Boiler & Pressure Vessel Welding Standards
Welding plays a crucial role in the fabrication and maintenance of boilers and pressure vessels, two key components in industries like power generation, oil and gas, and manufacturing. But how do we ensure these welds are safe, reliable, and compliant? That’s where welding standards come in. Let’s dive into the details.
Introduction to Boiler and Pressure Vessel Welding
Welding for boilers and pressure vessels isn’t just any type of welding; it’s a precise and highly regulated craft. These components are often subjected to extreme pressure and temperature, making the integrity of welds absolutely critical.
Importance of Welding Standards
Why do we need strict welding standards? Simply put, they’re the backbone of safety and reliability. Standards ensure that every weld can withstand high stress, prevent catastrophic failures, and prolong the lifespan of equipment.
Overview of Boiler and Pressure Vessels
Boilers generate steam by heating water, while pressure vessels store substances under pressure. Both require robust construction to manage the mechanical and thermal stresses they encounter during operation.
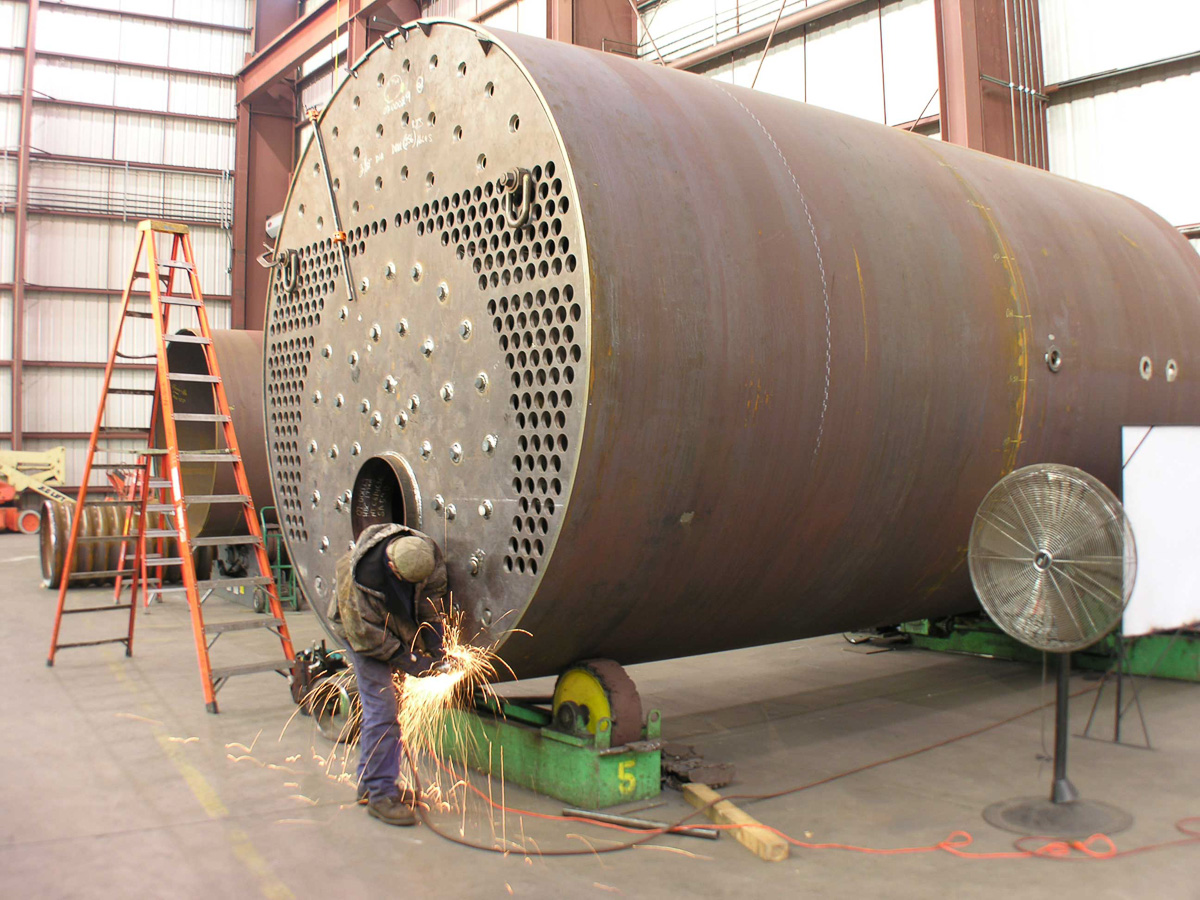
Image source
Key Organizations Defining Welding Standards
Several leading organizations play pivotal roles in establishing and maintaining welding standards for boilers and pressure vessels. Their work ensures uniformity, safety, and quality across the industry globally. Let’s dive into their contributions and real-world applications.
American Society of Mechanical Engineers (ASME)
The ASME sets the gold standard in the form of its Boiler and Pressure Vessel Code (BPVC). Section IX of the BPVC, specifically dedicated to welding and brazing qualifications, is recognized worldwide. ASME standards guide fabricators and engineers in producing pressure vessels that can withstand extreme operating conditions.
For example, in nuclear power plants, where failure is not an option, ASME’s rigorous guidelines ensure that every weld meets the highest safety and durability standards. This ensures the structural integrity of components that operate under immense pressure and high temperatures.
American Welding Society (AWS)
AWS contributes a comprehensive range of welding codes, such as AWS D1.1, which focuses on structural welding. While it is not exclusively aimed at pressure vessels, AWS standards often complement ASME guidelines, particularly in projects requiring diverse welding techniques.
A notable application of AWS standards can be seen in offshore oil platforms. Here, robust welds are vital for structural stability against harsh marine environments. The AWS guidelines ensure weld quality and durability in such critical applications.
International Organization for Standardization (ISO)
ISO standards, particularly ISO 3834, address the quality requirements for fusion welding of metallic materials. These standards are integral for international projects, where multiple contractors from different countries collaborate.
One such example is the construction of liquefied natural gas (LNG) storage tanks. These projects often involve multinational teams, and ISO 3834 ensures consistent welding practices and quality assurance across the board, regardless of geographical location.
Together, ASME, AWS, and ISO define the benchmarks that ensure global consistency, safety, and efficiency in boiler and pressure vessel welding projects.
American Society of Mechanical Engineers (ASME)
ASME’s Boiler and Pressure Vessel Code (BPVC) is a global benchmark for safety. Section IX, in particular, focuses on welding and brazing qualifications, ensuring welders and procedures meet stringent requirements.
American Welding Society (AWS)
The AWS develops standards like AWS D1.1, which guide structural welding practices. While not exclusive to pressure vessels, AWS standards complement ASME codes to enhance weld quality.
International Organization for Standardization (ISO)
ISO standards, such as ISO 3834, address quality requirements for welding, making them an essential part of international projects involving boilers and pressure vessels.
Welding Standards for Boilers and Pressure Vessels
Understanding the core welding standards is essential to ensure compliance, safety, and efficiency in manufacturing and maintaining boilers and pressure vessels. These standards, though unique in their scope, often complement one another to create a comprehensive framework for welding practices.
ASME Section IX
ASME Section IX is the cornerstone standard for welding and brazing qualifications. It outlines the requirements for creating Welding Procedure Specifications (WPS) and Performance Qualification Records (PQR). These documents ensure that welding processes and welders are qualified to meet the rigorous demands of boiler and pressure vessel construction.
For instance, in the fabrication of high-pressure steam boilers, ASME Section IX ensures that each weld undergoes stringent testing for strength and durability. This minimizes risks associated with high-temperature and high-pressure environments, safeguarding both equipment and personnel.
AWS D1.1 and Other Relevant Codes
While AWS D1.1 primarily focuses on structural welding, it complements ASME standards by addressing the broader techniques and applications that might be involved in boiler and pressure vessel fabrication. Additional AWS standards, such as those for SMAW and GTAW, offer detailed guidance for specific welding processes.
Consider a scenario involving the repair of pressure vessels in chemical plants. AWS standards provide the procedural clarity needed to execute precise and durable repairs, ensuring the vessel’s continued safe operation under demanding conditions.
ISO 3834 for Quality Requirements
ISO 3834 sets out quality requirements for fusion welding processes. This standard is especially relevant in projects involving international collaboration, where consistency across teams and regions is crucial.
A practical example of ISO 3834’s application is in the construction of LNG storage tanks. These massive structures, often involving multinational contractors, rely on ISO 3834 to ensure uniform welding quality and adherence to agreed-upon specifications, regardless of geographical differences.
Interrelation and Practical Applications
While each standard has its specific focus, they often interrelate to provide a holistic approach to welding quality and safety. For example, a project might use ASME Section IX for procedural qualifications, AWS D1.1 for specific welding methods, and ISO 3834 for overarching quality assurance.
In the aerospace industry, where pressure vessels must meet exceptional standards, these codes work together seamlessly. ASME ensures procedural compliance, AWS guides technique-specific practices, and ISO maintains uniform quality control across global teams.
ASME Section IX
This is the go-to standard for qualifying welding procedures and personnel. It provides detailed guidelines on creating and testing welding procedure specifications (WPS) and performance qualification records (PQR).
AWS D1.1 and Other Relevant Codes
AWS D1.1 focuses on structural welding, while other AWS codes address specific processes like SMAW, GTAW, and SAW. These standards ensure welders’ skills are up to par.
ISO 3834 for Quality Requirements
ISO 3834 ensures the quality of fusion welding processes, from material selection to final inspection. It’s particularly useful for projects involving international teams and contractors.
Welding Techniques for Boilers and Pressure Vessels
Shielded Metal Arc Welding (SMAW)
SMAW, or stick welding, is widely used due to its simplicity and versatility. It’s especially effective for thicker materials often found in boilers and pressure vessels.
Gas Tungsten Arc Welding (GTAW)
Known for its precision, GTAW is ideal for welding exotic alloys and achieving high-quality welds. However, it’s slower compared to other methods.
Submerged Arc Welding (SAW)
SAW is a high-efficiency process suitable for long, straight welds in pressure vessels. Its automation capabilities make it a favorite for large-scale projects.
The Role of Welders in Compliance
Required Certifications and Qualifications
Welders must obtain certifications like ASME’s Section IX qualifications. These credentials prove their skills and adherence to standards.
Continuous Training and Development
As technology evolves, welders need ongoing training to master new techniques and stay compliant with updated standards.
FAQs
What is the purpose of welding standards for boilers and pressure vessels?
Welding standards ensure the safety, reliability, and quality of welds, preventing failures and ensuring compliance with regulations.
How do ASME and AWS standards differ?
ASME focuses on boiler and pressure vessel codes, while AWS provides broader guidance on welding techniques and qualifications.
What are the most common welding techniques used in this industry?
Techniques like SMAW, GTAW, and SAW are commonly used due to their effectiveness and adaptability to various materials.
Why is non-destructive testing critical in pressure vessel welding?
NDT identifies weld defects without damaging the structure, ensuring safety and compliance with industry standards.
How are advancements in technology shaping the future of welding in this field?
Automation, robotics, and innovative materials are enhancing efficiency, precision, and overall weld quality.
Conclusion
Welding standards for boilers and pressure vessels are the foundation of safety, quality, and efficiency in this critical industry. From adhering to ASME codes to embracing cutting-edge techniques, welders and manufacturers must prioritize compliance to succeed in a competitive landscape.