Boiler Welding Techniques – A Complete Guide for Professionals
Boiler welding is a specialized craft essential to the structural integrity and performance of boilers. Boilers operate under high pressure and temperature, often containing volatile substances. Welding for boilers demands advanced skill and understanding to ensure joints can withstand extreme stresses without failure. This article offers an in-depth exploration of boiler welding techniques, covering everything from preparation to post-weld treatment, and aims to equip you with a thorough understanding of every aspect involved.
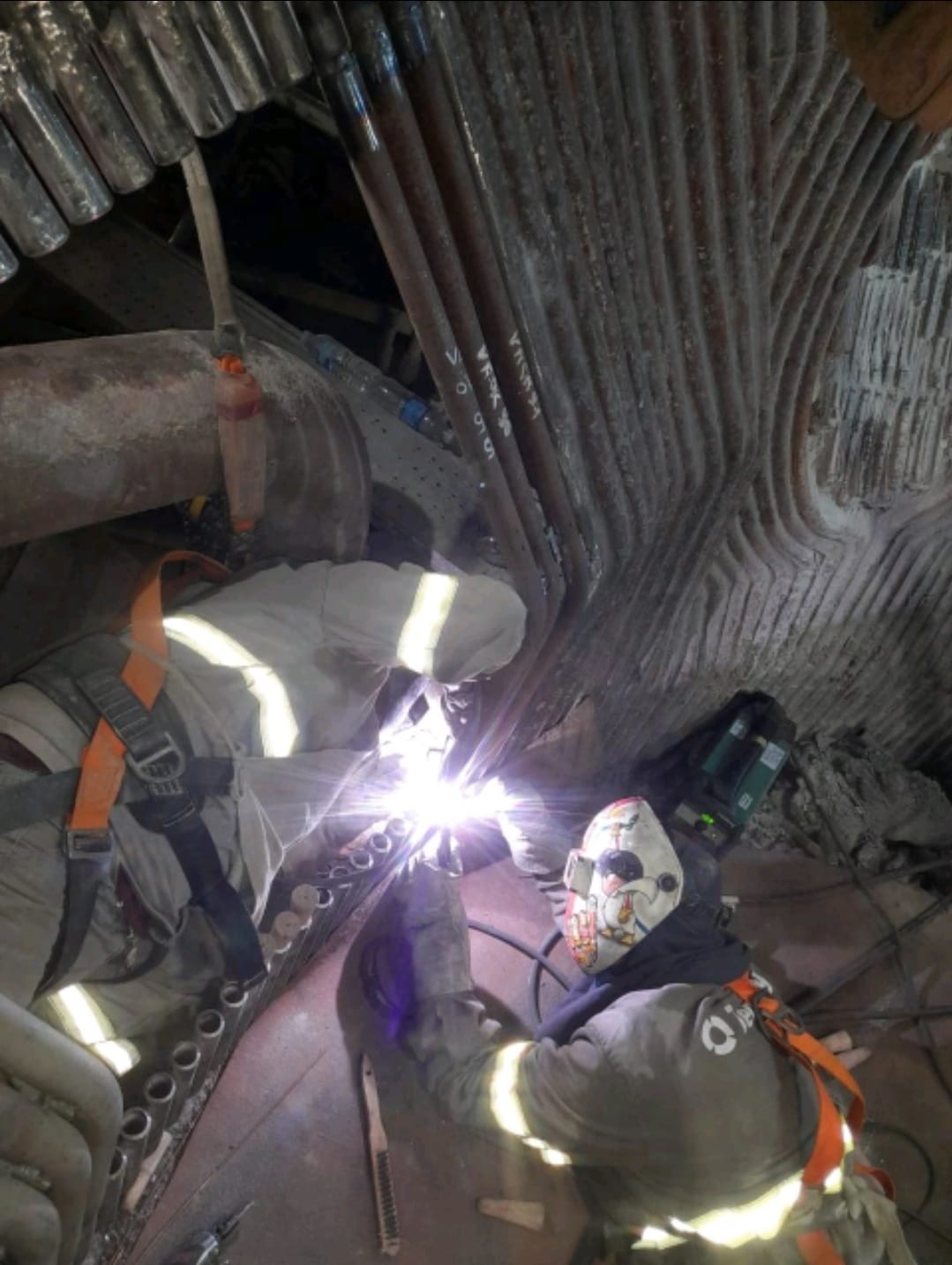
Understanding the Importance of Boiler Welding
Boiler welding isn’t just about joining metal parts; it’s about creating a bond that must withstand both internal and external pressures for a prolonged period. Poorly executed welds can cause leaks, energy loss, and even dangerous failures. This is especially crucial in industries where any flaw could compromise safety and productivity, making skilled boiler welding fundamental for both performance and safety.
Applications of Boiler Welding Across Industries
Industries such as power generation, oil refineries, and chemical processing rely on robust, well-welded boilers. For example, power plants use large boilers to generate steam that powers turbines, while chemical plants use boilers for heating and processing chemicals. Each of these applications has strict requirements for boiler welding to ensure that the boiler performs reliably under heavy loads, high temperatures, and sometimes corrosive environments.
Types of Welding Techniques for Boilers
Different welding techniques cater to different types of boiler joints and structural needs. Each method has unique properties that make it suitable for specific applications.
Shielded Metal Arc Welding (SMAW)
SMAW, commonly known as stick welding, is widely used for its versatility and effectiveness on various metals, especially in industrial settings. This method is particularly suitable for thicker sections of a boiler, as it achieves deep penetration. SMAW’s robustness makes it ideal for high-stress environments, although it requires experienced welders to avoid common issues like slag inclusion. Proper skill in SMAW ensures clean, strong welds for boiler shells and pressure-bearing components.
Gas Tungsten Arc Welding (GTAW)
Gas Tungsten Arc Welding (GTAW), also known as TIG welding, is the preferred technique for high-precision welding. It’s commonly used on thinner boiler components or for areas that require fine detail. With minimal spatter and high control, GTAW is suitable for complex boiler joints. Although it is slower and requires significant skill, TIG welding produces high-quality, clean welds, making it ideal for delicate areas that cannot tolerate any weld contamination.
Flux-Cored Arc Welding (FCAW)
Flux-Cored Arc Welding (FCAW) is valued for its high-speed application, particularly in industrial settings where time efficiency is key. FCAW is effective for welding thick metals and can be used outdoors, making it a preferred method for maintenance and fieldwork on boilers. Since FCAW offers excellent fusion and can produce strong, durable welds, it’s frequently chosen for large industrial boilers that require both strength and speed.
Submerged Arc Welding (SAW)
Submerged Arc Welding (SAW) is often used for the longitudinal seams of boiler shells. SAW allows for deep penetration and high-quality welds with minimal defects due to its submerged arc, which protects the weld from contamination. This method is especially suited for larger, cylindrical boiler sections that require continuous, even welds to handle high pressures and stresses.
Materials Used in Boiler Construction
Choosing the right materials for boilers is critical, as they need to resist heat, pressure, and sometimes corrosive substances. Each material comes with its specific welding challenges.
Types of Steel for Boilers
Steel is the most common material for boilers due to its strength, durability, and resistance to high temperatures. Carbon steel is widely used as it welds easily and has good heat tolerance. However, other types of steel, like stainless steel or alloyed steels, are sometimes required for added strength or corrosion resistance. Each type has different welding needs; for example, alloyed steels often require special techniques to prevent cracking and ensure a reliable weld.
Alloy Considerations and Their Implications on Welding
Boilers often incorporate alloys like chromium-molybdenum for high-temperature applications. These alloys offer greater strength and heat resistance but present specific welding challenges due to their sensitivity to thermal stress. Proper techniques, such as preheating and controlled cooling, are necessary to prevent cracking and embrittlement in alloyed steels. Understanding these requirements is essential for maintaining the structural integrity of alloy-based boilers.
Essential Equipment for Boiler Welding
Specialized equipment is essential to ensure precision, safety, and quality in boiler welding.
Welding Machines
Selecting the right welding machine is crucial. For boilers, machines capable of handling high amperage and voltage are needed to manage thick metals and long welds. TIG welders, MIG welders, and stick welders each have their place in boiler welding, depending on the specific requirements of the task. High-quality machines with reliable power controls are indispensable for maintaining consistent weld quality.
Tools and Accessories for Precision and Safety
Additional tools like grinders, clamps, and weld gauges enhance accuracy and ease during the welding process. For safety, welding helmets, gloves, protective eyewear, and respirators protect welders from heat and fumes. Tools like angle grinders help in preparing the surface and removing impurities, which is vital for ensuring a clean and strong weld.
Preparing for Boiler Welding
Preparation is key to achieving high-quality welds that can withstand intense pressure and temperature.
Pre-weld Inspection and Preparation
Before welding begins, it’s essential to thoroughly inspect the materials and equipment. This involves cleaning the metal surfaces to remove any rust, oil, or debris. For some materials, preheating may be required to prevent cracking, especially when welding thicker sections or certain alloys. Proper preparation minimizes the risk of defects and ensures a stronger weld.
Handling Safety Precautions Before Welding
Safety is paramount in boiler welding. Proper ventilation, PPE, and equipment checks are necessary to reduce the risk of accidents. Boilers often require work in confined spaces, so additional precautions like gas monitoring and emergency procedures are vital. Ensuring a safe environment allows welders to work more effectively and reduces the risk of injuries.
Step-by-Step Boiler Welding Process
Following a methodical approach is essential to achieving a durable and reliable weld.
Tack Welding and Alignment
Tack welding involves placing small welds to hold components in place before final welding. This step ensures proper alignment, which is crucial for the final weld’s quality. Misalignment can cause stress points, leading to weld failures. Tack welding provides stability and helps maintain the intended shape and position of the components.
Managing Weld Layers and Heat Control
In boiler welding, it’s essential to control the heat input to prevent issues like warping. Layered welding, where welds are built up in layers, helps manage heat distribution. Controlling the heat through precise adjustments in welding parameters allows for smoother welds and prevents overheating, which can compromise the weld’s strength and durability.
Common Challenges in Boiler Welding
Boiler welding comes with specific challenges that must be managed to ensure long-lasting welds.
Warping and Distortion Issues
High heat can cause metal to warp, leading to misalignment and weak points. Tack welding, clamps, and controlling welding speed can help reduce these effects. In some cases, preheating or using heat-dampening techniques can prevent distortion. Understanding how to control and distribute heat during welding is key to maintaining the correct shape and strength.
Ensuring Weld Strength and Integrity
Boiler welds must withstand pressure and temperature fluctuations. Weak welds are prone to leaks and can lead to boiler failure. Quality control measures, like non-destructive testing (NDT), and maintaining proper heat control throughout the process help ensure the weld’s integrity.
Quality Control and Testing for Boiler Welds
Quality control is vital in boiler welding to verify that the welds meet safety and performance standards.
Non-Destructive Testing (NDT) Techniques
NDT techniques, such as ultrasonic and radiographic testing, are used to inspect welds without damaging them. These methods detect internal flaws that are not visible to the naked eye, ensuring the weld’s strength and reliability. For boilers, these tests are essential for validating that welds can withstand the demanding operational conditions.
Visual Inspection and Radiographic Testing
Visual inspection helps identify surface flaws, such as cracks or improper weld beads. Radiographic testing, often conducted with X-rays, provides insight into internal defects. Combining these tests ensures that both visible and hidden issues are addressed before the boiler is put into service.
Best Practices for Long-lasting Boiler Welds
Following best practices ensures that the welded boiler components remain reliable and safe over time.
Post-Weld Heat Treatment (PWHT)
Post-Weld Heat Treatment is a method of relieving residual stress in the weld, reducing brittleness and preventing cracking. PWHT is essential for thicker sections or high-stress joints in boilers, as it ensures a more durable weld and extends the lifespan of the welded area.
Maintaining the Weld Over Time
Regular inspection and maintenance help detect and repair minor issues before they escalate. Routine checks ensure that the weld remains strong and that no weaknesses develop. Preventive maintenance reduces the chances of unexpected failures, enhancing boiler safety and longevity.
FAQs
What is the best welding technique for boiler repairs?
For repairs, SMAW or stick welding is often the most suitable due to its adaptability to various metals and deep penetration capabilities.
How can I prevent weld cracks in high-temperature boiler welding?
To prevent cracks, ensure proper preheating, controlled heat input, and apply post-weld heat treatment if needed.
What safety measures should be taken during boiler welding?
Key safety measures include wearing PPE, ensuring proper ventilation, and conducting equipment checks before starting work.
Which materials are ideal for boiler welding?
Carbon steel and specific alloy steels are ideal due to their strength and ability to handle high pressure and temperature.
How does post-weld heat treatment enhance boiler weld durability?
PWHT relieves stress, prevents brittleness, and extends the weld’s lifespan, especially in high-stress areas.
Conclusion
Boiler welding is a specialized skill that requires precision, knowledge, and adherence to best practices. From selecting the right welding technique and materials to following a structured process, every step plays a role in creating a durable, high-quality weld. Understanding the nuances of each method—SMAW, GTAW, FCAW, and SAW—along with thorough preparation, quality control, and post-weld treatment, allows for the creation of reliable and efficient boilers that withstand even the most demanding environments.