Formation in Aluminum Welding
Smut formation in aluminum welding is typically caused by a few key factors. Here’s a closer look at the primary contributors:
Oxidation on the Aluminum Surface
Aluminum readily reacts with oxygen in the air, creating a naturally protective oxide layer. However, if this oxide layer isn’t removed before welding, it can react with the heat from the welding process, leading to smut formation on the weld’s surface. This is especially common when welding without proper surface cleaning or in an environment with excessive airborne contaminants.
Heat and Temperature Factors
Aluminum’s high thermal conductivity means that it heats up quickly, and if the temperature isn’t well-regulated, it can cause surface oxidation and carbonization, leading to smut. Using excessive heat can cause hydrocarbons to deposit on the surface, creating a layer of smut.
Environmental Contaminants
Contaminants like oil, dirt, or even moisture on the aluminum surface or in the surrounding environment can react during welding, producing smut. Proper cleaning and environmental control can significantly reduce this issue, as foreign particles are a major cause of surface discoloration and smut.
The Effects of Smut on Weld Quality
While smut might seem like a surface-level issue, it can have various impacts on weld quality, including:
Impact on Weld Integrity and Strength
Smut deposits can interfere with the bond between layers in the weld, potentially causing weak points. These weak spots may lead to premature failure, especially under stress or load, reducing the overall strength of the weld.
Aesthetic Concerns in Final Weld Appearance
For applications where appearance matters, such as visible joints in car bodies or structural architecture, smut can ruin the aesthetics of the weld. The black residue is unsightly, and removing it requires extra time and effort, especially if the weld needs a polished, clean finish.
Issues with Adherence in Coatings and Finishes
Smut can create adhesion problems if you need to apply coatings or paint over the weld. The smut layer prevents paints, coatings, or sealants from bonding to the metal surface, potentially causing the finish to peel, chip, or wear prematurely.
How to Prevent Smut in Aluminum Welding
Prevention is often more effective than removal when it comes to smut. Here are some methods to avoid smut formation during aluminum welding:
Cleaning the Aluminum Surface Properly
One of the most effective ways to prevent smut is to thoroughly clean the aluminum surface before welding. This includes:
- Removing the Oxide Layer: Use an abrasive pad or a dedicated aluminum cleaner to remove the natural oxide layer, which can prevent smut formation.
- Degreasing: Aluminum surfaces should be free of oils and contaminants. Use solvents like acetone or alcohol for thorough degreasing.
Choosing the Right Welding Technique and Parameters
Certain welding processes and settings can produce more or less smut. For instance, TIG welding generally produces less smut than MIG welding for aluminum. Additionally, adjusting parameters like:
- Heat Input: Use lower heat settings to avoid surface oxidation.
- Gas Flow: A consistent shielding gas flow can help prevent oxygen from contaminating the weld area.
Controlling Heat Input and Environment
To minimize smut formation, control both heat input and environmental factors. Try welding in a clean, well-ventilated space free from dust or airborne contaminants, and avoid overheating the aluminum, which can cause oxidation and smut.
Removing Smut After Aluminum Welding
If smut still forms despite preventive measures, there are effective ways to remove it without damaging the weld. Here are some popular methods:
Mechanical Cleaning Methods (Grinding, Sanding)
For light smut, mechanical cleaning such as light sanding or grinding can remove the residue. Use fine-grit sandpaper or abrasive pads to avoid removing too much metal, as aluminum is relatively soft.
Chemical Cleaning Solutions
Chemical cleaning solutions, including mild acids designed for aluminum, can be used to dissolve smut and clean the weld area. These are often available as specialized aluminum cleaning agents and should be used according to the manufacturer’s instructions to avoid damaging the weld.
Using Abrasive Blasting
For larger welded areas with more extensive smut, abrasive blasting can be effective. However, select an abrasive material that won’t damage the aluminum surface, such as walnut shell grit or plastic media.
Safety Precautions When Dealing with Smut and Aluminum Dust
Smut removal, especially with mechanical and chemical methods, produces dust and particles that can be hazardous if inhaled. Here are some safety tips:
Health Hazards Associated with Smut
Aluminum dust and smut contain fine particles that can be harmful when inhaled, causing respiratory issues or irritation over time. Prolonged exposure may increase risks for specific lung conditions.
Importance of Proper Ventilation and Protective Gear
When removing smut, always work in a well-ventilated area, ideally with an exhaust system. Wearing masks, goggles, and gloves is crucial for personal safety, especially when dealing with fine dust and chemical cleaning agents.
Common Mistakes to Avoid in Aluminum Welding
Avoiding these common mistakes can greatly reduce smut formation and enhance weld quality:
Lack of Pre-Weld Cleaning
Failing to clean aluminum before welding leaves surface contaminants, which are a primary cause of smut. Even a slight residue of oil, dirt, or oxidation can lead to issues during welding.
Using Excessive Heat
Excessive heat can lead to both smut and warping of the aluminum. Avoid using settings that are too high and always monitor the temperature to prevent burning the metal’s surface.
Ignoring Environmental Control
Welding in a dirty, dusty, or uncontrolled environment can lead to smut, as airborne particles often settle on the weld during the process. Try to weld in a clean, controlled area to minimize these issues.
FAQs
What are some common cleaning agents for removing smut from aluminum welds?
Specialized aluminum cleaners, mild acids, and even household solvents like acetone can be effective for smut removal.
How does smut affect the durability of an aluminum weld?
If smut is not removed, it can prevent coatings from adhering and compromise the weld’s strength over time.
Can smut formation be completely prevented in aluminum welding?
While smut is hard to eliminate entirely, proper preparation and controlled settings can reduce its occurrence significantly.
What is the safest method for removing smut?
Light sanding or the use of mild chemical cleaners is effective for small areas, while abrasive blasting can be used for larger surfaces, provided the right media is used.
Does smut affect the welding of all metals, or is it specific to aluminum?
Smut is most commonly seen in aluminum welding due to its oxide layer and reactivity but can occasionally appear in other metals under similar conditions.
Conclusion
Smut formation is a common, but manageable, challenge in aluminum welding. By understanding the causes, effects, and prevention techniques for smut, you can significantly improve the appearance and quality of your aluminum welds. Whether it’s through proper cleaning, heat control, or post-weld treatment, minimizing smut ensures your welds are not only functional but also professional in appearance. Adopting these best practices will lead to more successful, smut-free aluminum welds and help you consistently produce high-quality results.